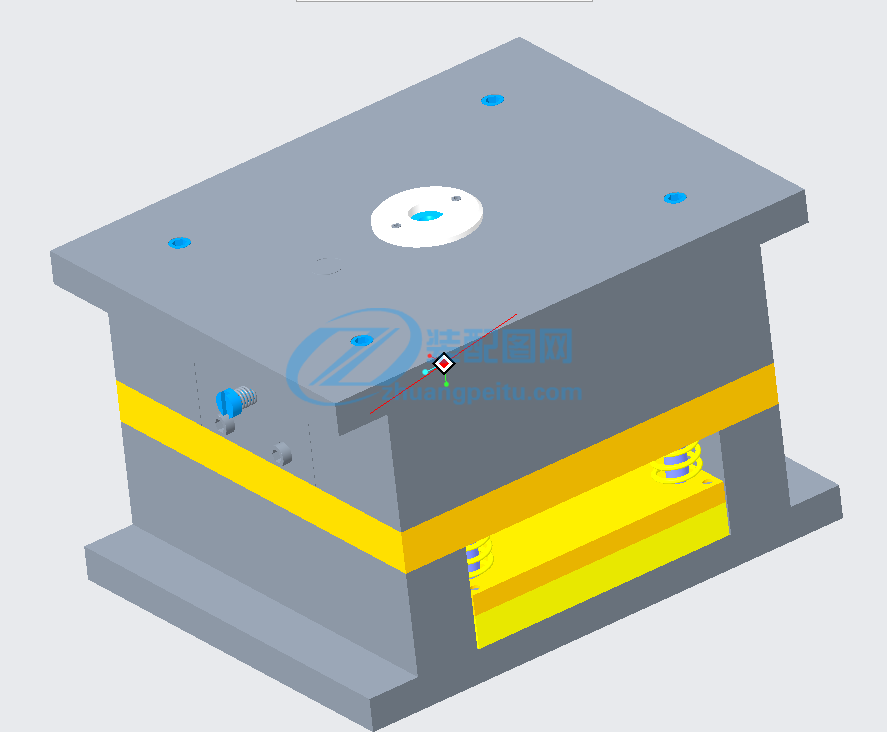
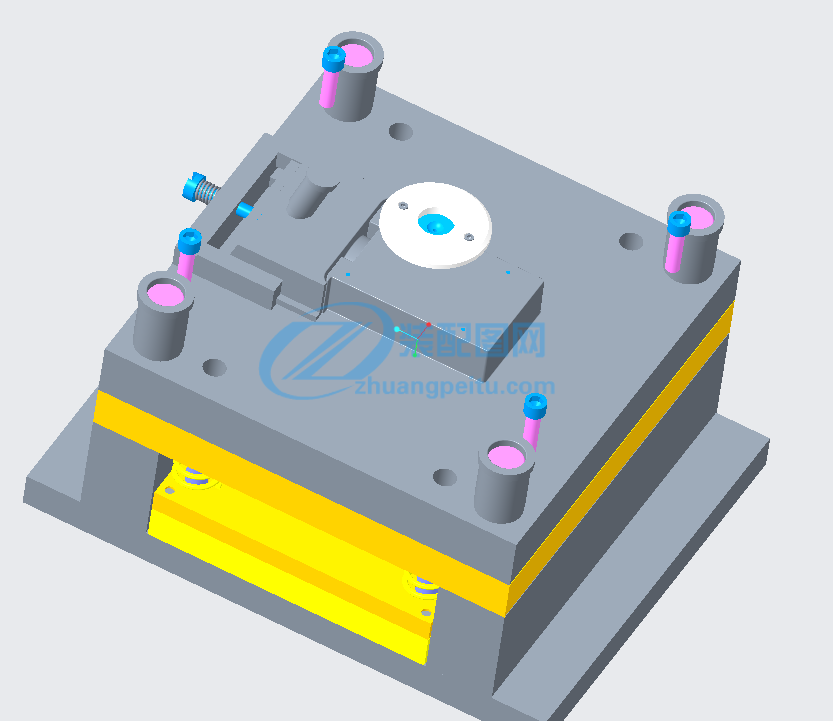






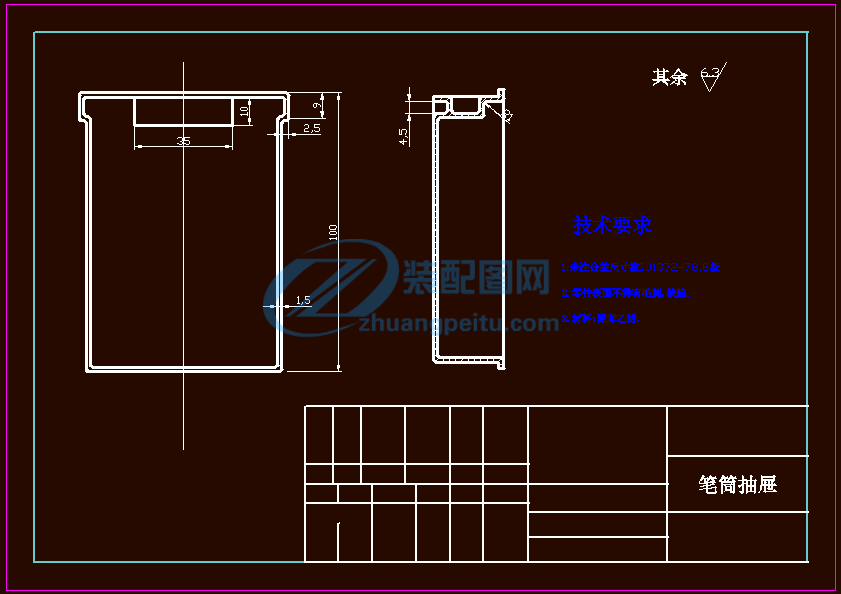

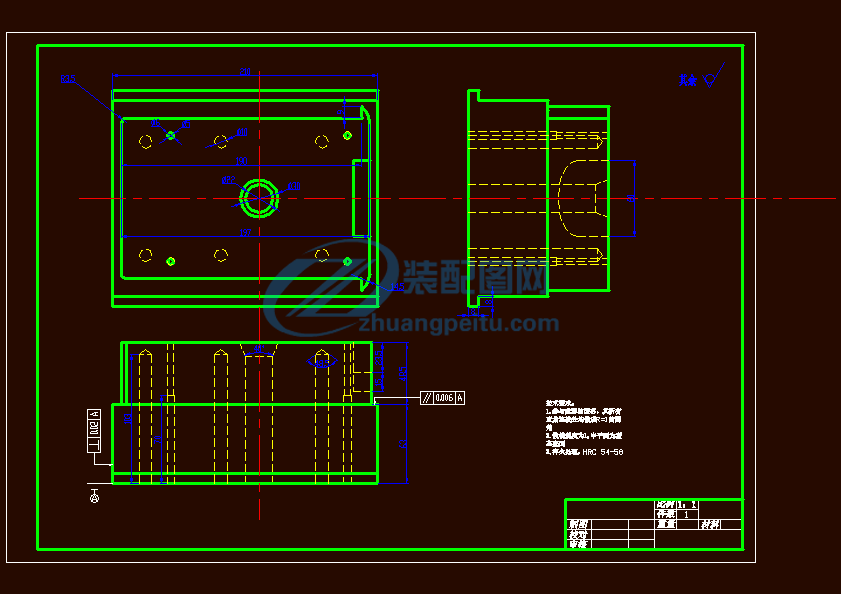
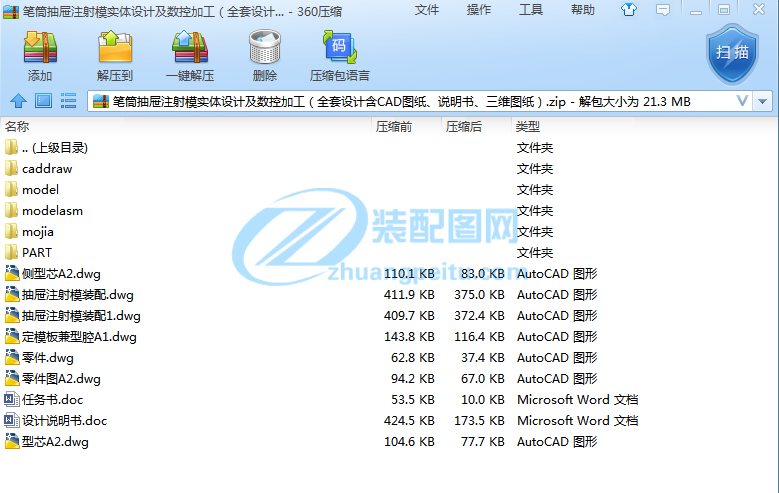
畢業(yè)論文(設計)任務書論文(設計)題 目 筆筒抽屜注塑模具設計工程 院(系) 專業(yè) 級學生姓名指導教師 職務起訖日期設計地點發(fā)任務書日期: 1畢業(yè)論文(設計)任務的內容和要求(包括原始數(shù)據(jù)、技術要求、工作要求)設計題目: 注塑模具設計設計依據(jù):1 、生產(chǎn)綱領:大批量生產(chǎn)2、零件圖3、國家有關注射模具設計標準。設計要求:(一)注射模實體設計(1) 、分析塑件圖工藝性和工藝條件 首先了解塑件的用途、使用情況及工作要求,對于塑件圖上提出的塑件形狀、尺寸精度、表面粗糙度等工藝分析,即從成型工藝、塑件的設計原則、模具結構合理性等方面進行綜合分析。(2) 、確定塑件成型工藝及設備1)確定成型工藝條件,包括注射溫度、模具和冷卻介質的溫度、注射速度和注射循環(huán)周期等。2)根據(jù)塑件形狀尺寸,估算塑件體積和重量。確定型腔數(shù)。3)選擇設備型號規(guī)格,并校核與模具有關的技術參數(shù),包括額定注射量,注射壓力、鎖模力、最大、最小模厚、開模行程、推出裝置及裝模部分的尺寸(模板尺寸、拉桿空間、定位孔直徑、噴嘴定位半徑等) 。(3)確定模具總體結構方案1) 選擇成型位置、確定分型面、脫模方式、側孔、側凹的成型方法、澆注系統(tǒng)形式、澆口開設位置等。22) 選擇合適的標準模架,確定模具成型零件的材料和加工方法。3) 通常需構思幾種模具結構方案,采用容易制造、便于操作、確保成型塑件質量的模具結構。(4)繪制模具裝配圖(5)對模具各部分進行受力分析 對模具進行必要的強度及剛度計算,對于薄弱部分在結構上進行加強。(6)成型零件成型尺寸的計算。(7)加工零件工作圖的繪制。(8)完成二維模具結構總體設計。(二)用 CAD/CAM 軟件進行模具構件的三 D 造型,并演示其加工過程。1.用三維 CAD 軟件(Pro-E、Caxa 等)構建三維曲面或實體模型要求:所構建的模型直接決定能否加工,并決定了型腔質量,故要求所構建的模型美觀、無錯誤。2. 所構建的模型正確分模3. CAM 軟件(MasterCam、Caxa 等)對上下模型腔進行銑削模擬加工,生成刀具路徑。需確保所生成的刀具路徑能完善地加工出上下模腔,不允許有粗劣的刀路;保證加工過程中不產(chǎn)生過切或切不到的現(xiàn)象;避免刀具和工件的干涉。要求:(1)較好地構建加工輔助線、面(2)確定合理的粗、精加工工序數(shù),(3)對每道加工工序,正確地選擇加工方法,并正確地選擇刀具和加工參數(shù),3如刀具半徑、主軸轉速、進給速度、切削深度、走刀刀距、走刀方向等。(4)查看刀具路徑,能從中發(fā)現(xiàn)三維造型或加工中的錯誤,并進行修正。4.對所生成的刀具路徑進行模擬仿真。4. 對刀具路徑進行后置處理,生成 NC 文件。45圖紙內容及張數(shù)零件圖 1 張模具總體裝配圖 1 張凹凸模零件圖 1 張非標準零件圖 若干張補充零件加工圖 若干張實物內容及要求6其 他1、設計說明書 1 份 6000 字左右2、外文資料譯文 1 份7參考文獻8主要參考文獻:1.《注塑模具設計與制造實用技術》 王樹勛 主編 西安電子科技長出版社 2001.32.《實用模具設計與制造手冊》 葉偉昌 主編 -北京:機械工業(yè)出版社出版,1999.53. 《塑料成型加工與模具》 黃虹 主編 化學工業(yè)出版社4. 《塑料擠塑模與注射模優(yōu)化設計》 李遠波 主編1、 《塑料模具設計 》 機械工業(yè)出版社2、 《模具標準應用手冊 》 機械工業(yè)出版社3、 《實用塑料注射模設計與制造》 機械工業(yè)出版社5、 《注射成型模具設計 108 例》 中國輕工業(yè)出版社6、 《機械零件設計手冊 》 冶金工業(yè)出版社8、 《模具技術 》 上海交通大學出版社9、 《Pro-E 模具設計與數(shù)控加工 》 易際明等編著 清華大學出版社10、 《CAXA 數(shù)控機床操作機仿真試訓教程》 北京航空航天大學出版社 11、 《CAXA 實體設計》 北京航空航天大學出版社9畢業(yè)論文(設計)進度計劃起訖日期 工 作 內 容 備注4.30~5.3 確定模具總體結構方案5.4~ 5.17 繪制模具裝配圖5.18~5.21 零 件 圖5.22~5.28 用 Pro-E 等 構 建 三 維 實 體 模 型 和 模 擬 加工5.29~6.4 寫 畢 業(yè) 設 計 抽屜注塑模具設計大綱第 1 章緒論1、1、1 何謂注塑成型所謂注塑成型(Injection Molding)是指,將已加熱融化的材料噴射注入到模具內,經(jīng)由冷卻與固化后,得到成形品的方法。