廈門大學(xué)材料表面工程第四章
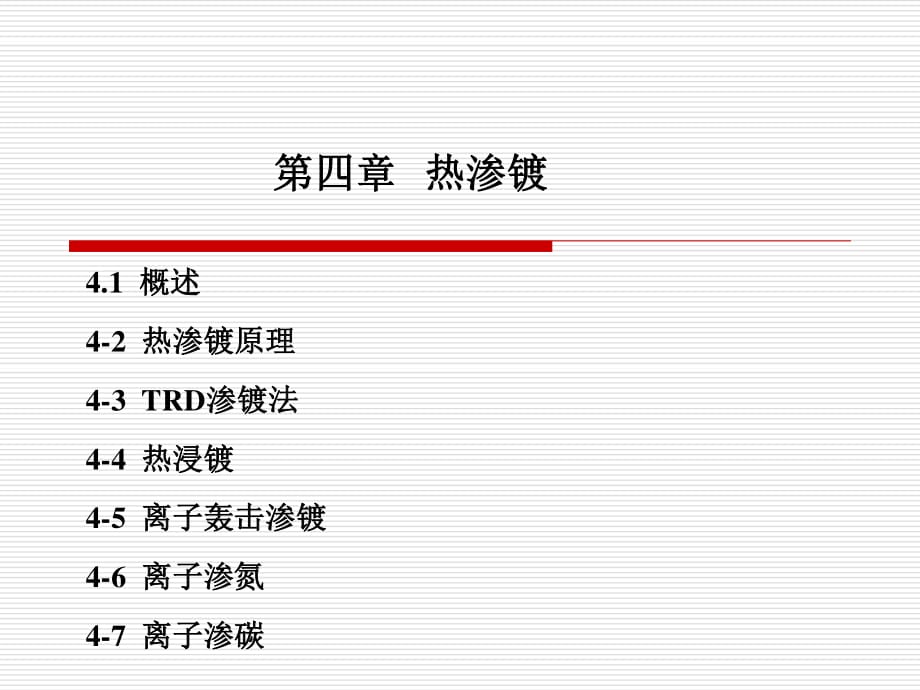


《廈門大學(xué)材料表面工程第四章》由會員分享,可在線閱讀,更多相關(guān)《廈門大學(xué)材料表面工程第四章(68頁珍藏版)》請?jiān)谘b配圖網(wǎng)上搜索。
1、第四章 熱滲鍍 4.1 概述 4-2 熱滲鍍原理 4-3 TRD滲鍍法 4-4 熱浸鍍 4-5 離子轟擊滲鍍 4-6 離子滲氮 4-7 離子滲碳 4.1 概述 用加熱擴(kuò)散的方法把一種或幾種元素滲入基體金屬的表 面 , 得到一擴(kuò)散合金層 , 稱為熱滲鍍 。 該技術(shù)的突出特點(diǎn)是表面強(qiáng)化層的形成主要依靠加熱擴(kuò)散 的作用 , 因而不存在結(jié)合力不足的問題 。 熱滲鍍: 加熱 + 擴(kuò)散 滲入基體 合金層 熱滲鍍材料的選擇范圍很寬 , 滲入不同元素可得到不同組 織和性能的表面 , 這些性能包括:耐腐蝕性 、 耐磨性 、 耐 高溫氧化性等 。 熱滲鍍的方法很多 , 按接觸介質(zhì)劃分有:固滲 、 液滲 、 氣 滲
2、和等離子滲;按復(fù)合手段劃分有:電泳滲 、 料漿滲 、 噴 涂滲 、 電鍍滲和化學(xué)鍍滲等 。 熱滲鍍方法分類詳見下圖: 1 固滲法 粉末包滲法 粉末包滲法是固滲中最普通的方法。 把工件埋人裝有滲層金屬粉末的容器里 進(jìn)行加熱擴(kuò)散,在粉末中加入防粘結(jié)粉 末 (如 Al2O3)和活化劑。 活化劑一般為鹵化物,如 NH4C1, NH4Br, NH4I等。 以 NH4C1為例 , 加熱時(shí)發(fā)生下列反應(yīng): NH4C1 NH3 + HCl 2NH3 3H2 + N2 2HCl + MF MC12 + H2 M是欲滲金屬 。 鹵化物分解生成的 N2和 H2會排除容器內(nèi) 的空氣造成還原氣氛 。 HCl與 M反應(yīng)生成
3、 MCl2, 隨著加熱的進(jìn)行 , MCl2氣化 , 與基體金屬 A反應(yīng) , 生成活性原子 M: MC12 + A AC12 + M 活性金屬原子 M隨后擴(kuò)散滲入基體金屬表面,與基體 形合金鍍層。 粉末包滲法的優(yōu)點(diǎn) : 設(shè)備簡單,操作容易,適用于形狀復(fù)雜的工件的 滲鍍; 缺點(diǎn):效率低,尺寸受限制,溫度高,時(shí)間長,基體金屬 的強(qiáng)度有一定降低。 流化床法 這種方法與粉末包滲法相似 , 不同之處是將工件放于帶 有固體滲劑的流化床內(nèi) , 然后加熱 , 同時(shí)通人鹵氣和運(yùn) 載氣體 (H2, Ar), 使之與流體粒子反應(yīng)產(chǎn)生欲滲金屬的 活性原子滲入工件 。 優(yōu)點(diǎn):傳熱性好 , 滲速快 , 滲層質(zhì)量高并有利于機(jī)
4、械化 和自動化;缺點(diǎn):流化床設(shè)備裝置成本極高 , 運(yùn)轉(zhuǎn)費(fèi)用 大 , 尚未推廣使用 。 2 液滲法 熱浸法 將工件直接浸入某一液態(tài)金屬中 , 經(jīng)較短時(shí)間即形成合 金鍍層 。 當(dāng)浸漬時(shí)間極短時(shí) , 所形成的鍍層只是附著層 而不是擴(kuò)散層 , 與基體金屬結(jié)合不牢固 , 在熱浸后還要 加熱使鍍層進(jìn)行擴(kuò)散 , 以形成合金層 。 優(yōu)點(diǎn):設(shè)備簡單 , 操作容易 , 被廣泛采用 。 這種方法多用于鋼鐵制品的鍍鋅 、 鍍鋁 、 鍍錫等 。 熔燒法 把滲鍍金屬或合金粉末加粘結(jié)劑后制成料漿,再將料 漿均勻涂敷于工件表面上,干燥后在惰性氣體或真空 環(huán)境中以稍高于料漿熔點(diǎn)的溫度加熱燒結(jié),通過液 -固 界面擴(kuò)散而形成合金層
