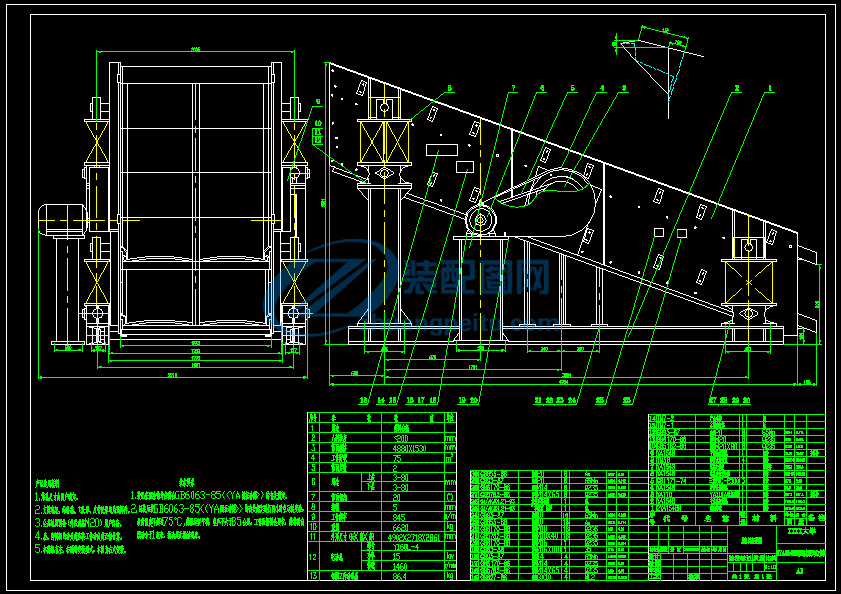

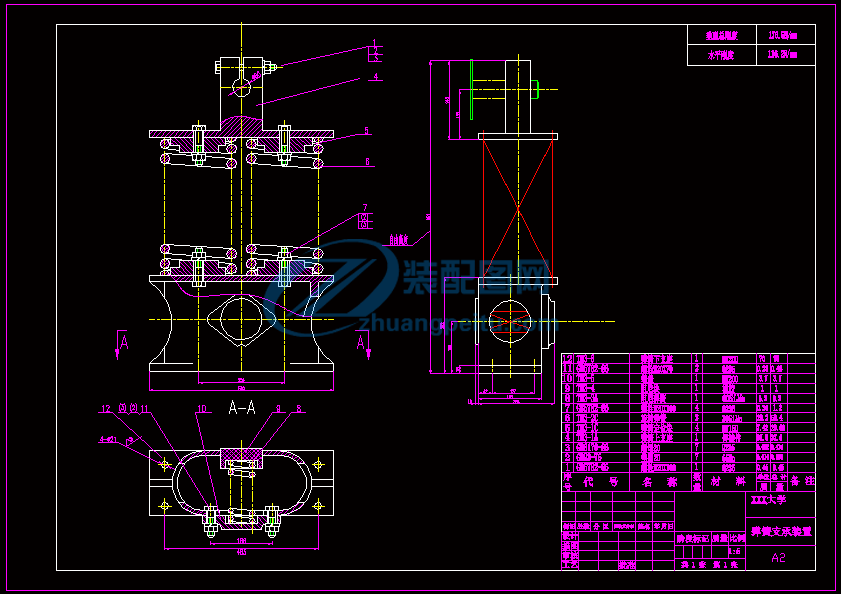
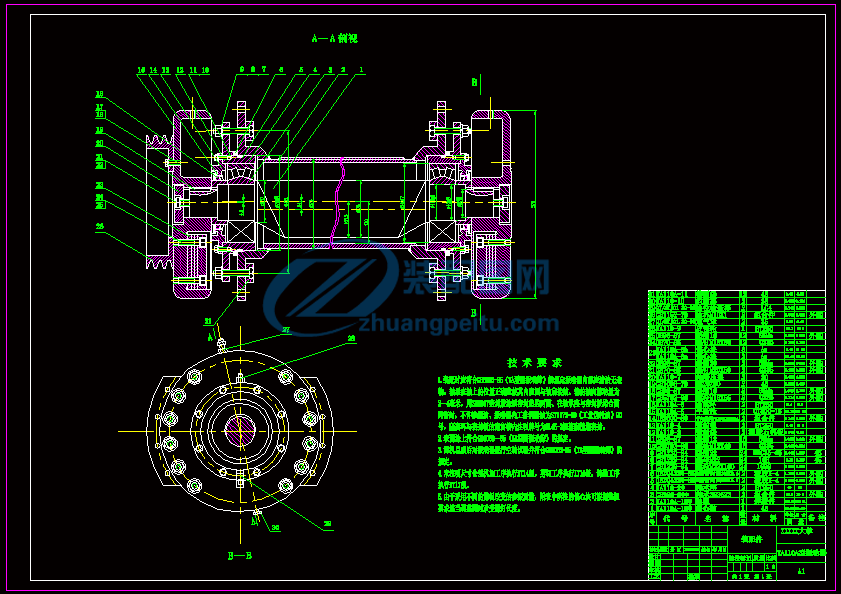
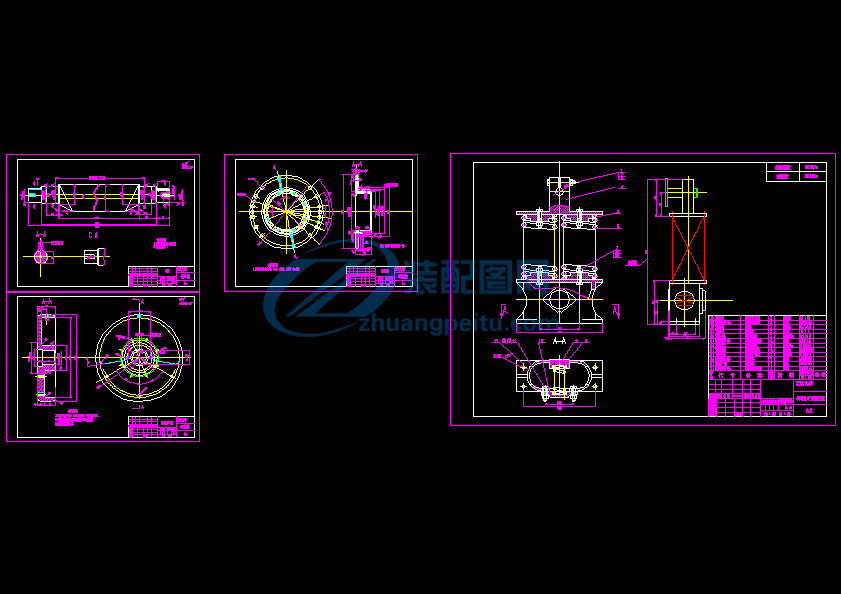
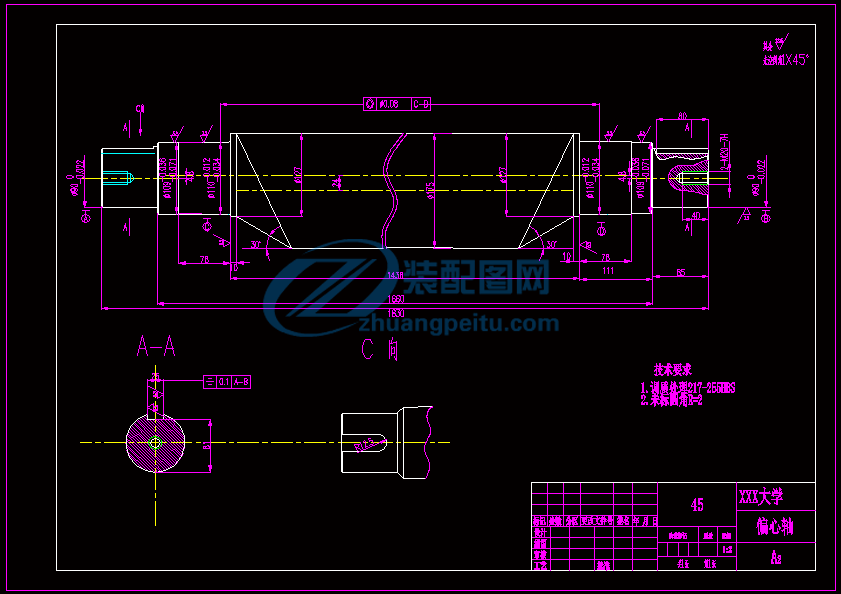
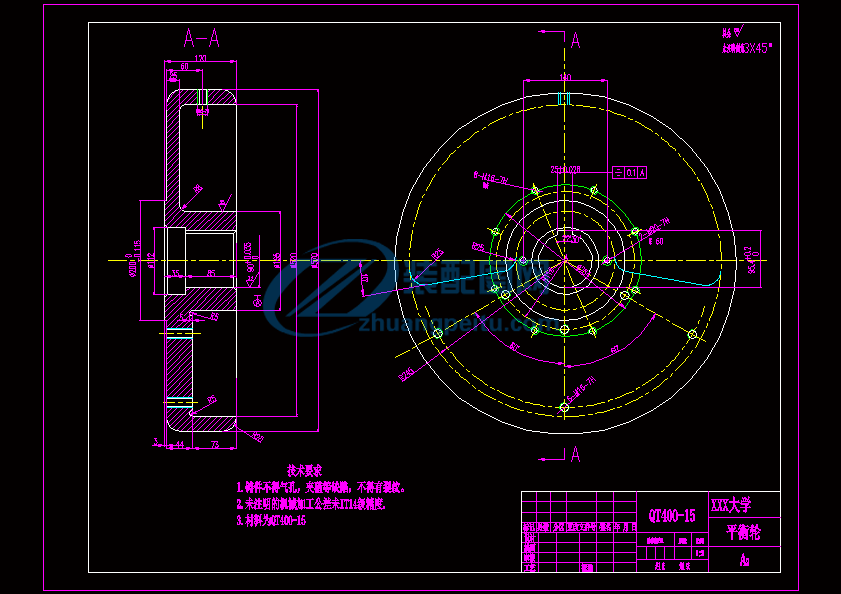
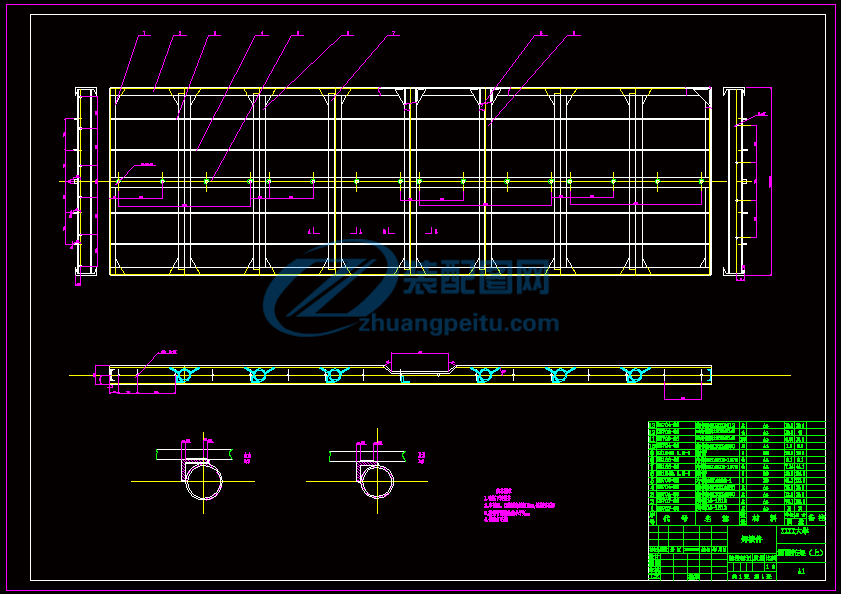
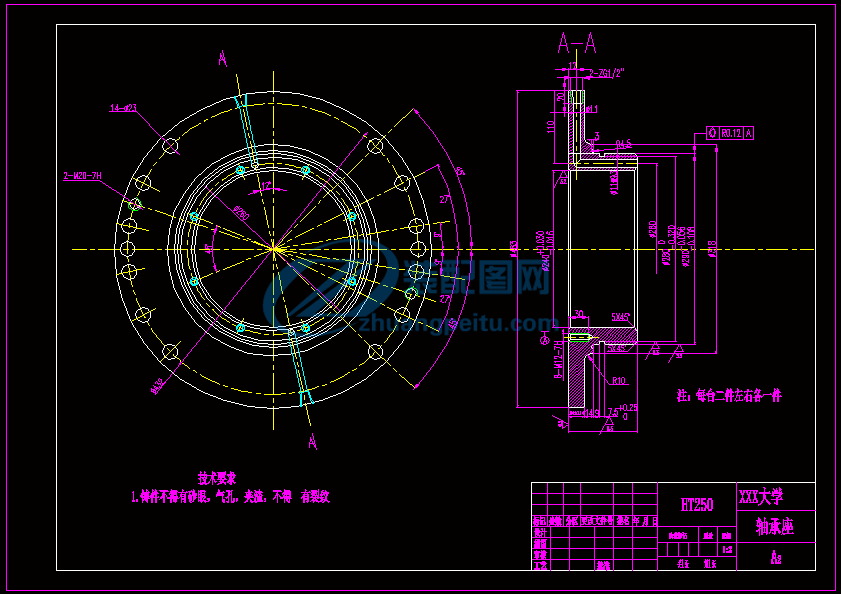

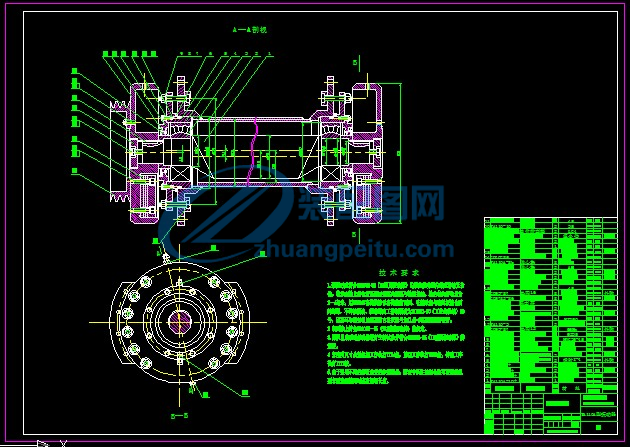
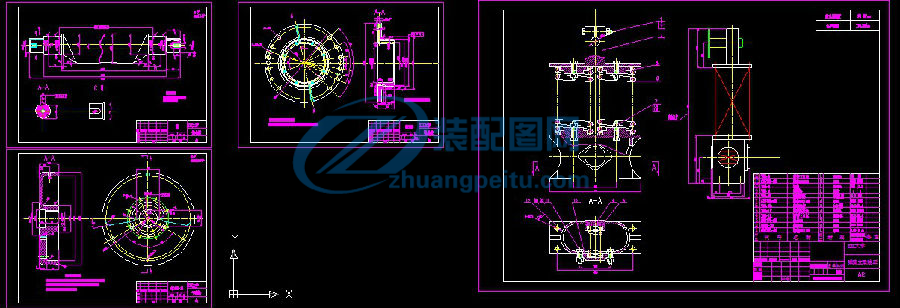
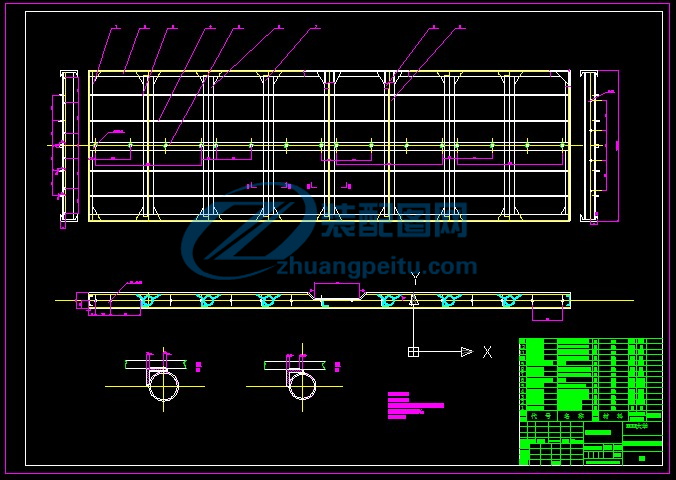
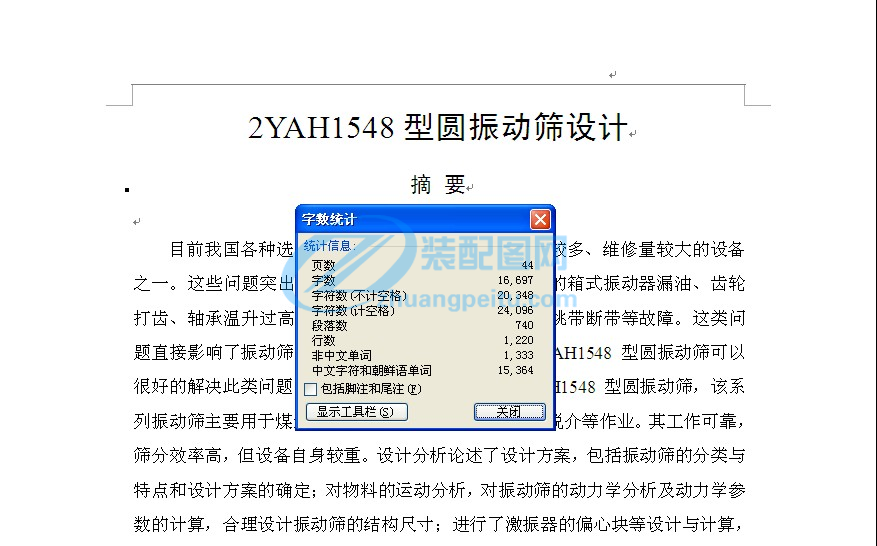
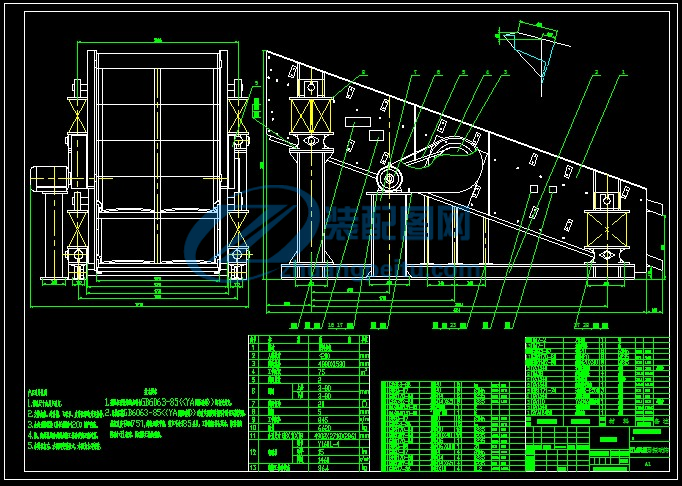
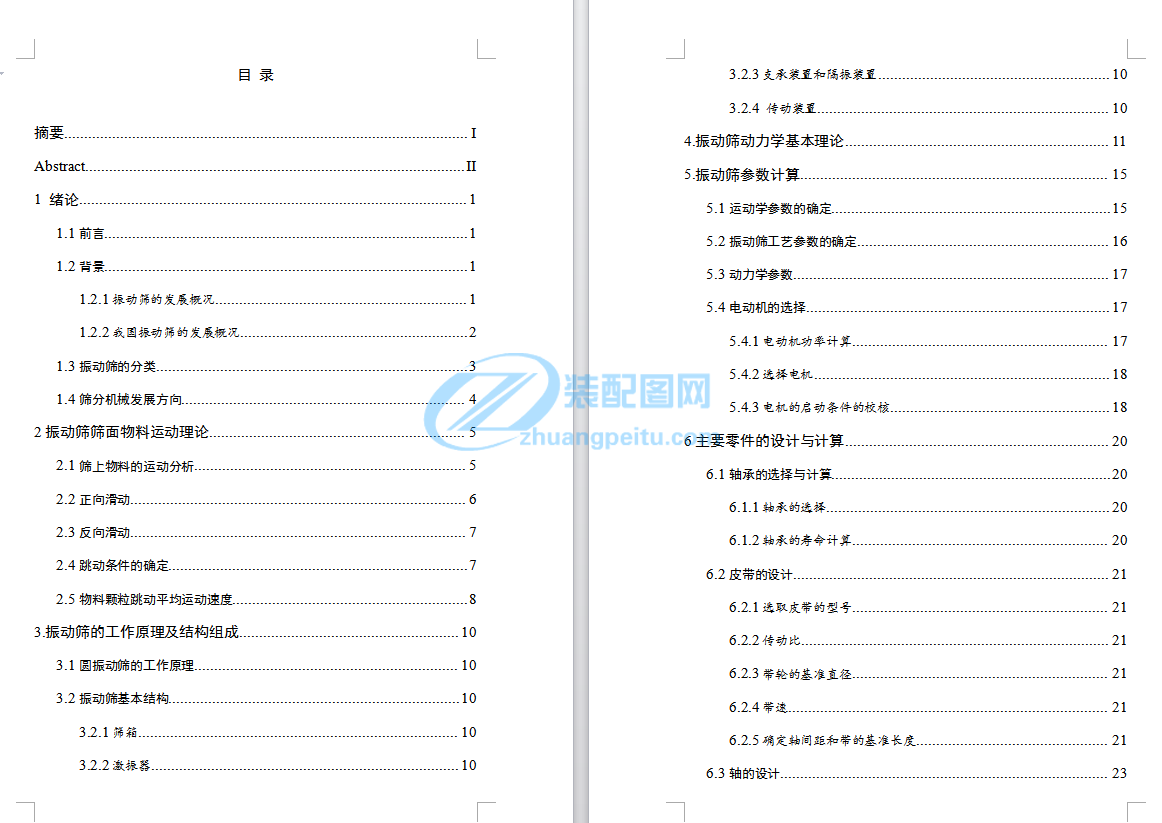

遼寧科技大學(xué)本科生畢業(yè)設(shè)計(jì) 第 1 頁(yè) Screening Vibrating screensPrinciples --Vibrating screens save space and weight and operate on little power because the screening surface may be actuated by vibrating, gyrating or pulsating movement of small amplitude, but at frequencies that normally exceed 3,000/min. Selection of Proper Vibration Sereen --Be sure the screen supplier knows all details of the application. The centrifugal force factor, or combination of frequency of vibration (speed) and amplitude (throw), may affect performance of any vibrating screen. Also, a correct combination of slope and direction of mechanism rotation is vital for inclined screens. Usually, the larger the opening, the greater the amplitude needed for a screen. If the throw is too small, the material may clog or wedge in the openings. Increasing the throw beyond what is required to prevent blinding or plugging does not necessarily increase the life of the bearings and reduce screening efficiency. Increased rate of travel permits more tonnage to be passed over the screen per unit of time. For a given tonnage, a faster rate of travel results in a thinner bed of material and high screening efficiency. Maximum slope is reached when the material travels too fast for the fines to penetrate the ribbon of material and reach the apertures in the screen cloth. At this point an excessive amount of fine material passes over the screen with the oversize, resulting in poor efficiency. When an existing screen is to be used for an application other than that for which it was originally intended, check with the Supplier to see if any of the operating characteristics need modification and if the the screen is structurally suitable for the new application. The operator can get the correct vibrating screen by providing the supplier with the following information: ? Maximum tons per hour to be screened, including any circulating load or any surges in the feed rate. ? A complete size consist or sieve analysis of the material or, if available, an estimated analysis. ? Type of material and weight per cubic foot in broken state. ? Separations desired on each deck. ? Surface moisture carried by the material if screening is to be dry or amount of water with feed if wet. ? Special operating requirements or conditions such as temperature, abrasiveness, corrosiveness or other physical characteristics of the feed, 遼寧科技大學(xué)本科生畢業(yè)設(shè)計(jì) 第 2 頁(yè) efficiency or product requirements which