適用于量產(chǎn)與形狀復雜產(chǎn)品等成形加工領域。1、1 、2 注塑成型機 注塑成型機可區(qū)分為合模裝置與注射裝置。合模裝置是開閉模具以執(zhí)行脫模(eject)作業(yè)。注射裝置是將樹脂予以加熱融化後再射入模具內。1、1、3 模具所謂模具(Mold)是指,為了將材料樹脂做成某種形狀,而用來承接射出注入樹脂的金屬制模型。已溶解的材料是從澆口進入模具內,再經(jīng)由流道與流道口填充到模槽內。接下來則經(jīng)由冷卻工程與開模成型機脫模桿上的模具脫模板,推頂出成形品。1、1、4 成形品成形品是由流入融化樹脂的澆口、導入模槽的流道與產(chǎn)品部份所構成。1、1、5 使用回料成形品中的澆口與流道并不屬于產(chǎn)品。因此該部分往往被廢棄,甚至粉碎后再度用作成形專用材料,這就稱為回料?;亓喜荒軉为氉鳛槌尚螌S貌氖褂?,通常都是配合造粒才能予以使用。由于會經(jīng)過成形工程,因此可讓樹脂做出各種特性的變化。回料之配方比例的上限為 30%左右,若配方比例過高就有可能會損害到樹脂的原有性質。1、1、6 成形條件所謂成形條件是指,為了獲得所需的成形品,而利用成型機的汽缸溫度、射出速度、模具溫度等組合成無數(shù)個設定條件。由于可獲得的成形品外觀、尺寸、機械物性會因成形條件而異,因此要找出最佳的成形條件,就必須仰賴熟練的技術與經(jīng)驗。1、2CAD/CAM 的技術現(xiàn)狀經(jīng)過四十多年的發(fā)展,CAD/CAM 技術有了長足的進步?,F(xiàn)在 CAD/CAM主要運行在工作站或微機平臺上。工作站雖然性能優(yōu)越,圖形處理速度快,但價格卻十分昂貴,這在一定程度上限制了 CAD/CAM 技術的推廣。隨著 Pentium 芯片和 WindowsNT 操作系統(tǒng)的出現(xiàn)并流行,以前只能運行在工作站上的 CAD/CAM 軟件現(xiàn)在也可以運行在微機上。由于微機的價格遠遠比工作站低,性能也不比中低檔工作站遜色多少,并且windowsNT 操作系統(tǒng)的安全性與 DOS、Windows3.x 、Windows95/98等操作系統(tǒng)相比有了很大提高。所以,微機平臺為普及 CAD 應用創(chuàng)造了絕好的條件。在此基礎上,CAD/CAM 軟件廠商展開了新一輪的競爭。一方面工作站上著名的 CAD/CAM 的軟件(如 UG、CATIA )全功能地移植到微機平臺,使微機完全對等地實現(xiàn)了工作站環(huán)境的處理能力;另一方面 CAD/CAM 軟件打破了原有 Unix 環(huán)境的桎梏,在 Windows 平臺上全面拓展。Pentium 以上處理器和 NT 環(huán)境已經(jīng)或者正在成為 CAD/CAM軟件運行和應用的主流平臺。當今 CAD/CAM 軟件動態(tài)如下 :(6) 一、使用微機作為開發(fā)和應用平臺微機平臺的 CAD/CAM 軟件的特點是:1.采用 Windows 環(huán)境采用 WindowsNT 操作系統(tǒng)是新一代推出的微機 CAD/CAM 軟件的共同特點?,F(xiàn)在,個人計算機已經(jīng)具備了與中低檔工作站競爭的實力,再加上其價格低廉,使得普及 CAD 應用成為可能。Windows平臺上的新一代 CAD/CAM 軟件基本上都采用典型的 Windows 界面和操作規(guī)范,同時由于 DDE 和 OLE 技術的廣泛應用,這些CAD/CAM 軟件可以與 Windows 平臺的其他軟件進行動態(tài)數(shù)據(jù)交換,也可以在不退出 CAD/CAM 軟件的前提下嵌入(或鏈接)其他應用程序的對象。2.采用 COM 技術COM(ComponentObjectModel)是國際上為提高軟件穩(wěn)定性和開發(fā)效率而引入的重要技術。現(xiàn)今推出的 Windows 平臺的 CAD/CAM 軟件都或多或少地應用了 COM 技術。通過使用現(xiàn)成的組件,軟件開發(fā)商可以避免軟件開發(fā)中許多煩瑣和困難的基礎部分,從而可以從極高的起點出發(fā),大大縮短 CAD 軟件上市周期,這樣容易取得競爭優(yōu)勢。同時,由于采用面向對象技術,使得微機 CAD 軟件的可維護性和可擴展性得以增強。3.吸收 Unix 平臺軟件的優(yōu)點新一代微機平臺 CAD 軟件充分吸取 Unix 工作站軟件的精華。