5、。 與熱浸法相比,該法能獲得成分和厚度都很均勻的滲 層,同時(shí)具有熱傳遞性好、滲速快等特點(diǎn)。 鹽浴法 鹽浴法是在金屬鹽熔融液體中加入 V, Nb, Cr, Ti, Ta 等鐵合金粉末,然后把含有較高 C, N的鋼件浸入,在 800 1250C溫度下,經(jīng)過 0.5 10 h的時(shí)間后,可在表 面上形成一極硬的金屬的碳氮化合物薄層,從而賦予工 件表面很高的耐磨性。 3 氣滲法 首先把工件加熱到滲劑原子在基體中能產(chǎn)生顯著擴(kuò)散的 溫度 , 然后把含有滲鍍金屬鹵化物 (MCl2)的氫氣通人 , 氣體和表面接觸時(shí) , 工件表面的金屬 A和氫與 MCl2發(fā)生 反應(yīng) 。 MCl2 + A ACl2 + M MCl
6、2 + H2 2HCl + M 反應(yīng)生成的活性原子 M滲人工件表面 。 實(shí)現(xiàn)氣滲工藝大致可分為兩大類: 一類是滲鍍金屬同工件不在同一空間,用氫氣做載體把欲 滲金屬的鹵化物運(yùn)載到工件表面; 另一類是滲鍍金屬同工件在同一空間,使 HCl氣體先流過 被加熱了的滲劑金屬產(chǎn)生金屬氯化物氣體,隨后使氯化物 氣體流經(jīng)金屬表面,置換出活性原子 M,進(jìn)行滲鍍。 優(yōu)點(diǎn):滲層厚度均勻,易控制,對異形件和小孔結(jié)構(gòu)的滲 鍍效果好,且無粉塵,勞動條件好。 4 離子轟擊滲鍍法 離子轟擊滲鍍法是利用物質(zhì)的第四態(tài) 等離子體進(jìn)行滲 鍍。等離子體是利用低真空下氣體輝光放電獲得的,因 為離子活性比原子高,加上電場的作用,因此滲速較高
7、, 質(zhì)量較好。 但是該法除離子氮化已經(jīng)成熟,包括滲碳在內(nèi)的離子滲 金屬尚在開發(fā)之中。 5 復(fù)合滲 復(fù)合滲是固滲的發(fā)展,即采用各種鍍層手段先在工件表面制造一固相 涂層,然后把工件連同涂層一起加熱。 包括: 電泳滲 料漿滲 噴鍍滲 電鍍滲 化學(xué)鍍滲 真空滲鍍 4-2 熱滲鍍原理 4-2-1 熱滲鍍的基本過程 一般說來熱滲鍍的基本過程應(yīng)包括四個(gè)步驟 。 介質(zhì)中發(fā)生化學(xué)反應(yīng) , 以提供界面反應(yīng)所需要的反應(yīng)物; 反應(yīng)物通過擴(kuò)散輸運(yùn)至金屬表面,此稱為外擴(kuò)散; 反應(yīng)物中的某些粒子被金屬表面吸附,并發(fā)生界面反應(yīng); 界面反應(yīng)產(chǎn)生的活性原子為金屬表面層吸收并向縱深遷移,達(dá)到一 定的深度,此稱內(nèi)擴(kuò)散。 在這四個(gè)步驟
