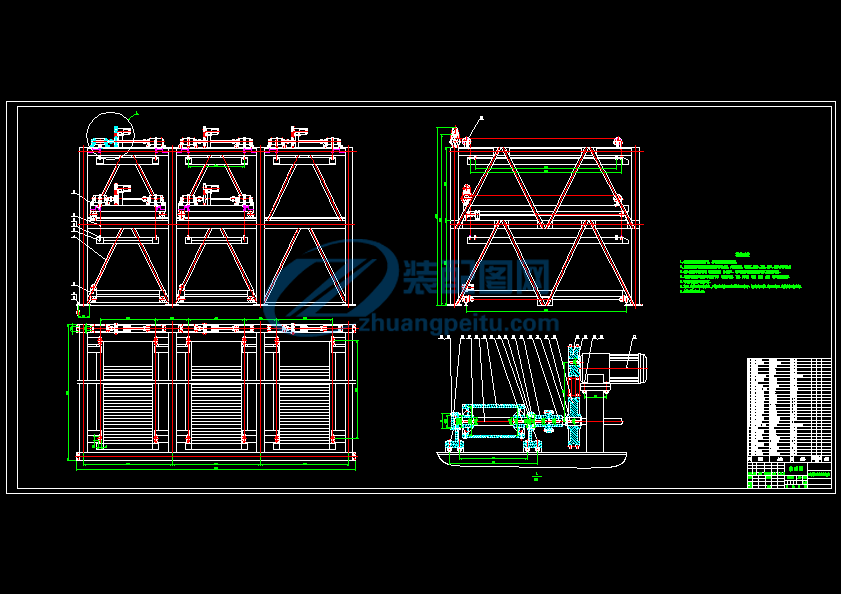
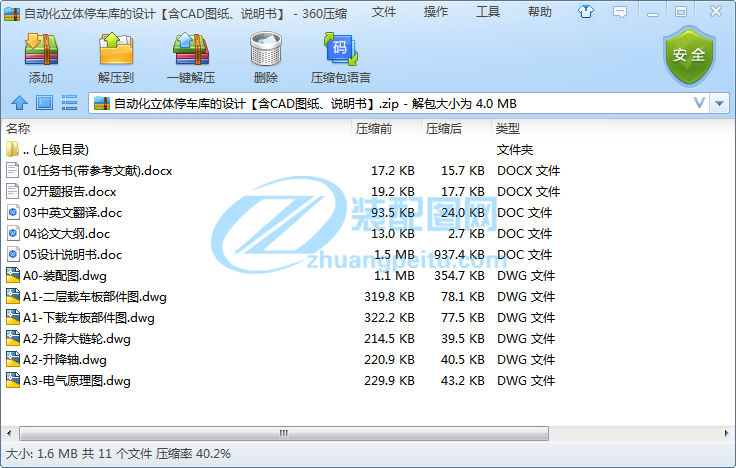
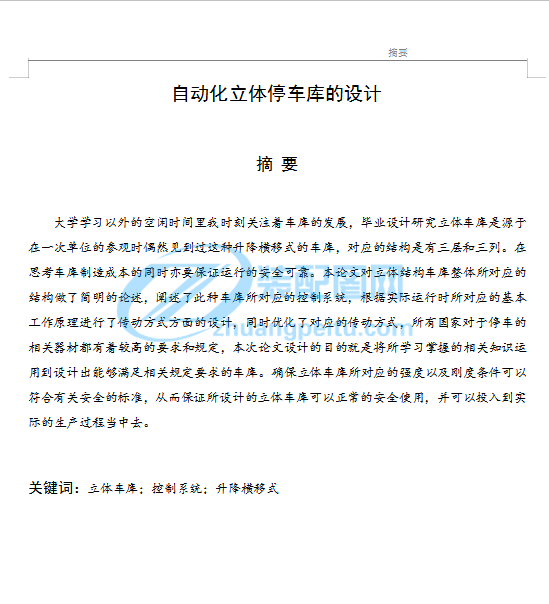
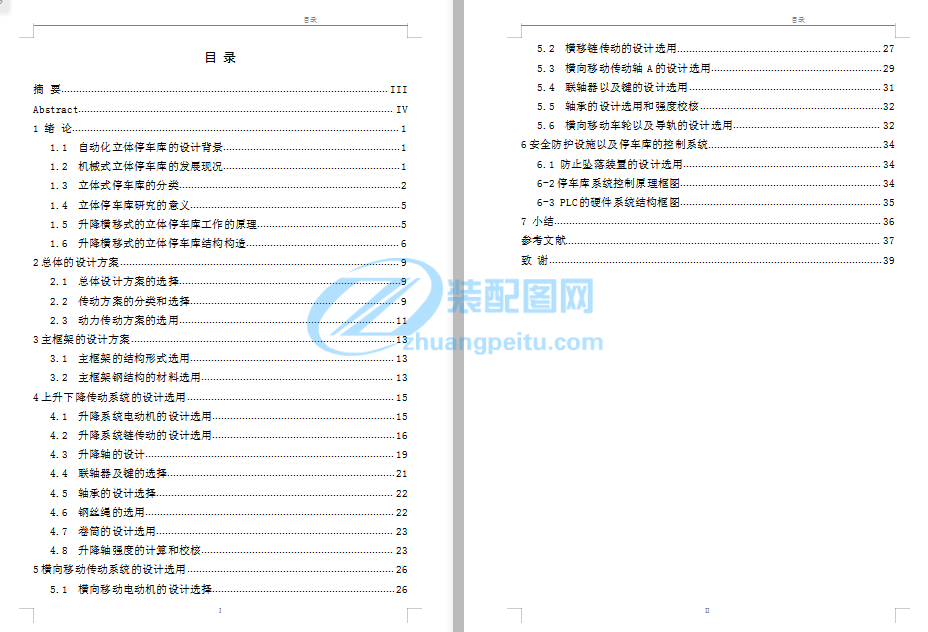
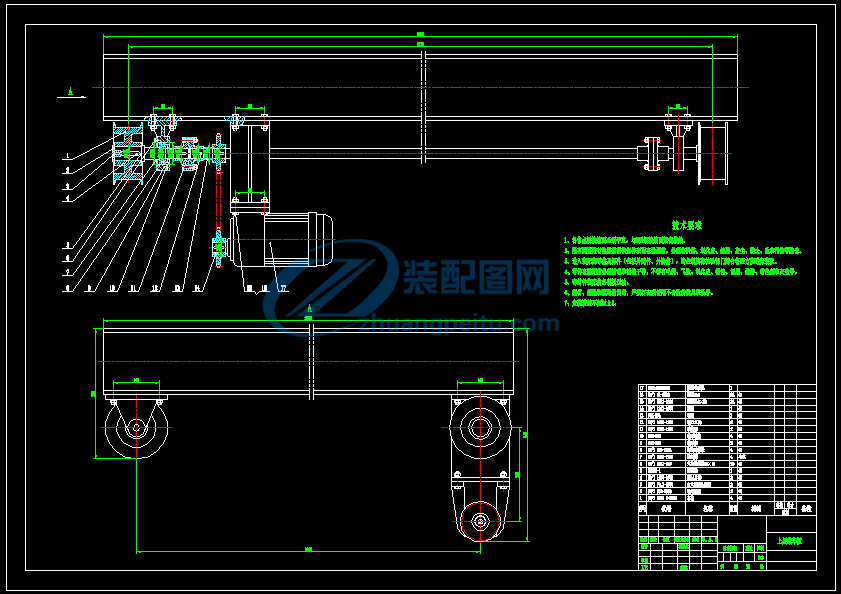
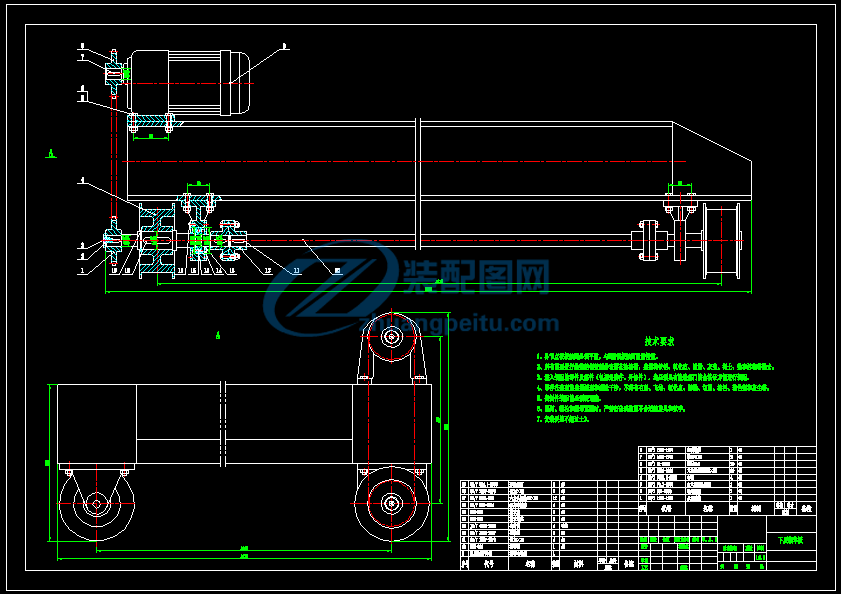
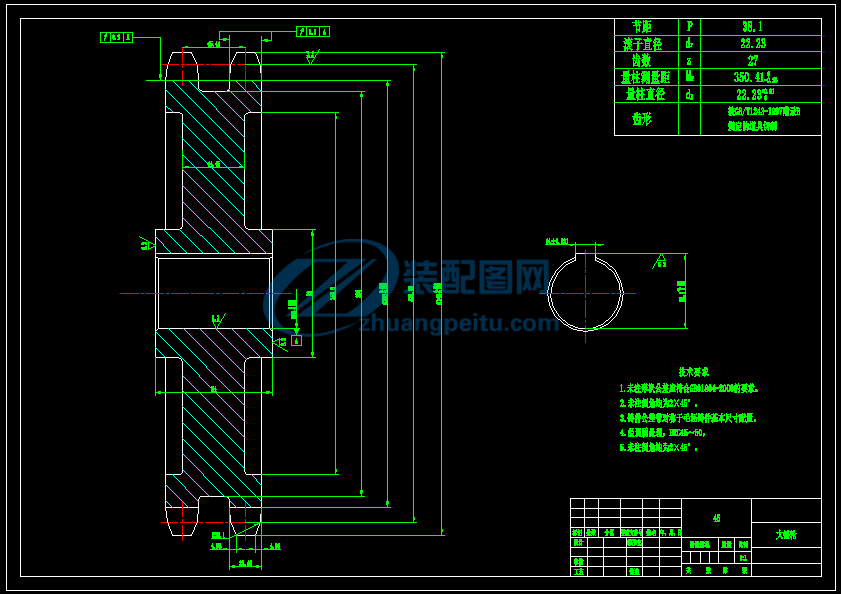
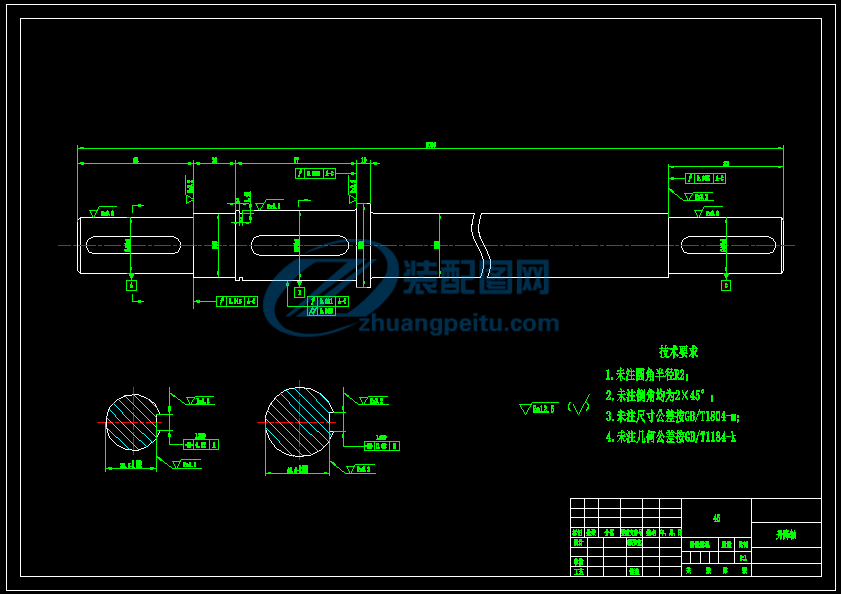
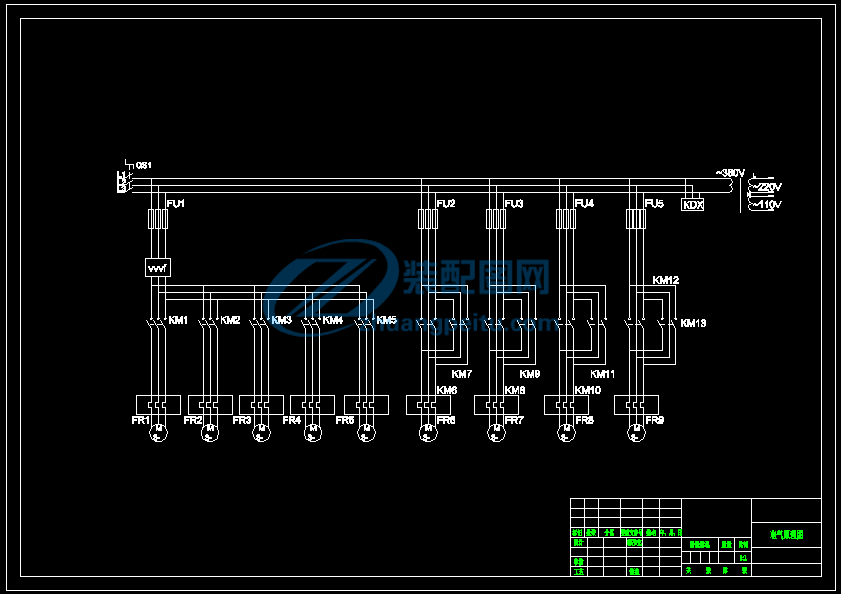
畢 業(yè) 設(shè) 計(jì)(論 文)任 務(wù) 書設(shè)計(jì)(論文)題目: 自動(dòng)化立體停車庫(kù)的設(shè)計(jì) 學(xué)生姓名:專 業(yè):所在學(xué)院:指導(dǎo)教師:職 稱:發(fā)任務(wù)書日期:年月日 任務(wù)書填寫要求1.