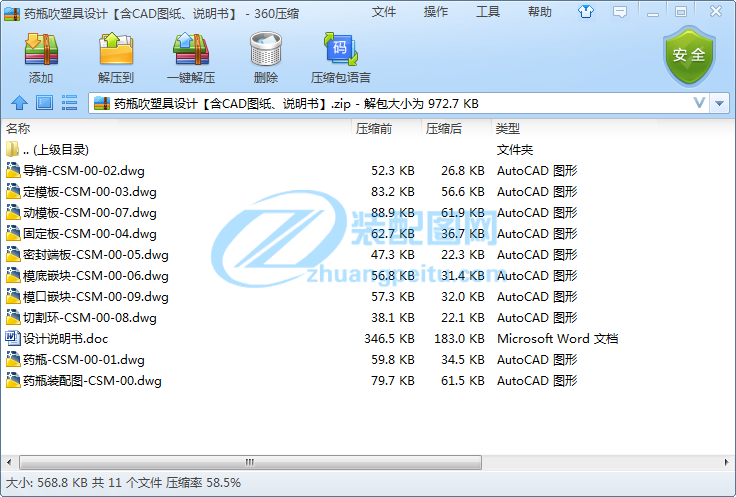
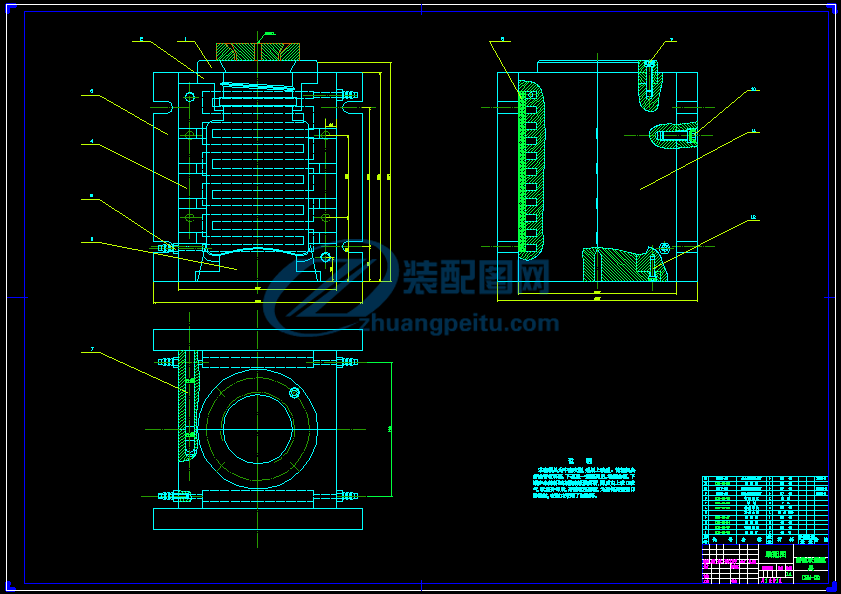
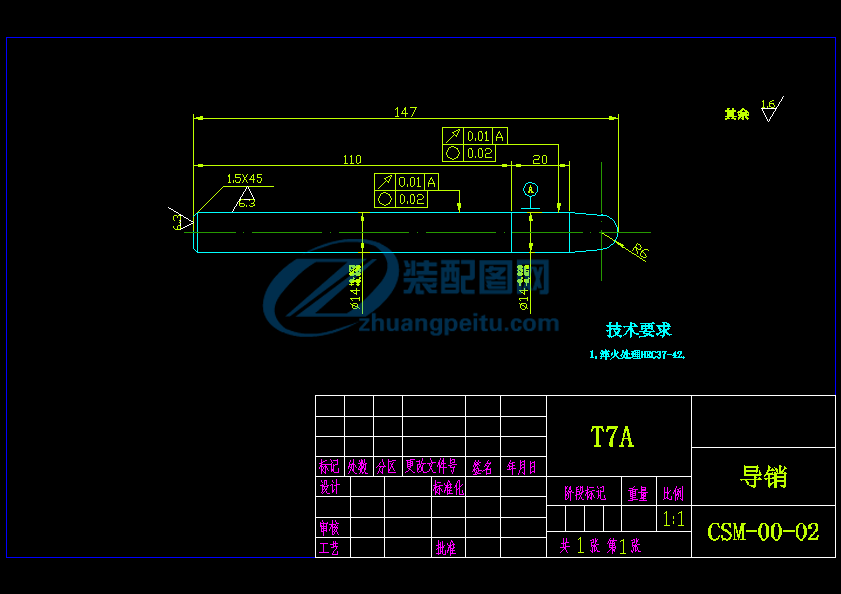
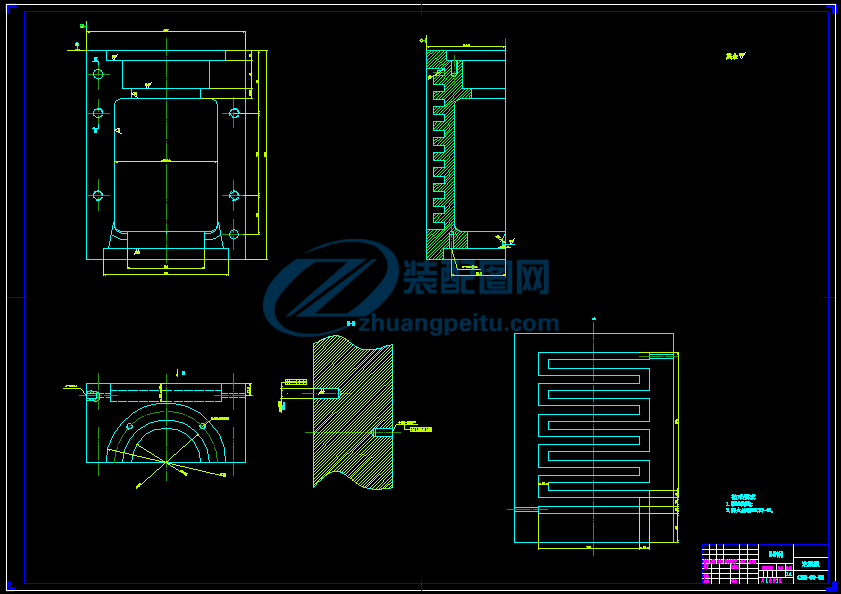
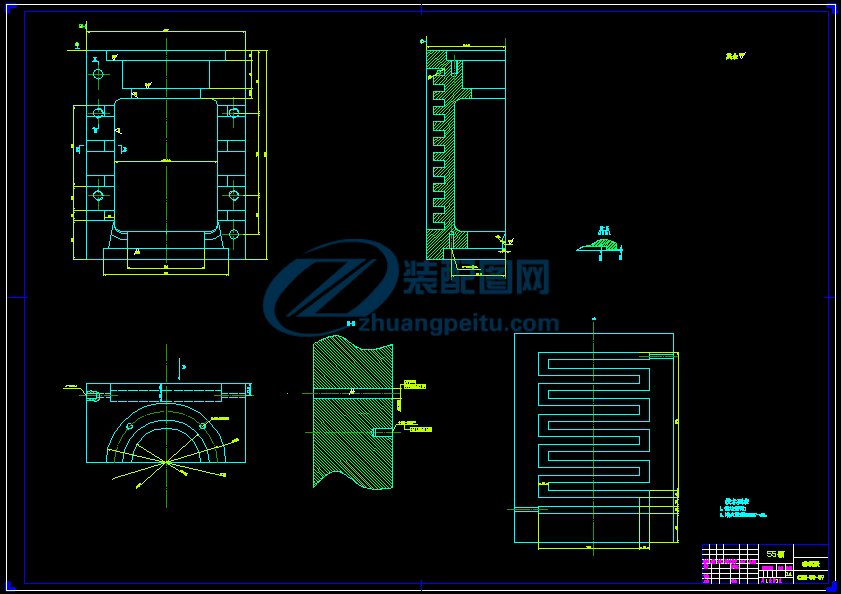
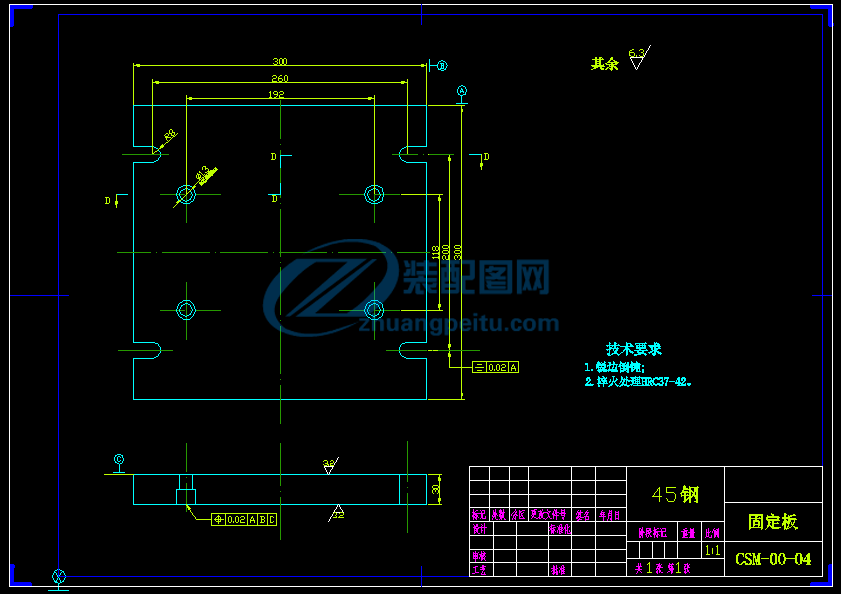
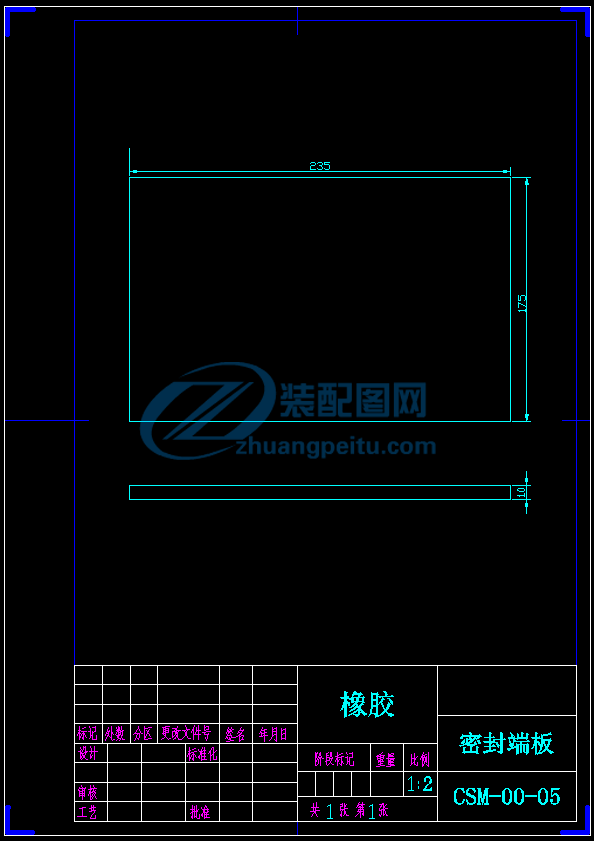
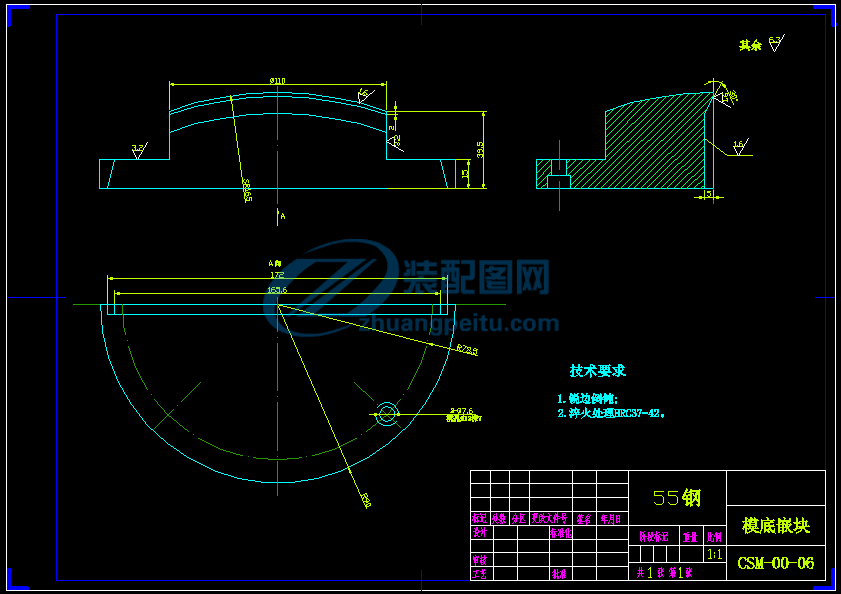
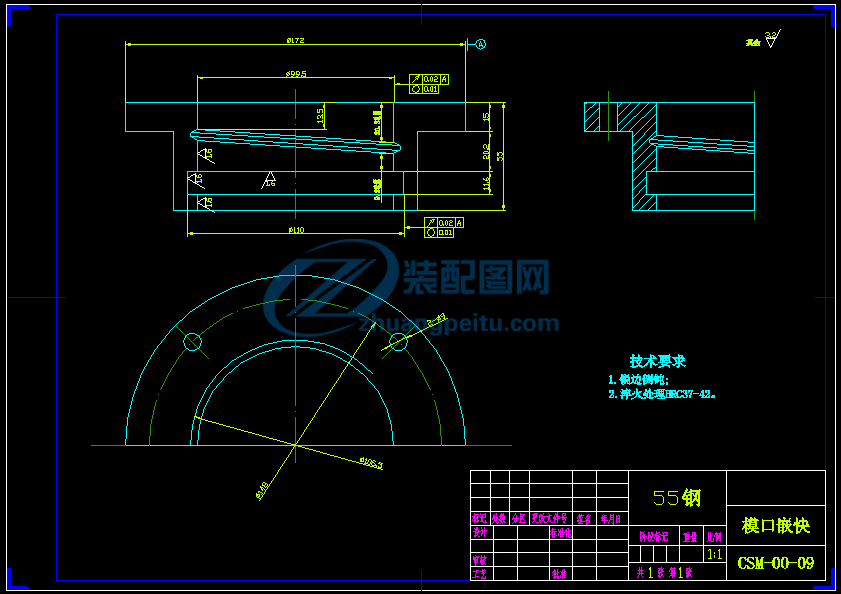
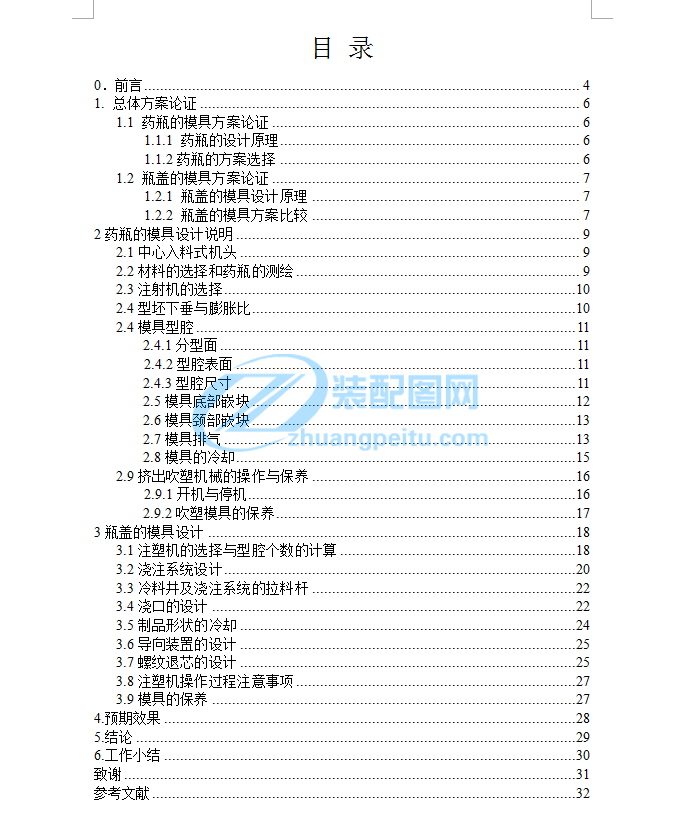
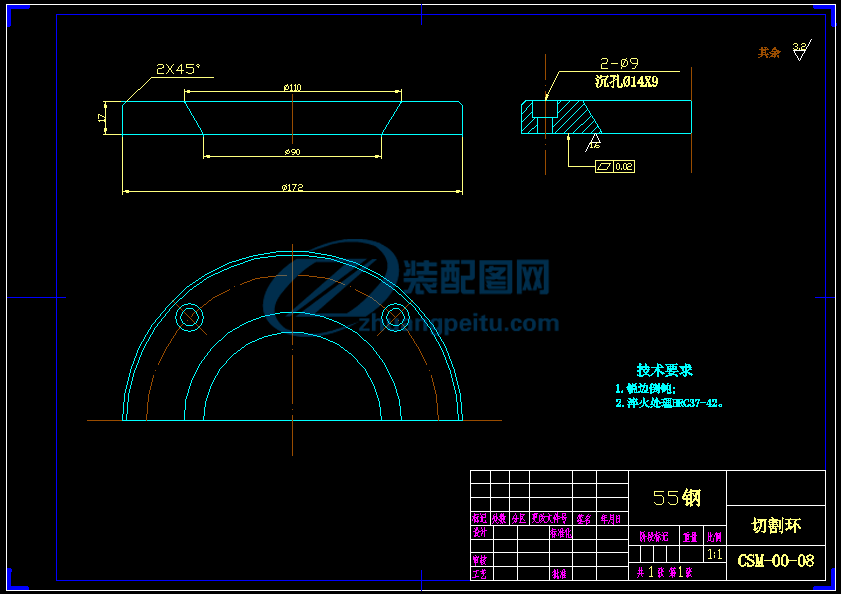
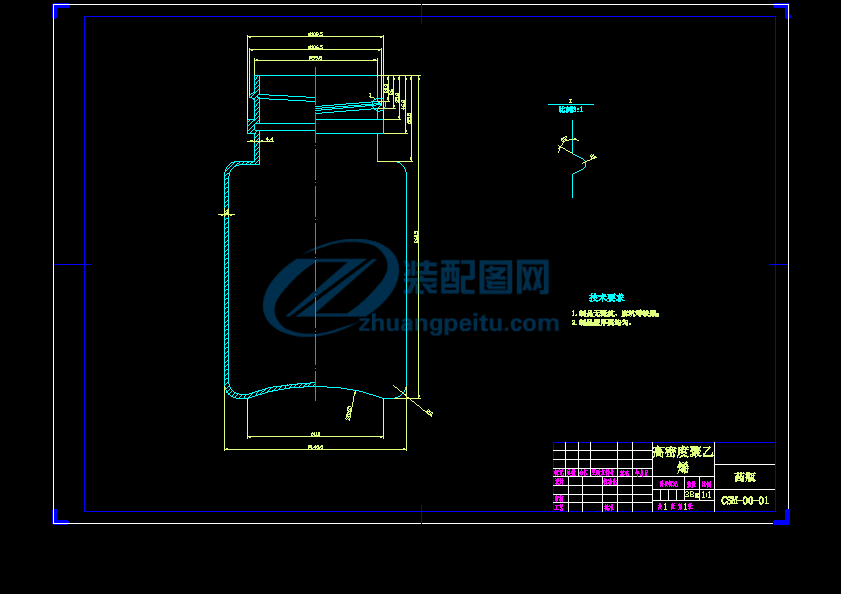
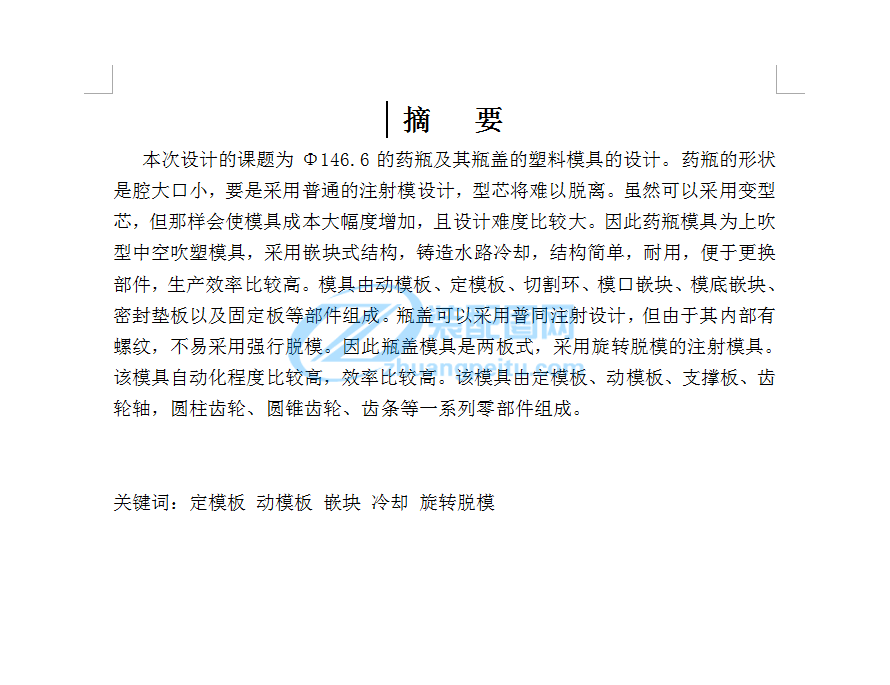
- 1 -摘 要本次設(shè)計的課題為 Φ146.6 的藥瓶及其瓶蓋的塑料模具的設(shè)計。藥瓶的形狀是腔大口小,要是采用普通的注射模設(shè)計,型芯將難以脫離。雖然可以采用變型芯,但那樣會使模具成本大幅度增加,且設(shè)計難度比較大。因此藥瓶模具為上吹型中空吹塑模具,采用嵌塊式結(jié)構(gòu),鑄造水路冷卻,結(jié)構(gòu)簡單,耐用,便于更換部件,生產(chǎn)效率比較高。模具由動模板、定模板、切割環(huán)、模口嵌塊、模底嵌塊、密封墊板以及固定板等部件組成。瓶蓋可以采用普同注射設(shè)計,但由于其內(nèi)部有螺紋,不易采用強行脫模。因此瓶蓋模具是兩板式,采用旋轉(zhuǎn)脫模的注射模具。該模具自動化程度比較高,效率比較高。該模具由定模板、動模板、支撐板、齒輪軸,圓柱齒輪、圓錐齒輪、齒條等一系列零部件組成。關(guān)鍵詞:定模板 動模板 嵌塊 冷卻 旋轉(zhuǎn)脫模- 2 -AbstractThe program of this design is Φ the medicine bottle of 146.6 and the plastic pattern of its cap have design . the shape of medicine bottle is cavity big mouth little, if design , type core with ordinary injection mould will be hard slip away . may adopt though change type core, can but so make mould cost increase substantially, design difficulty just compare big. therefore the mould of medicine bottle is blow type hollow blow mould mould, adopt inlay piece type structure, casting waterway cool , structure simple, durable, change parts easily, production efficiency is ring and mould high fairly. mould from the fixed die board and board of movable mould , cut mouth inlay piece and mould base inlay piece, gaskets board as well as the etc. parts of fixed head form . cap may adopt general inject design together, but have thread because of its inside, do not be easy adopting force take off mould. therefore cap mould is two board type, adopt spin take off the injection mould of mould have . this mould automation level is mould high fairly, efficiency is high fairly. this mould from fixed die board, the board of movable mould, gripper shoe, gear axle, cylinder gear, cone gear, rack and such a series of component composition.Keywords: the fixed die board board of movable mould inlay piece cool spin take off- 3 -目 錄0.前言 41. 