8、中,最關(guān)鍵的是進(jìn)行最慢的步驟,即控制步 驟。 步驟速度快,不會對整個(gè)過程產(chǎn)生阻礙作用。 步驟雖然是一個(gè)擴(kuò)散過程,但此擴(kuò)散是在氣態(tài)或液態(tài)下進(jìn) 行,擴(kuò)散速率要遠(yuǎn)遠(yuǎn)大于元素在固態(tài)內(nèi)的擴(kuò)散,因而也不可 能成為控制步驟。 后兩個(gè)步驟都有可能成為過程中的控制步驟。可根據(jù)滲層深 度和時(shí)間的關(guān)系來判定究竟是步驟還是是控制步驟。 大部分滲鍍處理的控制步驟是內(nèi)擴(kuò)散,因此提高溫度可加 速擴(kuò)散的進(jìn)行。但如果界面反應(yīng)是控制步驟,則僅靠提高 溫度就未必會收到加速的效果。 一般來說,在初始階段,金屬表面上的濃度較低,界面反 應(yīng)大多是控制步驟;到一定的程度,滲鍍元素在表面的濃 度高達(dá)某一值后,滲層厚度的增長主要靠內(nèi)擴(kuò)散來進(jìn)行
9、, 因此擴(kuò)散成了控制步驟。 4-2-2 滲層的形成條件 滲層是基體金屬和滲入元素原子混合或化合組成的薄合金層 , 形成 條件為: (a) 滲入元素必須能與基體金屬形成固溶體或金屬間化合物; (b) 滲入元素與基體金屬必須保持緊密的接觸,即滲入元素可在界 面被吸附; (c) 必須保持一定的溫度,使原子獲得足夠的擴(kuò)散動力; (d) 生成活性原子的化學(xué)反應(yīng)必須滿足一定的熱力學(xué)條件。 滲層能否形成,關(guān)鍵在于滲入元素能否與基體金屬形成 有一定濃度變化范圍的二元合金相。形成這種相后,才 可能造成濃度差,從而使?jié)B入元素獲得擴(kuò)散所需要的驅(qū) 動力。 影響固溶體或金屬間化合物形成的因素主要有:原子相 對大小,原子
10、間的化學(xué)親合力,點(diǎn)陣類型以及相對原子 價(jià)。多數(shù)情況下,可通過原子相對大小初步判定固溶體 滲層形成的可能性。 4-3 TRD滲鍍法 TRD (Surface Coating by Thermo-Reactive Deposition and Diffusion) 稱為熱反應(yīng)沉積和擴(kuò)散的表面覆層法, 簡稱為 TRD滲鍍法或 TD法。 應(yīng)用最廣泛的是用熔鹽浸鍍法在工件表面上涂覆 VC, NbC, CrxCy等碳化物。 4-3-1 處理方法 TRD處理的設(shè)備如圖 4-4所示。 將 70 90的硼砂放人耐熱鋼坩堝中熔融后,向坩堝中加入可形成 欲鍍覆的碳化物的物質(zhì)。例如欲涂 VC時(shí),加入 Fe-V的合金粉
11、末或 V2O5粉末,將含碳的鋼件浸入此鹽浴中,在 800 1200C保溫 110 h, 便得到了僅由碳化物鍍覆的表面層。碳的來源完全依靠鋼中自身的碳 向外擴(kuò)散。 4-3-2 影響涂層厚度的因素 影響涂層厚度的主要因素是鹽浴溫度 、 處理時(shí)間和鋼中的含 碳量 。 鍍層成長的速率主要取決于碳原子的擴(kuò)散速率 , 有下列關(guān)系 式: 2 = A t e -Q RT 式中, 為涂層厚度, t為浸鍍時(shí)間, T為浸鍍溫度, Q為碳 擴(kuò)散活化能 鋼中的含碳量越高,溫度越高,鍍層增厚越快。 4-3-3 鍍層性能 鍍層特點(diǎn): 1硬度 : 高 2耐磨性 : 好 3抗熱粘結(jié)性 : 良好 4抗剝離性 : 良好 5 抗氧化
12、及耐蝕性:一般具有良好的抗氧化及耐蝕性 , 隨鍍覆的碳化物種類的不同而不同 。 6 韌脆性 :與淬火回火鋼大體處于同一水平 。 4-4 熱浸鍍 4-4-1 熱鍍鋅 1 鍍層形成理論 熱鍍鋅是一種經(jīng)濟(jì)實(shí)惠的材料保護(hù)工藝 , 其形成要經(jīng)歷如下 步驟: 鐵基表面被鋅液溶解形成鐵鋅合金相層; 合金層中的鋅原子進(jìn)一步向基體擴(kuò)散 , 形成鋅鐵固溶體; 合金層表面包絡(luò)一薄鋅層 。 熱鍍鋅層的組織由內(nèi)向外按下列順序排列: 與鋼基體相接的是 相,即 Zn在 Fe中的固溶體 (Zn-Fe合金 ); 由 相 向外,是化合物 相, Fe3Zn10,硬度 515 HV,質(zhì)脆; 再向外是 1化合物相, FeZn7, 成柵
