叉車工作裝置設計(共24頁)
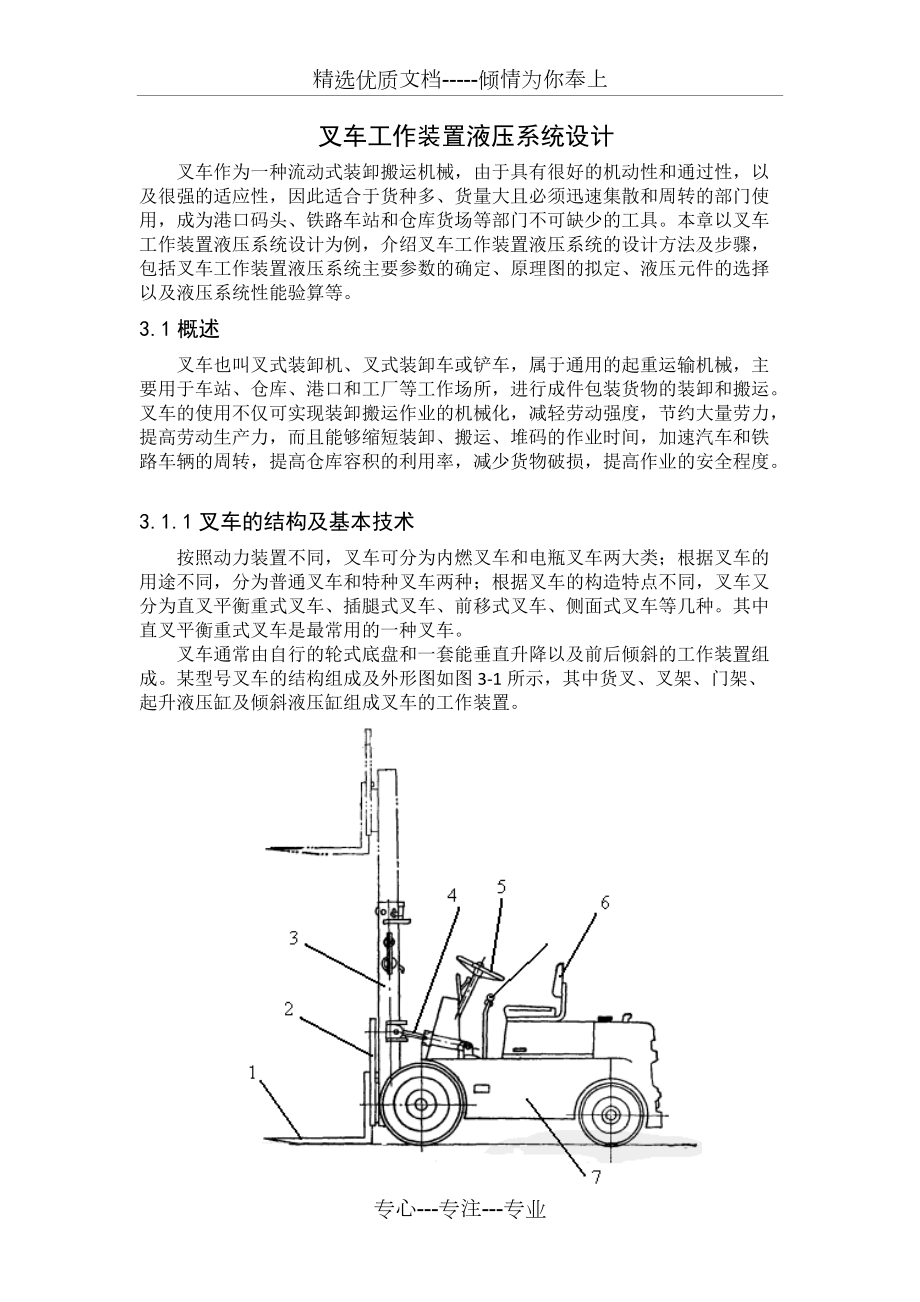


《叉車工作裝置設計(共24頁)》由會員分享,可在線閱讀,更多相關《叉車工作裝置設計(共24頁)(25頁珍藏版)》請在裝配圖網(wǎng)上搜索。
1、精選優(yōu)質文檔-----傾情為你奉上 叉車工作裝置液壓系統(tǒng)設計 叉車作為一種流動式裝卸搬運機械,由于具有很好的機動性和通過性,以及很強的適應性,因此適合于貨種多、貨量大且必須迅速集散和周轉的部門使用,成為港口碼頭、鐵路車站和倉庫貨場等部門不可缺少的工具。本章以叉車工作裝置液壓系統(tǒng)設計為例,介紹叉車工作裝置液壓系統(tǒng)的設計方法及步驟,包括叉車工作裝置液壓系統(tǒng)主要參數(shù)的確定、原理圖的擬定、液壓元件的選擇以及液壓系統(tǒng)性能驗算等。 3.1概述 叉車也叫叉式裝卸機、叉式裝卸車或鏟車,屬于通用的起重運輸機械,主要用于車站、倉庫、港口和工廠等工作場所,進行成件包裝貨物的裝卸和搬運。叉車
2、的使用不僅可實現(xiàn)裝卸搬運作業(yè)的機械化,減輕勞動強度,節(jié)約大量勞力,提高勞動生產(chǎn)力,而且能夠縮短裝卸、搬運、堆碼的作業(yè)時間,加速汽車和鐵路車輛的周轉,提高倉庫容積的利用率,減少貨物破損,提高作業(yè)的安全程度。 3.1.1叉車的結構及基本技術 按照動力裝置不同,叉車可分為內燃叉車和電瓶叉車兩大類;根據(jù)叉車的用途不同,分為普通叉車和特種叉車兩種;根據(jù)叉車的構造特點不同,叉車又分為直叉平衡重式叉車、插腿式叉車、前移式叉車、側面式叉車等幾種。其中直叉平衡重式叉車是最常用的一種叉車。 叉車通常由自行的輪式底盤和一套能垂直升降以及前后傾斜的工作裝置組成。某型號叉車的結構組成及外形圖如圖3-1所示,其中貨
3、叉、叉架、門架、起升液壓缸及傾斜液壓缸組成叉車的工作裝置。 1-貨叉 2-叉架 3-門架及起升液壓缸 4-傾斜液壓缸 5-方向盤 6-操縱桿 7-底盤及車輪 圖3-1 叉車的結構及外形 叉車的基本技術參數(shù)有起重量、載荷中心矩、起升高度、滿載行駛速度、滿載最大起升速度、滿載爬坡度、門架的前傾角和后傾角以及最小轉彎半徑等。 其中,起重量(Q)又稱額定起重量,是指貨叉上的貨物中心位于規(guī)定的載荷中心距時,叉車能夠舉升的最大重量。我國標準中規(guī)定的起重量系列為:0.50,0.75,1.25,1.50,1.75,2.00,2.25,2.50,2.75,3.00,3.50,4
4、.00,4.50,5.00,6.00,7.00,8.00,10.00…….噸。 載荷中心距e,是指貨物重心到貨叉垂直段前表面的距離。標準中所給出的規(guī)定值與起重量有關,起重量大時,載荷中心距也大。例如平衡重式叉車的載荷中心距如表3-1所示。 表3-1 平衡重式叉車的載荷中心距 額定起重量 Q/t Q<1 1≤Q<5 5≤ Q≤ 10 12≤ Q≤ 18 20≤ Q≤ 12 載荷中心距 e/mm 100 500 600 900 1250 起升高度hmax,指叉車位于水平堅實地面上,門架垂直放置且承受額定起重量的貨物時,貨叉所能升起的最大高度,即貨叉升
5、至最大高度時水平段上表面至地面的垂直距離?,F(xiàn)有的起升高度系列為:1500,2000,2500,2700,3000,3300,3600,4000,4500,5000,5500,6000,7000mm。 滿載行駛速度vmax,指貨叉上貨物達到額定起重量且變速器在最高檔位時,叉車在平直干硬的道路上行駛所能達到的最高穩(wěn)定行駛速度。 滿載最大起升速度vamax,指叉車在停止狀態(tài)下,將發(fā)動機油門開到最大時,起升大小為額定起重量的貨物所能達到的平均起升速度。 滿載爬坡度a,指貨叉上載有額定起重量的貨物時,叉車以最低穩(wěn)定速度行駛所能爬上的長度為規(guī)定值的最陡坡道的坡度值。其值以半分數(shù)計。 門架的前傾角β
6、f及后傾角βb,分別指無載的叉車門架能從其垂直位向前和向后傾斜擺動的最大角度。 最小轉彎半徑Rmin,指將叉車的轉向輪轉至極限位置并以最低穩(wěn)定速度作轉彎運動時,其瞬時中心距車體最外側的距離。 在叉車的基本技術參數(shù)中,起重量和載荷中心距能體現(xiàn)出叉車的裝載能力,即叉車能裝卸和搬運的最重貨件。最大起升高度體現(xiàn)的是叉車利用空間高度的情況,可估算倉庫空間的利用程度和堆垛高度。速度參數(shù)則體現(xiàn)了叉車作業(yè)循環(huán)所需要的時間,與起重量參數(shù)一起可估算出生產(chǎn)率。 3.1.2叉車的工作裝置 叉車的工作裝置是叉車進行裝卸作業(yè)的直接工作機構。貨物的叉取卸放、升降堆碼,都靠工作裝置來完成。工作裝置是保證叉車能夠完成工
7、作任務的最重要組成部分之一。叉車工作裝置主要由貨叉、叉架、門架、鏈條和滑輪、起升液壓缸和傾斜液壓缸組成,如圖3-2所示。其中起升液壓缸驅動叉架升降,傾斜液壓缸驅動門架前后傾斜,以滿足工作需要。為了做到一機多用,提高機器效能,除貨叉外,叉車還可配備多種工作屬具。 1-貨叉 2-叉架 3-門架 4-鏈條和滑輪 5-起升液壓缸 6-傾斜液壓缸 圖3-2 叉車工作裝置 叉車工作裝置上的貨叉是直接承載貨物的叉形構件,叉架是一個框架形狀的結構,鏈條的一端與叉架相連,鏈條在繞過起升液壓缸頭部的滑輪后,另一端固定在缸筒或外門架上。起升液壓缸通過滑輪和鏈條,使叉架沿著內門