畢業(yè)設(shè)計(jì)(論文)任務(wù)書由指導(dǎo)教師根據(jù)各課題的具體情況填寫,經(jīng)學(xué)生所在專業(yè)的負(fù)責(zé)人審查、系(院)領(lǐng)導(dǎo)簽字后生效。此任務(wù)書應(yīng)在畢業(yè)設(shè)計(jì)(論文)開始前一周內(nèi)填好并發(fā)給學(xué)生。2.任務(wù)書內(nèi)容必須用黑墨水筆工整書寫,不得涂改或潦草書寫;或者按教務(wù)處統(tǒng)一設(shè)計(jì)的電子文檔標(biāo)準(zhǔn)格式(可從教務(wù)處網(wǎng)頁(yè)上下載)打印,要求正文小 4 號(hào)宋體,1.5 倍行距,禁止打印在其它紙上剪貼。3.任務(wù)書內(nèi)填寫的內(nèi)容,必須和學(xué)生畢業(yè)設(shè)計(jì)(論文)完成的情況相一致,若有變更,應(yīng)當(dāng)經(jīng)過所在專業(yè)及系(院)主管領(lǐng)導(dǎo)審批后方可重新填寫。4.任務(wù)書內(nèi)有關(guān)“學(xué)院”、“專業(yè)”等名稱的填寫,應(yīng)寫中文全稱,不能寫數(shù)字代碼。學(xué)生的“學(xué)號(hào)”要寫全號(hào),不能只寫最后 2 位或 1 位數(shù)字。 