13、狀分布, 硬度 454 HV, 韌性好;再向外是 相, FeZnl3,硬度不高 (270 HV),性脆; 最外層是 相,即純 Zn層,該層是鋼鐵件從鋅液中取出時(shí), 在合金層上粘附的液體鋅凝固而成。 熱鍍鋅的工藝就是調(diào)整各相的比例,得到結(jié)合力高、致密且 具有良好外觀的鍍鋅層。 2 熱鍍鋅的方法 目前工業(yè)上應(yīng)用的熱鍍鋅方法有: 干法熱 、 氧化還原法 、 濕法 、 鉛鋅法 、 單面熱鍍鋅等多種 。 應(yīng)用最多的是干法熱鍍鋅和氧化還原法熱鍍鋅 。 干法熱鍍鋅 干法熱鍍鋅是先把預(yù)處理后的清潔工件進(jìn)行溶劑處理, 干燥后再把工件浸入熔融鋅液中去。 溶劑處理的目的是去除工件表面上殘存的鐵鹽,將預(yù) 處理后新生成
14、的銹層溶解,活化鋼件表面,提高鋅液 浸潤鐵基體的能力,增加鍍層的結(jié)合力。 鋅的熔點(diǎn)是 419.5 , 在熱鍍鋅工業(yè)中把鋅液溫度分為 5個(gè) 區(qū)域: 1) 在 480 以下 , 鋅液對基體鐵溶解緩慢 , 工業(yè)上一般不 采用; 2) 在 540 左右 , 鋅液對鐵溶解力很強(qiáng) , 可用于鍍灰鑄鐵 工件; 3) 495 左右 , 這是鋅液對鐵的惡性溶解溫度 , 鍍層疏松 , 是熱鍍鋅的禁區(qū); 4) 620 左右 , 鐵鋅結(jié)合層很快形成 , 是鋼鐵件熱鍍鋅的 最佳溫度; 5) 660 以上 , 鐵急劇溶解 , 工件表面掛不上鋅 , 這是應(yīng) 避免的溫度 。 干法熱鍍鋅允許有較高的含鋁量,因此鋅液表面能生成一
15、 層薄 (0.1m) A12O3保護(hù)膜,防止鋅液氧化。 加鋁還可得到塑性較高的鍍鋅層。 氧化還原法熱鍍鋅 該法取消了堿洗 、 酸洗和溶劑處理等表面預(yù)處理 。 其工藝過程為先使鋼件通過氧化性氣氛的預(yù)熱爐 (爐內(nèi) 加熱溫度為 440 460 ), 再把工件送進(jìn)還原性氣氛 爐中把氧化皮還原并加熱到規(guī)定的溫度 , 接著將鋼件浸 人約 440 460 溫度的鋅液中進(jìn)行鍍鋅 。 3 熱鍍鋅層的性能 鍍鋅層的防護(hù)性能表現(xiàn)在兩個(gè)方面: 1、 鋅在大氣中能在表面形成一層致密 、 堅(jiān)固 、 耐蝕 的 ZnCO33Zn(OH)3保護(hù)膜 , 保護(hù)了下面的 Zn和 Fe免于腐蝕; 2、 對于局部損壞處有陰極保護(hù)的作用
16、。 4熱鍍鋅的應(yīng)用 熱鍍鋅不僅適用于較小的工件 (如螺母、螺栓、彈簧等標(biāo) 準(zhǔn)件 ),而且還能用于鍍鋅鋼管、鋼板、鋼絲的大批量生 產(chǎn)。 目前該工藝正廣泛地應(yīng)用于在大氣和海洋中工作的鋼鐵 構(gòu)件上。 4-4-2 熱滲鍍鋁 當(dāng)鋼中含鋁量高于 8時(shí),其表面能形成致密的鋁氧化膜, 有良好的抗氧化性和抗蝕性。但鋼中含這樣高的鋁時(shí)就會變 脆。 采用滲鋁的方法既可保持鋼件心部的韌性,又可提高表面 的抗氧化性和抗蝕性。 1熱浸鋁 熱浸鍍鋁是當(dāng)前最受重視的滲鋁方法 。 把預(yù)處理過的工件浸 人熔融的 鋁浴中保溫一定時(shí)間取出 , 使其表面滲入一層鋁 。 (1) 熱浸鋁機(jī)理 當(dāng)液態(tài)鋁與鐵接觸時(shí) , 由于相界面 反應(yīng)首先生