8、架升降,內門架又以外門架為導軌上下伸縮。為了滿足碼垛作業(yè)對起升高度的要求,同時為了減小叉車自身的高度外形尺寸,門架通常為伸縮式結構,由內外兩節(jié)組成。外門架的下部鉸接在車架或前橋上,借助于傾斜液壓缸的作用,門架可以在前后方向傾斜一定角度。前傾的目的是為了裝卸貨物方便,后傾的目的是當叉車行駛時,使貨叉上的貨物保持穩(wěn)定。 3.1.3叉車的液壓系統(tǒng) 叉車液壓系統(tǒng)是叉車的重要組成部分,其工作裝置、助力轉向系統(tǒng)甚至行走傳動系統(tǒng)等都需要由液壓系統(tǒng)驅動完成。因此,叉車液壓系統(tǒng)的質量優(yōu)劣直接影響著叉車的性能。 某型號叉車工作裝置的液壓系統(tǒng)原理圖如圖3-3所示,該液壓系統(tǒng)有起升液壓缸4、傾斜液壓缸9和屬具液
9、壓缸10三個執(zhí)行元件,由定量泵6供油,多路換向閥(屬具滑閥1、起升液壓缸滑閥7、傾斜液壓缸滑閥8)控制各執(zhí)行元件的動作,單向節(jié)流閥3調節(jié)起升和屬具動作速度,從而驅動工作裝置完成相應的工作任務。 1-屬具滑閥 2-分配閥 3-單向節(jié)流閥 4-起升液壓缸 5-安全閥 6-液壓泵 7-起升液壓缸滑閥 8-傾斜液壓缸滑閥 9-傾斜液壓缸 10-屬具液壓缸 圖3-3 工作裝置液壓系統(tǒng) 由于叉車原動機(內燃機和電動機)的轉速高,扭矩小,而叉車的行駛速度較低,驅動輪的扭矩較大,因此在原動機和驅動輪之間必須有起減速增矩作用的傳動裝置,當叉車在不同載荷和不同作業(yè)條件下工作
10、時,傳動裝置必須要保證叉車具有良好的牽引性能。對于內燃叉車,由于內燃機不能反轉,叉車要想倒退行駛,必須依靠傳動裝置來實現(xiàn)。叉車的傳動裝置有機械式、液力式、液壓式和電動機械式幾種。機械式傳動只能具有有限數(shù)目的傳動比,因此只能實現(xiàn)有級變速。液力傳動效率較機械式低,液壓傳動能夠使傳動系大大簡化,取消機械式和液力式傳動中的傳動軸和差速器。 某型號叉車行走驅動液壓系統(tǒng)的原理圖如圖3-4所示,該液壓系統(tǒng)由變量主液壓泵1供油,執(zhí)行元件為液壓馬達7,主液壓泵的吸油和供油路與液壓馬達的排油和進油路相連,形成閉式回路。雙向安全閥5保證液壓回路雙向工作的安全,梭閥6和換油溢流閥8使低壓的熱油排回油箱,輔助液壓泵2
11、把油箱中經(jīng)過冷卻的液壓油補充到系統(tǒng)中,起到補充系統(tǒng)泄漏和換油的作用,溢流閥4限定補油壓力,單向閥3保證補油到低壓油路中。 1- 主泵 2-輔助液壓泵 3-補換油溢流閥 4-單向閥 5-雙向安全閥 6-梭閥 7-液壓馬達 8-換油溢流 圖3-4 行走驅動液壓系統(tǒng) 叉車作業(yè)時轉向頻繁,轉彎半徑小,有時需要原地轉向。叉車空載時,轉向橋負荷約占車重的60%。為了減輕駕駛員的勞動強度,現(xiàn)在起重量2噸以上的叉車多采用助力轉向——液壓助力轉向或全液壓轉向。液壓助力轉向操作輕便,動作迅速,有利于提高叉車的作業(yè)效率,油液還可以緩沖地面對轉向系的沖擊。 某叉車液壓助
12、力轉向系統(tǒng)原理圖如圖3-5所示,該轉向液壓系統(tǒng)和叉車工作裝置液壓系統(tǒng)屬各自獨立的液壓系統(tǒng),分別由單獨的液壓泵供油。系統(tǒng)中流量調節(jié)閥2可保證轉向助力器穩(wěn)定供油,并使系統(tǒng)流量限制在發(fā)動機怠速運轉時液壓泵流量的1.5倍。隨動閥3與普通的三位四通換向閥基本相同,只不過該閥的閥體與轉向液壓缸缸筒連接為一體,隨液壓缸缸筒的動作而動作。叉車直線行駛時,方向盤處于中間位置,隨動閥3的閥芯也處于中間位置,轉向液壓缸4不動作,叉車直線行駛。當叉車轉彎時,駕駛員轉動方向盤,聯(lián)動機構帶動隨動閥4的閥芯動作,使轉向液壓缸的兩腔分別與液壓泵或油箱連通,液壓缸動作,驅動轉向輪旋轉,叉車轉向,直到液壓缸缸筒的移動距離與閥芯的
13、移動距離相同時,閥芯復位,轉向停止。 1-液壓泵 2-調速閥 3-隨動閥 4-轉向液壓缸 5-濾油器 6-單向閥 7-安全閥 8-油箱 圖3-5 叉車助力轉向液壓系統(tǒng) 叉車液壓系統(tǒng)的設計要能夠保證叉車正常安全地完成工作任務,對液壓系統(tǒng)的工作要求包括: 1超載保護,多路換向閥殼體無裂紋、滲漏;工作性能應良好可靠;安全閥動作靈敏,在超載25%時應能全開,調整螺栓的螺帽應齊全堅固。操作手柄定位準確、可靠,不得因震動而變位。 叉車在裝卸運輸作業(yè)時不允許貨物的重量大于叉車本身的重量。在叉車試驗項目中,有一項是允許叉車以110%的起重量載荷進行聯(lián)合操作,即一邊起升載荷一邊向
14、前運行,以檢驗叉車各部件的協(xié)調性和動作的可能性,此時發(fā)動機的功率、轉速應達到額定的參數(shù),液壓系統(tǒng)應能夠承壓、無滲油。對超載起升保護的性能檢驗是以125%的起重量載荷進行起升動作。此時,液壓系統(tǒng)中應設置相應的超載保護裝置,例如多路換向閥中安全閥。超載時,雖然多路換向閥閥桿動作,但貨叉和125%起重量載荷不得離開地面或離開地面不超過300mm,即叉車應呈現(xiàn)出起升速度下降或起升動作失靈。 2最大下降速度控制,為了提高裝卸效率,如果叉車起升速度增大,滿載下降速度也增大,下降速度過大是危險的,因此叉車液壓系統(tǒng)中應設置下降限速閥,既要控制貨叉的下降速度不超過限定的速度值,又要防止起升液壓缸的高壓橡膠軟管