5.任務(wù)書內(nèi)“主要參考文獻(xiàn)”的填寫,應(yīng)按照《金陵科技學(xué)院本科畢業(yè)設(shè)計(jì)(論文)撰寫規(guī)范》的要求書寫。6.有關(guān)年月日等日期的填寫,應(yīng)當(dāng)按照國(guó)標(biāo) GB/T 7408—94《數(shù)據(jù)元和交換格式、信息交換、日期和時(shí)間表示法》規(guī)定的要求,一律用阿拉伯?dāng)?shù)字書寫。如“2002 年 4 月 2 日”或“2002-04-02”。畢 業(yè) 設(shè) 計(jì)(論 文)任 務(wù) 書1.本畢業(yè)設(shè)計(jì)(論文)課題應(yīng)達(dá)到的目的:通過進(jìn)行本次畢業(yè)設(shè)計(jì),全面系統(tǒng)地對(duì)學(xué)生進(jìn)行設(shè)計(jì)方法和研究方法的基本訓(xùn)練。要求學(xué)生樹立正確的設(shè)計(jì)思想,培養(yǎng)學(xué)生進(jìn)行科學(xué)的研究。學(xué)生能獨(dú)立進(jìn)行資料的收集、加工與整理,能綜合運(yùn)用科學(xué)的理論、知識(shí)和技能,鍛煉獨(dú)立解決設(shè)計(jì)問題的能力,圖紙繪制規(guī)范,符合國(guó)家標(biāo)準(zhǔn),編寫符合要求的設(shè)計(jì)說明書并答辯,從而使學(xué)生樹立嚴(yán)謹(jǐn)、實(shí)事求是的科學(xué)態(tài)度,并掌握工程設(shè)計(jì)的一般程序規(guī)范和方法。 2.本畢業(yè)設(shè)計(jì)(論文)課題任務(wù)的內(nèi)容和要求(包括原始數(shù)據(jù)、技術(shù)要求、工作要求等):本論文設(shè)計(jì)的自動(dòng)化立體停車庫(kù)需要滿足以下的要求:停車庫(kù)的框架結(jié)構(gòu)強(qiáng)度要求較高、輕便漂亮、便于拆卸安裝以及運(yùn)輸;能夠?qū)崿F(xiàn)每一個(gè)載車板都有著自己完整的電機(jī)和傳動(dòng)系統(tǒng),以實(shí)現(xiàn)載車板能夠?qū)崿F(xiàn)升降和橫向的移動(dòng);需要設(shè)置一定的安全防護(hù)措施,避免制動(dòng)器故障時(shí)下降壓壞下面的汽車,在移動(dòng)的過程中遇到不應(yīng)該觸碰的物體電機(jī)需要停止