機(jī)械專業(yè)外文翻譯--在高速潮濕機(jī)械加工條件下后刀面表層磨損機(jī)理
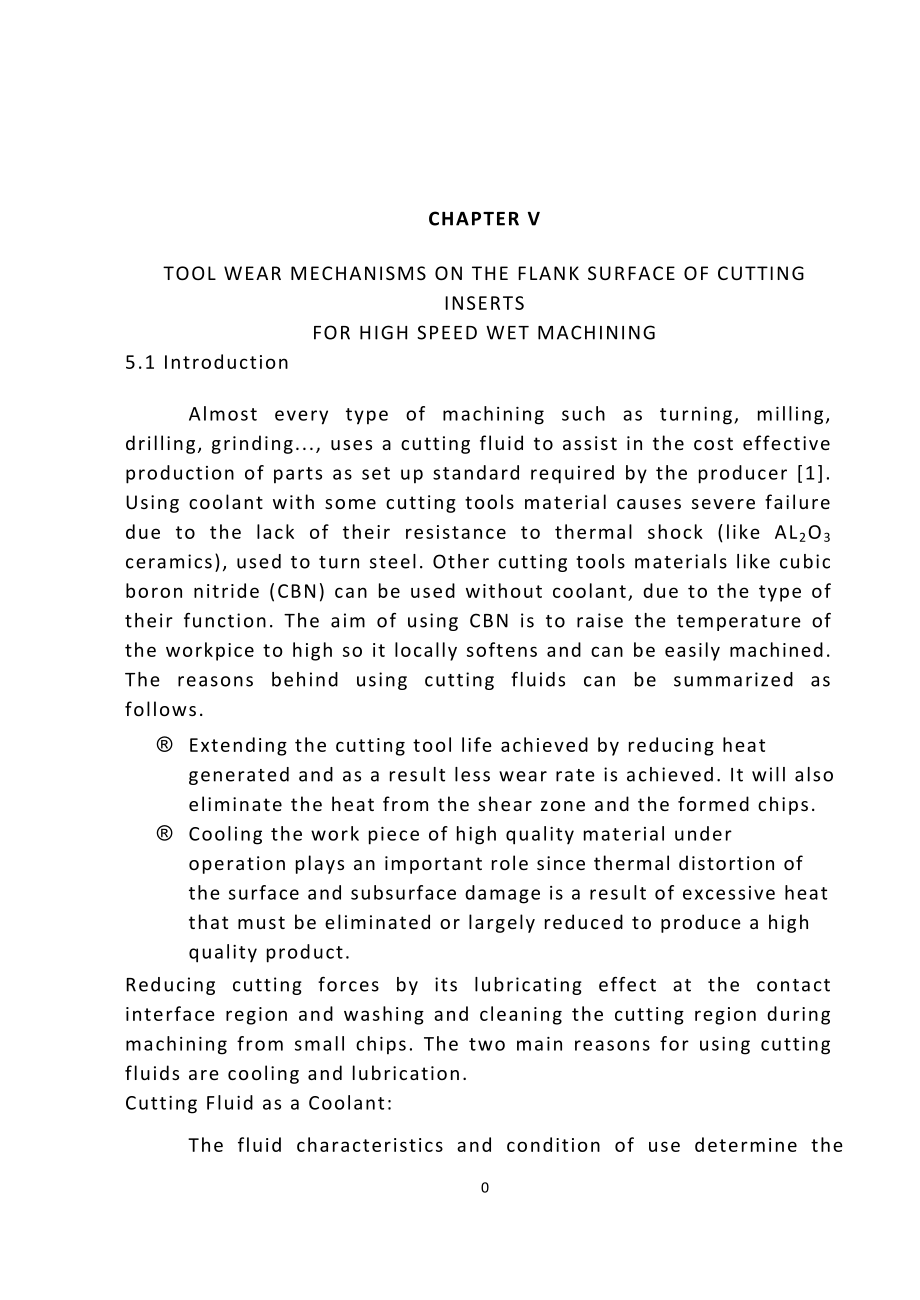


《機(jī)械專業(yè)外文翻譯--在高速潮濕機(jī)械加工條件下后刀面表層磨損機(jī)理》由會(huì)員分享,可在線閱讀,更多相關(guān)《機(jī)械專業(yè)外文翻譯--在高速潮濕機(jī)械加工條件下后刀面表層磨損機(jī)理(45頁(yè)珍藏版)》請(qǐng)?jiān)谘b配圖網(wǎng)上搜索。
1、19 CHAPTER V TOOL WEAR MECHANISMS ON THE FLANK SURFACE OF CUTTING INSERTS FOR HIGH SPEED WET MACHINING 5.1 Introduction Almost every type of machining such as turning, milling, drilling, grinding..., uses a cutting fluid to assist in the cost effective production of parts as set up standard r
2、equired by the producer [1]. Using coolant with some cutting tools material causes severe failure due to the lack of their resistance to thermal shock (like AL2O3 ceramics), used to turn steel. Other cutting tools materials like cubic boron nitride (CBN) can be used without coolant, due to the type
3、of their function. The aim of using CBN is to raise the temperature of the workpice to high so it locally softens and can be easily machined. The reasons behind using cutting fluids can be summarized as follows. ? Extending the cutting tool life achieved by reducing heat generated and as a result l
4、ess wear rate is achieved. It will also eliminate the heat from the shear zone and the formed chips. ? Cooling the work piece of high quality material under operation plays an important role since thermal distortion of the surface and subsurface damage is a result of excessive heat that must be eli
5、minated or largely reduced to produce a high quality product. Reducing cutting forces by its lubricating effect at the contact interface region and washing and cleaning the cutting region during machining from small chips. The two main reasons for using cutting fluids are cooling and lubrication.
6、Cutting Fluid as a Coolant: The fluid characteristics and condition of use determine the coolant action of the cutting fluid, which improves the heat transfer at the shear zone between the cutting edge, work piece, and cutting fluid. The properties of the coolant in this case must include a high he
7、at capacity to carry away heat and good thermal conductivity to absorb the heat from the cutting region. The water-based coolant emulsion with its excellent high heat capacity is able to reduce tool wear [44]. Cutting Fluid as a Lubricant: The purpose is to reduce friction between the cutting edge
8、, rake face and the work piece material or reducing the cutting forces (tangential component). As the friction drops the heat generated is dropped. As a result, the cutting tool wear rate is reduced and the surface finish is improved. Cutting Fluid Properties Free of perceivable odor Preserve cl
9、arity throughout life Kind and unirritated to skin and eyes. Corrosion protection to the machine parts and work piece. Cost effective in terms off tool life, safety, dilution ratio, and fluid life. [1] 5.1.1 Cutting Fluid Types There are two major categories of cutting fluids Neat Cutting Oils
10、 Neat cutting oils are poor in their coolant characteristics but have an excellent lubricity. They are applied by flooding the work area by a pump and re-circulated through a filter, tank and nozzles. This type is not diluted by water, and may contain lubricity and extreme-pressure additives to enh
11、ance their cutting performance properties. The usage of this type has been declining for their poor cooling ability, causing fire risk, proven to cause health and safety risk to the operator [1]. ? Water Based or Water Soluble Cutting Fluids This group is subdivided into three categories: 1. Emul