determine selection of screening surface, or installation problems which affect screen size selection or capacity. General Types --Vibrating screens may be divided into two main classes: mechanically-vibrated and electrially-vibrated. The former can be subdivided into classes based on how the vibration is produced--by eccentrics; by unbalanced weight; by cams or bumpers. They can also be subdivided as inclined and horizontal. Sizes --Vibrating screens are made in standard sizes of from 12 in. to 10 ft wide and from 2 1/2 ft to 28 ft long. Common practice dictates that the length of the screen should be 2.5 times the width for dry screening. For wet screening, wider and shorter screen is best. Screens for scalping ahead of primary crushers, operate at a slope of from 12 degrees to 18 degrees and have openings as large as 11-in. square. The eccentric throw for openings from 5 to 11 in. is usually 1/2 in.; for openings from 3 to 5 in. about 3/8 in.; and for smaller openings 1/4 in. The screening surface consists of a heavy cast desk, perforated steel with or without skid bars welded between the holes, rod deck, etc. The mechanical shaking screen comprises a rectangular frame, with perforated steel or wire cloth screening medium. It is usually inclined and suspended on loose rods or cables. These screens now are used mainly for special tasks of coarse screening, having given way to vibrating screens.Electrically-Heated Screens --Electrically heated screen cloth decks have afforded better screening and less dust. Modern or updated screening operations, now handling clays, limestone, potash, salts, phosphates and various hydroscopic materials, report minimum dust loss when equipped with heated screens. The controlling factor in this improvement is the electrically-heated screen doth deck. Any vibratory screen with fine opening (less than 1/2 in.) can be equipped with low volt-age-high amperage resistance heating. The principle of electric heating is based on the fact that small diameter wire of screen cloth (especially stainless steel) serves as a conductor, but offers resistance to a high-amperage current. This resistance causes heating of the wire when powerful transformer and specially designed bus bars connected to screen doth decks push up to 6,000 amps current into a circuit. The current is safe and shock-proof because voltage is low, ranging from approximately 1 1/2 to 16 volts. Workers can do their jobs around electrically-heated screens without special precautions. Heated screens are effective in preventing moisture content of material from causing buildup and blinding. The screen wire is kept at 100 degrees to 130 degrees F depending on character and tonnage of the material processed. This temperature is not high enough to weaken the wire cloth or screen structure, nor does it suffice to drive off moisture held in material. The warm wire stays dry, breaking the surface tension that otherwise would bind damp material to cold, damp metal. This differential or 遼寧科技大學(xué)本科生畢業(yè)設(shè)計(jì) 第 3 頁(yè) warm, dry