總體方案論證 .61.1 藥瓶的模具方案論證 .61.1.1 藥瓶的設(shè)計原理 61.1.2 藥瓶的方案選擇 .61.2 瓶蓋的模具方案論證 .71.2.1 瓶蓋的模具設(shè)計原理 71.2.2 瓶蓋的模具方案比較 72 藥瓶的模具設(shè)計說明 .92.1 中心入料式機頭 92.2 材料的選擇和藥瓶的測繪 92.3 注射機的選擇 102.4 型坯下垂與膨脹比 102.4 模具型腔 112.4.1 分型面 .112.4.2 型腔表面 .112.4.3 型腔尺寸 .112.5 模具底部嵌塊 122.6 模具頸部嵌塊 132.7 模具排氣 132.8 模具的冷卻 152.9 擠出吹塑機械的操作與保養(yǎng) 162.9.1 開機與停機 .162.9.2 吹塑模具的保養(yǎng) .173 瓶蓋的模具設(shè)計 .183.1 注塑機的選擇與型腔個數(shù)的計算 183.2 澆注系統(tǒng)設(shè)計 203.3 冷料井及澆注系統(tǒng)的拉料桿 223.4 澆口的設(shè)計 223.5 制品形狀的冷卻 243.6 導向裝置的設(shè)計 253.7 螺紋退芯的設(shè)計 253.8 注塑機操作過程注意事項 273.9 模具的保養(yǎng) 274.預期效果 .285.結(jié)論 .296.工作小結(jié) .30致謝 31參考文獻 32- 4 -0.前言12 月 11 日,中國正式成為世貿(mào)組織成員。中國加入 WTO 這個被稱為“經(jīng)濟聯(lián)合國”的組織,中國的各個行業(yè)將被進一步開放。作為機械工業(yè)行業(yè)之一的模具行業(yè)也將受到影響??傮w來說,應是機遇大于挑戰(zhàn)。加入世貿(mào)組織后,我國將獲得一個更加穩(wěn)定的國際經(jīng)貿(mào)環(huán)境,從而有利于我國的改革開放.有利于我國與各國、各地區(qū)的經(jīng)濟貿(mào)易合作,有利于世界經(jīng)濟的穩(wěn)定發(fā)展。我國在制定法律法規(guī)時要遵守 WTO 的規(guī)則,增加透明度,減少行政干預等;在市場開放方面,需要逐步降低關(guān)稅,取消非關(guān)稅措施,開放服務業(yè)市場等。這無論在觀念上還是在體制上都會帶來一定的變化。我國加入 WTO 同時也將為各國、各地區(qū)的貿(mào)易伙伴提供更好、更穩(wěn)定的市場進入機會。使我國的投資環(huán)境將更為寬松、透明、穩(wěn)定,我國的利用外資領(lǐng)域?qū)⑦M一步擴大,我國的市場體系將更加完善和發(fā)達。國內(nèi)和國外模具企業(yè)都可以從中得到更多的機會和收益。 由于國內(nèi)某些模具在技術(shù)上和質(zhì)量上與國外先進水平存在著較大的差距,使短期內(nèi)國內(nèi)模具難以與國外先進模具的抗衡。這對我國模具產(chǎn)業(yè)將產(chǎn)生一定的沖擊。另一方面也促進國內(nèi)行業(yè)優(yōu)化資源配置、調(diào)整經(jīng)濟結(jié)構(gòu)、提高社會勞動效率,促使企業(yè)苦練內(nèi)功,提高管理水平。應該清醒地認識到競爭才會帶來更快的發(fā)展.只要發(fā)揮自身優(yōu)勢,減少技術(shù)差距,我國的模具必將逐步占領(lǐng)國內(nèi)市場,并拓展國際空間塑料模是應用最廣泛的一類模具。在國外,塑料模占模具行業(yè)的 50%以上,而我國只有 30%左右,因而有較大的發(fā)展空間。近年來,我國塑料模有長足的進步。但模具制造周期仍比國外長 2-4 倍,模具的質(zhì)量穩(wěn)定性較差,總體水平與國外比尚有較大差距。而塑料模的主要應用領(lǐng)域:汽車摩托車行業(yè),家電電子行業(yè)在加入 WTO 后將會有更多的新產(chǎn)品開發(fā),對各個檔次的模具需求均有大幅增長??傮w來說,塑料模將是發(fā)展最快的一類模具。加入 WTO 之后,模具企業(yè)將在開放的環(huán)境中與國外的企業(yè)在同一市場上展開競爭。模具企業(yè)必須做到以下幾項,才能在激烈的競爭獲得一席之地:1、加強吸收和引進國外先進技術(shù),盡量提高產(chǎn)品的技術(shù)含量;2、提高管理水平,抓好模具的質(zhì)量,提高生產(chǎn)率,保證模具準確的交貨期;3、增加科技術(shù)方面的投入,加強人才培養(yǎng),提高職工的工作積極性;4、做好模具的售后服務,建立長期穩(wěn)定的客戶關(guān)系。同時,模具企業(yè)之間應建立一種合作的關(guān)系,共同提高競爭力,以艦隊的形式應戰(zhàn)。- 5 -目前,塑料工業(yè)已形成設(shè)計、生產(chǎn)、檢測、標準以及教學等一套完整的工業(yè)體系。就其制品而言,如木材般輕盈、鋼鐵般堅強、石頭般堅硬、青銅般耐磨、玻璃般透明、鮮花般艷麗,以其優(yōu)越的性能深入到了各個領(lǐng)域,從航天火箭到人們的日常生活用品,無所不有。面對如此大的市場,如何能快捷、高效的設(shè)計出模具已是當今模具的頭等課題。第一個設(shè)計出模具的人,就意味著第一個搶占了市場。WTO 的加入,我國的模具設(shè)計行業(yè)受到了前所未有的挑戰(zhàn),提高模具的設(shè)計技術(shù)含量已迫在眉睫。我國模具生產(chǎn)能力和水平,與國外相比則差距頗大,造成上世紀九十年代模具進口量占全國模具銷售總額的三分之一以上,達 6-10 億美元。因此,結(jié)合我國具體情況,學習國外模具工業(yè)建設(shè)和模具生產(chǎn)的經(jīng)驗,宣傳、推行科學合理化的模具和產(chǎn)工程,推行科學合理化的模具生產(chǎn)工程,應當是我國當前模具工業(yè)建設(shè)中的重要任務 50 年以前,模具生產(chǎn)一直延用單件生產(chǎn)方式,但是,經(jīng)過長其他期、大量生產(chǎn)實踐,模具設(shè)計師們在模具生產(chǎn)實踐中,經(jīng)總結(jié)、研究、分析與設(shè)計,將其中通用、常用結(jié)構(gòu)件,制訂成系列化標準件和通用件,并組織批量生產(chǎn)和商品化供應,從而改變了模具完全處于單位生產(chǎn)的狀態(tài)。