17、成 FeAl3化合物;此后 繼續(xù)擴(kuò)散 , FeAl3層加厚 , 由于濃度 起伏 , FeAl3表 面上出現(xiàn) Fe2Al5微區(qū); 隨著 Al的進(jìn)一步 擴(kuò)散 , Fe2Al5相不 斷擴(kuò)大成柱狀晶 , F e A l 3 相逐 漸減少。 (2) 浸鋁層的組織特點(diǎn) 基本可分為兩層: 最外層為富 A1層,成分基本同鋁液; 次層是 Al, Fe合金層,主要是金屬化合物 Fe2Al5相,還有 少量 FeAl3相, Fe2Al5相呈舌狀伸人鋼中。 Fe2Al5相質(zhì)硬而脆,要盡可能抑制其生長,一股把其控制 在滲層的 1/10范圍內(nèi)為好。 控制浸鍍溫度 (700 730 ),加入 2 6的 Si或加入 0.6 的
18、 Be都有助于減少 Fe2Al5的厚度。 2其它滲鍍鋁的方法 固體粉末滲鋁 固體粉末滲鋁是將滲鋁工件埋在粉末狀的滲鋁劑中, 然后加熱到 900 1050 保溫?cái)?shù)小時(shí)即可,優(yōu)點(diǎn)是設(shè)備 簡單,操作方便,特別適合于機(jī)械的零部件;缺點(diǎn)是 工件尺寸受到限制,效率不高。 滲鋁劑一般由三部分組成: 鋁粉或鋁鐵合金粉;氧化鋁粉,起稀釋填充和防止金屬粉 末粘結(jié)的作用;氯化銨 (活化劑 )。 工件可以是鋼鐵件,也可以是鎳基和鈷基高溫合金,還可 用于鈦合金、銅合金及鉬、鈮等難熔金屬。 鋼的滲鋁是通過下列反應(yīng)實(shí)現(xiàn)的: 2NH4Cl 2HCl + N2 + 3H2 6HCl + 2Al 2A1C13 + 3H2 Fe
19、+ A1C13 FeCl3 + A1 滲劑可按表 4-2配制。 噴鍍滲鋁法 把熱噴涂鋁后的工件在 800 1000 溫度下保溫 5h,讓 Al進(jìn) 行擴(kuò)散,稱為噴鍍滲鋁。該處理不僅改善了噴鋁層與基體 表面的結(jié)合強(qiáng)度,還提高了噴 Al層的密度。 料漿滲鋁法 料漿滲鋁是由固體粉末滲鋁法發(fā)展而來的一種工藝方法。 將滲鋁劑調(diào)成糊狀,然后涂刷在工件表面上,在 120 時(shí)烘 干,再加熱到 1000 左右進(jìn)行擴(kuò)散滲鋁。 氣體滲鋁法 氣體滲鋁是在密封的貫通式爐或井式爐中進(jìn)行,滲鋁氣氛 為鋁的鹵化物,反應(yīng)機(jī)理基本同固體粉末法,氣氛可以從 爐外通人,也可以在爐內(nèi)制取。該法質(zhì)量穩(wěn)定,效率較 高。 其它滲鋁法 上面介紹
20、的五種方法已在我國應(yīng)用,還有下述一些方法正在 研究中: 電泳滲鋁法: 先用電泳法將鋁粉均勻地沉積在工件表面上, 再加熱擴(kuò)散制成鍍層。電泳沉積鋁的溶液是由鋁粉 (10m)、 無水乙醇和三氯化鋁組成的,配比時(shí)按每升乙醇含鋁粉 50g、 三氯化鋁約 5 8g配制。工件為陰極,鋁板為陽極。 快速電加熱滲鋁法 有三種快速滲鋁工藝: (1)高頻加熱熱噴涂之后的工件; (2)在滲鋁氣氛中用高頻電流加熱工件; (3)在活性膏劑中用高頻感應(yīng)加熱工件。 該滲鋁法可使?jié)B鋁周期從幾十小時(shí)縮短為幾分鐘甚至 幾十秒鐘,且可改善鋁層質(zhì)量,實(shí)現(xiàn)自動化生產(chǎn),是 近十幾年出現(xiàn)的一種滲鋁新工藝。 3滲鋁層的性能 各種滲鋁法形成的滲