screen wire versus cold, damp material can be maintained economically through transformer control settings. With every opening in the heated screen mesh protected against blinding, there is no guesswork about what size particle will be delivered. A uniform, unvarying quality to meet tough specifications comes through day after day, no matter what the weather. (High humidity makes trouble with unheated screens.) Plants operating heated screens will have no trouble with excessive amounts of fine, dusty material that formerly sifted through reduced meshes on clogged screens. Service life of screen cloth is greatly increased when electric heating ends the punishment of old-fashioned cleaning methods, such as rough pounding or brushing. Blowtorch flames put too much heat in one spot and bouncing chains added to wear and tear. But, screens kept clean and open with electric heating reportedly are seldom mistreated and last up to eight times as long. Heated decks end the threat of pile ups and strains that can break the mesh. Economical operation of electric heating for screens requires one transformer for installations of up to three panels of screen cloth (maximum area 4- x 12-ft). Two transformers are used on longer decks. Any deck (top, center or bottom) can be heated. Electric heating is most desirable of all where a screen surface is hard to get at. Changing heated screens does not involve more unbolting than needed for ordinary screens. In specifying screens to deliver a uniform particle through heated mesh, the first thing to consider is weight per square foot of the wire cloth needed to set up appropriate resistance. Most calculations are based on square openings. Slotted openings must be identified as to width of clear opening, diameter of wire and number of wires per inch before weight per square foot can be found in any screen cloth manufacturer's catalog. Having determined the usable weight per square foot of screen cloth, the next step is to select the size of clear opening needed, making no allowance for reduction in this size as formerly was the case when material stuck to the wires. Heated wires will maintain the clear opening at all times, making it possible to screen finer without blinding. From a wire catalog, select a mesh weighing no more per square foot (can weigh less) than determined using the method above with the clear opening characteristics desired. This often turns out to be a more efficient screen because the wire diameter will be smaller and the percentage of the open area will be greater. For example, where a 1/8-in. clear opening was desired (but often blinded) on unheated screens, the wire diameter was 0.63 and the open area was 44 percent. The cloth weighed 1.43 lb/ft. 2. For a heated 3- x 12-ft screen, the weight must not exceed 遼寧科技大學(xué)本科生畢業(yè)設(shè)計(jì) 第 4 頁(yè) 1.1 lb/ft2. Two options were found in cloth with 1/8-in. clear opening: wire diameter .054 weighing 1.09 lb/ft2 providing 48.8 percent open area; and wire diameter .047 weighing 0.85 lb/ft2 with a 52.8 percent