汽車懸架擺臂鋁合金壓鑄件壓鑄工藝設計機械設計和制造專業(yè)論文設計
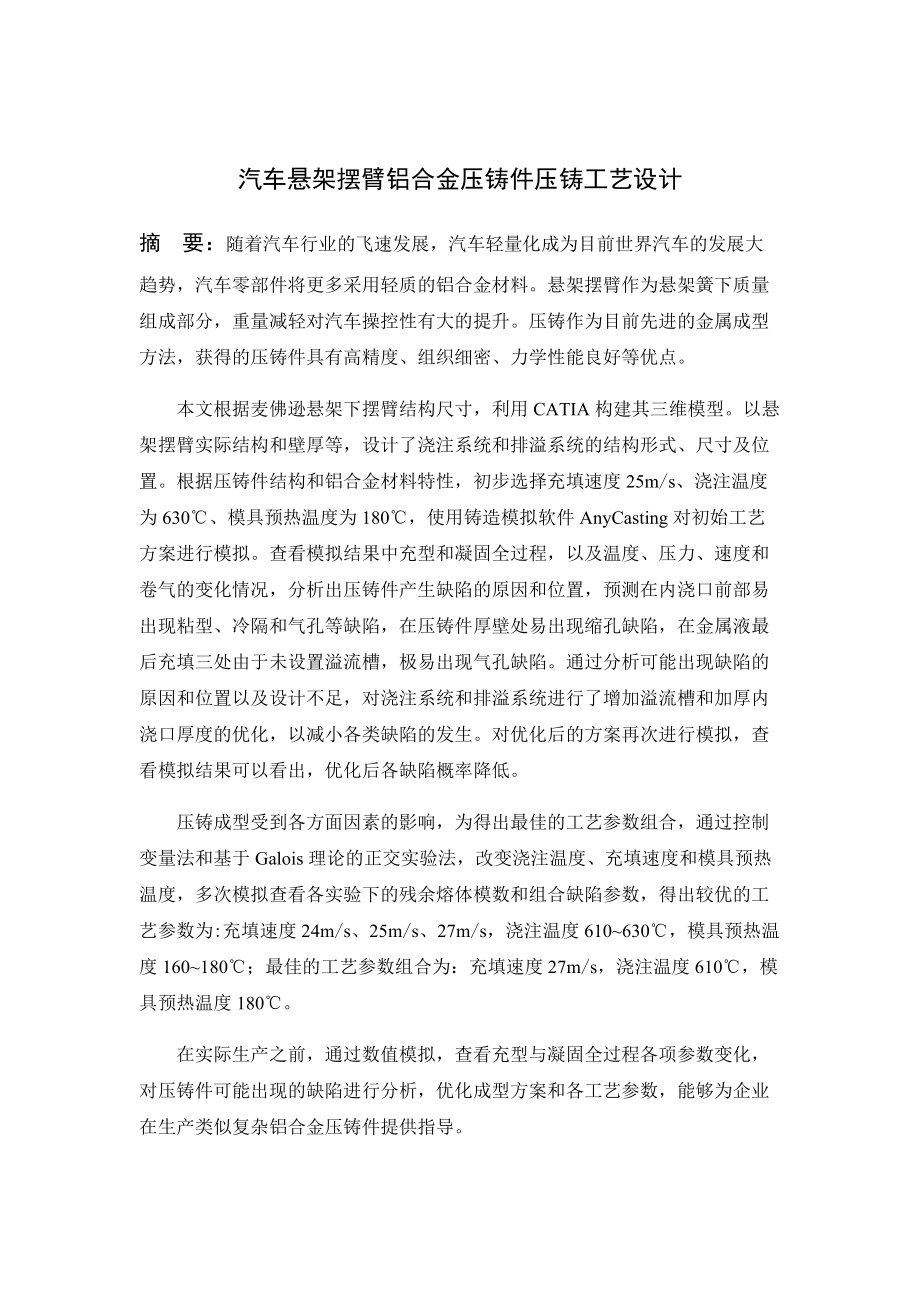


《汽車懸架擺臂鋁合金壓鑄件壓鑄工藝設計機械設計和制造專業(yè)論文設計》由會員分享,可在線閱讀,更多相關(guān)《汽車懸架擺臂鋁合金壓鑄件壓鑄工藝設計機械設計和制造專業(yè)論文設計(81頁珍藏版)》請在裝配圖網(wǎng)上搜索。
1、 汽車懸架擺臂鋁合金壓鑄件壓鑄工藝設計 摘 要:隨著汽車行業(yè)的飛速發(fā)展,汽車輕量化成為目前世界汽車的發(fā)展大趨勢,汽車零部件將更多采用輕質(zhì)的鋁合金材料。懸架擺臂作為懸架簧下質(zhì)量組成部分,重量減輕對汽車操控性有大的提升。壓鑄作為目前先進的金屬成型方法,獲得的壓鑄件具有高精度、組織細密、力學性能良好等優(yōu)點。 本文根據(jù)麥佛遜懸架下擺臂結(jié)構(gòu)尺寸,利用CATIA構(gòu)建其三維模型。以懸架擺臂實際結(jié)構(gòu)和壁厚等,設計了澆注系統(tǒng)和排溢系統(tǒng)的結(jié)構(gòu)形式、尺寸及位置。根據(jù)壓鑄件結(jié)構(gòu)和鋁合金材料特性,初步選擇充填速度25m/s、澆注溫度為630℃、模具預熱溫度為180℃,使用鑄造模擬軟件AnyCasting對初
2、始工藝方案進行模擬。查看模擬結(jié)果中充型和凝固全過程,以及溫度、壓力、速度和卷氣的變化情況,分析出壓鑄件產(chǎn)生缺陷的原因和位置,預測在內(nèi)澆口前部易出現(xiàn)粘型、冷隔和氣孔等缺陷,在壓鑄件厚壁處易出現(xiàn)縮孔缺陷,在金屬液最后充填三處由于未設置溢流槽,極易出現(xiàn)氣孔缺陷。通過分析可能出現(xiàn)缺陷的原因和位置以及設計不足,對澆注系統(tǒng)和排溢系統(tǒng)進行了增加溢流槽和加厚內(nèi)澆口厚度的優(yōu)化,以減小各類缺陷的發(fā)生。對優(yōu)化后的方案再次進行模擬,查看模擬結(jié)果可以看出,優(yōu)化后各缺陷概率降低。 壓鑄成型受到各方面因素的影響,為得出最佳的工藝參數(shù)組合,通過控制變量法和基于Galois理論的正交實驗法,改變澆注溫度、充填速度和模具預熱溫
3、度,多次模擬查看各實驗下的殘余熔體模數(shù)和組合缺陷參數(shù),得出較優(yōu)的工藝參數(shù)為:充填速度24m/s、25m/s、27m/s,澆注溫度610~630℃,模具預熱溫度160~180℃;最佳的工藝參數(shù)組合為:充填速度27m/s,澆注溫度610℃,模具預熱溫度180℃。 在實際生產(chǎn)之前,通過數(shù)值模擬,查看充型與凝固全過程各項參數(shù)變化,對壓鑄件可能出現(xiàn)的缺陷進行分析,優(yōu)化成型方案和各工藝參數(shù),能夠為企業(yè)在生產(chǎn)類似復雜鋁合金壓鑄件提供指導。 關(guān)鍵詞:擺臂;鋁合金;壓鑄;模擬;缺陷;工藝參數(shù)優(yōu)化 Diecastingprocessdesignforaluminumalloydiecasting
4、 ofautomobilesuspensionswingarm Abstract:Withtherapiddevelopmentoftheautomobileindustry,automotivelightweighthasbecomethedevelopmenttrendoftheworldsautomobiles.Die-castingtechnologyanddie-castingaluminumalloyarewidelyusedinthekeypartsofautomobiles.Suspensionswingarmisusedasthemasscomponentofthesus
5、pensionspring,andtheweightreductiongreatlyimprovesthevehiclehandling.Asanadvancedmetalformingmethod,thediecastinghastheadvantagesofhighprecision,finestructureandgoodmechanicalproperties. Inthispaper,CATIAisusedtoconstructa3dmodelofMcPhersonsuspensionbasedonitsstructuresize.Basedontheactualstructure
6、andwallthicknessofsuspensionswingarm,thestructureform,sizeandpositionofpouringsystemandoverflowsystemaredesigned. Preliminaryselectionpouringtemperatureis630℃,thefillspeedof25m/s,mouldpreheatingtemperatureis180℃,usingAnyCastingcastingsimulationsoftwareforsimulatingtheinitialsolution,andbylookingatt
7、hefillingprocess,solidificationprocesschanges,changesintemperature,pressure,velocityandvolumeairconditionandsoon,analysesthereasonsofthecastingdefectsandposition,predictaself-adhesiveisseeninsidethefrontgate,coldinsulation,porosityandotherdefects,causingshrinkagecavitydefectsincastingthickwallplace,
8、attheendoftheliquidmetalfillingthreeplacesduetonotsettheoverflowgroove,appeareasilyblowholedefects.Byanalyzingthecausesandlocationsofpossibledefectsandthedesigndeficiencies,thepouringsystemandoverflowsystemareoptimizedbyincreasingtheoverflowgrooveandthickeningtheinnergatethicknesstoreducetheoccurren