15、突然爆破時,起升在一定高度的載荷不會和貨叉一起突然落下,損傷貨物或傷人。 3液壓系統(tǒng)管路接頭牢靠、無滲漏,與其它機件不磨碰,橡膠軟管不得有老化、變質現(xiàn)象。 4液壓系統(tǒng)中的傳動部件在額定載荷、額定速度范圍內不應出現(xiàn)爬行、停滯和明顯的沖動現(xiàn)象。 5其它為節(jié)省叉車攜帶電動機,減少叉車附屬設備,從而減小液壓系統(tǒng)的整體尺寸,叉車工作裝置液壓系統(tǒng)可以由叉車發(fā)動機直接驅動液壓泵來提供油源。為適應叉車有可能工作在具有粉塵和沙粒的廠房環(huán)境中,因此應考慮為液壓系統(tǒng)設置合適的過濾器,液壓油的工作溫度應限定在合適的范圍內,叉車的工作環(huán)境溫度一般為-10~45C。 3.1.5本設計要求及技術參數(shù) 1起升裝置液
16、壓系統(tǒng)技術參數(shù) 本設計實例所設計的叉車主要用于工廠中作業(yè),要求能夠提升5000kg的重物,最大垂直提升高度為2m,叉車桿和導軌的重量約為200kg,在任意載荷下,叉車桿最大上升(下降)速度不超過0.2m/s,要求叉車桿上升(下降)速度可調,以實現(xiàn)叉車桿的緩慢移動,并且具有良好的位置控制功能。要求對叉車桿具有鎖緊功能,無論在多大載荷作用下,或者甚至在液壓油源無法供油,油源到液壓缸之間的液壓管路出現(xiàn)故障等情況下,要求叉車桿能夠被鎖緊在最后設定的位置。叉車桿在上升過程中,當液壓系統(tǒng)出現(xiàn)故障時,要求安全保護裝置能夠使負載安全下降。 本設計實例所設計叉車工作裝置中叉車桿起升裝置示意圖如圖3-6所示,
17、由起升液壓缸驅動貨叉沿支架上下運動,從而提升和放下貨物。 圖 3-6 起升裝置 2傾斜裝置液壓系統(tǒng)技術參數(shù) 叉車工作裝置中的叉車桿傾斜裝置示意圖如圖3-7所示,該裝置由傾斜液壓缸驅動貨叉及門架圍繞門架上某一支點做擺動式旋轉運動,從而使貨叉能夠在轉運貨物過程中向后傾斜某一角度,以防止貨物在轉運過程中從貨叉上滑落。傾斜裝置的最大傾斜角為距垂直位置20,最大扭矩為18000Nm,傾斜角速度應限制在1~2/s之間。 圖 3-7 傾斜裝置 設計過程中,除了要滿足叉車工作裝置液壓系統(tǒng)的技術參數(shù)要求外,還應注意叉車的工作條件對液壓系統(tǒng)的結構、尺寸及工作可靠性等其他要求。綜上所述
18、,本設計實例叉車工作裝置液壓系統(tǒng)的設計要求及技術參數(shù)如表3-2所示。 表3-2 技術參數(shù) 技術參數(shù) 起升工作裝置 額定載荷質量m(kg) 5000 最大提升負載質量m(kg) 5200 提升高度h(m) 2 最大提升速度v(m/s) 0.2 傾斜工作裝置 最大傾斜扭矩T(Nm) 18000 傾斜角度α() 20 最大傾斜角速度ω(/s) 1~2 力臂r(m) 1 本設計實例中已給出所設計起升液壓系統(tǒng)和傾斜液壓系統(tǒng)的最大負載和最大速度,因此可直接確定液壓系統(tǒng)的主要參數(shù),無須再對液壓系統(tǒng)進行工況分析,因此該步驟可以省略。 3.3液壓系統(tǒng)
19、的主要參數(shù)確定 本設計實例叉車工作裝置液壓系統(tǒng)包括起升液壓系統(tǒng)和傾斜液壓系統(tǒng)兩個子系統(tǒng),分別由起升液壓缸和傾斜液壓缸驅動,因此首先確定兩個子系統(tǒng)執(zhí)行元件的設計參數(shù)和系統(tǒng)的工作壓力。 3.3.1 起升液壓系統(tǒng)的參數(shù)確定 起升液壓系統(tǒng)的作用是提起和放下貨物,因此執(zhí)行元件應選擇液壓缸。由于起升液壓缸僅在起升工作階段承受負載,在下落過程中液壓缸可在負載和液壓缸活塞自重作用下自動縮回,因此可采用單作用液壓缸。 如果把單作用液壓缸的環(huán)形腔與活塞的另一側連通,構成差動連接方式,則能夠在提高起升速度的情況下減小液壓泵的輸出流量。如果忽略管路的損失,單作用液壓缸的無桿腔和有桿腔的壓力近似相等,則
20、液壓缸的驅動力將由活塞桿的截面積決定。實現(xiàn)單作用液壓缸的差動連接,可以通過方向控制閥在外部管路上實現(xiàn),如圖3-8(a)。為減小外部連接管路,液壓缸的設計也可采用在活塞上開孔的方式,如圖3-8(b)所示。這種測試方法有桿腔所需要的流量就可以從無桿腔一側獲得,液壓缸只需要在無桿腔外部連接一條油路,而有桿腔一側不需要單獨連接到回路中。 (a)管路連接方式 (b)活塞上開孔方式 圖3-8 差動連接液壓缸 起升液壓缸在驅動貨叉和叉架起升時,活塞桿處于受壓狀態(tài),起支撐桿的作用,所以在設計起升液壓缸時,必須考慮活塞桿的長徑比,為保證受壓狀態(tài)下的穩(wěn)定工作,應考慮活塞桿