open area. Load conditions may make fine diameters of carbon steel wire inadequate. In such cases, stainless steel wire of larger diameter with greater load-carrying capacity will have the necessary resistance for good heating. Lighter wire with more open area yields higher tonnage and heated mesh stays open 100 percent. Two screen cloths connected in a series may be of different mesh sizes or clear openings, as long as they both weigh the same per ft2 and do not exceed the weight allowed for that particular size of screen. With heated screens, major savings in pollution control are possible. Also moisture content of material is reportedly increased in a range of 5 to 8 percent. This moisture is added during or after crushing-grinding operations and holds down dust during transfer of material and passage over heated screens. Warm wire handles 5 to 8 percent moisture in stride. The cost of heating equipment and mist spraying reportedly is less than the cost of having bag towers and precipitators. 振動(dòng)篩的選擇振動(dòng)篩的選擇原則:選擇振動(dòng)篩的原則是所選擇的振動(dòng)篩要節(jié)省空間、重量并且驅(qū)動(dòng)的功率要小,因?yàn)楹Y選表面可以驅(qū)動(dòng)并且發(fā)生振動(dòng)。同時(shí)還要保證旋轉(zhuǎn)或脈動(dòng)運(yùn)動(dòng)振幅要小,但振動(dòng)篩的振動(dòng)頻率在通常情況下是要超過(guò)三千次每分鐘的。選擇合適的振動(dòng)顯示屏:要確定顯示屏供應(yīng)商知道所有有關(guān)方面的使用細(xì)節(jié)。離心力或組合頻率振動(dòng)(速度)以及振幅(投擲)等因素都可能影響到任何振動(dòng)篩的正常工作。此外,需要有一個(gè)正確的組合坡度和方向的輪換機(jī)制,這對(duì)于顯示屏來(lái)說(shuō)是至關(guān)重要的。通常情況下,振動(dòng)篩需要大開(kāi)放、大振幅的顯示屏。如果投入太少的話,則這些材料可能出現(xiàn)木屐或楔形開(kāi)口等情況。增加投入以后,需要知道如何防止堵塞因?yàn)槎氯遣槐匾模視?huì)增加日常軸承的磨損以及和降低篩選的效率。單位時(shí)間內(nèi)材料上升速率曲線都要通過(guò)整個(gè)屏幕,因此該處材料以較快的速率通過(guò)較薄的車床的同時(shí)需要用較高的效率來(lái)進(jìn)行篩選。當(dāng)材料速度過(guò)快導(dǎo)致材料絲帶被擊穿并當(dāng)材料到達(dá)屏幕布料開(kāi)口處時(shí)出現(xiàn)最大傾斜角。此時(shí)大量的優(yōu)質(zhì)材料通過(guò)屏幕的速度過(guò)快,從而導(dǎo)致效益不佳。 當(dāng)一個(gè)現(xiàn)有的屏幕畫面出現(xiàn)故障時(shí),如果該屏幕的結(jié)構(gòu)還適合于新的應(yīng)用,這時(shí)應(yīng)及時(shí)進(jìn)行檢查并詢問(wèn)供應(yīng)商,看看是否有需要修改的地方。操作者還可以通過(guò)供應(yīng)商提供的下列資料得到良好的振動(dòng)篩: ?通過(guò)最高每小時(shí)噸數(shù)進(jìn)行篩選,包括任何循環(huán)負(fù)荷或任何突然增加的進(jìn)給速度。?通過(guò)一個(gè)完整的粒度分析或?qū)Σ牧线M(jìn)行篩分分析,如果條件允許的話,最好使用估計(jì)分析法。?材料的種類和每立方米重量失效的概率。?各個(gè)篩板的預(yù)期斷裂的情況。?通過(guò)表面材料所攜帶的水分進(jìn)行篩選,如果是潮濕的需要將水份曬干或添加一定數(shù)量的材料。?特殊的操作要求或條件,例如溫度、磨損情況、腐蝕情況或具有其他物理特性的材料、效率或產(chǎn)品的要求,確定篩選表面或安裝問(wèn)題,因?yàn)檫@將直接影響到屏幕尺寸的選擇以及屏幕實(shí)際使用的能力。一般的類型:振動(dòng)篩可分為兩大類:一類為機(jī)械振動(dòng)型振動(dòng)篩,另一類為電力振動(dòng)型振動(dòng)篩。 前者是根據(jù)振動(dòng)是如何產(chǎn)生的可被細(xì)分入類—由偏心輪產(chǎn)生;由失衡的重量產(chǎn)生;由凸輪或防撞器產(chǎn)生;它們也可以按照傾斜和橫向進(jìn)行細(xì)分。 尺寸:振動(dòng)的屏幕通常被制造成寬為從 12 英尺到 10 英尺,長(zhǎng)為從 2 1 / 2 英尺到 28 英尺。在通常情況下,干式篩選顯示屏的長(zhǎng)度應(yīng)該是寬度的 2.5 倍。對(duì)于濕式篩選來(lái)說(shuō),更寬和更短的屏幕是最好的選擇。為防止屏幕提前而導(dǎo)致被壓碎,操作斜率應(yīng)保持在 12 度至 18 度左右,并有多達(dá) 11 種開(kāi)口情況。異常投擲為開(kāi)頭從 5 英尺到 11 英尺通常是 1/2 英尺;開(kāi)頭為 3 英尺到 5 英尺,大約 3 / 8 英尺和較小的開(kāi)口 1/4 英尺。篩選表面是由一輛重型鑄造服務(wù)臺(tái)、鋼穿孔或無(wú)打滑焊接鋼筋之間的空隙、篩網(wǎng)等部分組成的。機(jī)械振動(dòng)篩的屏幕由一個(gè)長(zhǎng)方形框架、已打孔的鋼或絲織物組成。它通常傾斜和暫停在懸浮松散桿或電纜上。這些屏幕現(xiàn)在主要用于有特殊任務(wù)的時(shí)侯,此時(shí)應(yīng)讓位給振動(dòng)篩的屏幕。電熱屏幕--電熱布屏幕面板提供了較佳的保護(hù)功能并且具有粉塵少等優(yōu)點(diǎn)?,F(xiàn)代或更新篩選作業(yè),現(xiàn)在處理粘土、石灰石、鉀、鹽、磷和各種的吸濕材料,當(dāng)配備暖簾時(shí),報(bào)告的粉塵損失最低。 