諸如參數(shù)驅動、特征造型、動態(tài)導航、二維與三維雙向相關、STEP 標準和動態(tài)圖形顯示等這些比較好的特點已經(jīng)被微機平臺軟件全部吸收。二、PDM 技術的實施隨著 CAD 技術的推廣,原有的技術管理系統(tǒng)面臨著巨大的挑戰(zhàn)。在采用計算機輔助設計以前,產(chǎn)品的設計、工藝和經(jīng)營管理過程中涉及到的各類圖紙、技術文檔、工藝卡片、生產(chǎn)單、更改單、采購單、成本核算單和材料清單等均由人工編寫、審批、歸類、分發(fā)和存檔,所有的資料均通過技術資料室進行統(tǒng)一管理。自從采用計算機技術之后,上述與產(chǎn)品有關的信息都變成了電子信息。簡單地采用計算機技術模擬原來人工管理資料的方法往往不能從根本上解決先進的設計制造手段與落后的資料管理之間的矛盾。要解決這個矛盾,必須采用 PDM 技術。PDM(產(chǎn)品數(shù)據(jù)管理)是從管理 CAD/CAM 系統(tǒng)的高度上誕生的先進的計算機管理系統(tǒng)軟件。它管理的是產(chǎn)品整個生命周期內的全部數(shù)據(jù)。工程技術人員根據(jù)市場需求設計的產(chǎn)品圖紙和編寫的工藝文檔僅僅是產(chǎn)品數(shù)據(jù)中的一部分。PDM 系統(tǒng)除了要管理上述數(shù)據(jù)外,還要對相關的市場需求、分析、設計與制造過程中的全部更改歷程、用戶使用說明及售后服務等數(shù)據(jù)進行統(tǒng)一有效的管理。由此可見,PDM 系統(tǒng)管理的產(chǎn)品信息將涉及到企業(yè)的產(chǎn)品設計、工藝、制造、經(jīng)營和服務等部門。因此,PDM 系統(tǒng)的實施具有涉及面廣、信息工作量大等特點。實施 PDM 技術可以實現(xiàn)并行工程,提高產(chǎn)品設計效率,支持全面質量管理,實現(xiàn)人、過程、技術三者的平衡。因此它可以為企業(yè)帶來巨大收益。PDM 技術實施與 CAD/CAM 技術的實施不一樣,前者調整的是企業(yè)的管理模式。將原來的人工管理方式轉變?yōu)?PDM 的計算機管理模式,既要兼顧原有的管理習慣,又要考慮信息集成的要求。由于企業(yè)技術環(huán)境、管理水平、企業(yè)文化等方面的差異,每個企業(yè)的 PDM 實施過程都不會相同。只有對企業(yè)的計算機環(huán)境、企業(yè)過程以及 PDM 的總體目標有了充分的理解后,全面地分析企業(yè)對 PDM 產(chǎn)品的詳細需求,才能選出最適合本企業(yè)發(fā)展的 PDM 產(chǎn)品和解決方案。目前國際主流的 PDM 產(chǎn)品有 UG 的 IMAN,SDRC 的 Metaphase 等軟件,國內 PDM 產(chǎn)品有高華 PDM,華中 PDM 等。第 2 章 CAD/CAM 軟件簡介2.1PRO/E 簡介Pro/Engineer 包括三維實體造型、裝配模擬、加工仿真 NC 自動編程,鈑金設計、電路布線、裝配管路設計等專有模塊,ID 反求工程,鈰并行工程等先進的設計方法和模式。其主要特點是參數(shù)化的特征造型;統(tǒng)一的能使各模塊集成起來的數(shù)據(jù)庫;設計修改的關聯(lián)性,即一處修改,別的模塊中相應圖形或數(shù)據(jù)也會自動更新。它的性能優(yōu)良、功能強大,是一套可以應用于工業(yè)設計、機械設計、功能仿真、制造和管理等眾多領域的工程自動化軟件包。Pro/Engineer 自 1988 年問世以來,10 多年來已成為全世界最普及的 3DCAD/CAM 系統(tǒng)。Pro/Engineer 在今日儼然已成為 3DCAD/CAM 系統(tǒng)的標準軟件,廣泛應用于電子、機械、模具、工業(yè)設計、汽車、自行車、航天、家電、玩具、等各行業(yè)。Pro/Engineer可謂是全方位的 3D 產(chǎn)品開發(fā)軟件,集成了零件設計、產(chǎn)品裝配、模具開發(fā)、NC 加工、鈑金件設計、鑄造設計、造型設計、逆向工程、自動測量、機構模擬、應力分析、產(chǎn)品數(shù)據(jù)管理于一體,其模塊眾多。Pro/Engineer 是一套由設計至生產(chǎn)的機械自動化軟件,是新一代的產(chǎn)品造型系統(tǒng),是一個參數(shù)化、基于特征的實體造型系統(tǒng),并且具有單一數(shù)據(jù)庫功能。2.1 AUTOCAD 的簡介20 世紀 60 年代初,由美國學者首先提出 CAD 的概念。CAD(Computer Aided Design)是“計算機輔助設計”這三個詞的英文縮寫。30 多年來,CAD 技術飛速發(fā)展,其內涵也有了充實和延伸,它與 CG(Computer Graphics— 計算機圖形學)相結合形成了一門新學科。