21、的長徑比不超過20:1。 如果采用液壓缸直接驅動貨叉實現(xiàn)起升和下落的設計方案,則為滿足起升高度要求,根據(jù)表3-2中設計要求,液壓缸活塞桿長度應為2m。根據(jù)上述長徑比設計規(guī)則,活塞桿直徑至少為0.1m。當起升液壓缸使用的活塞桿直徑為100mm時,根據(jù)差動液壓缸輸出力計算方法,此時液壓缸提升負載的有效面積為活塞桿面積(在計算液壓缸受力的時候,活塞上的孔可以忽略。),即 m2 根據(jù)表3-2中設計要求,起升液壓缸需承受的負載力為: N 因此,如果忽略壓力損失和摩擦力,液壓系統(tǒng)所需提供的工作壓力應為: 00000 Pa = 6.5 MPa 這個壓力值比較低,為充分利用液壓系統(tǒng)的傳動優(yōu)勢
22、,應考慮能夠采用更高液壓系統(tǒng)工作壓力的設計方案。但提高壓力后,液壓缸活塞桿直徑會相應變小,如果按活塞桿長徑比的設計規(guī)則,此時活塞桿長度有可能不足以把負載提升到2m的高度,所以必須考慮其他設計方案。 本設計實例通過增加一個傳動鏈條和動滑輪機構對起升裝置前述設計方案進行改進,即如圖3-6所示實施方案。根據(jù)傳動原理,采用這一液壓缸與鏈條和動滑輪結合的機構可以使液壓缸行程減小一半,但是需要對輸出力和活塞桿截面積進行校核。由于傳動鏈條固定在叉車門架的一端,液壓缸活塞桿的行程可以減半,因此活塞桿的直徑也可以相應地減半,但同時也要求液壓缸輸出的作用力為原來的兩倍。即液壓缸行程為1m,活塞桿直徑變?yōu)?0mm
23、。于是,該起升液壓缸的有效作用面積變?yōu)椋? m2 按照前面的計算,由于液壓缸所需輸出的功保持不變,但是液壓缸移動的位移減半,所以液壓缸輸出的作用力變?yōu)樵瓉淼膬杀?,? N 液壓系統(tǒng)所需的工作壓力變?yōu)椋? MPa 取起升液壓缸的工作壓力為13MPa,該工作壓力對于液壓系統(tǒng)來說屬于合適的工作壓力,因此起升液壓缸可以采用這一設計參數(shù)。 起升液壓缸所需的最大流量由起升裝置的最大速度決定。在由動滑輪和鏈條組成的系統(tǒng)中,起升液壓缸的最大運動速度是叉車桿最大運動速度(0.2m/s)的一半,于是 m3/s= 47.1L/min 此時,起升液壓缸活塞桿移動1m,叉車貨叉和門架移動2m,能夠滿足設
24、計需求。 查液壓工程手冊或參考書,取傾斜液壓缸活塞桿直徑d和活塞直徑(液壓缸內徑)D之間的關系為 ,計算得到起升液壓缸的活塞直徑為 =65mm 根據(jù)液壓缸參數(shù)標準,取液壓缸活塞直徑為80mm,液壓缸的行程為1m。 圖3-7傾斜裝置示意圖表明,由貨物重量引起的傾斜裝置負載扭矩總是傾向于使貨叉和支架回復到垂直位置。 3.3.2傾斜液壓系統(tǒng)的參數(shù)確定 叉車的貨叉傾斜工作裝置主要用于驅動貨叉和門架圍繞門架上的支點在某一個小角度范圍內擺動,因此傾斜液壓系統(tǒng)也采用液壓缸作執(zhí)行元件即可。傾斜液壓缸與貨叉門架的連接方式主要有三種,如圖3-9所示。 圖3-9 傾斜液壓缸與門架的三種連接方
25、式 圖3-9叉車傾斜液壓缸與門架的三種連接方式表明,叉車傾斜液壓缸應輸出的作用力不僅取決于叉車貨門架及負載產(chǎn)生的傾斜力矩,而且也取決于液壓缸和門架的連接位置到叉車貨叉門架傾斜支點的距離,因此叉車傾斜液壓缸的尺寸也取決于傾斜液壓缸的安裝位置。液壓缸安裝位置越高,距離傾斜支點越遠,液壓缸所需的輸出力越小。 已知本設計實例傾斜液壓缸連接位置到叉架傾斜支點的距離為r=1m,表3-2中傾斜力矩給定為T=18000Nm,因此傾斜液壓缸所需輸出力Ft為: N 在叉車工作過程中,貨叉叉起貨物后,貨叉和門架在傾斜液壓缸作用下向里傾斜,放下貨物時,貨叉和門架復位,門架恢復豎直位置。因此傾斜液
26、壓缸的作用是單方向的,此外基于減小占用空間和尺寸的考慮,傾斜液壓缸應采用單作用液壓缸。門架的傾斜可由一個液壓缸驅動,也可采用兩個并聯(lián)液壓缸同時驅動,如果采用兩個單作用液壓缸并聯(lián)方式做傾斜液壓系統(tǒng)的執(zhí)行元件,則貨叉和門架的受力更加合理,貨叉不容易產(chǎn)生在貨物的作用下側翻或傾斜的現(xiàn)象,因此工作更加平穩(wěn)。本設計實例傾斜裝置采用兩個單作用液壓缸并聯(lián)方式驅動門架動作。 如果上述傾斜作用力由兩個并聯(lián)的液壓缸同時提供,則每個液壓缸所需提供的作用力為9000N。 在前述起升液壓系統(tǒng)的計算中,工作壓力約為12.99MPa,因此假設傾斜液壓缸的工作壓力與之相近為12MPa,門架和貨叉向后傾斜時,如圖3-7所示,
27、傾斜液壓缸有桿腔一側為工作腔,則傾斜液壓缸的有桿腔作用面積為: m2 由于負載力矩的方向總是使叉車桿回到垂直位置,所以傾斜裝置一直處于拉伸狀態(tài),活塞桿不會發(fā)生彎曲。 查液壓工程手冊或參考書,取傾斜液壓缸活塞桿直徑d和活塞直徑(液壓缸內徑)D之間的關系為 ,有桿腔作用面積為,則傾斜液壓缸活塞直徑可以用如下方法求出。 mmm 根據(jù)液壓缸國家標準,活塞直徑D取圓整后的標準參數(shù)mm,則活塞桿直徑為mm。 此時傾斜液壓缸有桿腔作用面積為 mm2 可見,按照上述確定的活塞和活塞桿尺寸,重新計算得到的有桿腔有效作用面積小于前述按照假定工作壓力計算得到的有桿腔有效作用面積,因此應減