控制因素在這方面的改善是使用電熱幕小靈通平臺(tái)。任何振動(dòng)篩的屏幕以良好的開(kāi)幕(小于 1 / 2 英寸),可配備低電壓使用年齡高的焙電阻來(lái)抵抗熱化。 電熱化的原則是基于這樣的事實(shí):小直徑線材絲網(wǎng)布( 尤其是不銹鋼) 作為導(dǎo)體,但是能夠抵抗高焙電流。當(dāng)強(qiáng)有力的變壓器和特別地被設(shè)計(jì)的母線接上屏 幕面板被推至 6000 安培電流進(jìn)入電路時(shí),這種抵抗導(dǎo)致導(dǎo)線的熱化目前是安全防震,因?yàn)殡妷狠^低,從大約從 1 / 2 伏特至 16 伏特。因此工人們可以在沒(méi)有殊防范措施的情況下在電熱屏幕附近安全的工作。熱屏幕能有效地防止材料的水分累積和堵塞。根據(jù)材料本身的特征和被處理的噸位,屏幕導(dǎo)線能夠被被保留在 100 度到 130 華氏度。這個(gè)溫度并不足夠高導(dǎo)致減弱導(dǎo)線布料或屏幕的結(jié)構(gòu),也不足夠除去材料中的水分。 加熱導(dǎo)線使其保持干燥,否則會(huì)打破束縛在潮濕的材料中對(duì)冷, 潮濕的金屬的表面張力。這一差動(dòng)或溫暖、干燥篩線對(duì)寒冷、潮濕的材料可以通過(guò)控制設(shè)定,而變得更加經(jīng)濟(jì)合理。每個(gè)熱屏幕篩網(wǎng)的前端被保護(hù),以避免堵塞。無(wú)法猜測(cè)多少尺寸的顆粒將被提供。無(wú)論是什么天氣,一個(gè)統(tǒng)一的、品質(zhì)不變的、滿足苛刻的規(guī)格每天都有通過(guò)。(高濕度造成未加熱的屏幕的問(wèn)題) 。操作熱的顯示屏不會(huì)有太多的麻煩 ,多灰塵的材料以前是在被堵塞的屏幕上通過(guò)減少篩網(wǎng)來(lái)過(guò)濾的。當(dāng)電熱化結(jié)束后可以使用傳統(tǒng)的清潔方法清理屏幕,如果使用粗洗或電刷洗等方法,屏幕布料產(chǎn)品的使用壽命將會(huì)大大的提高。小型發(fā)焰裝置在一定的區(qū)域內(nèi)產(chǎn)生大量的熱量,他所產(chǎn)生的連鎖反映就是增加了磨損以及斷裂。但是,據(jù)說(shuō)屏幕電熱化保持清潔和開(kāi)放很少被采用而且最多能使用 8 次。暖底甲板的物料堆積和應(yīng)變,可以導(dǎo)致濾網(wǎng)被打破。對(duì)于電熱屏幕來(lái)說(shuō)最經(jīng)濟(jì)的操作是需要有一個(gè)變壓器裝置來(lái)為屏幕布料(最大面積 4×12 英尺) 。兩臺(tái)變壓器是用在更長(zhǎng)的甲板。任何甲板( 頂部中心或底部),都可以用來(lái)加熱。處理屏幕表面是很難獲取的地方,使用電熱化是最可取的方法。對(duì)于普通的屏幕來(lái)說(shuō),更換熱的顯示屏?xí)r并不需要過(guò)多的開(kāi)插銷。在指定的顯示屏里通過(guò)加熱網(wǎng)提供一個(gè)一致的微粒,首先要考慮的事情是量出每平方英尺導(dǎo)線布料所要求的重量,以便設(shè)來(lái)定適當(dāng)?shù)淖枇Α4蠖鄶?shù)計(jì)算都是基于方形洞口的基礎(chǔ)上進(jìn)行的。開(kāi)槽開(kāi)孔被識(shí)別是在量出每平方英尺的重量和找到任何屏幕布料制造商的產(chǎn)品目錄之前,通過(guò)前端精確的寬度,導(dǎo)線的直徑和每平方英尺一定數(shù)量導(dǎo)線的重量來(lái)實(shí)現(xiàn)的。被確定能用的每平方英尺屏幕布料的重量,下一步是清楚的選出所需要的開(kāi)頭的大小,制造無(wú)加工余量尺寸大小減少到以前的情況時(shí),材料貼到電線上。加熱導(dǎo)線將一直保持清晰的開(kāi)放,使得畫面清晰無(wú)黑屏。 通過(guò)導(dǎo)線編目,僅僅通過(guò)重量選擇一個(gè)篩網(wǎng)(重量可以少稱量) 使用的方法是通過(guò)前端特征來(lái)決定的。這通常是一個(gè)更有效率的方法,因?yàn)檫@樣屏幕上的鋼絲直徑將變得更小,而且開(kāi)放范圍的百分比將會(huì)變得更大。例如,在一個(gè) 1/8 英尺的未加熱的顯示屏上,它的前端能夠被清楚的顯示出來(lái),(但是屏幕經(jīng)常黑屏 ),其導(dǎo)線直徑為 0.63 及開(kāi)放范圍的百分比為為 44%。布料重量為 1.43 磅/ 英尺 。一個(gè)被加熱的 3×12 英尺的顯示屏,重量不得超過(guò)21.1 磅/英尺 。兩個(gè)方案通過(guò)比較發(fā)現(xiàn),布料以 1/8 英尺前端被清楚的顯示出來(lái)2的顯示屏上: 導(dǎo)線直徑為 0.054,重量 1.09 磅/ 英尺 ,開(kāi)放范圍的百分比為248.8%;一個(gè)加熱 3×12 英尺的顯示屏上:線直徑為 0.047,重 0.85 磅/英尺 ,2開(kāi)放范圍的百分比為 52.8%。 在負(fù)荷的狀態(tài)下可以解決碳鋼導(dǎo)線直徑不足的問(wèn)題。在這種情況下,對(duì)于好的熱化來(lái)說(shuō),不銹鋼導(dǎo)線直徑以更大的承載能力來(lái)抵抗外部的載荷。更輕的導(dǎo)線并有更多開(kāi)闊地帶能夠產(chǎn)生更高的噸位,而且熱的篩網(wǎng)能夠保持百分之百處于打開(kāi)的狀態(tài)。兩塊屏幕布料被連系成一個(gè)系列,也許是網(wǎng)格尺寸大小不同或者是前端的清晰度不同。只要它們滿足每平方英尺的重量相同而且不超過(guò)該規(guī)定的重量,尤其是屏幕的尺寸。 對(duì)于振動(dòng)篩的熱屏幕來(lái)說(shuō),通過(guò)控制從而大大節(jié)省污染是可能的。同時(shí)材料中的水分根據(jù)數(shù)據(jù)顯示增加了 5 至 8 個(gè)百分點(diǎn)。這些水分是在破碎粉磨作業(yè)的期間或之后產(chǎn)生的,通過(guò)灰塵在材料中的持續(xù)運(yùn)動(dòng)以及通過(guò)以上所述的熱屏幕來(lái)降低的。溫暖的導(dǎo)線的處理量在 5 %到百 8 %之間。供熱設(shè)備和噴霧設(shè)備的成本據(jù)說(shuō)是低于袋子塔和沉淀器的成本。