大幅度地提高了模具設(shè)計水平與制造質(zhì)量,大幅度地縮短了模具設(shè)計與制造周期。美國、德國進行模具標準化工作已有 100 年的歷史。日本在二戰(zhàn)后,也進行了全面推行模具標準化工作。故而這些國家已全面實現(xiàn)了模具標準化。其中,中草藥小型模具中 90%以上的零、部件,中大型模具中的 60%以上的零、部件,均已實現(xiàn)了標準化、通用化、系列化和商品化供應。故而,日本、美國模具的平均生產(chǎn)周期已縮短到 1.5-2.5 個月,百我國模具的平均生產(chǎn)周期在 4-5 個月以上,其主要原因之一是模具標準化程度和水平不高!目前,我國中小模具中,標準零、部件使用覆蓋率尚不到 30%。生產(chǎn)供應的標準件品種、規(guī)格不齊,質(zhì)量不高,不能滿足互換性要求。從而造成我國模具生產(chǎn)水平,仍基本上處于極不合理的單件生產(chǎn)狀態(tài)。為此,應當采取相應措施,針對模具生產(chǎn)特點,組織行業(yè)力量,進行標準件的“快捷、適時、定點、優(yōu)質(zhì)、安全、配套”地對模具生產(chǎn)企業(yè)進行和產(chǎn)和商品化服務,以便全面推行模具標準化工作。本作者的畢業(yè)設(shè)計課題是 Ф146.6 的藥瓶設(shè)計,為了更好的完成設(shè)計,我們在還親自參觀學習了多家注塑廠,查閱了一系列相關(guān)資料當然,由于個人能力有限,書中缺點和錯誤在所難免,望各位評審老師批評指正。- 6 -1. 總體方案論證1.1 藥瓶的模具方案論證1.1.1 藥瓶的設(shè)計原理藥瓶采用上吹型中空吹塑,嵌塊式結(jié)構(gòu)。中空吹塑的基本工作過程主要包括以下幾個步驟:1.擠出管狀熔坯(或稱型坯) ;2.模具夾住型坯;3.通入壓縮空氣,將型坯吹脹成模腔形狀,空氣壓力一般為 0.26~0.49兆帕;4.制品在模內(nèi)充分冷卻,保持壓力;5.放出制品內(nèi)的壓縮空氣;6.開模時取出制品。1.1.2 藥瓶的方案選擇方案一、采用上吹型中空吹塑,在瓶口和瓶底分別設(shè)有??谇秹K和模底嵌塊。由于??诤湍5啄p比較快,易于更換就可以延長模具的使用壽命,節(jié)省資金。方案二、采用吹型中空吹訴,但不設(shè)有嵌塊結(jié)構(gòu),由于瓶口螺紋和瓶底凹坑易使其相應部位磨損,一旦磨損,便要全部更換,即不經(jīng)濟也不省時。綜上所述,采用方案一。具體結(jié)構(gòu)如下:- 7 -藥瓶模具示意圖1.2 瓶蓋的模具方案論證 1.2.1 瓶蓋的模具設(shè)計原理瓶蓋模具為注射模具,采用旋轉(zhuǎn)螺紋脫模,兩板式。在注射成型后,動模與定模分開的過程中,由固定的齒條迫使與之相連的齒輪旋轉(zhuǎn),然后通過一系列的齒輪傳動,最后使型芯旋轉(zhuǎn)。瓶蓋由于受到側(cè)澆口和本身止滑條紋的約束,不能旋轉(zhuǎn),于是型芯和瓶蓋可以自動分離。1.2.2 瓶蓋的模具方案比較方案一、模具采用螺紋旋轉(zhuǎn)脫模,通過齒條帶動齒輪旋轉(zhuǎn)脫模。該模具自動化程度高,效率高,節(jié)省了人力物力。方案二、模具采用螺紋旋轉(zhuǎn)脫模,通過手工把瓶蓋和螺紋一起擰下,然后再交給其他人用扳手脫模。該模具費時,且須多個型芯,辦事效率低。綜上所述,采用第一方案。具體結(jié)構(gòu)如下:- 8 -瓶蓋模具示意圖- 9 -2 藥瓶的模具設(shè)計說明2.1 中心入料式機頭本套模具為上吹型中空吹塑模具,選用中心入料式機頭,其采用支架來支撐分流體與芯棒,支架設(shè)置有若干條分流肋。這樣,熔體流經(jīng)支架時被分成了若干股,之后重新匯合。因此,這類機頭又可稱為支架式機頭。這類機頭的流徑較短,各熔體的停留時間相差較小,型坯周向壁厚較均勻,熔體降解的可能性較小。因此。這累機頭可用于 PVC 等熱敏性塑料。熔體流經(jīng)支架后形成的匯合線會降低制品性能,尤其對薄壁制品。在分流肋表面上,熔體所受的剪切速率較大,其分之取向也較大,這會降低熔體匯合線的強度。為提高熔體匯合線的強度,要使聚合物分子重新纏結(jié),在支架后開設(shè) U 形流道以延長熔體的停留時間。2.2 材料的選擇和藥瓶的測繪采用高密度聚乙烯(HDPE)樹脂,密度為 0.94~0.7g/cm3,霧狀半透明,濕氣滲透性很低,氧氣滲透性很高,CO 很高,吹漲氣壓 P= 0.4~0.7MP.2最小合模力 F =1.2nAP=25.16kNminn 型坯模具(吹塑模具)數(shù)量A 型坯(或容器)在分型面上的投影P 型坯模具型腔內(nèi)的熔體壓力(或型坯的吹脹壓力)藥瓶的模具測繪尺寸如下圖:- 10 -2.3 注射機的選擇該藥瓶重量為 38g,,故選用 XS-Z-60 型注射機一次注射量 125cm 3螺桿直徑 38mm注射壓力 119.6MP a鎖模力 490×10 N3壓板行程 180mm模具最大厚度 200mm模具最小厚度 70mm壓板尺寸 330×440mm拉桿空間 190×300mm模具主要由以下部分組成:1. 動模部分;2.定模部分;3.冷卻部分;4.切口部分;5.導向部分。2.4 型坯下垂與膨脹比型坯擠出后,仍處于熔融狀態(tài),其自身的重量會造成型坯下垂伸長,通常稱之為型坯下垂。型坯下垂會造成壁薄或壁厚不均。因此,在可能的條件下,要盡力控制型- 11 -坯下垂伸長。通常用加快擠出型坯速度、減少型坯在空間停留的時間等方法來解決。型坯自機頭擠出后,因壓力消除而膨脹,其膨脹的計算方法可按下面經(jīng)驗公式dDx??