計算機繪圖是由計算機及圖形輸入/輸出設備實現(xiàn)圖形顯示及繪圖輸出,它是圖形學、計算學和計算機科學的三者結合的結晶,是CAD/CAM 的基礎之一。計算機輔助設計是利用計算機強有力的計算功能和高效率的圖形處理能力,按照設計師的意圖進行分析和計算,作出判斷和選擇,最后得到滿意的設計效果和生產(chǎn)圖紙,大大地提高提高了設計效率。第 3 章模型的設計3D 模型的建立零件模具的設計第 4 章 模型的仿真加工第 5 章 零件材料的選擇及材料性能5.1 制品的材料選擇依據(jù)5.1 .1 PS 聚苯乙烯化學和物理特性: 大多數(shù)商業(yè)用的 PS 都是透明的、非晶體材料。PS 具有非常好的幾何穩(wěn)定性、熱穩(wěn)定性、光學透過特性、電絕緣特性以及很微小的吸濕傾向。它能夠抵抗水、稀釋的無機酸,但能夠被強氧化酸如濃硫酸所腐蝕,并且能夠在一些有機溶劑中膨脹變形。典型的收縮率在0.4~0.7%之間。 注塑模工藝條件 干燥處理:除非儲存不當,通常不需要干燥處理。如果需要干燥,建議干燥條件為80C、2~3 小時。熔化溫度:180~280C 。對于阻燃型材料其上限為 250C。模具溫度:40~50C 。注射壓力:200~600bar。注射速度:建議使用快速的注射速度。流道和澆口:可以使用所有常規(guī)類型的澆口。典型用途: 產(chǎn)品包裝,家庭用品(餐具、托盤等) ,電氣(透明容器、光源散射器、絕緣薄膜等) 。5.1 .2 PS 主要技術指標如下表:密度(g/cm3) 1.05~1.08 抗拉屈服強度(Mpa) 42~56比容(cm3/g) 0.92 拉伸彈性模量(Mpa)吸水率 24h(%) 0.03~0.10 沖擊強度 無缺口收縮率(%) 0.4~0.7 kj/m2 缺口熔點(℃ ) 180~280(230) 彎曲強度(Mpa)硬度(HB)熱變形溫度(℃)體積電阻率5、2 分析計算:在 PRO/E 中可以分析得到:體積 = 1.0808451e+05 毫米^3曲面面積 = 1.3020789e+05 毫米^2密度 = 1.0500000e-03 克 / 毫米^3質量 = 1.1348874e+02 克 根據(jù)_PART 坐標邊框確定重心:X Y Z -1.8645351e-03 1.7856011e+01 7.9160117e+00 毫米相對于_PART 坐標系邊框之慣性. (克 * 毫米^2)慣性張量Ixx Ixy Ixz 6.4489761e+05 0.0000000e+00 1.8113848e+01Iyx Iyy Iyz 0.0000000e+00 8.3525619e+05 -1.5908008e+04Izx Izy Izz 1.8113848e+01 -1.5908008e+04 3.3634826e+05重心的慣性(相對_PART 坐標系邊框) (克 * 毫米^2)慣性張量Ixx Ixy Ixz 6.0160161e+05 -3.5702160e+00 1.6438790e+01Iyx Iyy Iyz -3.5702160e+00 8.2814462e+05 1.3344275e+02Izx Izy Izz 1.6438790e+01 1.3344275e+02 3.0016384e+05主慣性力矩 (克 * 毫米^2)I1 I2 I3 3.0016381e+05 6.0160161e+05 8.2814465e+05從_PART 定位至主軸的旋轉矩陣:-0.00005 1.00000 -0.00002-0.00025 0.00002 1.000001.00000 0.00005 0.00025從_PART 定位至主軸的旋轉角( 度):相對 x y z 的夾角 -89.986 0.000 -90.003 相對主軸的回旋半徑:R1 R2 R3 5.1428372e+01 7.2807835e+01 8.5423374e+01 毫米208*156*52-13第 6 章 塑料注射成型模具的設計6、1 注射機類型的選擇根據(jù)產(chǎn)品的注射形式和最大注射量等要求,選用臥式注射機型號 SZ160/1000 拉桿內間距(mm) 360*260結構型式 臥式 移模行程(mm) 280理論注射容量(cm3) 179 最大模具厚度(mm) 360螺桿直徑(mm) 44 最小模具厚度(mm) 170注射壓力(Mpa) 150 鎖模形式 液壓注射速率(g/s) 110 模具定位孔直徑(mm) 125塑化能力(g/s) 10.5 噴嘴球半徑(mm) SR10螺桿轉速(r/min) 10~150 噴嘴口孔徑(mm)鎖模力(KN) 10006、2 注射機有關工藝參數(shù)的校核6、2 、1 注射量的校核據(jù)式 注件 V8.0?式中: —塑件與澆注系統(tǒng)的體積( )件 3cm—注射機的注射量( )注 30.8—最大注射容量的利用系數(shù)0.8V V注 ?