Screening Vibrating screensPrinciples --Vibrating screens save space and weight and operate on little power because the screening surface may be actuated by vibrating, gyrating or pulsating movement of small amplitude, but at frequencies that normally exceed 3,000/min. Selection of Proper Vibration Sereen --Be sure the screen supplier knows all details of the application. The centrifugal force factor, or combination of frequency of vibration (speed) and amplitude (throw), may affect performance of any vibrating screen. Also, a correct combination of slope and direction of mechanism rotation is vital for inclined screens. Usually, the larger the opening, the greater the amplitude needed for a screen. If the throw is too small, the material may clog or wedge in the openings. Increasing the throw beyond what is required to prevent blinding or plugging does not necessarily increase the life of the bearings and reduce screening efficiency. Increased rate of travel permits more tonnage to be passed over the screen per unit of time. For a given tonnage, a faster rate of travel results in a thinner bed of material and high screening efficiency. Maximum slope is reached when the material travels too fast for the fines to penetrate the ribbon of material and reach the apertures in the screen cloth. At this point an excessive amount of fine material passes over the screen with the oversize, resulting in poor efficiency. When an existing screen is to be used for an application other than that for which it was originally intended, check with the Supplier to see if any of the operating characteristics need modification and if the the screen is structurally suitable for the new application. The operator can get the correct vibrating screen by providing the supplier with the following information: ? Maximum tons per hour to be screened, including any circulating load or any surges in the feed rate. ? A complete size consist or sieve analysis of the material or, if available, an estimated analysis. ? Type of material and weight per cubic foot in broken state. ? Separations desired on each deck. ? Surface moisture carried by the material if screening is to be dry or amount of water with feed if wet. ? Special operating requirements or conditions such as temperature, abrasiveness, corrosiveness or other physical characteristics of the feed, efficiency or product requirements which determine selection of screening surface, or installation problems which affect screen size selection or capacity. General Types --Vibrating screens may be divided into two main classes: mechanically-vibrated and electrially-vibrated. The former can be subdivided into classes based on how the vibration is produced--by eccentrics; by unbalanced weight; by cams or bumpers. They can also be subdivided as inclined and horizontal. Sizes --Vibrating screens are made in standard sizes of from 12 in. to 10 ft wide and from 2 1/2 ft to 28 ft long. Common practice dictates that the length of the screen should be 2.5 times the width for dry screening. For wet screening, wider and shorter screen is best. Screens for scalping ahead of primary crushers, operate at a slope of from 12 degrees to 18 degrees and have openings as large as 11-in. square. The eccentric throw for openings from 5 to 11 in. is usually 1/2 in.; for openings