式中 X---膨脹比(HDPE 膨脹率為 15%~65¥,取 50%) D---型坯離口模后的實際直徑d----機頭口模直徑在生產(chǎn)中,型坯離模膨脹現(xiàn)象應控制,通常采用升高料溫、選擇合適的辦法。0. 5= md3.65.9???2.4 模具型腔2.4.1 分型面設(shè)計吹塑模具首先要考慮的一個 問題是分型面的選擇,其一般在于使兩半模對稱,減小吹脹比,易于制品拖模。因此,分型面的位置由吹塑制品的形狀確定。對橫截面為圓形的容器,分型面通過其直徑設(shè)置,因此藥瓶采用過中心對稱分型。2.4.2 型腔表面吹塑的模具腔表面應稍微有點粗糙。否則,會造成模具型腔的排氣不良,夾留有氣泡,使制品出現(xiàn)“桔皮紋”的表面缺陷,還會導致系統(tǒng)的冷卻速度低而且不均勻,使制品上各處的收縮率不一樣。由于 PE 吹塑模具的溫度較低,加上型坯吹脹壓力較小,吹脹的型坯不會楔入至粗糙型腔表面的波谷,而是位于并跨過波峰,這樣,可保證制品有光滑的表面,并提供微小的網(wǎng)狀通道,使模強易于排氣。對模腔作噴沙處理,就可以形成粗糙的表面??捎媒饎偸?、石英沙、或硬沙礫來噴沙,噴沙沙礫要適當。對小 PE 瓶,可采用 60#~120#的粒度,較大的粗度,LDPE 要采用較細的粒度。2.4.3 型腔尺寸尺寸主要由制品的外行尺寸 并同時考慮制品的收縮率來確定。收縮率一般- 12 -是指室溫(22 攝氏度)下模腔尺寸與成型 24h 后制品尺寸之間的差異。以 HDPE其收縮率的 80%~90%是在成型后的 24h 內(nèi)發(fā)生的。影響吹塑制品收縮率的因素有多種。結(jié)晶制品的制品收縮率要比非結(jié)晶的大;對結(jié)晶塑料(例如 PE) ,收縮率隨著制品的壁厚而增加,這是因為冷卻速率較小會導致有序的晶體增加;提高型芯的熔體溫度雖然不會明顯影響制品的外部尺寸,但會使較多的收縮出現(xiàn)在壁內(nèi),這是因為較高的熔體溫度可減小應變恢復與吹脹應力;吹脹氣壓較高或模具溫度較低,可減少收縮率;加入的填料也會影響制品的收縮率;吹塑制品的收縮率還有方向性,縱向的收縮率要比橫向的少大些。2.5 模具底部嵌塊吹塑底部一般設(shè)置單獨的嵌塊,以擠壓、封接型坯的一端,并切除尾料。設(shè)計模具嵌塊時應主要考慮夾坯口刃與尾料槽,它們對吸塑制品的成型與性能有重要的意義。因此,對它們的下述四個方面的要求。1. 有足夠的強度、剛性與耐磨性,在以后的反復合模過程中承受壓模型坯熔體產(chǎn)生的壓力。2. 坯區(qū)的厚度一般比制品壁的大些,積聚的熱量較多。為此,夾坯嵌塊要選用熱導性能高的材料來制造。同時考慮嵌塊耐用性的話,銅鈹合金是一種理想的材料。當然,由鋼制成的嵌塊使用壽命會更長,但導熱性能較差。3. 接合縫通常是吹塑容器最薄弱的部位,故要在合模后但末切斷尾料前把少量熔體擠入接合縫,以適當增加其厚度與強度。4. 應切斷尾料。夾坯口刃的設(shè)計:夾坯口刃是一個重要的參數(shù)。B 過小會減小容器接合縫的厚度,降低其接合強度,甚至切斷接合縫,無法吹脹型坯;b 過則無法切斷尾料,甚至無法使模具閉合。要根據(jù)塑料特性、容器壁厚與容積、合模厚度與尾料夾角來確定 b值。對任性較大的塑料, b 要小些;合模速度較低時,b 也可以取小些。根據(jù)經(jīng)驗,用 HDPE 吹塑的容積小于 200L 的大桶、容器時,可這樣來確定b:b=v 3/1式中,b 的單位為 mm,V 的單位為 L。對于小瓶(10ml) ,b 可取 0~0.3) 。大于200ml 的取 0.5~4mm 之間。- 13 -因此藥瓶的切口寬取 b=2尾料槽的設(shè)計:在夾坯口刃的下方開設(shè)尾料槽,其位于模具分橫面上。下圖給出了尾料槽的結(jié)構(gòu)。尾料槽的深度對吹塑的成型與制品自動休整有很大的影響,尤其對直徑大、壁厚小的型坯。槽深過小使尾料受到過大的壓力的擠壓,是模具尤其是夾坯口刃受到過高的應變,甚至則不能與完全閉和,難以切斷尾料;若槽深過大,尾料則不能與槽壁接觸,無法快速冷卻,其熱量會傳至容器結(jié)合縫,使之軟化,休整時,會對接合縫產(chǎn)生拉伸。每半邊模具的尾料槽深度最取型坯壁厚的80%~90%尾料的夾角 α 也要適當,常取 30°~90°夾坯口刃寬度較大時 α 一般取大值。α 較小 時有助于把少量熔體擠入接合縫中。2.6 模具頸部嵌塊成型容器頸部的嵌塊主要有模頸圈與剪切塊,剪切塊位于模頸圈之上,有助于切去頸部余料,減小模頸圈的磨損。剪切塊的開口可為錐形的,夾角一般為 60°。模頸圈與剪切塊由工具鋼制成,并硬化至 HRC56~58。定頸進氣桿插入型坯時,可把型坯擠入模頸圈的螺紋槽內(nèi),形成實心螺紋,進氣桿端部則可成型容器頸部的內(nèi)表面。剪切塊口刃與進氣桿的剪切套配合,切斷頸部余料。2.7 模具排氣成型容積相同的容器時,吹塑模具內(nèi)要排出的空氣量要比注射成型的大許多。注射成型的模具要排出的空氣量最多等于注射模具內(nèi)的熔體量。而對吹塑模具,要排除的空氣體積等于模腔容積減去完全合模瞬時型坯已被吹脹后的體積,其中后者占較大比例,但仍有一定的空氣夾留在型坯與模腔之間,尤其對- 14 -桶、罐、燃油箱之類的大容積吹塑制品。以吹塑 120L 大桶為例,模腔容積為145L,完全合模瞬時型坯已被吹脹成體積約 90L。此外,與注射成型模具相比,吹塑模腔內(nèi)的壓力很?。ㄒ话愕扔?1MP ) 。因此,對吹塑模具的排氣性能要求a較高(尤其是形腔拋光的模具) 。若夾留在型腔與型坯之間的空氣無法完全或盡快排出,型坯就不能快速地吹脹,吹脹后不能與模腔良好的接觸(尤其是棱角部位) ,會使制品表面粗糙、凹痕等缺陷,表面文字、圖案不夠清晰,影響制品的外觀性能與外部形狀,尤其當型坯擠出時,出現(xiàn)條痕或發(fā)生溶體斷裂。