21、層基本上可用圖 4-6來表示。 滲鋁層具有特殊的抗氧化性和耐腐蝕性。 抗氧化性能 滲鋁后的鋼與原來未滲鋁的鋼相比,使用溫度可提高 200 。 A3鋼滲鋁后抗高溫氧化性能優(yōu)于 0Crl7Mnl3Mo2N不銹 鋼,與未滲鋁的 A3鋼比較,抗高溫氧化能力提高 100倍 以上。 耐腐蝕性 滲鋁是目前提高鋼材耐硫化物腐蝕最有效的手段之一。在 大氣條件下,滲鋁鋼比熱鍍鋅鋼具有更好的耐蝕性。滲鋁 鋼的腐蝕量僅是熱鍍鋅鋼的 1/10 1/5。使用壽命與滲鋁層 厚度的關(guān)系見表 4-3。 4滲鍍鋁的應(yīng)用 滲鍍鋁主要用于提高機(jī)件的耐熱耐腐蝕壽命,可用于爐 內(nèi)構(gòu)件、煙道、汽車消音器、汽車進(jìn)排氣零部件、高溫石 油化工用
22、換熱器、加熱管、熱風(fēng)管、加熱爐排風(fēng)扇、空氣 預(yù)熱器和熱處理用設(shè)備,以及一切與 H2S, SO2, CO2, H2CO3, HNO3,液 N2,水煤氣接觸的設(shè)備。 4-5 離子轟擊滲鍍 4-5-1 概述 離子轟擊滲鍍是利用低真空中氣體輝光放電產(chǎn)生的離子 轟擊工件表面,使表面成分、組織結(jié)構(gòu)及性能發(fā)生改變 的處理方法。 它與傳統(tǒng)的固、液、氣態(tài)中的滲鍍原理不同,是近幾年 物質(zhì)的第四態(tài) 等離子體在熱滲鍍領(lǐng)域的應(yīng)用。 通過輝光放電獲得的等離子體是正離子、負(fù)離子、分子、 中性原子、電子、光子等各種粒子的復(fù)合體。其中帶電粒 子在電場的作用下作定向運(yùn)動,具有足夠能量的粒子與中 性的氣體原子或分子相撞,使其處于激
23、發(fā)態(tài),成為活性原 子或離子。這些活性原子或離子,比較容易被金屬表面吸 收,進(jìn)入金屬內(nèi)部。 離子轟擊滲鍍的基本方法可示意于圖 4-7 以工件為陰極,容器壁為陽 極,調(diào)節(jié)滲劑送氣和抽氣速 率,使維持 133 1333 Pa的 壓力,極間施以 300 V以上的 直流電壓,使產(chǎn)生輝光放電。 用離子轟擊進(jìn)行滲鍍,有以下優(yōu)點(diǎn): (1) 離子對表面的轟擊可使表面高度活化,且離子和隨離 子一起沖擊表面的活性原子易被表面吸收,因而滲鍍 速度很快。 (2) 可方便地通過調(diào)整滲劑氣成分、有關(guān)電參數(shù)和氣體參 數(shù)控制滲鍍層組織,從而實(shí)現(xiàn)對滲鍍層的要求。 (3) 由于離子的轟擊作用,可以去除氧化膜和鈍化膜,對 于那些易氧
24、化或鈍化的金屬如不銹鋼特別適合。 (4) 輝光放電可均勻地覆蓋于工件表面,因此比較適合形 狀復(fù)雜及多溝槽和孔隙工件的處理。 (5) 易實(shí)現(xiàn)工藝過程的計(jì)算機(jī)控制。 4-6 離子滲氮 可顯著提高鋼鐵零件表面抗磨、耐疲勞和耐腐蝕性的表面處理新工藝。 把被處理的工件放在真空室,抽真空至 13.3 1.33 Pa,充以稀薄的含氮?dú)怏w如熱分解氨 或氮?dú)浠旌蠚怏w,在陰陽極間加上直流高壓 后,氣體被電離而發(fā)生輝光放電,放電過程 中氮和氫離子在高壓電場的作用下,沖向陰 極表面,產(chǎn)生大量的熱把工件加熱到所需的 溫度,同時(shí)氮的離子或原子為工件表面所吸 附,并迅速擴(kuò)散,形成了一定厚度的氮化層。 4-6-1 離子氮化機(jī)