12、sion ` mineral soluble' white-milky color as a result of emulsion of oil in water. Contain from 40%-80% mineral oil and an emulsifying agent beside corrosion inhibitors, beside biocide to inhibit the bacteria growth. 2. Micro emulsion `semi-synthetic' invented in 1980's, has less oil concentration
13、and/or higher emulsifier ratio 10%-40% oil. Due to the high levels of emulsifier the oil droplet size in the fluid are smaller which make the fluid more translucent and easy to see the work piece during operation. Other important benefit is in its ability to emulsify any leakage of oil from the mach
14、ine parts in the cutting fluid, a corrosion inhibitors, and bacteria control. 3. Mineral oil free `synthetic' is a mix of chemicals, water, bacteria control, corrosion inhibitors, and dyes. Does not contain any mineral oils, and provides good visibility .23 to the work piece. bare in mind that t
15、he lack of mineral oil in this type of cutting fluid needs to take more attention to machine parts lubrication since it should not leave an oily film on the machine parts, and might cause seals degradation due the lack of protection. 5.1.2 Cutting Fluid Selection Many factors influence the select
16、ion of cutting fluid; mainly work piece material, type of machining operation, machine tool parts, paints, and seals. Table 5-1 prepared at the machine tool industry research association [2] provides suggestions on the type of fluid to be used. 5.1.3 Coolant Management To achieve a high level of c
17、utting fluids performance and cost effectiveness, a coolant recycling system should be installed in the factory. This system will reduce the amount of new purchased coolant concentrate and coolant disposable, which will reduce manufacturing cost. It either done by the company itself or be rented out
18、, depends on the budget and management policy of the company [1]. Table 5-1 Guide to the selection of cutting fluids for general workshop applications. Machining operation Workpiece material Free machining and low - carbon steels Medium- Carbon steels High Carbon and alloy steels Stai
19、nless and heat treated resistant alloys Grinding Clear type soluble oil, semi synthetic or chemical grinding fluid Turning General purpose, soluble oil, semi synthetic or synthetic fluid Extreme-pressure soluble oil, semi-synthetic or synthetic fluid Milling General purpose, soluble o
20、il, semi synthetic or synthetic fluid Extreme- pressure soluble oil, semi- synthetic or synthetic fluid Extreme-pressure soluble oil, semi-synthetic or synthetic fluid(neat cutting oils may be necessary) Drilling Extreme pressure soluble oil, semi synthetic or synthetic fluid
21、Gear Shapping Extreme-pressure soluble oil, semi-synthetic or synthetic fluid Neat-cutting oils preferable Hobbing Extreme-pressure soluble oil, semi-synthetic or synthetic fluid (neat cutting oils may be preferable) Neat-cutting oils preferable Bratching Extreme-pressure soluble oil, sem
22、i-synthetic or synthetic fluid (neat cutting oils may be preferable) Tapping Extreme-pressure soluble oil, semi-synthetic or synthetic fluid(neat cutting oils may be necessary) Neat-cutting oils preferable Note: some entreis deliberately extend over two or more columns, indicating a wi
23、de range of possible applications. Other entries are confined to a specific class of work material. Adopted from Edward and Wright [2] 5.2 Wear Mechanisms Under Wet High Speed Machining It is a common belief that coolant usage in metal cutting reduces cutting temperature and extends tools life. H