排氣不良還會延長制品的冷卻時間,降低其機械性能,造成其壁厚不均勻。為此,要設(shè)法提高吹塑模具的排氣性能。瓶體部分在閉模時有大量空氣,在吹賬時應盡快把空氣排出,以使瓶體能完整地成型,緊貼于模腔壁上。如果某一局部有空氣滯留,外形即不完整成為廢品。最有效的辦法是在分型面上設(shè)排氣槽,而截面突然改變處也應設(shè)排氣孔。1.分型面上的排氣槽分型面是模具主要的排氣部位,合模后應盡可能多快的排出空氣。否則,會在制品上對應分型面部位出現(xiàn)縱向凹痕。這是因為制品上分型面處因夾留空氣而無法快速冷卻、溫度尚較高的部位產(chǎn)生了拉力。排氣槽的選取要恰當,不應在制品上留下痕跡,尤其對外觀要求較高的制品(例如化裝品瓶) ,這于塑料特性、吹脹氣壓及容器的閉厚和容積有關(guān)。型腔的分型面的接觸面上應適當減小,以使兩個半模能密合。因為吹塑機的瑣模遠小于注射機,為了增大分型面的鎖模壓強,一般都沿型腔周圍留有 3~10 的空隙。而排氣槽則開在留下的接觸面上。槽深 0.1mm,一般用平面磨床精磨而成,槽寬 10~25mm,依模具大小而定。而一付模具在分型面上的槽數(shù)也依型腔的容積而定,在型腔的兩邊各開三條以上的排氣槽。2.隅角部的排氣在瓶肩及瓶底的周圍,是容易滯留空氣的所在。而瓶肩及瓶底有時是用嵌件組成的,不便設(shè)排氣槽。即便可以設(shè)排氣槽,而有時由于瓶底的造型不同,往往在這些部位易使空氣滯留。因此必須設(shè)排氣孔。大致有以下幾種方式:a)為盲孔排氣,用于型腔小的模具,儲留氣量不大。盲孔徑為 0.6~1.2,深25~35mm.一般都在試模后發(fā)現(xiàn)有局部憋氣時采用,新模不用。b)為漏斗形,型腔有深凹的最凹處,徑孔自 0.2~0.5mm,根據(jù)所用的材料而定,如聚乙烯,聚丙烯,PET,孔徑要小。制造時應先鉆小洞,待試模后決定。孔徑的大小雖然與排氣快慢有關(guān)系,但孔的位置更是關(guān)鍵。如果孔的位置正確,孔徑雖小也可以排出儲留的氣體。c)為排氣栓塞,一般作成六角形柱體,用圓柱在六角上削去- 15 -0.1~0.2 平面,嵌入需要排氣的部位。由于型腔表面多為弧面,所以栓塞型腔精加工以前嵌入。但應注意在精加工時不可被切屑堵塞氣息。d)為燒結(jié)金屬通氣塞,一般用銅燒結(jié)合金。本套模具在試模后,若發(fā)現(xiàn)憋氣,可采用,盲孔排氣。2.8 模具的冷卻模具的冷卻效果量否直接影響瓶子的表面質(zhì)量,所以冷卻系統(tǒng)的設(shè)計在吹塑中很重要.如果冷卻不均勻,吹出的成品質(zhì)量的表面便有明顯的差異,十分影響外觀。模具的冷卻方法可分為外冷法、內(nèi)冷法與后冷卻這三種。外冷法較為常用,其又可以分為以下四種:第一種方式是在模具入口引入較大流量的冷卻流體,設(shè)置的折流板形成的迷宮式流道有助于形成湍流狀態(tài),提高冷卻效果。密封端板打開后即可清理冷卻通道。象鋁。銅鈹合金這類材料具有多孔性,因此其鑄造通道一般要用環(huán)氧樹脂浸漬,以防止冷卻流體滲入模腔內(nèi),但這會降低熱傳導性。第二種方法是在模腔內(nèi)從縱、橫方向鉆出冷卻通道。模具由機械加工制造時,就可以用這種方式。在孔內(nèi)設(shè)置螺旋銅片可以加劇流體的湍流速度。冷卻通道一般取 10 沒扎~15mm,對大型模具可達 30mm.。孔徑較大時要求冷卻流體有較高的流率,既要求配置大功率的泵送裝置。兩相鄰孔道之間的孔徑的 3~5倍(例如 35~50) ,孔壁與模腔之間的距離為孔徑的 1~2 倍,以均勻、充分地冷卻制品。鉆孔式冷卻通道易于清理,設(shè)計不合理時便于修改。第三種方式,在模壁內(nèi)嵌入冷卻彎管,這主要用于鋁、銅鈹合金或鋅合金鑄造的模具中。這里彎管之間的距離對應上述孔道之間的距離。彎管用銅制成時具有高的熱性能。這種方式比較簡單,可提高冷卻流體的湍流程度與傳熱性能,避免其泄露,但管道不易清理。第四種方式為噴霧冷卻,在模壁空腔內(nèi)通過一組噴管噴射出水霧。此方式主要用于大型模具,以減少模具質(zhì)量。吹塑制品各部位的壁厚一般是有差異的,而冷卻時間由最厚的部位確定,且冷卻不均勻會使制品產(chǎn)生翹曲與殘余應力。通過以上分析,第一種鑄造水路簡單方便,易于加工,故采用此種方式。- 16 -鑄造式冷卻通道1---冷卻流體出口;2---模腔;3---冷卻流體入水口;4---折流板;5---密封端板2.9 擠出吹塑機械的操作與保養(yǎng)2.9.1 開機與停機擠出吹塑機械的啟動要按下述步驟進行。a.按要求設(shè)定各加熱段溫度;b.各加熱段達到預定溫度并保溫一定時間,螺桿開始以最低的速度連續(xù)地旋轉(zhuǎn),然后逐漸提高轉(zhuǎn)速至要求的值;c.型坯擠出穩(wěn)定后,開始吹塑操作。停止吹塑生產(chǎn)時要按以下步驟進行:a.暫停生產(chǎn) 1h 以內(nèi)時,停止螺桿轉(zhuǎn)動,機筒與機頭的各加熱段仍按加工要求設(shè)定溫度;b.暫停生產(chǎn) 1~8h 時,停止螺桿轉(zhuǎn)動,各加熱段設(shè)定較低溫度(例如HDPE135℃) ;- 17 -c.停止生產(chǎn) 8h 以上時,停止螺桿的轉(zhuǎn)動及機筒與機頭的加熱。但這樣,留在機筒的熔體會冷卻、收縮,產(chǎn)生氧化、降解。為此,最好的操作:適當降低機筒上對應過度段與計量段的溫度(例如對 HDPE 為 160℃) ,螺桿低速轉(zhuǎn)動,以把機筒內(nèi)的熔體排出,最后停止螺桿及加熱。2.9.2 吹塑模具的保養(yǎng)吹塑模具夾坯口刃磨損后,要由熟練的制模工人來修復。吹塑模具頸部的剪切塊與進氣桿上的剪切套是關(guān)鍵部件,要保持良好狀態(tài),必要時更換。