9、ceofvariousdefects.Theoptimizedschemewassimulatedagain,andthesimulationresultsshowedthattheprobabilityofeachdefectdecreasedafteroptimization. Formingtechnologyundertheinfluenceofthefactors,obtainsthebesttechnologicalparametersforcombination,throughthecontrolvariablemethodandtheorthogonalexperimentm
10、ethod,basedonthetheoryoftheGaloischangespeedandmouldpreheatingtemperature,pouringtemperature,fillingsimulationoftheresidualmeltunderchecktheexperimentmanytimesmodulusandcompositedefectparameters,itisconcludedthattheoptimalprocessparametersasfollows:thepouringtemperatureof610~630℃,thefillspeed24m/s,2
11、5m/s,27m/s,mouldpreheatingtemperature160~180℃;Thebestcombinationofprocessparametersis:pouringtemperature610℃,fillingspeed27m/s,moldpreheatingtemperature180℃. Beforeactualproduction,throughnumericalsimulation,variousparameterchangesinthewholeprocessofmoldfillingandsolidificationcanbeobserved,possibl
12、edefectsofcastingscanbeanalyzed,andformingschemesandprocessparameterscanbeoptimized,whichcanprovideguidanceforenterprisesintheproductionofsimilarcomplexaluminumalloydiecasting. Keywords:Swingarm;Aluminumalloy;Diecasting;Simulation;Thedefect;Process parameteroptimization 目錄 第一章 緒論 1 1.1壓鑄概述 2
13、 1.2壓鑄技術(shù)的發(fā)展及趨勢 2 1.2.1壓鑄技術(shù)在國外的發(fā)展 2 1.2.2壓鑄技術(shù)在國內(nèi)的發(fā)展 2 1.2.3壓鑄技術(shù)的發(fā)展趨勢 3 1.3鋁合金壓鑄件概述 4 1.4論文的研究目的、意義和內(nèi)容 6 1.4.1研究目的與意義 6 1.4.2研究內(nèi)容 6 第二章 壓鑄工藝設計及參數(shù)選擇 7 2.1壓鑄件結(jié)構(gòu)設計 7 2.1.1壓鑄工藝對壓鑄件結(jié)構(gòu)的要求 7 2.1.2壓鑄件的結(jié)構(gòu)工藝要素 7 2.2實體建模 8 2.3壓鑄合金的選擇 9 2.3.1 壓鑄合金的選擇 9 2.3.2 壓鑄模材料的選擇 9 2.4壓鑄工藝參數(shù) 11 2.4.1 壓力 11
14、 2.4.2 速度 12 2.4.3 溫度 13 2.4.4 時間 15 2.5壓鑄機簡介及選用 16 2.6 方案設計 18 2.6.1 分型面的設計 18 2.6.2 澆注系統(tǒng)設計 18 2.6.3 排溢系統(tǒng)設計 23 2.7 初始工藝方案 25 2.8 本章小結(jié) 26 第三章 壓鑄模擬及各工藝參數(shù)對壓鑄件產(chǎn)生缺陷的分析 26 3.1 AnyCasting軟件介紹 26 3.2 模流理論 27 3.2.1壓鑄充型過程數(shù)學模型 28 3.2.2壓鑄充型過程數(shù)值模擬技術(shù) 30 3.2.3壓鑄凝固過程數(shù)學模型 31 3.3充型過程數(shù)值模擬 32 3.4 工
15、藝參數(shù)對壓鑄件產(chǎn)生缺陷的分析 33 3.5 本章小結(jié) 37 第四章 壓鑄工藝方案優(yōu)化及最佳工藝參數(shù)組合的確定 37 4.1工藝方案優(yōu)化 37 4.2控制變量法和正交實驗法確定最佳工藝參數(shù)組合 39 4.2.1控制變量法確定較優(yōu)組合參數(shù) 39 4.2.2正交實驗法確定最佳參數(shù)組合 49 4.3本章小結(jié) 55 第五章 結(jié)論與展望 56 5.1 結(jié)論 56 5.2 展望 56 參考文獻 58 致謝 61 第1章 緒論 1.1壓鑄概述 壓力鑄造簡稱為壓鑄,是一種致密、無切屑的金屬快速成型工藝[[1]江
16、昌勇.壓鑄成形工藝與模具設計[M].北京:北京大學出版社,2012. ]。實質(zhì)是金屬液在高壓高速下充填進壓鑄型腔內(nèi),凝固成型后獲得高精度、高致密性且力學性能優(yōu)良的壓鑄件。壓鑄的兩大特點是高壓和高速。壓鑄生產(chǎn)中常用的壓射比壓為20~200MPa;常用充填速度為10~50m/s;由于高壓高速充填,充填時間較短,一般為0.01~0.2s。壓鑄與其他鑄造工藝相比,有下列優(yōu)點[[2]賴華清.壓鑄工藝與模具[M].北京:機械工業(yè)出版社,2005. ]: (1)質(zhì)量精度高:壓鑄件尺寸精度最高可達CT4級;表面粗糙度低;表層組織細密,力學性能優(yōu)良;互換性好;對于復雜和薄壁類的也可以壓鑄。 (2)加工