25、理 陰極濺射模型 : 在輝光放電中,具有高能量的氮、氫離子轟擊作為陰極的 工件,一部分離子直接為表面所吸附,滲人工件,另一部 分通過陰極濺射轟擊出電子及鐵、氧等原子。濺射出的鐵 原子與附近的活性氮原子結(jié)合,形成 FeN,被工件吸收。 FeN受到高溫作用和離子的轟擊按照 FeN Fe2N Fe3N Fe4N的順序分解為低價(jià)氮化鐵,同時(shí)析出原子 氮,析出的原子氮向工件內(nèi)部滲入。 4-6-2 離子氮化的應(yīng)用 離子氮化的應(yīng)用范圍很廣,碳鋼、合金結(jié)構(gòu)鋼、高速鋼和 鑄鐵都可以用離子氮化來強(qiáng)化表面。 例如,機(jī)床工業(yè)中用離子氮化大批量的齒輪、絲桿、離合 器、頂針套、軸等。切削工具通過離子氮化,可提高壽命 1.
26、5 2倍,用于連桿、曲軸、輪轂的熱鍛模,壽命提高 140 265。 4-7 離子滲碳 滲碳是一門古老的表面熱處理技術(shù),直到目前仍是提高鋼 鐵表面硬度、耐磨性和疲勞強(qiáng)度的主要的表面處理方法之 一,約占表面強(qiáng)化零件的 70以上。 近幾十年來,滲碳工藝不斷進(jìn)步,由最早的固體滲碳發(fā)展 為氣體滲碳、真空滲碳。 二十世紀(jì) 70年代以后,開始研 究、開發(fā)離子滲碳工藝,并在 80年代中期開始在工業(yè)上 應(yīng)用。 4-7-1 離子滲碳原理 在真空狀態(tài)下,以工件為陰極,施以直流電壓,產(chǎn)生輝光 放電,碳離子轟擊工件表面,把工件表面加熱并被表面吸 收,然后向內(nèi)部擴(kuò)散。 4-7-2 等離子滲碳的特點(diǎn) 1不使晶界氧化:等離子
27、滲碳工件在真空中加熱,而且工 作氣中不含 O2和 H2O,所以不會發(fā)生晶界氧化。 2表面滲碳量容易控制:表面滲碳層深度、碳濃度和晶粒 大小對工件和機(jī)械性能有重大影響,因此必須嚴(yán)格控制。 采用丙烷等離子滲碳可通過氣體流量和等離子體中 C3H8分 壓的高精度控制來控制表面滲碳量。 3多次循環(huán)處理形成復(fù)合硬化層:可以迅速更換滲碳室 的反應(yīng)氣,為達(dá)到 “ 先滲碳后氮化 ” 或 “ 先氮化后滲 碳 ” 的表面硬化目標(biāo),可以對連續(xù)的多循環(huán)處理進(jìn)行 程序控制。 例如:對于 SVS316零件,經(jīng) 950 , 60 min滲碳后, 再進(jìn)行 650 , 30 min高溫氮化處理,表面硬度可 達(dá) HV550 600
28、,硬化深度為 0.2 mm,硬化層的 組織中既有大量碳化物又有大量氮化物。如果單純用 滲碳的方法僅能達(dá) HV400 450的硬度。 4-7-3 等離子滲碳的應(yīng)用 1代替氣體滲碳 等離子滲碳可在比較短的時(shí)間內(nèi)得到高得多的碳濃度,此 外不會出現(xiàn)晶界氧化層和異常滲碳層。 2等離子高濃度滲碳 通常的滲碳表面的 C濃度規(guī)定為 0.8左右。 如果有意地使碳化物在表面層析出,使表面改質(zhì),稱為高 濃度滲碳。 對于含 Cr, Mo, V, Ti合金元素的鋼,當(dāng)有微細(xì)碳化物 析出時(shí),耐磨性會大大提高。 用氣體滲碳進(jìn)行高濃度滲碳時(shí),碳黑會大量沉積于工件表 面和爐壁上,而且含 Cr高的鋼,氣體滲碳時(shí),晶界會 劇烈氧化