件0.8V =0。8*179=143.2cm注 3巳知:產(chǎn)品 V =113.5 cm件 3符合條件。6、2 、2 鎖模壓力的校核鎖模力是在成型時鎖緊模具的最大力,用于實現(xiàn)動、定模緊密閉合保證塑料制品的尺寸精度,盡量減少分型面處的溢邊(或毛邊)厚度和確保操作者的人身安全。因此,成型時高壓熔融塑料在分型面上顯現(xiàn)的漲力(或稱推力)應小于鎖模力。/1000(KN) [4]155 mKAPF?鎖式中: —注射機的額定鎖模力(KN)鎖A— 制品和分流道在分型面上的投影面積( )2cm—型腔的平均壓力(Mpa) ,PS 等薄壁類容器制品一般取mP30MpaK—安全系數(shù),通常取 K=1.1~1.2已知:K=1.1, 模型的投影面積 = 29252.9MpaPm30? 2mK A/1000=1.1*30* 29252.9/1000=960.382KN 1000KNmP ?滿足要求。6、2、3 注射壓力的校核注射壓力是成型時柱塞或螺桿施于料筒內熔融塑料上的壓力。常取70~150Mpa。注成 P?式中 —塑件成型所需要的注射壓力(Mpa) ,一般取 100Mpa成—所選注射機的額定注射壓力(Mpa)注P已知 ;P =132MpaMpa10?成 注故滿足要求6、2 、4 注射速率注射速率即注射過程中每秒鐘通過噴嘴的塑料容量。常取 33~58 mm/s.6、2 、5 模具閉合厚度的校核模具閉合時的厚度在注射機動、定模板的最大閉合高度和最小閉合高度之間,其關系按下式校核Hmin≤H m≤H max式中 Hmin—注射機允許的最小模具厚度(mm)Hm—模具閉合厚度(mm)Hmax—注射機允許的最大模具厚度(mm)已知:H = 170mm H =mm H =360mmminmmax所以滿足要求第 7 章 成型零件的設計7、1 型腔分型面的設計a 分型面的位置要不影響制品的精度和外觀b 盡量簡單,避免采用復雜形狀,使模具制造增加困難c 要盡量有利于塑料制品的脫模和抽芯d 有利于澆注系統(tǒng)的合理設置e 盡可能與料流末端重合,以利于系統(tǒng)排氣按以上原則選取。7.2 排氣槽的設計該注射模屬于中小型模具,在推桿的間隙和分型面上都有排氣效果,已能滿足要求,故不再考慮排氣槽。7·3 成型零件的設計7、3、1 凹模的結構設計考慮到注塑零件的結構和模具的加工,凹模結構采用整體式,其特點是牢固,不易變形。7、3、2 型芯結構設計主型芯采用局部嵌入固定。其特點是節(jié)約模具鋼的便于加工。7、3、3 成型零件工件尺寸7、3、3、1 型腔與型芯的尺寸計算(1)型腔內徑尺寸計算Dm=(D+DQ-3/4* ) (mm) ?z??Dm——型腔內徑 (mm)D——制品的最大尺寸( mm)Q——塑料平均收縮率(%) 取 0.5 % ——制品公差 ?3/4——系數(shù),可隨制品精度變化。一般取 0.5~0.8 之間。若制品偏差大則取小值,若制品偏差小則取大值——模具制造公差,一般取 =(1/6~1/4) z?零件的長度最大尺寸為 D =208mm,取 9 級精度,查得 =0.115,則1 ?D =(207+207*0.005- *0.115) =208.124 mm1M4325.0?25.0?零件的寬度最大尺寸 D =156mm,同樣查得 =0.100,則2 ?D =(154+154*0.005- *0.100) =154.855 mm2M4325.0?25.0?(2)型芯徑向尺寸的計算模具型芯徑向尺寸是由制品的內徑尺寸所決定的,與型腔徑向尺寸的計算原理一樣,分為兩個部分來計算:dm= mm??ZQD????341式中: dm—型芯外徑尺寸(mm)D1—制品內徑最小尺寸(mm)其余的符號含義同型腔計算公式零件內徑長度最大尺寸 d =197mm, =0.1151?d =(197+197*0.005+ *0.115) = 198.060 mm1m4325.0?25.0?零件內徑寬度最大尺寸 d =147mm, =0.100mm2d =(147+147*0.005+ *0.100) =147.810 mm2m4325.0?25.0?(3)型腔深度尺寸計算模具型腔深度尺寸是由制品的高度尺寸所決定的,設制品高度名義尺寸為最大尺寸,其公差 為負偏差。型腔深度名義尺寸為最小尺寸,?其公差為正偏差+ 。z?HM= (mm)ZQh???????????321H ——型腔深度尺寸(mm)h1——制品高度最大尺寸(mm)最大尺寸 h1=52mm, =0.074?H =(52+52*0.005+ *0.074) = 52.310 mmM3225.0?25.0?(4)型芯高度尺寸計算模具型芯的高度尺寸是由制品的深度尺寸決定的,假設制品深度尺寸H1 為最小尺寸,其公差為正偏差+△,型芯高度尺寸為最大尺寸,其公差為負偏差- 。