17、效率高:國內(nèi)使用最廣泛的臥式冷壓機每小時可壓鑄75~87次,機器生產(chǎn)效率快;壓鑄??芍貜褪褂蒙习偃f次,壽命長;易實現(xiàn)大批量和一模多腔生產(chǎn);易實現(xiàn)自動化和機械化。 (3)經(jīng)濟效益好:由于壓鑄件質(zhì)量精度高、表面質(zhì)量優(yōu)良,一般在壓鑄后無需再次加工或較少量加工就可使用,材料利用率高;壓鑄件價格與其他合金材料價格相比更便宜。 1.2壓鑄技術(shù)的發(fā)展及趨勢 1.2.1壓鑄技術(shù)在國外的發(fā)展 在19世紀初期,由于印刷工業(yè)的興起,也萌發(fā)和蘊育了壓鑄業(yè)的誕生。從19世紀初期到中期的一段時間,開始出現(xiàn)將熔融狀態(tài)的金屬壓入容器內(nèi)制造簡易零件。到19世紀中期,陸續(xù)制造出各類用于壓鑄的機械設備。1855年默根瑟勒(
18、Mergen-thaler)以前人專利為基礎,設計出印字壓鑄機,并在之后對該機器進行了優(yōu)化改良,可用于生產(chǎn)簡易的鋅合金壓鑄件。 在20世紀初期,工業(yè)上開始大量使用壓鑄件,隨后壓鑄機也迅速的發(fā)展。1904年法蘭克林(H.H.Franklin)公司壓鑄制造出汽車連桿軸承,開創(chuàng)了壓鑄件在汽車上的應用先例,壓鑄件應用領(lǐng)域由此從印刷工業(yè)逐漸轉(zhuǎn)變?yōu)槠嚬I(yè);1905年多勒(H.H.Doehler)發(fā)明出多用型熱室壓鑄機,該壓鑄機既能壓鑄鋅合金也能壓鑄鉛錫合金;隨后瓦格納(Van Wagner)設計出適用于鋁合金壓鑄的氣壓立式冷壓機。20世紀50年代開始出現(xiàn)大型壓鑄機,使壓鑄行業(yè)更快應用到更多新領(lǐng)域。隨著
19、壓鑄工藝、壓鑄技術(shù)和壓鑄設備的發(fā)展,壓鑄合金的種類也在不斷增多,也促進了壓鑄行業(yè)更加迅速的發(fā)展。 1.2.2壓鑄技術(shù)在國內(nèi)的發(fā)展 與國外先進鑄造國家相比,我國壓鑄行業(yè)起步晚。在1953年左右,我國先后從國外購買少量的壓鑄設備,開始進行壓鑄件的生產(chǎn),我國壓鑄行業(yè)由此誕生。隨后我國壓鑄業(yè)得到快速發(fā)展,50年代末期時,我國開始嘗試改進仿制并自行設計出不同類型的壓鑄機。由于壓鑄行業(yè)技術(shù)生產(chǎn)不規(guī)范,我國在1978年統(tǒng)一了壓鑄技術(shù)規(guī)范,并制定了新系列的壓鑄機和壓鑄合金型號。 從21世紀開始,我國的壓鑄行業(yè)迅速發(fā)展壯大。據(jù)統(tǒng)計,中國此時設計壓鑄產(chǎn)業(yè)的廠商多達7000多家,更有幾十萬的從業(yè)人員,還有遍布
20、全國各地的壓鑄模制造、原材料以及相應的輔助企業(yè),壓鑄生產(chǎn)能力和壓鑄件產(chǎn)量都在世界前列。 我國壓鑄行業(yè)經(jīng)過近半個世紀的蓬勃發(fā)展,目前已成為國家的新興產(chǎn)業(yè)??陀^上來說,我國的壓鑄機質(zhì)量和加工效率,與國外壓鑄先進國家相比存在一定差距,但由于我國壓鑄件應用領(lǐng)域?qū)?、市場大,可為國?nèi)的壓鑄行業(yè)帶來更多機會和空間,我國還擁有充足的有色金屬和長期從事壓鑄工藝研究和實踐的技術(shù)隊伍,這些都是構(gòu)成了我國壓鑄行業(yè)發(fā)展的基礎。我國已經(jīng)初步構(gòu)建完整的壓鑄產(chǎn)業(yè)及其配套產(chǎn)業(yè)鏈的壓鑄工業(yè)基地,正逐步從世界壓鑄行業(yè)大國向壓鑄行業(yè)強國邁進。 1.2.3壓鑄技術(shù)的發(fā)展趨勢 壓鑄技術(shù)的發(fā)展,主要有以下幾大趨勢[[3]陳金誠.21
21、世紀壓鑄展望[J].特種鑄造及有色合金,1999,(4):41-43. ]: (1) 不斷提高合金材料成型機理、工藝研究和充填過程的分析。 (2) 對于各類壓鑄工藝參數(shù)的檢測將不斷提高和完善,計算機控制技術(shù)將廣泛應用在壓鑄技術(shù)上。 (3) 對于大型和形狀復雜的壓鑄件,壓鑄技術(shù)不斷完善成熟,新型半固態(tài)壓鑄技術(shù)有較大的進展,快速原型模樣設計的運用成為新的熱點。 (4) 真空壓鑄和擠壓鑄造壓鑄件的應用領(lǐng)域不斷擴大。 (5) 壓鑄模材料有新的發(fā)展,對于新型鋼種有大的進展。 (6) 壓鑄合金新品種以及復合材料為壓鑄件的應用開辟了新途徑,鎂合金壓鑄件應用將會有大幅度的增長。 (7) 壓鑄單
22、元的完整培植將成為壓鑄技術(shù)的新突破。 1.3鋁合金壓鑄件概述 鋁合金壓鑄件是指采用壓鑄技術(shù)成型后經(jīng)過少量加工得到的鋁合金零件。鋁合金壓鑄件的強度比鑄鐵或鑄鋼大,在高低溫工作情況下,能夠保證良好的力學性能。在承受同樣載荷的情況下,使用鋁合金壓鑄件可以減輕零件的重量,故在汽車上得到越來越廣泛的應用。壓鑄鋁合金除滿足零件的使用和工藝性能、生產(chǎn)條件和使用場合等,還應該具有以下性能: 1 在過熱度要求不高時,應具備優(yōu)良的塑性體流變性能,使熔融金屬液不僅能夠充填復雜型腔,還可以改善壓鑄型腔的工作狀況; 2 裂紋傾向性較小,盡可能減小壓鑄件出現(xiàn)變形和裂紋等缺陷; 3 結(jié)晶溫度范圍穩(wěn)定,可減少
23、壓鑄件出現(xiàn)縮孔和縮松等缺陷; 4 高溫下有良好的固態(tài)強度,可防止開模時壓鑄件出現(xiàn)變形或破裂缺陷; 5 常溫下強度和硬度高,盡可能提升壓鑄件的力學性能; 6 壓鑄時合金材料不與壓鑄型腔發(fā)生反應,防止出現(xiàn)粘型和相互合金化。 根據(jù)添加元素不同可將壓鑄鋁合金分為Al-Si系合金、Al-Mg系合金、Al-Si-Mg系合金和Al-Si-Cu系合金等。 Al-Si系合金由于結(jié)晶溫度范圍和收縮系數(shù)小,其鑄造性能高于其他鋁合金。保證優(yōu)良鑄造性能的前提是要求鑄造合金中共晶體數(shù)量足夠,但過多的共晶體數(shù)量會導致合金脆性增大,從而影響其力學性能。而Al-Si合金中存在的大量Si元素,可改善合金脆性,從
24、而同時保證了良好的鑄造性能和力學性能,目前Al-Si系合金是所有鋁合金中最廣泛的。 A1-Mg系合金具有良好的力學性能和耐腐蝕性,但由于加入了Mg元素,在合金的熔煉時,會加劇夾渣和氧化的傾向,壓鑄時不宜控制,其鑄造性能比較差,在長期使用時會出現(xiàn)開裂的缺陷。綜合來看,Al-Mg系合金的缺點大于其優(yōu)點,所以在實際應用中會受到限制,目前Al-Mg系合金主要用于低力學性能以及外觀特殊和防腐類的壓鑄件上。德國萊茵鋁業(yè)公司研究開發(fā)出了一款名為Magsimal-59的合金,該合金是在AlMgSi合金中增加Si元素的含量。此合金有優(yōu)良的力學性能,且具有高韌性。該合金可應用于高力學性能要求但無需熱處理的結(jié)構(gòu)件