24、owever, this research showed that this is not necessarily true to be generalized over cutting inserts materials. Similar research was carried out on different cutting inserts materials and cutting conditions supporting our results. Gu et al [36] have recorded a difference in tool wear mechanisms bet
25、ween dry and wet cutting of C5 milling inserts. Tonshoff et al [44] also exhibited different wear mechanisms on AL2O3/TiC inserts in machining ASTM 5115, when using coolants emulsions compared to dry cutting. In addition, Avila and Abrao [20] experienced difference in wear mechanisms activated at th
26、e flank side, when using different coolants in testing AL2O3lTiC tools in machining AISI4340 steel. The wear mechanisms and the behavior of the cutting inserts studied in this research under wet high speed-machining (WHSM) condition is not fully understood. Therefore, it was the attempt of this rese
27、arch to focus on the contributions in coating development and coating techniques of newly developed materials in order to upgrade their performance at tough machining conditions. This valuable research provides insight into production timesavings and increase in profitability. Cost reductions are es
28、sential in the competitive global economy; thus protecting local markets and consisting in the search of new ones. 5.3 Experimental Observations on Wear Mechanisms of Un-Coated Cemented Carbide Cutting Inserts in High Speed Wet Machining In this section, the observed wear mechanisms are presented
29、of uncoated cemented carbide tool (KC313) in machining ASTM 4140 steel under wet condition. The overall performance of cemented carbide under using emulsion coolant has been improved in terms of extending tool life and reducing machining cost. Different types of wear mechanisms were activated at fla
30、nk side of cutting inserts as a result of using coolant emulsion during machining processes. This was due to the effect of coolant in reducing the average temperature of the cutting tool edge and shear zone during machining. As a result abrasive wear was reduced leading longer tool life. The materia
31、ls of cutting tools behave differently to coolant because of their varied resistance to thermal shock. The following observations recorded the behavior of cemented carbide during high speed machining under wet cutting. Figure 5-1 shows the flank side of cutting inserts used at a cutting speed of 18
32、0m/min. The SEM images were recorded after 7 minutes of machining. It shows micro-abrasion wear, which identified by the narrow grooves along the flank side in the direction of metal flow, supported with similar observations documented by Barnes and Pashby [41] in testing through-coolant-drilling in
33、serts of aluminum/SiC metal matrix composite. Since the cutting edge is the weakest part of the cutting insert geometry, edge fracture started first due to the early non-smooth engagement between the tool and the work piece material. Also, this is due to stress concentrations that might lead to a co
34、hesive failure on the transient filleted flank cutting wedge region [51, 52]. The same image of micro-adhesion wear can be seen at the side and tool indicated by the half cone 27 shape on the side of cutting tool. To investigate further, a zoom in view was taken at the flank side with a magnificat
35、ion of 1000 times and presented in Figure 5-2A. It shows clear micro-abrasion wear aligned in the direction of metal flow, where the cobalt binder was worn first in a higher wear rate than WC grains which protruded as big spherical droplets. Figure 5-2B provides a zoom-in view that was taken at anot