29、;而等離子滲碳克服了這些缺點(diǎn)。 3難滲材料的等離子滲碳 高鉻馬氏體和奧氏體鋼,很 難 用一般的滲碳方法滲碳,稱 為難滲材料。等離子滲碳在減壓下進(jìn)行,由于等離子的作用, 使這些材料的滲碳成為可能。 4 高熔點(diǎn)金屬的等離子滲碳 對 W, Cr和 Nb等高熔點(diǎn)金屬進(jìn)行等離子滲碳在表面上可形 成一系列碳化物。 5 熱噴涂層的等離子滲碳 對 Ni基自熔合金和 WC-Co系熱噴涂層進(jìn)行了等離子滲碳, 提高了熱噴涂層的耐磨性。 等離子滲碳具有一系列優(yōu)點(diǎn),應(yīng)用前景廣闊。 到目前應(yīng)用并不普遍,這主要有兩個(gè)原因: ( 1)作為一門新工藝,本身還需進(jìn)一步完善,近些年雖然有 一些研究,但是從深度和廣度來說都還是很不夠的; ( 2)盡管等離子滲碳有許多優(yōu)越性,但更新設(shè)備要相當(dāng)?shù)耐?資。 開發(fā)等離子滲碳的新領(lǐng)域,用于解決傳統(tǒng)的滲碳無法解決的 表面改質(zhì)問題,是今后的研究方向。 作業(yè): 1、熱滲鍍的基本過程是什么?何謂滲鍍的控制步驟。 2、熱滲鍍滲層形成的基本條件是什么?如何根據(jù)基體和 滲入元素的特性來判定滲層形成的可能性? 3、舉出一種熱浸鋅和熱浸鋁的工藝,并說明每一步的理 由。 4、離子氮化的機(jī)理是什么? 5、簡述甲烷等離子 滲碳工藝。
- 溫馨提示:
1: 本站所有資源如無特殊說明,都需要本地電腦安裝OFFICE2007和PDF閱讀器。圖紙軟件為CAD,CAXA,PROE,UG,SolidWorks等.壓縮文件請下載最新的WinRAR軟件解壓。
2: 本站的文檔不包含任何第三方提供的附件圖紙等,如果需要附件,請聯(lián)系上傳者。文件的所有權(quán)益歸上傳用戶所有。
3.本站RAR壓縮包中若帶圖紙,網(wǎng)頁內(nèi)容里面會有圖紙預(yù)覽,若沒有圖紙預(yù)覽就沒有圖紙。
4. 未經(jīng)權(quán)益所有人同意不得將文件中的內(nèi)容挪作商業(yè)或盈利用途。
5. 裝配圖網(wǎng)僅提供信息存儲空間,僅對用戶上傳內(nèi)容的表現(xiàn)方式做保護(hù)處理,對用戶上傳分享的文檔內(nèi)容本身不做任何修改或編輯,并不能對任何下載內(nèi)容負(fù)責(zé)。
6. 下載文件中如有侵權(quán)或不適當(dāng)內(nèi)容,請與我們聯(lián)系,我們立即糾正。
7. 本站不保證下載資源的準(zhǔn)確性、安全性和完整性, 同時(shí)也不承擔(dān)用戶因使用這些下載資源對自己和他人造成任何形式的傷害或損失。
最新文檔
- 隱蔽工程驗(yàn)收要點(diǎn)
- 給排水中水泵揚(yáng)程與壓力的關(guān)系
- 水泥廠燒成回轉(zhuǎn)窯中控操作問題解答
- 地暖安裝注意事項(xiàng)
- 水泥廠中控操作自動化專業(yè)試題(附答案)
- 防水套管的應(yīng)用與分類
- 施工現(xiàn)場職業(yè)健康管理制度
- 常見基坑工程的支護(hù)方式
- 水泥包裝車間各崗位職責(zé)
- 打樁機(jī)的種類
- 水泥磨操作員試題(附答案)
- 鋼結(jié)構(gòu)工程量計(jì)算注意事項(xiàng)
- 水泥控制工試題(附答案)
- 水泥生產(chǎn)工藝類知識考試題(附答案)-
- 鋼結(jié)構(gòu)安裝施工安全技術(shù)交底范文