25、上或是懸掛上。 Al-Si-Mg系合金具有良好的力學性能,且比強度、抗疲勞性和耐熱性較好。其中的A357號合金,被大量應用在航空和軍工上[[4]候峻嶺,宋鴻武,楊繼偉,等.高壓開關(guān)殼體用高強鑄造鋁合金的研究[J].鑄造,2007,56(2):130-132. ]。但是國內(nèi)工藝和設備不達標,生產(chǎn)出的合金的拉伸強度和伸長率不能滿足要求。經(jīng)過不斷試驗,米國發(fā)等[[5]米國發(fā),孔留安,朱兆軍,等.高強韌鑄造Al-Si合金A357的成分優(yōu)化[J].輕合金加工技術(shù),2005,33(3):10-12. ]優(yōu)化了A357合金的配比,優(yōu)化后該合金的抗拉強度和伸長率得到顯著提高,趕超了國外的研究水平。Sil
26、afont-36和Castasil-37是德國萊茵鋁業(yè)公司開發(fā)出的兩款不同特性的壓鑄鋁合金,其中的Silafont-36合金主要用在高負荷和高韌性的汽車零件上,Castasil-37在壓鑄時的伸長率和屈服強度高,可用于復雜汽車零部件的壓鑄,這兩款鋁合金的應用前景都十分良好[[6]高鵬. 鋁合金在汽車輕量化中的應用[J]. 工業(yè)技術(shù),2019(2):724. ]。 A1-Si-Cu系合金具有較好的鑄造性能和中等的力學性能。馮俊等人[[7]馮俊,鮑衛(wèi)寧,馮潔.新型鋁硅銅壓鑄合金[J].特種鑄造及有色合金,2002,(壓鑄???:98-99. ]通過添加稀土元素優(yōu)化YL112合金,開發(fā)出新型的
27、Al-Si-Cu-RE壓鑄合金,該合金力學性能較YL112合金優(yōu)很大提高,其耐磨性和抗熱裂性等也較好,主要用于汽車變速箱、發(fā)動機殼體、方向器和活塞等零部件上。下表1-1是各類壓鑄鋁合金的性能和特性。 表1-1 壓鑄鋁合金的性能及其他特性表 合金牌號 YZAlSi10Mg YZAlSi12 YZAlSi10 YZAlSi9Cu4 YZAlSi11Cu3 YZAlSi17Cu5Mg YZAlMg5Si1 合金代號 YL101 YL102 YL104 YL112 YL113 YL117 YL302 抗熱裂性 1 1 1 2 1 4 5 致密性 2
28、 1 2 2 2 4 5 充型能力 3 1 3 2 1 1 5 不粘型性 2 1 1 1 2 2 5 耐腐蝕性 2 2 1 4 3 3 1 加工性 3 4 3 3 2 5 1 拋光性 3 5 3 3 3 5 1 電鍍性 2 3 2 1 1 3 5 陽極處理 3 5 3 3 3 5 1 氧化保護層 3 3 3 4 4 5 1 高溫強度 1 3 1 3 2 3 4 注:1表示最佳,5表示最差。 1.4論文的研究目的、意義和內(nèi)容 1.4.1
29、研究目的與意義 汽車懸架擺臂在汽車行駛中主要傳遞車輪所需各向支撐力,同時,擺臂作為非簧載質(zhì)量,降低重量能夠提高汽車的操作穩(wěn)定性和安全性。汽車懸架擺臂目前多為沖壓件或鑄鐵件,擺臂的重量較重,因此迫切的需要對擺臂進行輕量化設計。鋁合金材料力學性能優(yōu)良,密度較低,且導熱性和吸能性良好,材料還可回收利用。壓鑄是鋁合金材料快速的成型工藝,成型后得到的鋁合金壓鑄件具有高強度、高精度、力學性能良好等優(yōu)點。鋁合金壓鑄件在汽車上的應用越來越廣泛,但在目前都局限應用在一些易于成型的簡單零件上,如發(fā)動機缸體、殼蓋類。 本課題以汽車懸架擺臂為基礎研究對象,使用鋁合金材料運用壓鑄成型技術(shù)進行工藝設計。在工藝設計時,
30、從懸架擺臂的結(jié)構(gòu)和尺寸、鋁合金材料的特性、壓鑄成型影響因素等多方面綜合考慮,使用CATIA進行三維建模、AnyCasting進行數(shù)值模擬,通過查看不同工藝參數(shù)下的模擬結(jié)果,對壓鑄件產(chǎn)生缺陷原因及位置進行分析,優(yōu)化成型方案與工藝參數(shù),最終得到最佳的成型方案與工藝參數(shù)組合。所得到的結(jié)果,可為企業(yè)在使用壓鑄工藝生產(chǎn)類似的復雜汽車零件時提供參考。 1.4.2研究內(nèi)容 本文以普通壓鑄工藝為基礎,根據(jù)理論及經(jīng)驗設計了壓鑄件成型方案,運用數(shù)值模擬模擬分析,預測了壓鑄件缺陷,優(yōu)化了成型方案與工藝參數(shù)。主要研究內(nèi)容如下: (1) 實體建模與成型方案設計 使用CATIA對汽車懸架擺臂進行三維建模;根據(jù)其結(jié)
31、構(gòu)尺寸,結(jié)合理論與生產(chǎn)經(jīng)驗,合理選擇合金材料、模具材料和壓鑄機型號;確定出壓鑄件的分型面,設計澆注系統(tǒng)和排溢系統(tǒng)的結(jié)構(gòu)形式、尺寸和位置;預選出一組合適的工藝參數(shù),確定初始工藝方案; (2) 數(shù)值模擬與缺陷分析 使用AnyCasting對初始工藝方案進行數(shù)值模擬,查看模擬結(jié)果中充型和凝固全過程;根據(jù)溫度、壓力、速度和卷氣的變化情況,預測壓鑄件產(chǎn)生缺陷的位置并分析原因,并根據(jù)預測缺陷和設計不足來優(yōu)化工藝方案; (3)確定最佳工藝參數(shù) 對優(yōu)化后的工藝方案再次模擬,使用控制變量法改變工藝參數(shù)值,多次模擬對比得到較優(yōu)工藝參數(shù);使用正交實驗法對較優(yōu)工藝參數(shù)進行組合,通過再次模擬分析,得出最佳的工藝
32、參數(shù)組合。 第2章 壓鑄工藝設計及參數(shù)選擇 2.1壓鑄件結(jié)構(gòu)設計 2.1.1壓鑄工藝對壓鑄件結(jié)構(gòu)的要求 1. 盡可能使分型面簡單,避免分型面上出現(xiàn)圓角 2. 避免模具局部過厚或過薄 3. 壓鑄件結(jié)構(gòu)設計須利于脫模和抽芯 4. 防止壓鑄件出現(xiàn)變形 2.1.2壓鑄件的結(jié)構(gòu)工藝要素 1. 壁厚 壓鑄件壁厚是否合理與壓鑄件結(jié)構(gòu)尺寸、合金特性和壓鑄工藝參數(shù)的選擇等多方面因素有關(guān)。實踐證明,隨著壁厚的增加,壓鑄件內(nèi)部縮孔和疏松等缺陷會隨之增加,導致壓鑄件的力學性能降低。在設計時,應同時保證壓鑄件有足夠的強度和剛度,且壁厚為薄壁或均勻壁厚。 2.鑄造圓角 鑄造圓角可改善金