36、her location for the same flank side. Thermal pitting revealed by black spots in different depths and micro-cracks, propagated in multi directions as a result of using coolant. Therefore, theii~ial pitting, micro-adhesion and low levels of micro-abrasion activated under wet cutting; while high level
37、s of micro-abrasion wear is activated under dry cutting (as presented in the previous Chapter). Figure 5-3A was taken for a cutting insert machined at 150mlmin. It shows a typical micro-adhesion wear, where quantities of chip metal were adhered at the flank side temporarily. Kopac [53] exhibited si
38、milar finding when testing HSS-TiN drill inserts in drilling SAE1045 steel. This adhered metal would later be plucked away taking grains of WC and binder from cutting inserts material and the process continues. In order to explore other types of wear that might exist, a zoom-in view with magnificati
39、on of 750 times was taken as shown in Figure5-3B. Figure 5-3B show two forms of wears; firstly, micro-thermal cracks indicated by perpendicular cracks located at the right side of the picture, and supported with similar findings of Deamley and Trent [27]. Secondly, micro-abrasion wear at the left si
40、de of the image where the WC grains are to be plucked away after the cobalt binder was severely destroyed by micro-abrasion. Cobalt binders are small grains and WC is the big size grains. The severe distortion of the binder along with the WC grains might be due to the activation of micro-adhesion an
41、d micro-abrasion Figure 5-1 SEM image of (KC313) showing micro abrasion and micro-adhesion (wet). SEM micrographs of (KC313) at 180m/min showing micro-abrasion where cobalt binder was worn first leaving protruded WC spherical droplets (wet). (a) SEM micrographs of (KC313) at 180m/min showi
42、ng thermal pitting (wet). Figure 5-2 Magnified views of (KC313) under wet cutting: (a) SEM micrographs of (KC313) at 180mlmin showing micro-abrasion where cobalt binder was worn first leaving protruded WC spherical droplets (wet ), (b) SEM micrographs of (KC313) at 180.m/min showing thermal pitting
43、 (wet ). SEM image showing micro-adhesion wear mechanism under 150m/min (wet). (a) SEM image showing micro-thermal cracks, and micro-abrasion. Figure 5-3 Magnified views of (KC313) at 150m/min (wet): (a) SEM image showing micro-adhesion wear mechanism under 150m/min (wet), (b) SEM image show
44、ing micro-fatigue cracks, and micro-abrasion (wet). Wear at the time of cutting conditions of speed and coolant introduction. Therefore, micro-fatigue, micro-abrasion, and micro-adhesion wear mechanisms are activated under wet condition, while high levels of micro-abrasion were observed under dry o
45、ne. Next, Figure 5-4A was taken at the next lower speed (120m/min). It shows build up edge (BUE) that has sustained its existence throughout the life of the cutting tool, similar to Huang [13], Gu et al [36] and Venkatsh et al [55]. This BUE has protected the tool edge and extended its life. Under
46、dry cutting BUE has appeared at lower speeds (90 and 60 m/min), but when introducing coolant BUE started to develop at higher speeds, This is due to the drop in shear zone temperature that affected the chip metal flow over the cutting tool edge, by reducing the ductility to a level higher than the o
47、ne existing at dry condition cutting. As a result, chip metal starts accumulating easier at the interface between metal chip flow, cutting tool edge and crater surface to form a BUE. In addition to BUE formation, micro-abrasion wear was activated at this speed indicated by narrow grooves. To explor