根據(jù)有關的經(jīng)驗公式:z?hM= (mm) 0132ZQH??????????hM—型芯高度尺寸(mm)H1—制品深度最小尺寸(mm)其余公式中字母的含義同前面的含義深度最小尺寸 H =48.5mm, =0.0431?h =(48.5+48.5*0.005+ *0.043) =48.772 mmM3225.0?25.0?(5)型腔壁厚與底板厚計算注射成型模型壁厚得確定滿足模具剛度好、強度大和結構輕巧、操作方便等要求。在塑料注射充型過程中,塑料模具型腔受到熔體的高壓作用,故應有足夠的強度、剛度。否則可能因為剛度不足而產(chǎn)生塑料制件變形損壞,也可能會彎曲變形而導致溢料和飛邊,降低塑料的尺寸精度,并影響塑料制品的脫模。從剛度計算一般要考慮下面幾個因素:a. 使型腔不發(fā)生溢料,ABS 不溢料的最大間隙為 0.05。b. 保證制品的順利脫模,為此,要求型腔允許的彈性變形量小于制品冷卻固化收縮量。c. 保證制品達到精度要求,制品有尺寸要求,某些部位的尺寸常要求比較高的精度,這就要求模具型腔有很好的剛度。經(jīng)驗數(shù)據(jù)A、矩形型腔側壁厚度的確定。側壁厚度一般取制品長度 (長的邊長)或直徑 D 的 0.2~0.5 倍。當1L型腔為整體式, 100mm,需要乘以 0.85~0.9。在 p49Mpa 時,1mS72.01??因此S=0.2*208*0.9+17=58.6mm取側壁厚度 60mm 就滿足要求。B、矩形型腔底板厚度的確定因為 p49Mpa, L 1.5b?查表可得 S =0.08*156=0.08*156=12.3mmh取底板厚度 15mm 就滿足要求。7、4 塑件脫模機構的設計由于改塑件脫模阻力不大,而頂桿加工簡單、更換方便、脫模效果好,因此選用頂桿脫模機構。而中間的部分采用推管機構。推桿位置的設置采取了以下的原則:a 推桿設在脫模阻力大的地方b 推桿位置均勻分布c 推桿設在塑料制品強度剛度大的地方d 推桿直徑應滿足相應的剛度、強度條件,在滿足條件的前提下,應盡量選用直徑較大的推桿。本次設計的零件,所以推桿直徑取得比較小,為了達到強度剛度要求設置了較多的推桿。7、4 脫模力計算矩環(huán)形薄壁制品 s/d 0.05 F= (N)? AktgfSEQl1.0)1(cos22????r——型芯平均半徑 (m)S——制品壁厚 (m)E——塑料彈性模量 (Mpa) Q——塑料平均收縮率 (%)l——制品對型芯的包容長度 (m)f——制品與型芯靜摩擦系數(shù) f=0.1~0.2——脫模斜度 ( ) 取 1 ?om——塑料的泊松比 m=0.38~0.42 k ——系數(shù) k =2 /(cos +2 cos )1 12?2??k ——系數(shù) k =1+fsin cos 12 2?A——盲孔制品型芯在脫模方向投影面積 (m )2已知 , ,S3105.???MpaE3108.??05.?Q, , , ,l2.f??2k43?、29.mAF= +0.1*0.029=6052N1*)43.0( )12.0(cos51*8.05.*9??tg7、5 側向分型與抽芯機構設計本次設計有一個側向型芯。所以使用外側抽芯。(1)斜導柱 斜導柱直徑 d 與導柱孔應保持 0.5~1mm 的間隙。(2)導柱的角度 本設計 α=18°,楔緊塊角度為 20°。(3)抽心距的計算 通常抽心距等于側芯深度加 2~5mmS=13+4=17mm(4)斜導柱工作部分長度L =S/sin18 =5640開模行程H=Sctg18 =530(5)抽拔力的計算F1=lhp(fcosθ-sinθ)式中 l—活動側芯被塑料包緊的斷面周長(m);h—成型芯部分的深度(m);p—制品對側心的壓力,一般取 8~12Mpa;f—塑料對鋼的摩擦系數(shù),常用 f=0.1~0.2;θ—側芯的脫模斜度,常取 θ=1°~2°。已知 l=132mm,h=13mm,p=10Mpa,f=0.2, θ=1°F1=0.132×0.013×10×106×(0.2×cos1°-sin1°)=3132N(6)斜導柱所受彎曲力的計算P=θ/cosαP—彎曲力Q—抽拔阻力(與抽拔力大小相等,方向相反)α—斜導柱的傾斜角∴P=3132/cos18°=3293N(7)斜導柱直徑的計算d= ??31.0彎?pl式中 p—最大彎曲力;l—斜導柱有效工作長度;[σ] 彎 —彎曲許用應力,對碳鋼可取 137Mpad=23.79mm取標準斜導柱的公稱直徑為 25。第 8 章 澆注系統(tǒng)的設計澆注系統(tǒng)是指模具中從注射機噴嘴開始到型腔為止的塑料流動通道。澆注系統(tǒng)設計好壞對制品性能,外觀和成型難易程度影響頗大。根據(jù)注塑件的要求及模具的結構等方面來考慮選擇澆注系統(tǒng)。設計原則(1)能順利地引導熔融塑料充滿型腔,不產(chǎn)生渦流,又有利于型腔內氣體的排出。(2)在保證成型和排氣良好的前提下,選取短流程,少彎折,以減小壓力損失,縮短填充時間。