33、屬液的流動狀態(tài),減少渦流,便于排出氣體。在設計時,在壓鑄件壁面連接處,無論是什么角,都應設計成圓角,只有預選為分型面處才可不用圓角連接。 3.鑄孔和槽 由于模具的限制,在壓鑄孔和槽時,其尺寸會受到限制,并且尺寸還受型芯位置影響[[8]駱生,許琳.金屬壓鑄工藝與模具設計[M].北京:清華大學出版社,2006. ]。在一般的情況下,壓鑄孔和槽的有關(guān)尺寸可見下表2-1。 表2-1 鑄孔最小孔徑及孔徑與孔深的關(guān)系 合金 最小孔徑d/mm 深度為孔徑d的倍數(shù) 經(jīng)濟上合理的 技術(shù)上可能的 不通孔 通孔 d>5 d<5 d>5 d<5 鋅合金 1.5 0.8
34、 6d 4d 12d 8d 鋁合金 2.5 2.0 4d 3d 8d 6d 鎂合金 2.0 1.5 5d 4d 10d 8d 銅合金 4.0 2.5 3d 2d 5d 3d 4.脫模斜度 脫模斜度與壓鑄件壁厚和合金種類有關(guān)。壓鑄件壁厚較厚和合金收縮率較大時,脫模斜度也應設計較大。為便于壓鑄件脫模,防止表面剮蹭,最好在零件設計時,就應考慮設計合理的脫模斜度。當零件結(jié)構(gòu)上未設計時,應由壓鑄工藝來考慮。 2.2實體建模 實體建模是數(shù)值模擬的基礎[[9]李英民,崔寶俠,方仕中.計算機在材料熱加工領(lǐng)域中的應用[M].北京:機械工業(yè)出版社,2001
35、. ]。根據(jù)懸架擺臂尺寸,用CATIA對懸架擺臂進行三維建模。該懸架擺臂為麥佛遜獨立懸架的下擺臂,在汽車行駛中,擺臂起支撐和導向的作用。在設計時應保證其有足夠的高的強度和剛度,另外考慮到擺臂作為簧下質(zhì)量組成,減輕重量對操控性有提升,故設計時在保證了力學性能和使用性能的前提下,零件應盡可能的輕。尹安東等人[[10]尹安東,王歡,豆力.電動汽車麥佛遜懸架下擺臂輕量化研究[J].汽車科技,2013(1):1-4. ]對懸架擺臂輕量化研究發(fā)現(xiàn),使用5mm的鋁材料與3mm厚的鋼材料,用有限元對其分析對比發(fā)現(xiàn),兩種材料在受到載荷時變形基本一致,且使用鋁材料固有頻率提升,最大應力減少。本設計決定將壁厚由
36、3mm調(diào)整為5mm,以保證擺臂的力學性能。擺臂長度為173mm、寬度為144mm、高度為14mm,中間部分厚度為5mm,平均壁厚約為4.2mm。兩處支點有兩孔,孔徑分別為6mm和14mm。擺臂通過三個部位分別與車架與轉(zhuǎn)向節(jié)下端相連,這些位置厚度較厚,在壓鑄過程中易出現(xiàn)氣孔和疏松等缺陷[[11]姜月明. 某復雜鋁合金鑄件低壓鑄造數(shù)值模擬及工藝優(yōu)化研究[D]. 貴州: 貴州大學,2018. ]。通過對壓鑄件進行壓鑄工藝設計和數(shù)值模擬軟件模擬,分析壓鑄件可能產(chǎn)生缺陷的位置及原因,優(yōu)化設計方案,以減少缺陷的產(chǎn)生,提高壓鑄件綜合性能[[12]R.L.Smith,D.E.Phenice et al.Op
37、timizing Production of a Die Casting by Numerical Simulation of Die Filling and Solidification.Issue of Die Casting Engineer.1993(7-8):16-19. ]。下圖2-1為汽車懸架擺臂三維模型。 圖2-1 汽車懸架擺臂三維模型 2.3壓鑄合金的選擇 2.3.1 壓鑄合金的選擇 壓鑄合金材料的正確選擇關(guān)系到整個工藝設計與數(shù)值模擬,在選擇時應根據(jù)生產(chǎn)設備、生產(chǎn)條件和實際經(jīng)驗等多方面因素來考慮。薄兵[[13]薄兵. 汽車用鋁合金壓鑄件的工藝優(yōu)化與組織及缺陷控制
38、[D]. 南京: 東南大學,2017. ]通過對ADC12鋁合金與AC4CH合金在不同壓鑄工藝下的力學性能對比,得出ADC12鋁合金綜合力學性能最好,所以此壓鑄件的壓鑄合金材料決定選擇A1-Si-Cu系中的ADC12鋁合金。ADC12鋁合金適用于壓鑄復雜壓鑄件,強度高,有良好的力學性能和鑄造性能。下表2-2是ADC12鋁合金的材料性能。 2.3.2 壓鑄模材料的選擇 壓鑄過程中,壓鑄模與高溫高壓金屬液直接接觸,且受熱時間長,金屬液在模具中重復的加熱冷卻和高速沖擊會加劇模具腐蝕和磨損。壓鑄模材料的選擇是十分重要的,合理的選材是保證壓鑄模壽命、延緩模具失效的基礎保證。 選擇的壓鑄模的材料,
39、必須具有較高的耐熱性、耐熱疲勞性、導熱性、耐腐蝕性、抗氧化性和淬透性等,且在高溫下能保持良好的力學性能。為滿足不同壓鑄模對材料性能的要求,通常還需要在材料中加入Cr、W、Ni、Co、Mo、V等元素。 目前國內(nèi)外常用的壓鑄模材料有3Cr2W8V、H13、SKD61、8407、W302和BH3等,結(jié)合壓鑄模材料的優(yōu)缺點分析,最終選擇SKD61來作為壓鑄模材料。SKD61材料加熱溫度為1120~1150℃,熱處理后,硬度要求達到43~47HRC,變形小,可進行滲氮處理,使其有良好耐磨性[[14]潘憲曾. 壓鑄模設計手冊[M]. 北京:機械工業(yè)出版社,2006. ]。下表2-3是鑄鋼材料SKD61
40、的材料性能。 表2-2 ADC12鋁合金材料性能 屬性 值 單位 密度 2.7 g/cm 比熱 0.229998 cal/s*cm*℃ 熱導率 0.219728 cal/s*cm*℃ 固相線溫度 515 ℃ 液相線溫度 580 ℃ 潛熱 92.9066 g/cm*s 動態(tài)粘度 0.0108 cal/g 熱膨脹系數(shù) 2.1e-005 ℃ 凝固收縮體積變化 7.14 % 臨界凝固比率 0.7 表面張力 685 dyne/cm 滲透性 無 cm/s 表2-3 SKD61材料性能 屬性 值 單位 密度 7
41、.85 g/cm 固相線溫度 1403.95 ℃ 液相線溫度 1471.2 ℃ 潛熱 50 g/cm*s 動態(tài)粘度 0.00302634 cal/g 熱膨脹系數(shù) 變量 ℃ 凝固收縮體積變化 3.16 % 臨界凝固比率 0.3 表面張力 1720 dyne/cm 滲透性 無 m 2.4壓鑄工藝參數(shù)及選擇 2.4.1 壓力 壓鑄壓力是壓鑄工藝中重要參數(shù)之一,表現(xiàn)形式有壓射力和壓射比壓。 1. 壓射力 壓射力是指壓射沖頭作用在金屬液單位面積上的力,壓射力在壓鑄周期內(nèi),會隨壓鑄階段變化而發(fā)生改變。 壓射力的計算公式:
42、 (2-1) 式中,F(xiàn)為壓射力(N);p為液壓系統(tǒng)的管路工作壓力(Pa);A為壓鑄機活塞截面積(m),A=D/4 ,其中D為活塞直徑(m)。 2. 壓射比壓 壓射比壓是指充模結(jié)束時壓射沖頭作用在金屬液單位面積上的壓力,其大小與壓鑄機壓室內(nèi)徑和規(guī)格有直接關(guān)系。 壓射比壓的計算公式: (2-2) 式中,p為壓射比壓(Pa);F為壓射力(N);A為壓射沖頭截面積(m),其中d為活塞直徑(m)。 壓射比壓
43、與壓射力成正比,與壓射沖頭截面積成反比,一般可通過調(diào)整壓射力和壓室內(nèi)徑來控制壓射比壓。 3.壓射比壓的選擇 壓射比壓不僅對壓鑄件的質(zhì)量精度和力學性能有影響,還對壓鑄模的使用壽命有影響。在選擇壓射比壓時,應同時考慮壓鑄件的尺寸、形狀、復雜程度、溫度、壁厚、合金特性及排溢系統(tǒng)等,根據(jù)壓鑄件多方面的綜合情況來選擇合適的壓射比壓。我國常用的壓射比壓推薦值可以參考下表2-4選用。 1) 合理的壓射比壓可改善壓鑄件力學性能 隨著壓鑄比壓的提高,壓鑄件內(nèi)部致密性提高,氣泡和孔隙會被壓縮,壓鑄件的強度提高。 2) 提高壓射比壓可改善金屬液對薄壁零件的充型能力 在壓鑄薄壁零件時,由于薄壁件內(nèi)澆口薄,
44、金屬液會受到較大的流動阻力,提前壓射比壓可使金屬液獲得足夠充填速度,防止壓鑄件產(chǎn)生充型不足缺陷。 3) 壓射比壓不應過高,否則會降低壓鑄模壽命 過高的壓射比壓會使熔融狀態(tài)的金屬液加劇沖蝕金屬模,導致壓鑄模壽命降低。 表2-4 常用壓鑄合金壓射比壓推薦值(MPa) 鋅合金 鋁合金 鎂合金 銅合金 一般件 13~20 30~50 30~50 40~50 承載件 20~30 50~80 50~80 50~80 耐氣密件 25~40 80~100 80~100 60~100 電鍍件 20~30 - - - 2.4.2 速度 壓鑄速度分為壓射
45、速度和充填速度。壓射速度指壓射沖頭推動金屬液前進的速度;充填速度是指壓射沖頭推動金屬液前進時通過內(nèi)澆道時的線速度。 金屬液在流經(jīng)澆注系統(tǒng)內(nèi)澆口時的速度可近似認為不變或變化很小,根據(jù)等流量連續(xù)性方程可以得出壓射速度和充填速度的關(guān)系: (2-3) (2-4) 式中,V為壓射速度(m/s);V為充填速度(m/s); A為壓射沖頭截面積(m); A為內(nèi)澆口的截面積(m);d為壓射沖頭的直徑(m)。 充填速度同時受壓射速
46、度、壓射比壓和內(nèi)澆口截面積的影響。根據(jù)水力學原理,壓射比壓和充填速度有如下關(guān)系: (2-5) 式中,為充填速度(m/s);p為壓射比壓(Pa);為阻力系數(shù),一般取=0.358;g為重力加速度(m/s);為液體金屬的假密度(N/m)。 根據(jù)上式2-4可以看出充填速度與壓射比壓成正比關(guān)系,即壓射比壓越大,充填速度越高。 充填速度會直接影響到壓鑄件的質(zhì)量,因此只有選擇合適的充填速度才能保證壓鑄件質(zhì)量合格。充填速度過高會增大壓鑄件內(nèi)部的氣孔缺陷,導致其力學性能降低,同時還會加劇金屬液對壓鑄模的沖
47、擊,導致壓鑄模壽命降低;充填速度過低則會使壓鑄件可能無法成型或是輪廓不清晰。 在選擇充填速度時,對于薄壁類或是表面質(zhì)量精度高以及形狀復雜的壓鑄件,壓射比壓和充填速度都應選擇較高值;而對于厚壁或是內(nèi)部質(zhì)量精度高的壓鑄件,壓射比壓和充填速度都應選擇較低值。下表2-5是我國常用充填速度參照值。 表2-5 常用的充填速度 (m/s) 合金 簡單壁厚壓鑄件 一般壓鑄件 復雜壁厚壓鑄件 鋅合金、銅合金 10~15 15 15~20 鎂合金 20~25 25~35 35~40 鋁合金
48、 10~15 10~25 25~30 2.4.3 溫度 壓鑄溫度分為合金澆注溫度和壓鑄模溫度。 1. 合金澆注溫度 合金澆注溫度指的是高溫熔融金屬液從澆注系統(tǒng)進入壓鑄型腔的平均溫度,一般高于合金液相線20~30℃。過高或過低的澆注溫度,都會影響壓鑄件質(zhì)量精度,使壓鑄件造成缺陷。當澆注溫度過低時,金屬液流動性變差,易出現(xiàn)冷隔、澆不足及流紋等現(xiàn)象;李昭[[15]李昭. 基于數(shù)值仿真的鋁合金壓鑄工藝研究[D]. 長沙:湖南大學,2010. ]通過模擬,得出充填速度相同時,隨著澆注溫度升高,壓鑄件縮孔和縮松減少,力學性能越好。但當澆注溫度過高時,由于熱脹冷縮,合金的收縮性會變大,易使
49、壓鑄件產(chǎn)生裂紋,澆注溫度過高還會導致合金晶粒粗大,造成壓鑄件脆性增大,會導致壓鑄件的質(zhì)量變差。通過實踐證明:壓力較高時,應盡可能降低澆注溫度。該證明可以顯著的提高壓鑄件的質(zhì)量和精度。因壁厚和結(jié)構(gòu)的不同,澆注溫服選取也不同,下表2-6是澆注溫度推薦選取值。 表2-6 各種壓鑄合計澆注溫度 (單位:℃) 合金 壓鑄件壁厚≤3mm 壓鑄件壁厚>3mm 簡單結(jié)構(gòu) 復雜結(jié)構(gòu) 簡單結(jié)構(gòu) 復雜結(jié)構(gòu) 鋅合金 含Al的 420~440 430~450 410~430 420~440 含Cu的 520~540 530~5
50、50 510~530 520~540 鋁合金 含Si的 610~630 640~680 590~630 610~630 含Cu的 620~650 640~700 600~640 620~650 含Mg的 640~660 660~700 620~660 640~670 鎂合金 640~680 660~700 620~660 640~680 銅合金 普通黃銅 870~920 900~950 850~900 870~920 硅黃銅 900~940 930~970 880~920 900~940 2. 壓鑄模的溫度 壓鑄模的溫度一