例如,剪切口刃被不均勻磨損后,成型的容器在使用時頸部會發(fā)生泄露現(xiàn)象。吹塑模具冷卻孔道因堵塞或腐蝕而影響冷卻介質(zhì)的流動時,應立即清洗。吹塑模具的導銷要定期潤滑,每工作一年,至少要工作一次,以確保兩半模對準,提高模具壽命。每當停機生產(chǎn)或吹塑模具要庫存時,要用壓縮空氣吹凈里面的冷卻孔道,模腔要涂上防護劑。- 18 -3 瓶蓋的模具設(shè)計材料的選擇和瓶蓋的測繪瓶蓋的材料和藥瓶的材料相同(見藥瓶的設(shè)計)平蓋的測繪如下:3.1 注塑機的選擇與型腔個數(shù)的計算瓶蓋的質(zhì)量為 12g,選用 XS-ZY-125 注射機。一次注射量 125cm 3螺桿(柱塞)直徑 42mm注射壓力 116.6MP a鎖模力 882×10 N3最大注射面積 320 cm 2壓板行程 300mm模具最大厚度 300mm- 19 -模具最小厚度 200mm壓板尺寸 450×420mm拉桿尺寸 260×290mm定位圈尺寸 ф100mm頂出形式 兩側(cè)頂出,中心距 230mm選用注射機的鎖模力必須大于型腔壓力產(chǎn)生的開模力,不然模具分型面要分開面產(chǎn)生溢料。注射時產(chǎn)生的型腔壓力對柱塞式注射機壓力損失較大,所以,型腔壓力均為注射壓力的 40~60%;而有預裝置的注射機及螺桿式注射壓力損失較小,所以型腔壓力較大。另外,對不同流動性的塑料,噴嘴和模具結(jié)構(gòu)形式。其壓力損失也不一樣,一般熔料經(jīng)噴嘴時其注射壓力達 60~80Mpa,經(jīng)澆注系統(tǒng)入型腔時則型腔壓力一般設(shè)為 25~50MPa;鎖模力和成型面積的生態(tài)系統(tǒng)由下式確定:10/AP??腔鎖式中 ----鎖模力,KN;鎖----型腔壓力,一般取 40~50MPa;腔PA---澆道進料口和塑件的投影面積,m㎡:則 10/AP??腔鎖=4.5X5000/1000=225(KN)XS-ZY-125 鎖模力為 882(KN);另外,鎖模力與成形面積的生態(tài)系統(tǒng)可直接查表。額定注射壓力如果只考慮注射機的最大注射量,最大成型面積和鎖模力來確定注射,這還不是夠的。有些塑件由于形狀及塑料的品種等因素,需用很高的注射壓力才能順利成形,為此選用的注射機注射壓力必須大于成形所需的注射壓力。即應滿足下人的公式:成注 P?式中 -選用的注射機的最大注射壓力;注-成形時需用的注射壓力 ,MPa;成- 20 -高密度聚乙烯成形時所需的注射壓力為(70~100)Mpa,XS-ZS-22 型注射機的注射壓力為 750 MPa=750 MPa>(70~100) MPa注P型腔的計算以機床注射能力為基礎(chǔ),每次注射量不超過注射機最大注射量的 80%,按公式計算: 件 澆WSN??8.0式中 N—型腔數(shù):S—注射機的注射量(g):--澆注系統(tǒng)的注射量(g)澆W--塑件重量(g);件初定注射 機為 XS-ZS-22 型,該注射機的注射量為 30g,即 S=30g,初估澆注系統(tǒng)的重量為 5g,即 =5g,塑件的重量 =12g澆 件W所以 5.12308.????N因此,模具的型腔數(shù)初定為 13.2 澆注系統(tǒng)設(shè)計澆注系統(tǒng)設(shè)計應注意的幾個問題1.首先根據(jù)塑料制品的結(jié)構(gòu)分析其充填過程,以保證塑料制品的內(nèi)在質(zhì)量和尺寸穩(wěn)定。這一點在大型塑料模具制品及其功能性塑料制品上尤為重要。2.在設(shè)計澆系統(tǒng)時,應當非常注意澆注系統(tǒng)對制品外觀的影響。在設(shè)計過程中經(jīng)常會遇到這樣的情況,某一塑料制品的澆口影響制品外觀,只能將澆口該設(shè)在其他部位。若實在無法處理時,可通過改變制品的結(jié)構(gòu)來解決。上述問題,對有外觀質(zhì)量要求的塑料制品尤為重要。3.在設(shè)計澆注系統(tǒng)時,應考慮到模具在注射時,是否能適應全自動操作。要達到全自動操作,必須保證在開模時,制品與澆注系統(tǒng)能自動脫落,澆口與制品亦要盡可能自動分離。- 21 -4.澆注系統(tǒng)的設(shè)計,必須考慮到塑料制品的后續(xù)工序。如因后續(xù)工序在加工、裝配、管理上需要,往往須設(shè)置輔助流道,將多件制品聯(lián)成一體。5.在設(shè)計澆注系統(tǒng)時,應留有一定的余地,這樣在使用是即使有些不足,亦可以比較方便的解決。6.多觀察分析各類塑件制品的澆注系統(tǒng)和澆口位置的選擇,吸取其成功之處,提高澆注系統(tǒng)的可靠性。7.設(shè)計澆注系統(tǒng)時,其主流道進口應盡量與模具中心重合。垂直式主流道的設(shè)計上圖是主流道的形式及設(shè)計參數(shù)d----主流道小端直徑,既主流道與注射機噴嘴接觸處的直徑。D=注射機噴嘴的孔徑+(0.5~1)=3mmL-----主流道長度。根據(jù)模具的具體結(jié)構(gòu),在設(shè)計時確定。α-----主流道的錐度。α 一般在 2°-4°對粘度較大的塑料,α 可取3~6°。但由于受標準錐刀的限制,應盡量選用標準度值,故取 α=4°。澆口套的設(shè)計主澆道是澆注系統(tǒng)的第一個組成部分,這部分的具體設(shè)計都集中在澆口套上,模具在工作時,澆口套直接與注射機噴嘴接觸,澆口套本身的工作條件比較苛刻,所以應選用較好的鋼材來制造,并應有 50~55HRC 的硬度。澆口套與注射機噴嘴的接觸部分有兩種形式,一種為平面接觸,另一種為球面接觸。平面接觸的主要特點是面積較大,密封較好,塑料不易外溢.其缺點是,若注射機的精度不高,容易造成噴嘴孔與澆口套孔不同軸.