from 3 to 5 in. about 3/8 in.; and for smaller openings 1/4 in. The screening surface consists of a heavy cast desk, perforated steel with or without skid bars welded between the holes, rod deck, etc. The mechanical shaking screen comprises a rectangular frame, with perforated steel or wire cloth screening medium. It is usually inclined and suspended on loose rods or cables. These screens now are used mainly for special tasks of coarse screening, having given way to vibrating screens.Electrically-Heated Screens --Electrically heated screen cloth decks have afforded better screening and less dust. Modern or updated screening operations, now handling clays, limestone, potash, salts, phosphates and various hydroscopic materials, report minimum dust loss when equipped with heated screens. The controlling factor in this improvement is the electrically-heated screen doth deck. Any vibratory screen with fine opening (less than 1/2 in.) can be equipped with low volt-age-high amperage resistance heating. The principle of electric heating is based on the fact that small diameter wire of screen cloth (especially stainless steel) serves as a conductor, but offers resistance to a high-amperage current. This resistance causes heating of the wire when powerful transformer and specially designed bus bars connected to screen doth decks push up to 6,000 amps current into a circuit. The current is safe and shock-proof because voltage is low, ranging from approximately 1 1/2 to 16 volts. Workers can do their jobs around electrically-heated screens without special precautions. Heated screens are effective in preventing moisture content of material from causing buildup and blinding. The screen wire is kept at 100 degrees to 130 degrees F depending on character and tonnage of the material processed. This temperature is not high enough to weaken the wire cloth or screen structure, nor does it suffice to drive off moisture held in material. The warm wire stays dry, breaking the surface tension that otherwise would bind damp material to cold, damp metal. This differential or warm, dry screen wire versus cold, damp material can be maintained economically through transformer control settings. With every opening in the heated screen mesh protected against blinding, there is no guesswork about what size particle will be delivered. A uniform, unvarying quality to meet tough specifications comes through day after day, no matter what the weather. (High humidity makes trouble with unheated screens.) Plants operating heated screens will have no trouble with excessive amounts of fine, dusty material that formerly sifted through reduced meshes on clogged screens. Service life of screen cloth is greatly increased when electric heating ends the punishment of old-fashioned cleaning methods, such as rough pounding or brushing. Blowtorch flames put too much heat in one spot and bouncing chains added to wear and tear. But, screens kept clean and open with electric heating reportedly are seldom mistreated and last up to eight times as long. Heated