28、小活塞桿直徑或提高傾斜液壓系統(tǒng)的工作壓力。 如果取傾斜液壓缸活塞桿直徑為圓整后的尺寸d=25mm,則有桿腔作用面積為 m2 此時傾斜液壓缸有桿腔作用面積大于原估算面積,因此能夠滿足設計要求。 如果提高傾斜液壓缸的工作壓力,則傾斜液壓缸所需的最大工作壓力為: MPa 傾斜液壓缸無桿腔的有效作用面積為 m2 本設計實例采用提高工作壓力的設計方案進行設計。 傾斜液壓缸的最大運動速度給定為= 2/s,轉換成線速度為 m/s 因此,在貨叉回復垂直位置,兩個傾斜液壓缸處于活塞桿伸出的工作狀態(tài)時,液壓缸所需的總流量為: m3/s=5.3 L/min 傾斜液壓缸需要走過的行程
29、為: m 3.3.3 系統(tǒng)工作壓力的確定 根據(jù)第1章液壓系統(tǒng)工作壓力的確定方法,在確定液壓系統(tǒng)工作壓力時應考慮系統(tǒng)的壓力損失,包括沿程的和局部的壓力損失,為簡化計算,本設計實例中假設這一部分壓力損失約為1.5~2.0 MPa,因此液壓系統(tǒng)應提供的工作壓力應比執(zhí)行元件所需的最大工作壓力高出1.5~2.0 MPa,即 起升液壓系統(tǒng) =13+1.5=14.5MPa 傾斜液壓系統(tǒng) =14.1+1.5=15.6MPa 3.4液壓系統(tǒng)原理圖的擬定 在完成裝卸作業(yè)的過程中,叉車液壓系統(tǒng)的工作液壓缸對輸出力、運動方向以及運動速度等幾個參數(shù)具有一定的要求,這些要求可分別由液壓系統(tǒng)的幾種基本
30、回路來實現(xiàn),這些基本回路包括壓力控制回路、方向控制回路以及速度控制回路等。所以,擬定一個叉車液壓系統(tǒng)的原理圖,就是靈活運用各種基本回路來滿足貨叉在裝卸作業(yè)時對力和運動等方面要求的過程。 3.4.1起升回路的設計 對于起升工作裝置,舉起貨物時液壓缸需要輸出作用力,放下貨物時,貨叉和貨物的重量能使叉車桿自動回落到底部,因此本設計實例起升回路采用單作用液壓缸差動連接的方式。而且為減少管道連接,可以通過在液壓缸活塞上鉆孔來實現(xiàn)液壓缸兩腔的連接,液壓缸不必有低壓出口,高壓油可同時充滿液壓缸的有桿腔和無桿腔,由于活塞兩側的作用面積不同,因此液壓缸會產(chǎn)生提升力。起升液壓缸活塞運動方向的改變通過多路閥或換
31、向閥來實現(xiàn)即可。 為了防止液壓缸因重物自由下落,同時起到調速的目的,起升回路的回油路中必須設置背壓元件,以防止貨物和貨叉由于自重而超速下落,即形成平衡回路。為實現(xiàn)上述設計目的,起升回路可以有三種方案,分別為采用調速閥的設計方案、采用平衡閥或液控單向閥的平衡回路設計方案以及采用特殊流量調節(jié)閥的設計方案,三種方案比較如圖3-10(a)、圖3-10(b)和圖3-10(c)所示。 (a)設計方案一 (b)設計方案二 (c) 設計方案三 圖3-10 起升回路三種設計方案比較 圖3-10(a)中設計方案之一是采用調速閥對液壓缸的下落速度進行控制,該設計方案不
32、要求液壓缸外部必須連接進油和出油兩條油路,只連接一條油路的單作用液壓缸也可以采用這一方案。無論貨物重量大小,貨物下落速度在調速閥調節(jié)下基本恒定,在工作過程中無法進行實時的調節(jié)。工作間歇時,與換向閥相配合,能夠將重物平衡或鎖緊在某一位置,但不能長時間鎖緊。在重物很輕甚至無載重時,調速閥的節(jié)流作用仍然會使系統(tǒng)產(chǎn)生很大的能量損失。 圖3-10(b)中設計方案之二是采用平衡閥或液控單向閥來實現(xiàn)平衡控制,該設計方案能夠保證在叉車的工作間歇,貨物被長時間可靠地平衡和鎖緊在某一位置。但采用平衡閥或液控單向閥的平衡回路都要求液壓缸具有進油和出油兩條油路,否則貨叉無法在貨物自重作用下實現(xiàn)下落,而且該設計方案無
33、法調節(jié)貨物的下落速度,因此不能夠滿足本設計實例的設計要求。 圖3-10(c)中設計方案之三是采用一種特殊的流量調節(jié)閥和在單作用液壓缸活塞上開設小孔實現(xiàn)差動連接的方式,該流量調節(jié)閥可以根據(jù)貨叉載重的大小自動調節(jié)起升液壓缸的流量,使該流量不隨叉車載重量的變化而變化,貨物越重,閥開口越小,反之閥開口越大,因此能夠保證起升液壓缸的流量基本不變,起到壓力補償?shù)淖饔?。從而有效的防止因系統(tǒng)故障而出現(xiàn)重物快速下落、造成人身傷亡等事故。而在重物很輕或無載重時,通過自身調節(jié),該流量調節(jié)閥口可以開大甚至全開,從而避免不必要的能量損失。本設計實例采用這一設計方案限定了貨叉的最大下落速度,保證了貨叉下落的安全。此外,
34、為了防止負載過大而導致油管破裂,也可在液壓缸的連接管路上設置一個安全閥。 3.4.2 傾斜回路的設計 本設計實例傾斜裝置采用兩個并聯(lián)的液壓缸作執(zhí)行元件,兩個液壓缸的同步動作是通過兩個活塞桿同時剛性連接在門架上的機械連接方式來保證的,以防止叉車桿發(fā)生扭曲變形,更好地驅動叉車門架的傾斜或復位。為防止貨叉和門架在復位過程中由于貨物的自重而超速復位,從而導致液壓缸的動作失去控制或引起液壓缸進油腔壓力突然降低,因此在液壓缸的回油管路中應設置一個背壓閥。一方面可以保證傾斜液壓缸在負值負載的作用下能夠平穩(wěn)工作,另一方面也可以防止由于進油腔壓力突然降低到低于油液的空氣分離壓甚至飽和蒸汽壓而在活塞另一側產(chǎn)生