48、e the possibility of other wear mechanisms a zoom-in view with a magnification of 3500 times was taken and shown in Figure 5-4B. Micro- fatigue is evident by propagated cracks in the image similar to Deamley and Trent [27] finding. Furthermore, Figure 5-4B shows indications of micro-abrasion wear, r
49、evealed by the abrasion of cobalt binder and the remains of big protruded WC grains. However, the micro-abrasion appeared at this speed of 120m/min is less severe than the same type of micro-wear observed at 150 m/min speed, supported with Barnes [41] similar findings. Therefore, micro-abrasion, BUE
50、 and micro-fatigue were activated under wet condition while, adhesion, high levels micro-abrasion, and no BUE were under dry cutting. SEM image of (KC313) showing build up edge under 120m/min (wet). (a) SEM image of (KC3 13) showing micro-fatigue, and micro-abrasion (wet). Figure 5-4 SEM image
51、s of (KC313) at 120m/min (wet), (a) SEM image of (KC313). showing build up edge, (b) SEM image of (KC313) showing micro-fatigue and micro-abrasion 33 Figure 5-5 is for a cutting tool machined at 90m/min, that presents a good capture of one stage of tool life after the BUE has been plucked away. Th
52、e bottom part of the flank side shows massive metal adhesion from the work piece material. The upper part of the figure at the edge shows edge fracture. To stand over the reason of edge fracture, the zoom-in view with magnification of 2000 times is presented in Figure 5-6A. The micro-fatigue crack i
53、mage can be seen as well as micro-attrition revealed by numerous holes, and supported with Lim et al [31] observations on HSS-TiN inserts. As a result of BUE fracture from the cutting tool edge, small quantities from the cutting tool material is plucked away leaving behind numerous holes. Figure 5-6
54、B is another zoom-in view of the upper part of flank side with a magnification of 1000 times and shows micro-abrasion wear indicated by the narrow grooves. Furthermore, the exact type of micro-wear mechanism appeared at the flank side under 60 m/min. Therefore, in comparison with dry cutting at the
55、cutting speed of 90 m/min and 60 m/min, less micro-abrasion, bigger BUE formation, and higher micro-attrition rate were activated. Figure 5-5 SEM image showing tool edge after buildup edge was plucked away. SEM image showing micro-fatigue crack, and micro-attrition. (a) SEM image showing
56、micro-abrasion. Figure 5-6 SEM images of (KC313) at 90m/min:(a) SEM image showing micro-fatigue crack, and micro-attrition, (b) SEM image showing micro-abrasion. 5.4 Experimental Observations on Wear Mechanisms of Coated Cemented Carbide with TiN-TiCN-TiN Coating in High Speed Wet Machining Inves
57、tigating the wear mechanisms of sandwich coating under wet cutting is presented in this section starting from early stages of wear. Figure 5-7 shows early tool wear starting at the cutting edge when cutting at 410m/min. Edge fracture can be seen, it has started at cutting edge due to non-smooth cont
58、act between tool, work piece, micro-abrasion and stress concentrations. To investigate further the other possible reasons behind edge fracture that leads to coating spalling, a zoom-in view with magnification of 2000 times was taken and presented at Figure 5-8A. Coating fracture can be seen where fr
59、agments of TiN (upper coating) had been plucked away by metal chips. This took place as result of micro-abrasion that led to coating spalling. On the other hand, the edge is the weakest part of the cutting insert geometry and works as a stress concentrator might lead to a cohesive failure on the tra