球面接觸噴嘴與澆口套的接觸面積較小,若配合不當,容易造成塑料外溢,但由于它能自動調(diào)節(jié)注射機的偏差,所以在注射機精度不高的情況下亦能正常應用.在國外,特別是西歐國家,使用平面接觸的澆口套較多,我國絕大部分使用的是球面接觸的澆口套。球面接觸的澆口套,在正常情況下,澆口套端部的球面半徑應大于注射機噴嘴的球面半徑,澆口套錐孔的小端直徑應大于注射機噴嘴孔徑澆口套與定模部分裝配后,必須與分型面有一定的間隙,其間隙a=0.05~0.15mm。因為該處受噴嘴的壓力影響,在注射時會產(chǎn)生變形。有時在試模中經(jīng)常發(fā)現(xiàn)在分模面上澆口套周圍出現(xiàn)飛邊,就是由于沒有間隙的原因。澆口套的凸肩處必須有圓弧過度,否則會因為應力集中而在工作時損壞。圓弧半徑 3~5mm 之間。- 22 -3.3 冷料井及澆注系統(tǒng)的拉料桿冷料井的位置及其作用1.冷料井分為主流道冷料井和分流道冷料井。冷料井的位置一般都設(shè)計在主流道或分流道的末端,亦即塑料最先到達的部位。2.冷料井的作用是防止在注射時將冷料注入型腔,而使制品產(chǎn)生缺陷。3.冷料井的大小要適宜,一般情況下,主流道冷料井圓柱的直徑為6~12mm,其深度為 6~10mm。對于大型制品,冷料井的具體尺寸可適當加大。分流道冷料井,其長度 L=5~8mm。4.在三板式模具上一般不設(shè)計主流道冷料井,只在分流道上設(shè)計冷料井,其尺寸與上述相同。通過以上分析,本模具的冷料井的設(shè)計如下圖:3.4 澆口的設(shè)計澆口設(shè)計包括澆口截面形狀及澆口截面尺寸的確定,澆口位置的選擇。影響澆口的截面形狀及其尺寸確定的因素,就制品而言,包括制品的形狀、大小、壁厚、尺寸精度、外觀質(zhì)量及力學性能等,制品所用塑料特性對澆口設(shè)- 23 -計的影響因素是塑料的成型溫度、粘度(流動性) 、收縮率及有無填充物等。此外,在澆口設(shè)計時,還應考慮澆口的加工、脫模及清除澆口的難易程度。澆口的截面尺寸宜小不宜大。在確定尺寸時,先確定得小一些,然后試模時,根據(jù)對型腔的充填情況在進行修正。特別是一模多腔的模具,通過修正可使各型腔同時均勻充填。小澆口可以增加熔料流速,并且熔料經(jīng)過小澆口時產(chǎn)生很大的摩擦而使熔料溫度升高,其表觀粘度降低,有利于充填。另外,由于小澆口的固化較塊,不會產(chǎn)生過量補縮而降低制品的內(nèi)應力,同時可以縮短注射成型周期,澆口過小會造成澆口處過早固化,使補料困難而造成制品缺陷。在選擇澆口位置時,還應注意以下幾點:1.澆口位置應設(shè)在制品最大壁厚處,使塑料從壁厚流向壁薄,并保持澆口至型腔的流程基本一致。2.防止?jié)部谔幃a(chǎn)生噴射而在充填過程中產(chǎn)生蛇行。3.澆口位置應設(shè)置在制品的主要受力方向上,因為塑料的流動方向上所承受的拉應力和壓應力最高,特別是帶填料的增強塑料,這種情況更加明顯。4.在選擇澆口位置時應考慮制品的尺寸要求,因為塑料經(jīng)澆口充填時,在塑料的流動方向與垂直方向上的收縮不盡相同,所以應考慮到變形和收縮的方向性。本模具設(shè)計選擇側(cè)澆口澆注。側(cè)澆口亦稱普通澆口,側(cè)澆口在一個制品上可以開設(shè)一個也可以開設(shè)多個,這種澆口的主要特點:形狀比較簡單,加工較方便;在一模多腔的非平衡布置的模具上,修正這種澆口也比較容易,有時在生產(chǎn)現(xiàn)場也可以;幾乎各種塑料都可以使用這種澆口。其不足之處是:制品和澆口不能自行分離,若要使其分離必須特殊設(shè)計;澆口痕跡雖然沒有直接澆口那樣明顯,但還是留下一定的痕跡。側(cè)澆口的長度 l 中小型模具 l=0.5~0.8mm.批量大,要求不高的制品,l=0.25~0.40mm。這樣做有兩個優(yōu)點,其一可以減小摩擦阻力,便于充填;其二可以直接用手工去除澆口,不需要任何工具,而在制品上幾乎不留澆口的殘余部分。對于大型制品 l 可在 1.0~1.5mm 之間根據(jù)具體情況進行設(shè)計。澆口厚度 h 主要根據(jù)制品的最大壁厚,一般取 1/3~1/2 的壁厚,通??扇?0.5~1.5mm。澆口寬度 b 對于中小型制品,b=1.0~2.0mm;大型制品 b≥3mm.下圖是本模具澆口的示意圖:- 24 -側(cè)澆口示意圖3.5 制品形狀的冷卻由于在整個成型周期中,50%~60%的時間用于對制品的冷卻,因此,在成型過程中冷卻時間的長短的重要意義是不言而遇的。制品的最短冷卻時間可按下面的公式計算:T= (s)?????????????mcxt4ln2???δ-----制品最大厚度 (mm)α-----塑料熱擴散系數(shù) (mm /s)2t -----塑料脫模溫度 (℃)xt -----模具溫度 (℃)mt ------塑料注射溫度 (℃)c冷卻水道應設(shè)置在塑料向模具熱傳導困難的地方,根據(jù)冷卻系統(tǒng)的設(shè)計原則,冷卻水道應圍繞模具所成型的制品,且盡量排列均勻一致。由于采用旋轉(zhuǎn)脫模,- 25 -不宜在型芯開設(shè)冷卻水道,但為了達到冷卻效果,節(jié)省冷卻時間,本模具采用了嵌塊式螺旋冷卻水道。為了確保冷卻水道的密封性,在水道的上下端處都加了密封墊圈。具體如下圖:冷卻系統(tǒng)示意圖3.6 導向裝置的設(shè)計導向裝置主要由導柱和導套構(gòu)成。導柱分為普通導柱和階梯導柱,由于階梯導柱在制造上較普通型導柱難度大,對導柱中兩段不同的直徑部分的同軸度要求較高,因此,在這次設(shè)計中采用普通導柱,其制造簡單、省時,適合普通的模具。