35、氣穴現(xiàn)象,其原理圖如圖3-11所示。傾斜液壓缸的換向也可直接采用多路閥或換向閥來實現(xiàn)。 圖3-11 傾斜回路原理圖 3.4.3 方向控制回路的設計 行走機械液壓系統(tǒng)中,如果有多個執(zhí)行元件,通常采用中位卸荷的多路換向閥(中路通)控制多個執(zhí)行元件的動作,也可以采用多個普通三位四通手動換向閥,分別對系統(tǒng)的多個工作裝置進行方向控制。本設計實例可以采用兩個多路閥加旁通閥的控制方式分別控制起升液壓缸和傾斜液壓缸的動作,其原理圖如圖3-12所示,也可以采用兩個普通的三位四通手動換向閥分別控制起升液壓缸和傾斜液壓缸的動作,如圖3-13所示。本設計實例叉車工作裝置液壓系統(tǒng)擬采用普通的三位四通手動換向
36、閥控制方式,用于控制起升和傾斜裝置的兩個方向控制閥均可選用標準的四通滑閥。 應注意的是,如果起升回路中平衡回路采用前述設計方案三流量調節(jié)閥設計方案,則起升液壓缸只需要一條連接管路,換向閥兩個連接執(zhí)行元件的油口A口和B口只需要用到其中一個即可。如果用到A口,則應注意B口應該與油箱相連,而不應堵塞。這樣,當叉車桿處于下降工作狀態(tài)時,可以令液壓泵卸荷,而單作用起升液壓缸下腔的液壓油可通過手動換向閥直接流回油箱,有利于系統(tǒng)效率的提高。同時為了防止油液倒流或避免各個回路之間流量相互影響,應在每個進油路上增加一個單向閥。 另外,還應注意采用普通換向閥實現(xiàn)的換向控制方式還與液壓油源的供油方式有關,如果采
37、用單泵供油方式,則無法采用幾個普通換向閥結合來進行換向控制的方式,因為只要其中一個換向閥處于中位,則液壓泵卸荷,無法驅動其它工作裝置。 圖3-12 多路換向閥控制方式 圖3-13 普通換向閥控制方式 3.4.4 供油方式 由于起升和傾斜兩個工作裝置的流量差異很大,而且相對都比較小,因此采用兩個串聯(lián)齒輪泵供油比較合適。其中大齒輪泵給起升裝置供油,小齒輪泵給傾斜裝置供油。兩個齒輪泵分別與兩個三位四通手動換向閥相連,為使液壓泵在工作裝置不工作時處于卸荷狀態(tài),兩個換向閥應采用M型中位機能,這樣可以提高系統(tǒng)的效率。 根據(jù)上述起升回路、傾斜回路、換向控制方式和供油方式的設計,
38、本設計實例初步擬定的液壓系統(tǒng)原理圖如圖3-14所示。 1-大流量泵 2-小流量泵 3-起升安全閥 4-傾斜安全閥 5-起升換向閥 6-傾斜換向閥 7-流量控制閥 8-防氣穴閥 9-起升液壓缸 10-傾斜液壓缸 11、12-單向閥 圖3-14 叉車工作裝置液壓系統(tǒng)原理圖 3.5液壓元件選擇 初步擬定液壓系統(tǒng)原理圖后,根據(jù)原理圖中液壓元件的種類,查閱生產(chǎn)廠家各種液壓元件樣本,對液壓元件進行選型。 3.5.1 液壓泵的選擇 圖3-14所示液壓系統(tǒng)原理圖中采用雙泵供油方式,因此在對液壓泵進行選型時考慮采用結構簡單、價格低廉的雙聯(lián)齒輪泵就能夠滿足設計要求。 假定齒輪泵的容積效率為
39、90%,電機轉速為1500r/min,則根據(jù)前述3.3.1和3.3.2中的計算結果,兩個液壓泵的排量可分別計算為: cm3/rev cm3/rev 查閱Sauer-Danfoss公司齒輪泵樣本,如表3-5所示。樣本中可查得,SNP2系列中與3.93 cm3/rev接近的齒輪泵排量為4 cm3/rev,SNP3系列中與34.9 cm3/rev接近的齒輪泵排量有33.1 cm3/rev和37.9 cm3/rev。而33.1 cm3/rev更接近于34.9 cm3/rev,如果選擇排量為37.9 cm3/rev的液壓泵,則工作過程中會有較大的流量經(jīng)過溢流閥溢流回油箱,造成能源的浪費,并有可能產(chǎn)
40、生嚴重的發(fā)熱,因此考慮在SNP3系列中選擇排量為33.1 cm3/rev的齒輪泵。同時考慮到前述計算中假定液壓泵的容積效率為90%,而實際工作過程中,液壓泵的容積效率可能高于90%,尤其是在低負載的時候。在低負荷的時候,電機轉速也有可能會略高于1500 r/min,因此液壓泵的實際輸出流量會增大。 例如,滿負載條件下(電機轉速1500r/min,容積效率90%)的實際流量為: l/min 而半負載條件下(電機轉速1550r/min,容積效率93%)的實際流量為: l/min 大于起升回路所需要的流量47.1 l/min,因此能夠滿足設計要求。 如果選擇排量為37.9 cm3/re
41、v的液壓泵,則滿負載條件下(電機轉速1500r/min,容積效率90%)的實際流量為 l/min 而半負載條件下(電機轉速1550r/min,容積效率93%)的實際流量為 l/min 可見,如果叉車大多數(shù)時間都不工作在滿負載的情況,則選用排量為37.9 cm3/rev的較大液壓泵會造成比較大的溢流損失。 對于傾斜回路的小流量液壓泵,滿載荷條件下(電機轉速1500r/min,容積效率90%)的實際流量為 = 5.4 l/min 大于傾斜回路所需要的流量5.3 l/min,因此能夠滿足設計要求。 表3-5 Sauer-Danfoss齒輪泵樣本 3.5.2 電機的