51、般指模具的表面溫度。在實際的連續(xù)生產(chǎn)過程中,壓鑄模的溫度會隨著時間逐漸升高,對于成型后的壓鑄件伸長率和拉伸強度有所提高,但會使壓鑄件的硬度下降。壓鑄模溫度取值可按下表2-7進行選取。 表2-7 不同壓鑄合金的壓鑄模工作溫度 (單位:℃) 合金 壓鑄件壁厚≤3mm 壓鑄件壁厚>3mm 簡單結(jié)構(gòu) 復雜結(jié)構(gòu) 簡單結(jié)構(gòu) 復雜結(jié)構(gòu) 鋅合金 預熱溫度 130~180 150~200 110~140 120~150 連續(xù)工作保持溫度 180~200 190~220 140~170 150~200 鋁合金 預熱溫度 150~180 200~230
52、 120~150 150~180 連續(xù)工作保持溫度 180~240 250~280 150~180 180~200 鋁鎂合金 預熱溫度 170~190 220~240 150~170 150~180 連續(xù)工作保持溫度 200~220 260~280 180~200 180~200 鎂合金 預熱溫度 150~180 200~230 120~150 170~190 連續(xù)工作保持溫度 180~240 250~280 150~180 200~240 銅合金 預熱溫度 200~230 230~250 170~200 200~230 連
53、續(xù)工作保持溫度 300~325 325~350 250~300 300~350 當壓鑄模的溫度過高時,可能會出現(xiàn)因冷卻緩慢導致壓鑄件不能完全凝固,推出時易出現(xiàn)變形,模具局部卡死等問題。同時也會造成壓鑄件晶粒粗大和金屬液易粘住型腔,從而影響壓鑄件的力學性能和表面質(zhì)量。因此在壓鑄模溫度過高時,應及時的采取高效冷卻措施。 壓鑄模的溫度過低又會使金屬液在凝固過程中產(chǎn)生較大的溫度梯度差,一定程度上可促進壓鑄件的凝固,成型后的壓鑄件晶粒比較細小,組織致密。但壓鑄件快速凝固中會產(chǎn)生較大的收縮應力,導致壓鑄件表面出現(xiàn)裂紋缺陷;壓鑄件凝固過快,無法及時進行補縮來降低縮松等缺陷;壓鑄模溫度過低
54、還會使金屬液激冷急劇,流動性變差,壓鑄件可能無法成型,甚至可能因為激冷引起壓鑄件出現(xiàn)裂紋和開裂,或是壓鑄件表面形成一層硬殼。 壓鑄模的溫度,一般按照下列經(jīng)驗公式進行計算。 (2-6) 式中,t為壓鑄模的溫度(℃);t為液體金屬澆注溫度(℃);Δt為溫度控制公差(一般取25℃)。 2.4.4 時間 壓鑄時間分為充填時間、持壓時間和留模時間。 1. 充填時間 充填時間是指金屬液從澆注系統(tǒng)進入型腔直至充滿整個型腔需要的時間。若要保證最佳充填時間則必須以金屬液在失去流動性之前就已經(jīng)完
55、全充滿型腔為前提,同時還受壓鑄件的結(jié)構(gòu)尺寸、形狀、壁厚、充填速度和內(nèi)澆口截面積等多方面因素的影響。 對于復雜和薄壁壓鑄件,或是表面質(zhì)量要求較高的壓鑄件,充填時間要盡量短一些,以保證壓鑄件有較高的表面質(zhì)量和輪廓清晰度。但充填時間越短,其充填速度相應越高,會造成壓鑄件的致密性較差,型腔中氣體無法及時排出,內(nèi)部氣孔數(shù)量會增多。對于體積較大或是形狀尺寸簡單的壓鑄件,充填時間要選擇的相對長。充填時間越長,充填速度也就越慢,有利于壓鑄中排氣,但壓鑄件的粗糙度較高,表面質(zhì)量較差。壓鑄件平均壁厚與充填時間推薦值見表2-8。 表2-8 壓鑄件的平均壁厚與充填時間的推薦值 壓鑄件平均壁厚 充填時間t/s
56、 壓鑄件平均壁厚 充填時間t/s 1 0.010~0.014 5 0.048~0.072 1.5 0.014~0.020 6 0.056~0.064 2 0.018~0.026 7 0.066~0.100 2.5 0.022~0.032 8 0.076~0.116 3 0.028~0.040 9 0.088~0.138 3.5 0.034~0.050 10 0.100~0.160 4 0.040~0.060 2. 持壓時間 持壓時間是指金屬液充滿型腔后到內(nèi)澆道完全凝固的一段時間,壓射沖頭會給金屬液施加恒定壓力。持壓的作用是壓射沖
57、頭將壓力均勻恒定傳遞給整個型腔中未凝固的金屬,使金屬在凝固中產(chǎn)生的收縮進行補償,以保證壓鑄件能在壓力下結(jié)晶,獲得致密性較高的組織。 持壓時間與合金材料和壓鑄件壁厚有直接關(guān)系。厚壁、高熔點和結(jié)晶溫度區(qū)間大的壓鑄件,持壓時間應較長,若持壓時間不足,會使壓鑄件內(nèi)部產(chǎn)生疏松或是出現(xiàn)孔洞的缺陷;而對于薄壁、熔點低和結(jié)晶溫度范圍小的壓鑄件,可以選擇較短的持壓時間。 3.留模時間 留模時間是指持壓結(jié)束到開模的一段時間。合理的留模時間,可使金屬液在型腔中充分冷卻,保證了壓鑄件的強度和剛度,同時也避免開模時出現(xiàn)變形或拉裂等缺陷的發(fā)生。留模時間受合金性能、壓鑄件壁厚和結(jié)構(gòu)尺寸等多方面影響,在選擇時以
58、壓鑄件推出不發(fā)生變形和開裂的最短時間為宜。 留模時間過短,會造成壓鑄件強度不足,對較差強度的合金還可能出現(xiàn)表面氣泡的缺陷。但留模時間過長,則會造成壓鑄件因溫度過低,收縮變大,壓鑄件在推出時阻力也會變大,同時也會使壓鑄機的生產(chǎn)效率降低。 2.5壓鑄機簡介及選用 壓鑄機按照壓室的受熱狀態(tài)分為熱室壓鑄機和冷室壓鑄機。冷室壓鑄機按照壓室和模具的位置方向差異又分為臥式、立式和全立式。 選擇壓鑄機時應首先考慮壓鑄件數(shù)量和種類,其次考慮壓鑄件的工藝參數(shù)和結(jié)構(gòu)。一般是根據(jù)鎖模力來選擇壓鑄機型號。 能夠鎖緊壓鑄模保證其不被脹型力脹開的力稱之為鎖模力。鎖模力必須要大于脹型力在合模方向上的合力,才能保證壓
59、鑄中壓鑄模不會被脹開。 (2-7) 式中,為壓鑄機的鎖模力(KN); 為主脹型力(KN); 為分脹型力(KN); 為安全系數(shù),一般取。 1.主脹型力 主脹型力可由式(2-8)求得 (2-8) 式中,為主脹型力(KN); A為壓鑄件在分型面上的總投影面積(cm); p為壓射比壓(MPa); 一般情況下,增加分型面總投影面積的30%作為澆注系統(tǒng)和排溢系統(tǒng)的面積。壓射比
60、壓可根據(jù)壓鑄件壁厚和復雜程度來選擇。 2.分脹型力 在壓鑄時,金屬液充滿型腔后會產(chǎn)生一定反壓力,該力會作用在型芯端面上,推動型芯活動,通常是在型芯連接處放置楔緊塊來消除。一般情況下,鎖模力足夠或是型芯成行面積不大,分脹型力可不加計算;若需計算,則按照下列式(2-9)計算。 (2-9) 式中,F(xiàn)為法向力引起的脹型力(KN),是各型芯產(chǎn)生的法向力之和;A為型芯端面投影面積(cm);P為壓射比壓(MPa);為楔緊塊的楔緊角。 懸架擺臂屬于復雜件,由表2-4選擇壓射比壓p=50MPa。通過CATIA