在設(shè)計中,導柱的長度也是一個不可忽視的重要參數(shù),即導柱的長度要比模具中最長的凸器部分長些,以免在組裝時因?qū)ξ徊粶识鰝>摺?.7 螺紋退芯的設(shè)計由于瓶蓋有兩圈內(nèi)螺紋,且螺紋較大,不可以強行脫模,因此采用旋轉(zhuǎn)脫模。為提高生產(chǎn)效率,節(jié)省人力物力,放棄手動手動旋轉(zhuǎn)退芯方法,采用機動旋轉(zhuǎn)退芯機構(gòu)。本模具采用齒條齒輪式,在注射成型后,動模與定模分開的過程中,由固定的齒條迫使與之相連的齒輪旋轉(zhuǎn),然后通過一系列的齒輪傳動,最后使型芯旋轉(zhuǎn)。瓶蓋由于受到側(cè)澆口和本身止滑條紋的約束,不能旋轉(zhuǎn),于是型芯和瓶蓋可以自動分離。襯套可延長模具的使用壽命,齒輪傳動系統(tǒng)要保持嚙合良好。- 26 -螺紋型芯退芯結(jié)構(gòu)示意圖圓柱齒輪的設(shè)計計算取齒輪的模數(shù)為 m=2,d=46mm, h =1, C =0.25a*齒輪的齒數(shù) z=d/m=46/2=23齒數(shù)為奇數(shù),分度圓直徑 d=46mm齒頂高 h =h m=1×2=2mma*齒跟高 h =(h +C )m=2.5mmf齒全高 h= h + h =(2 h + h )m=4.5mmafaf齒頂圓直徑 d =d +2 h =1??mz5021??齒跟圓直徑 d =fdcaf 41??基圓直徑 d = dcosα=46/cos20·=b齒距 p= mm28.614.3??m?齒厚 s= m2齒槽寬 e= 頂隙 c=c 5.0*??- 27 -3.8 注塑機操作過程注意事項養(yǎng)成良好的注塑機操作習慣對提高機器壽命和生產(chǎn)安全都大有好處。開機之前:(1)檢查電器控制箱內(nèi)是否有水、油進入,若電器受潮,切勿開機。應由維修人員將電器零件吹干后再開機。 (2)檢查供電電壓是否符合,一般不應超過±15%。 (3)檢查急停開關(guān),前后安全門開關(guān)是否正常。驗證電動機與油泵的轉(zhuǎn)動方向是否一致。 (4)檢查各冷卻管道是否暢通,并對油冷卻器和機筒端部的冷卻水套通入冷卻水。 (5)檢查各活動部位是否有潤滑油(脂) ,并加足潤滑油。 (6)打開電熱,對機筒各段進行加溫。當各段溫度達到要求時,再保溫一段時間,以使機器溫度趨于穩(wěn)定。保溫時間根據(jù)不同設(shè)備和塑料原料的要求而有所不同。 ( 7)在料斗內(nèi)加足足夠的塑料。根據(jù)注塑不同塑料的要求,有些原料最好先經(jīng)過干燥。 (8)要蓋好機筒上的隔熱罩,這樣可以節(jié)省電能,又可以延長電熱圈和電流接觸器的壽命。操作過程中:(1)不要為貪圖方便,隨意取消安全門的作用。 (2)注意觀察壓力油的溫度,油溫不要超出規(guī)定的范圍。液壓油的理想工作溫度應保持在45~50℃之間,一般在 35~60℃范圍內(nèi)比較合適。 (3)注意調(diào)整各行程限位開關(guān),避免機器在動作時產(chǎn)生撞擊。工作結(jié)束時:(1)停機前,應將機筒內(nèi)的塑料清理干凈,預防剩料氧化或長期受熱分解。 (2)應將模具打開,使肘桿機構(gòu)長時間處于閉鎖狀態(tài)。 (3)車間必須備有起吊設(shè)備。裝拆模具等笨重部件時應十分小心,以確保生產(chǎn)安全。3.9 模具的保養(yǎng) 每一套模具,往往造價及為昂貴,對模具必須進行保養(yǎng).1 防銹措施卸模時,必須從下部卸下冷卻管,用棉絲擦干,用壓縮空氣吹凈.在防銹方法上可涂飾耐水性的黃油,也可以打用除銹液將型腔和冷卻孔銹體清除.2 保持滑動部分的潤滑在保養(yǎng)上要定其在滑動部分涂油,涂飾必須適當.如潤滑油涂飾太多則會污染制品,涂少起不到潤滑的效果.- 28 -4.預期效果本人在規(guī)定時間內(nèi),保質(zhì)保量的完成了設(shè)計任務。在設(shè)計中,盡量采用新技術(shù),新方法,本著節(jié)能高效的原則,設(shè)計出了本套模具,符合設(shè)計任務書的要求,完成了領(lǐng)導交給我的設(shè)計任務。- 29 -5.結(jié)論本次設(shè)計研究了模具的中空吹塑和帶螺紋塑件的模具設(shè)計過程和方法,對注塑模具有了非常深刻的了解。經(jīng)過這三個月的緊張設(shè)計,不僅僅是學會了注塑模設(shè)計,而且學會了一般的設(shè)計方法,設(shè)計思路。在這三個月過程中,不但溫習了以前學的知識,而且學會了很多新的知識,并且熟練掌握了 AUTO CAD、PRO/E、CAD/CAM 等一系列繪圖軟件。- 30 -6.工作小結(jié)為期三個月的畢業(yè)設(shè)計已接近尾,回顧這緊張而充實的三個月的學習生活,感覺收益頗豐!在畢業(yè)設(shè)計前期,我們在鹽城十幾家注塑廠進行了一周的參觀實習,通過這段時間的觀察、了解,我對注塑模具有了比較具體的感性認識。我查找了一些相關(guān)資料,結(jié)合實習的收獲,初步制訂了畢業(yè)設(shè)計的寫作提綱。在吳德和老師的指導下,我對注塑模具的概念、具體內(nèi)容進行了進一步的研究。在設(shè)計期間,我閱讀、摘錄了許多相關(guān)資料,對注塑模具的認識進一步深化,積累了大量的感性材料。有時候為了某一個疑點去廠里做進一步了解,向工廠的老師傅請教,他們幫助我解決了很多難題,再次向他表示感謝!通過這三個多月的畢業(yè)設(shè)計,我學著獨立解決問題,提高了自己分析問題、解決問題的能力,為以后進入社會打下了基礎(chǔ)。在設(shè)計過程中培養(yǎng)了多聽、多問、多記的習慣,將使我終身受益。在畢業(yè)設(shè)計過程中我得到了吳德和老師的辛勤指導,在此我深表感謝。由于本人水平有限,文中難免不足之處,懇請各位評審老師批評、指正。