(3)盡量避免熔融塑料正面沖擊直徑較小的型芯和金屬嵌件,防止型芯位移或變形。(4)澆口料容易清除,整修方便,無損制品的外觀和使用。(5)澆注系統(tǒng)流程較長或需要開設兩面?zhèn)€以上澆口時,由于澆注系統(tǒng)的不均勻收縮導致制品變形,應設法防止。(6)在一模多腔時,應使各腔同步連續(xù)充澆,以保證各個制品一致性。(7)合理設置冷料井、溢料槽,使冷料不得直接進入弄腔及減小毛邊的負作用。(8)在保證制品質量良好的條件下,澆注系統(tǒng)的斷面和長度應盡量取小值,以減小對塑料的占用量,從而減小回收料。8、1 主流道的設計斷面形式:截面形狀采取圓形,這種形狀熱量損失小,流動阻力小,效果最佳,但加工較難。注射機的噴嘴頭部與主流道襯套的凹下的球面半徑 R 相接觸,二者必須匹配,無漏料。一般要求主襯套球面半徑 R 比噴嘴球面半徑大1~2mm,主流道進口直徑 d 比注射機噴嘴出口直徑 d 應大 0.5~1mm.其1作用:一是補償噴嘴與澆注道的對口誤差;二是使噴嘴與主襯套球面配合良好。為了便于凝料從主流道中拔出,主流道設計成圓錐形,其半錐角a=2°~4°,表面粗糙度應有 Ra=0.8 以上。主流道出口應做成圓角,圓角半徑 r=0.3~0.5mm 或 r=d /8.為減少壓力損失,主流道長度盡可能短些,2常取 L 60mm。?噴嘴球面半徑為 10mm (見上注射機技術參數(shù))主襯套球面半徑 R 取 12mm主流道進口直徑 d 取 4.5mm1主流道出口直徑 d 取 6mm2半錐角 a=3°主流道長度 L 取 45mm8、2 澆口的設計取用直接澆口,直接澆口是直接和主流道連接,由主流道直接進料。它可以做成頂澆口和中心澆口。由于澆口尺寸大,熔體壓力損失小,流動阻力小,進料快,容易成型,適用于任何塑料,常用于成型單腔模,大而深的殼型制品。因為流程短,壓力傳遞好。熔體從上端流向分型面(低端) ,故有利于排氣和消除接痕。直接澆口進、出口端直徑 d 、d 可以由主澆道的尺寸決定,它12第 9 章塑料溫控系統(tǒng)設計在注射工藝過程中,模具的溫度直接影響著制品質量和注射周期,各種塑料的性能、成型工藝要求的不同相應的模具對溫度的要求也不同,PS 在注射成型進所需要的模具溫度為 40~60℃,對于任何塑料制品,模具的溫度的波動較大都是不利的,過高的模具溫度會使塑料制品在冷卻脫模后發(fā)生變形,延長冷卻時間降低生產(chǎn)率,為了避免這種現(xiàn)象的發(fā)生,就必須采取模具溫度調節(jié)系統(tǒng)。塑料傳給模具的熱量:Q=n m C (T1-T2)式中: Q—單位時間內塑料傳給模具的熱量 KJ/h;n—每小注射的次數(shù);m—每次注射的塑料量,包括澆江系統(tǒng)(kg);C—塑料的比熱容(J/kg·℃) ;T1—熔融塑料進入模腔的溫度(℃) ;T2—制品脫模溫度(℃) ;選定注射機每小時注射的次數(shù)為 50,則根據(jù)以上公式:PS 的 C=1340(J/ kg·℃);已知 m=0.16, T1=180℃, T2=60℃,選定注射機的每小時注射的次數(shù)為 50,則根據(jù)以上的公式,得Q=50×0.16×1340×(180-60)=1.30×106 (KJ/h)冷卻時所需要的冷卻水量 )(431TQM???式中: M1—通過模具的冷卻水的質量(kg);T3—出水溫度(℃) ;T4—進水溫度(℃) ;λ—導熱系數(shù)(J/m·℃);由由[4]表 8-26,查得 λ=452(J/m·℃)所以有冷卻水的質量:M1= kg2486350.6??根據(jù)冷卻水處于湍流狀態(tài)下的流速 v 與水管道直徑 d 的關系,確定模具冷卻水道直徑 d:d= ??v/10413?式中:M 1—冷卻水的質量(Kg);v—管道內冷卻水的流速,一般取 0.8~2.5m/s;ρ—水的密度(Kg/m 3)。根據(jù)以上公式: md2.14)02/(486103?????取冷卻水管道的直徑為 14mm.冷卻管道總傳熱面積計算公式: TRMA??1式中:R—冷卻管道壁與冷卻介質間的傳熱系數(shù)(J/m 2·℃)(J/m 2·℃)??2.08.47dvf?f—與冷卻介質有關的物理系數(shù),查表 8-29[4] 得,f=7.98ΔT— 模具溫度與冷卻介質之間的平均溫度;其余符號意義同上∴??2363 62.08.1751.80649.74mAR?????其中 ΔT=(60+40)/2=50℃冷卻管道的孔數(shù):n= dLA?式中 A—冷卻裝置總的傳熱面積(m 2);d—冷卻水管管道直徑(m);L—冷卻管道的長度(m) 。則 08.1201473.033????????n所以,冷卻水道的孔數(shù)在動、定模板之中各取一個就可以達到冷卻的要求。