decks end the threat of pile ups and strains that can break the mesh. Economical operation of electric heating for screens requires one transformer for installations of up to three panels of screen cloth (maximum area 4- x 12-ft). Two transformers are used on longer decks. Any deck (top, center or bottom) can be heated. Electric heating is most desirable of all where a screen surface is hard to get at. Changing heated screens does not involve more unbolting than needed for ordinary screens. In specifying screens to deliver a uniform particle through heated mesh, the first thing to consider is weight per square foot of the wire cloth needed to set up appropriate resistance. Most calculations are based on square openings. Slotted openings must be identified as to width of clear opening, diameter of wire and number of wires per inch before weight per square foot can be found in any screen cloth manufacturer's catalog. Having determined the usable weight per square foot of screen cloth, the next step is to select the size of clear opening needed, making no allowance for reduction in this size as formerly was the case when material stuck to the wires. Heated wires will maintain the clear opening at all times, making it possible to screen finer without blinding. From a wire catalog, select a mesh weighing no more per square foot (can weigh less) than determined using the method above with the clear opening characteristics desired. This often turns out to be a more efficient screen because the wire diameter will be smaller and the percentage of the open area will be greater. For example, where a 1/8-in. clear opening was desired (but often blinded) on unheated screens, the wire diameter was 0.63 and the open area was 44 percent. The cloth weighed 1.43 lb/ft. 2. For a heated 3- x 12-ft screen, the weight must not exceed 1.1 lb/ft2. Two options were found in cloth with 1/8-in. clear opening: wire diameter .054 weighing 1.09 lb/ft2 providing 48.8 percent open area; and wire diameter .047 weighing 0.85 lb/ft2 with a 52.8 percent open area. Load conditions may make fine diameters of carbon steel wire inadequate. In such cases, stainless steel wire of larger diameter with greater load-carrying capacity will have the necessary resistance for good heating. Lighter wire with more open area yields higher tonnage and heated mesh stays open 100 percent. Two screen cloths connected in a series may be of different mesh sizes or clear openings, as long as they both weigh the same per ft2 and do not exceed the weight allowed for that particular size of screen. With heated screens, major savings in pollution control are possible. Also moisture content of material is reportedly increased in a range of 5 to 8 percent. This moisture is added during or after crushing-grinding operations and holds down dust during transfer of material and passage over heated screens. Warm wire handles 5 to 8 percent moisture in stride. The cost of heating equipment and mist spraying reportedly is less than the cost of having bag towers and precipitators.