42、選擇 為減小叉車工作裝置液壓系統(tǒng)的尺寸,簡化系統(tǒng)結構,對于內燃叉車,雙聯(lián)液壓泵可以由發(fā)動機直接驅動。如果叉車上的空間允許,也可以采用電動機驅動雙聯(lián)液壓泵的設計方式。 在叉車工作過程中,為保證工作安全,起升裝置和傾斜裝置通常不會同時工作,又由于起升裝置的輸出功率要遠大于傾斜裝置的輸出功率,因此雖然叉車工作裝置由雙聯(lián)泵供油,在選擇驅動電機時,只要能夠滿足為起升裝置供油的大流量液壓泵的功率要求即可。在最高工作壓力下,大流量液壓泵的實際輸出功率為: =10.8 kW 齒輪泵的總效率(包括容積效率和機械效率)通常在80~85%之間,取齒輪泵的總效率為80%,所需的電機功率為: =13.5 kW
43、 3.5.3液壓閥的選擇 圖3-7中叉車工作裝置液壓系統(tǒng)由雙聯(lián)泵供油,因此對于起升回路,流經(jīng)換向閥、單向閥、溢流閥和平衡閥的最大流量均為47.7 l/min (半載的工況),各元件的額定壓力應大于起升回路的最大工作壓力14.5MPa;對于傾斜回路,流經(jīng)各個液壓閥的最大流量為5.4 l/min,額定壓力應大于傾斜回路的最大工作壓力15.6MPa。流經(jīng)傾斜回路各液壓閥的流量較小,因此傾斜回路中使用的液壓閥可選擇比起升回路中液壓閥通徑更小的液壓閥。 在選擇溢流閥時,由于溢流閥在起升回路和傾斜回路中都是做安全閥,因此其調定壓力應高于供油壓力10%左右,起升回路和傾斜回路溢流閥的調定壓力是不同的,
44、按照前述計算起升回路溢流閥的調定壓力設為16MPa比較合適,傾斜回路溢流閥的調定壓力設為17MPa,具體調定數(shù)值將在后續(xù)壓力損失核算部分中做進一步計算。 查閱相關液壓閥生產(chǎn)廠家樣本,確定本設計實例所設計叉車工作裝置液壓系統(tǒng)各液壓閥型號及技術參數(shù)如表3-6所示。 表3-6 液壓閥型號及技術參數(shù) 序號 元件名稱 規(guī)格 額定流量 L/min 最高使用壓力 MPa 型號 1 三位四通 手動換向閥5 60 31.5 4WMM6T50 2 單向閥11 76 21 DT8P1-06-05-10 3 溢流閥3 120 31.5 DBDH6P-10/200
45、 4 單向閥12 10 21 DT8P1-02-05-10 5 流量調節(jié)閥7 67 31.5 VCDC-H-MF(G1/2) 6 三位四通 手動換向閥6 30 25 DMG-02-3C6-W 7 溢流閥4 12 21 C175-02-F-10 8 背壓閥和防氣穴閥8 120 31.5 MH1DBN 10 P2-20/050M 3.5.4 管路的選擇 本設計實例液壓管路的直徑可通過與管路連接的液壓元件進出口直徑來確定,也可通過管路中流速的建議值進行計算。 根據(jù)第1章中給出的液壓管路流速推薦范圍,假定液壓泵排油管路的速度為5 m/s,液
46、壓泵吸油管路的速度為1 m/s。在設計過程中也應該注意,液壓系統(tǒng)管路中油液的流動速度也會受到油路和裝置工作條件、功率損失、熱和噪聲的產(chǎn)生以及振動等各方面因素的影響。 按照半載工況,大流量泵排油管路中流過的最大流量為 q = 47.7 L/min 則管道的最小橫截面積為: mm2 mm2 mm 為減小壓力損失,管徑應盡可能選大些,所以選用管子通徑為15mm的油管作排油管即可。 大流量泵吸油管路中流過的最大流量為液壓泵的理論流量,即L/min,則管道的最小橫截面積為: mm2 mm2 mm 查液壓管路管徑標準,與上述計算值最接近的實際值為33mm,因此可選用通徑為40m
47、m的油管做大流量泵的吸油管。 3.5.5 油箱的設計 根據(jù)第1章油箱容積估算方法,按照貯油量的要求,初步確定油箱的有效容積 已知雙聯(lián)泵總理論流量為 L/min,對于行走工程機械,為減小液壓系統(tǒng)的體積和重量,在計算油箱的有效容積時取a = 2。因此 L 油箱整體容積為V ==139.125L,查液壓泵站油箱公稱容積系列,取油箱整體容積為150 L。 如果油箱的長寬高比例按照3:2:1設計,則計算得到長、寬、高分別為a=0.075m、b=0.05m、c=0.025m。 3.5.6其他輔件的選擇 叉車工作裝置液壓系統(tǒng)中使用的過濾器包括油箱注油過濾器和主回油路上的回油過濾
48、器。查相關廠家樣本,選擇型號為EF3-40的空氣濾清器,其性能參數(shù)為: 加油流量 21 L/min 空氣流量 170 L/min 油過濾面積 180 mm2 空氣過濾精度 0.279 mm 油過濾精度 125 m 選擇型號為RF-6020L-Y的濾油器作回油過濾器,其性能參數(shù)為: 額定流量 60 L/min 過濾精度 20m 額定壓力 1 MPa 3.6液壓系統(tǒng)的性能驗算 液壓系統(tǒng)原理圖和各液壓元件的型號確定后,可以對所設計叉車工作裝置液壓系統(tǒng)進行系統(tǒng)性能的驗算。 3.6.1壓力損失的驗算 為了
49、能夠更加準確地計算液壓泵的供油壓力和設定溢流閥的調定壓力,分別驗算由兩個液壓泵到起升液壓缸和傾斜液壓缸進口之間油路的壓力損失。 叉車工作裝置液壓系統(tǒng)的壓力損失包括油液流過等徑進油管路而產(chǎn)生的沿程壓力損失,通過管路中彎管和管接頭等處的管路局部壓力損失以及通過各種液壓閥的局部壓力損失。由于叉車工作裝置液壓系統(tǒng)管路較短,彎管和管接頭較少,因此沿程壓力損失和彎管以及管接頭等處的管路局部壓力損失與經(jīng)過各種液壓閥的局部壓力損失相比可以忽略不計,故本設計實例主要核算經(jīng)過各種液壓閥的局部壓力損失。圖3-14原理圖表明,起升回路起升動作過程中液壓閥產(chǎn)生的局部壓力損失主要包括由單向閥11、換向閥5和特殊流量調節(jié)