60、nsient filleted flank cutting wedge region [51, 52]. Both abrasion wear and stress concentration factor leave a non-uniform edge configuration at the micro scale after machining starts. Later small metal fragments started to adhere at the developed gaps to be later plucked away by the continuous ch
61、ip movement as shown in Figure 5-8A. Another view of edge fracture was taken of the same cutting tool with a magnification of 2000 times as shown in Figure 5-8B. It presents fracture and crack at the honed tool edge. A schematic figure indicated by Figure 5-9, presented the progressive coated cuttin
62、g inserts failure starting at the insert edge. It was also noticed during the inserts test that failure takes place first at the inserts edge then progressed toward the flank side. Consequently, a study on optimizing the cutting edge Figure 5-7 SEM image of (KC732) at 410m/min showing edge fractu
63、re and micro-abrasion (wet). SEM image showing edge fracture. (a) SEM image showing fracture and crack at the honed insert edge. Figure 5-8 SEM of (KC732) at 410m/min and early wear stage (wet): (a) SEM image showing edge fracture, (b) SEM image showing fracture and crack at the honed insert
64、 edge. radius to improve coating adhesion, and its wear resistance, might be also a topic for future work. Figure 5-1.0A was taken after tool failure at a speed of 410m/min. It shows completely exposed substrate and severe sliding wear at the flank side. The coating exists at the crater surface a
65、nd faces less wear than the flank side. Therefore it works as an upper protector for the cutting edge and most of the wear will take place at the flank side as sliding wear. Figure 5-10B is a zoom-in view with magnification of 3500 times, and shows coating remaining at the flank side. Nonetheless, m
66、icro-abrasion and a slight tensile fracture in the direction of metal chip flow. Ezugwa et al [28] and Kato [32] have exhibited similar finding. However, the tensile fracture in this case is less in severity than what had been observed at dry cutting. This is due to the contribution of coolant in dropping the cutting temperature, which has reduced the plastic deformation at high temperature as a result. Hence, in comparison with the dry cutting at the same speed, tensile fracture was available w
- 溫馨提示:
1: 本站所有資源如無(wú)特殊說(shuō)明,都需要本地電腦安裝OFFICE2007和PDF閱讀器。圖紙軟件為CAD,CAXA,PROE,UG,SolidWorks等.壓縮文件請(qǐng)下載最新的WinRAR軟件解壓。
2: 本站的文檔不包含任何第三方提供的附件圖紙等,如果需要附件,請(qǐng)聯(lián)系上傳者。文件的所有權(quán)益歸上傳用戶所有。
3.本站RAR壓縮包中若帶圖紙,網(wǎng)頁(yè)內(nèi)容里面會(huì)有圖紙預(yù)覽,若沒(méi)有圖紙預(yù)覽就沒(méi)有圖紙。
4. 未經(jīng)權(quán)益所有人同意不得將文件中的內(nèi)容挪作商業(yè)或盈利用途。
5. 裝配圖網(wǎng)僅提供信息存儲(chǔ)空間,僅對(duì)用戶上傳內(nèi)容的表現(xiàn)方式做保護(hù)處理,對(duì)用戶上傳分享的文檔內(nèi)容本身不做任何修改或編輯,并不能對(duì)任何下載內(nèi)容負(fù)責(zé)。
6. 下載文件中如有侵權(quán)或不適當(dāng)內(nèi)容,請(qǐng)與我們聯(lián)系,我們立即糾正。
7. 本站不保證下載資源的準(zhǔn)確性、安全性和完整性, 同時(shí)也不承擔(dān)用戶因使用這些下載資源對(duì)自己和他人造成任何形式的傷害或損失。
最新文檔
- 市教育局冬季運(yùn)動(dòng)會(huì)安全工作預(yù)案
- 2024年秋季《思想道德與法治》大作業(yè)及答案3套試卷
- 2024年教師年度考核表個(gè)人工作總結(jié)(可編輯)
- 2024年xx村兩委涉案資金退還保證書(shū)
- 2024年憲法宣傳周活動(dòng)總結(jié)+在機(jī)關(guān)“弘揚(yáng)憲法精神推動(dòng)發(fā)改工作高質(zhì)量發(fā)展”專題宣講報(bào)告會(huì)上的講話
- 2024年XX村合作社年報(bào)總結(jié)
- 2024-2025年秋季第一學(xué)期初中歷史上冊(cè)教研組工作總結(jié)
- 2024年小學(xué)高級(jí)教師年終工作總結(jié)匯報(bào)
- 2024-2025年秋季第一學(xué)期初中物理上冊(cè)教研組工作總結(jié)
- 2024年xx鎮(zhèn)交通年度總結(jié)
- 2024-2025年秋季第一學(xué)期小學(xué)語(yǔ)文教師工作總結(jié)
- 2024年XX村陳規(guī)陋習(xí)整治報(bào)告
- 2025年學(xué)校元旦迎新盛典活動(dòng)策劃方案
- 2024年學(xué)校周邊安全隱患自查報(bào)告
- 2024年XX鎮(zhèn)農(nóng)村規(guī)劃管控述職報(bào)告