61、測得懸架擺臂在分型面上的投影面積約≈2400mm。 (2-10) 預選的壓鑄機鎖模力足夠,分脹型力可不加計算,取。 (2-11) 臥式冷室壓鑄機在壓鑄工藝中占主導地位,應用非常廣泛。臥式冷室壓鑄機對壓鑄件尺寸和合金種類適應范圍廣,操作簡便效率高。本設計選用型號為J113A型號的臥式冷室壓鑄機。下表是J113A型壓鑄機各參數(shù)值。 表2-9 J113A型壓鑄機參數(shù)表 參數(shù)名稱 數(shù)值 參數(shù)名稱 數(shù)值 合型力(kN) 250
62、 壓射速度(m/s) 75 壓射力(kN) 35 壓射比壓(MPa) 48.7 動型板行程(mm) 200 壓室直徑(mm) 30 工作循環(huán)次數(shù) 300 壓鑄模厚度(mm) 120~320 壓鑄件最大投影面積(cm) 50 管路工作壓力(MPa) 7 建壓時間(ms) 25 電機功率(kW) 7.5 2.6 方案設計 2.6.1 分型面的設計 分型面的設計和選擇與壓鑄件成型部位的分布、澆注系統(tǒng)、壓鑄件尺寸精度和表面質(zhì)量、成型工藝條件及壓鑄模的結(jié)構(gòu)和工藝等都有著密切的聯(lián)系。分型面在選擇時應遵循以下基本原則: (1) 分型面應在壓鑄件外輪廓最大截
63、面處; (2) 盡可能在開模后將壓鑄件留在動模上,便于取出壓鑄件; (3) 分型面盡可能設計在同一個平面; (4) 分型面選擇應利于澆注和排溢系統(tǒng)布置,保證金屬液的充填; (5) 分型面選擇應保證壓鑄件的表面質(zhì)量和尺寸精度; (6) 應盡量精簡模具結(jié)構(gòu); (7) 保證活動型芯順利抽出,以及嵌件安放快速簡便。 2.6.2 澆注系統(tǒng)設計 澆注系統(tǒng)是指金屬液在高壓疏導下充填入型腔的一段通道,由內(nèi)澆口、直澆道、橫澆道以及余料等組成。澆注系統(tǒng)對于金屬液充填過程中的壓力、速度、流動狀態(tài)和排溢系統(tǒng)等都有很大影響,直接決定著壓鑄件質(zhì)量和氣密性等,還對壓鑄生產(chǎn)效率和壓鑄模壽命有影響。 (一)
64、內(nèi)澆口 內(nèi)澆口處于澆注系統(tǒng)最后一段通道,與型腔直接相連。其作用是將最佳流動狀態(tài)的金屬液引入型腔中。在設計內(nèi)澆口時,要充分結(jié)合金屬液的流動狀態(tài),盡可能保證壓鑄件減少縮孔和縮松等缺陷。 1. 內(nèi)澆口位置 設計整個澆注系統(tǒng)時首要確定內(nèi)澆口位置選擇是否合適。內(nèi)澆口位置的選擇與壓鑄件結(jié)構(gòu)尺寸和壁厚、合金性能、壓鑄機類型、分型面和壓鑄件力學性能等多方面因素有關(guān),還與金屬液的充填狀態(tài)、充填速度以及預計出現(xiàn)缺陷部位等有關(guān),通過多方面因素綜合考慮后,進而確定出合適的內(nèi)澆口位置[[16]盧宏遠. 壓鑄中計算機模擬澆口位置對金屬液化充型過程的影響[J]. 特種鑄造及有色合金,1994(4):27-30.
65、]。 在選擇內(nèi)澆口位置時,應考慮以下原則: (1) 內(nèi)澆口一般設計在厚壁處,有利于傳遞壓射壓力; (2) 內(nèi)澆口設計時應盡量使金屬液進入型腔后首先充填排氣困難部位; (3) 避免金屬液進入型腔對型壁或型芯直接沖擊,減少金屬液熱能和動能損失; (4) 減少金屬液的曲折迂回,避免渦流和卷氣; (5) 復雜形狀的壓鑄件,內(nèi)澆口盡量設計在型腔中心; (6) 減少金屬液出現(xiàn)分流和合流。金屬液分流再合流會造成沖擊,使渦流、卷氣和氧化夾渣缺陷增多; (7) 內(nèi)澆口不應設置在壓鑄件上精度和表面粗糙度要求較高處。 2.內(nèi)澆口截面積 內(nèi)澆口的截面積一般是以金屬液的流量進行理論計算的。金屬液的流量等于金屬液體積與時間之比,也等于通過內(nèi)澆口處金屬液體積與充滿型腔所用
- 溫馨提示:
1: 本站所有資源如無特殊說明,都需要本地電腦安裝OFFICE2007和PDF閱讀器。圖紙軟件為CAD,CAXA,PROE,UG,SolidWorks等.壓縮文件請下載最新的WinRAR軟件解壓。
2: 本站的文檔不包含任何第三方提供的附件圖紙等,如果需要附件,請聯(lián)系上傳者。文件的所有權(quán)益歸上傳用戶所有。
3.本站RAR壓縮包中若帶圖紙,網(wǎng)頁內(nèi)容里面會有圖紙預覽,若沒有圖紙預覽就沒有圖紙。
4. 未經(jīng)權(quán)益所有人同意不得將文件中的內(nèi)容挪作商業(yè)或盈利用途。
5. 裝配圖網(wǎng)僅提供信息存儲空間,僅對用戶上傳內(nèi)容的表現(xiàn)方式做保護處理,對用戶上傳分享的文檔內(nèi)容本身不做任何修改或編輯,并不能對任何下載內(nèi)容負責。
6. 下載文件中如有侵權(quán)或不適當內(nèi)容,請與我們聯(lián)系,我們立即糾正。
7. 本站不保證下載資源的準確性、安全性和完整性, 同時也不承擔用戶因使用這些下載資源對自己和他人造成任何形式的傷害或損失。
最新文檔
- 經(jīng)營管理之道培訓(經(jīng)營管理的核心價值戰(zhàn)略規(guī)劃與決策制定)
- 班組凝聚力執(zhí)行力培訓(班組長怎樣提升班組的凝聚力和執(zhí)行力)
- 燃放煙花爆竹安全培訓珍惜生命和健康安全燃放煙花爆竹
- 加強廉潔文化建設夯實廉政思想根基(開展廉潔文化建設具有深厚的文化基礎)
- XX學校班主任期末工作總結(jié)教學成果自我管理班級風采
- XX地區(qū)文旅部門新年工作計劃工作目標與愿景工作保障與監(jiān)督
- 2025從常長二字讀懂反腐倡廉(反腐敗斗爭永遠在路上)
- XX地區(qū)糧食部門未來工作計劃糧食安全保障產(chǎn)業(yè)發(fā)展人才隊伍建設
- 在線貸款平臺介紹如何選擇在線貸款平臺
- XX地區(qū)衛(wèi)生部門工作述職匯報工作成果與亮點
- 燃放煙花爆竹安全教育安全燃放的注意事項
- 節(jié)后收心主題班會節(jié)后收心再出發(fā)踔厲奮發(fā)譜新篇
- 四篇:普通黨員觀看《反腐為了人民》之以案促改促治心得體會范文
- 紀委書記(黨員)觀看《反腐為了人民》心得體會三篇匯編
- 2025年春節(jié)集體廉政談話會上的講話范文