50、閥7閥口產(chǎn)生的局部壓力損失。 對于起升回路,根據(jù)產(chǎn)品樣本,單向閥11(DT8P1-06-05-10)的開啟壓力為0.035MPa;在流量約為50L/min時,手動換向閥5(4WMM6T50)的壓力損失約為0.5MPa;在流量約為50L/min時,流量調節(jié)閥7(VCDC-H-MF(G1/2))的壓力損失為0.5MPa。因此起升回路進油管路總的局部壓力損失為 1.035 MPa 所以溢流閥調定壓力應為 15.4 MPa 取溢流閥的實際調定壓力為16MPa是適宜的。 對于傾斜回路,使貨叉傾斜過程中,產(chǎn)生局部壓力損失的液壓閥有單向閥12,換向閥6和防氣穴閥8。根據(jù)產(chǎn)品樣本,單向閥12(DT
51、8P1-02-05-10)的開啟壓力為0.035MPa;在流量約為5.4 L/min時,手動換向閥6(DMG-04-3C-W)的壓力損失最大約為0.15MPa;防氣穴閥中單向閥(MHSV10PB1-1X/M)的開啟壓力為0.05MPa則傾斜回路進油管路總的局部壓力損失為 MPa 所以溢流閥實際壓力應為 15.8 MPa 取溢流閥的實際調定壓力為16MPa是適宜的。 3.6.2 系統(tǒng)溫升驗算 起升回路消耗的功率遠大于傾斜回路所消耗的功率,因此只驗證起升回路的溫升即可。 對于起升油路,當叉車桿處于閑置或負載下降時,換向閥工作在中位,液壓泵在低壓下有49.65L/min的流量(理
52、論流量)流回油箱,此時液壓泵處于卸荷狀態(tài),因此液壓泵損失的功率較小。當負載上升時,液壓泵的大部分流量將進入液壓缸。當負載上升達到頂端時,液壓泵以44.7 l/min的額定流量從安全閥溢流回油箱,造成很大的能量損失。 假定液壓泵流量的90%通過安全閥流失,損失的功率為: = 10 kW 造成的油液溫度升高可計算為: 式中 ——液壓油液的密度,取870kg/m3 ——液壓油液的比熱,對于普通的石油型液壓油液,≈(0.4~0.5)4187 J/(kgK),取=2.0 KJ/(kg. K) 如果液壓系統(tǒng)的溫度單位用攝氏度,則油液溫升為 =8.57 ℃ 上
53、述溫升滿足行走機械溫升范圍要求,而且由于這一極端功率損失的情況只是偶爾在貨叉桿上升到行程端點時才出現(xiàn),因此該叉車工作裝置液壓系統(tǒng)不必設置冷卻器。 3.7 設計經(jīng)驗總結 叉車類工程機械或行走機械對液壓系統(tǒng)的要求是安全可靠、效率高、成本低,通過本設計實例,對叉車類工程機械或行走機械液壓系統(tǒng)的設計方法和設計經(jīng)驗總結如下: 1采用低成本的齒輪泵做能源元件,普通的手動換向閥做控制調節(jié)元件,系統(tǒng)造價低。 2為保證系統(tǒng)工作安全,對于有垂直下落工況的液壓系統(tǒng),應采用必要的平衡回路;對于有超越負載(負值負載)的液壓系統(tǒng),應在回油路上采用必要的增加背壓(防氣穴)措施。 3為提高系統(tǒng)的工作效率,降低能耗,對于流量差別較大的支回路,應采用不同流量的液壓泵分別供油的方式。 專心---專注---專業(yè)
- 溫馨提示:
1: 本站所有資源如無特殊說明,都需要本地電腦安裝OFFICE2007和PDF閱讀器。圖紙軟件為CAD,CAXA,PROE,UG,SolidWorks等.壓縮文件請下載最新的WinRAR軟件解壓。
2: 本站的文檔不包含任何第三方提供的附件圖紙等,如果需要附件,請聯(lián)系上傳者。文件的所有權益歸上傳用戶所有。
3.本站RAR壓縮包中若帶圖紙,網(wǎng)頁內容里面會有圖紙預覽,若沒有圖紙預覽就沒有圖紙。
4. 未經(jīng)權益所有人同意不得將文件中的內容挪作商業(yè)或盈利用途。
5. 裝配圖網(wǎng)僅提供信息存儲空間,僅對用戶上傳內容的表現(xiàn)方式做保護處理,對用戶上傳分享的文檔內容本身不做任何修改或編輯,并不能對任何下載內容負責。
6. 下載文件中如有侵權或不適當內容,請與我們聯(lián)系,我們立即糾正。
7. 本站不保證下載資源的準確性、安全性和完整性, 同時也不承擔用戶因使用這些下載資源對自己和他人造成任何形式的傷害或損失。
最新文檔
- 2025年防凍教育安全教育班會全文PPT
- 2025年寒假安全教育班會全文PPT
- 初中2025年冬季防溺水安全教育全文PPT
- 初中臘八節(jié)2024年專題PPT
- 主播直播培訓提升人氣的方法正確的直播方式如何留住游客
- XX地區(qū)機關工委2024年度年終黨建工作總結述職匯報
- 心肺復蘇培訓(心臟驟停的臨床表現(xiàn)與診斷)
- 我的大學生活介紹
- XX單位2024年終專題組織生活會理論學習理論學習強黨性凝心聚力建新功
- 2024年XX單位個人述職述廉報告
- 一文解讀2025中央經(jīng)濟工作會議精神(使社會信心有效提振經(jīng)濟明顯回升)
- 2025職業(yè)生涯規(guī)劃報告自我評估職業(yè)探索目標設定發(fā)展策略
- 2024年度XX縣縣委書記個人述職報告及2025年工作計劃
- 寒假計劃中學生寒假計劃安排表(規(guī)劃好寒假的每個階段)
- 中央經(jīng)濟工作會議九大看點學思想強黨性重實踐建新功