由于 PS 是要求模溫較低的塑料,不斷注入的熔融塑料使模溫能夠達到PS 注射成型所需的模溫,所以不必考慮需要加熱提升溫度的。第 10 章 標準模架的選擇本次設計選用的標準模架型號是:A —500500—42—Z GB/T12556.1—902 3A ——品種(基本型號)500500——系列(模板周邊尺寸)42——規(guī)格(基本組合編號)Z ——導柱的安裝方式3畢業(yè)論文(設計)任務書論文(設計)題 目 筆筒抽屜注塑模具設計工程 院(系) 專業(yè) 級學生姓名指導教師 職務起訖日期設計地點發(fā)任務書日期: 1畢業(yè)論文(設計)任務的內容和要求(包括原始數(shù)據(jù)、技術要求、工作要求)設計題目: 注塑模具設計設計依據(jù):1 、生產(chǎn)綱領:大批量生產(chǎn)2、零件圖3、國家有關注射模具設計標準。設計要求:(一)注射模實體設計(1) 、分析塑件圖工藝性和工藝條件 首先了解塑件的用途、使用情況及工作要求,對于塑件圖上提出的塑件形狀、尺寸精度、表面粗糙度等工藝分析,即從成型工藝、塑件的設計原則、模具結構合理性等方面進行綜合分析。(2) 、確定塑件成型工藝及設備1)確定成型工藝條件,包括注射溫度、模具和冷卻介質的溫度、注射速度和注射循環(huán)周期等。2)根據(jù)塑件形狀尺寸,估算塑件體積和重量。確定型腔數(shù)。3)選擇設備型號規(guī)格,并校核與模具有關的技術參數(shù),包括額定注射量,注射壓力、鎖模力、最大、最小模厚、開模行程、推出裝置及裝模部分的尺寸(模板尺寸、拉桿空間、定位孔直徑、噴嘴定位半徑等) 。(3)確定模具總體結構方案1) 選擇成型位置、確定分型面、脫模方式、側孔、側凹的成型方法、澆注系統(tǒng)形式、澆口開設位置等。22) 選擇合適的標準模架,確定模具成型零件的材料和加工方法。3) 通常需構思幾種模具結構方案,采用容易制造、便于操作、確保成型塑件質量的模具結構。(4)繪制模具裝配圖(5)對模具各部分進行受力分析 對模具進行必要的強度及剛度計算,對于薄弱部分在結構上進行加強。(6)成型零件成型尺寸的計算。(7)加工零件工作圖的繪制。(8)完成二維模具結構總體設計。(二)用 CAD/CAM 軟件進行模具構件的三 D 造型,并演示其加工過程。1.用三維 CAD 軟件(Pro-E、Caxa 等)構建三維曲面或實體模型要求:所構建的模型直接決定能否加工,并決定了型腔質量,故要求所構建的模型美觀、無錯誤。2. 所構建的模型正確分模3. CAM 軟件(MasterCam、Caxa 等)對上下模型腔進行銑削模擬加工,生成刀具路徑。需確保所生成的刀具路徑能完善地加工出上下模腔,不允許有粗劣的刀路;保證加工過程中不產(chǎn)生過切或切不到的現(xiàn)象;避免刀具和工件的干涉。要求:(1)較好地構建加工輔助線、面(2)確定合理的粗、精加工工序數(shù),(3)對每道加工工序,正確地選擇加工方法,并正確地選擇刀具和加工參數(shù),3如刀具半徑、主軸轉速、進給速度、切削深度、走刀刀距、走刀方向等。(4)查看刀具路徑,能從中發(fā)現(xiàn)三維造型或加工中的錯誤,并進行修正。4.對所生成的刀具路徑進行模擬仿真。4. 對刀具路徑進行后置處理,生成 NC 文件。45圖紙內容及張數(shù)零件圖 1 張模具總體裝配圖 1 張凹凸模零件圖 1 張非標準零件圖 若干張補充零件加工圖 若干張實物內容及要求6其 他1、設計說明書 1 份 6000 字左右2、外文資料譯文 1 份7參考文獻8主要參考文獻:1.《注塑模具設計與制造實用技術》 王樹勛 主編 西安電子科技長出版社 2001.32.《實用模具設計與制造手冊》 葉偉昌 主編 -北京:機械工業(yè)出版社出版,1999.53. 《塑料成型加工與模具》 黃虹 主編 化學工業(yè)出版社4. 《塑料擠塑模與注射模優(yōu)化設計》 李遠波 主編1、 《塑料模具設計 》 機械工業(yè)出版社2、 《模具標準應用手冊 》 機械工業(yè)出版社3、 《實用塑料注射模設計與制造》 機械工業(yè)出版社5、 《注射成型模具設計 108 例》 中國輕工業(yè)出版社6、 《機械零件設計手冊 》 冶金工業(yè)出版社8、 《模具技術 》 上海交通大學出版社9、 《Pro-E 模具設計與數(shù)控加工 》 易際明等編著 清華大學出版社10、 《CAXA 數(shù)控機床操作機仿真試訓教程》 北京航空航天大學出版社 11、 《CAXA 實體設計》 北京航空航天大學出版社9畢業(yè)論文(設計)進度計劃起訖日期 工 作 內 容 備注4.30~5.3 確定模具總體結構方案5.4~ 5.17 繪制模具裝配圖5.18~5.21 零 件 圖5.22~5.28 用 Pro-E 等 構 建 三 維 實 體 模 型 和 模 擬 加工5.29~6.4 寫 畢 業(yè) 設 計