運(yùn)行;設(shè)計(jì)出自動(dòng)控制和手動(dòng)控制一體的控制系統(tǒng),使最終設(shè)計(jì)出的停車庫(kù)有實(shí)際的使用價(jià)值和現(xiàn)實(shí)意義。二、畢業(yè)設(shè)計(jì)課題任務(wù)的要求:1、原始數(shù)據(jù):1.七個(gè)車位,分為三層,最上面有三個(gè)車位,下面兩個(gè)只有兩個(gè)車位,大致需要的空間為:長(zhǎng) 8m,寬 6m,高 6m。2.從保護(hù)環(huán)境和減少噪音的角度考慮選擇電動(dòng)機(jī)作為驅(qū)動(dòng)機(jī)構(gòu)3.為了實(shí)現(xiàn)升降的平穩(wěn)性,選擇鋼絲繩作為載車板的傳動(dòng)鏈2、技術(shù)要求和工作要求(1)停車庫(kù)的框架結(jié)構(gòu)強(qiáng)度要求較高、輕便漂亮、便于拆卸安裝以及運(yùn)輸。(2)能夠?qū)崿F(xiàn)每一個(gè)載車板都有著自己完整的電機(jī)和傳動(dòng)系統(tǒng),以實(shí)現(xiàn)載車板能夠?qū)崿F(xiàn)升降和橫向的移動(dòng)。(3)需要設(shè)置一定的安全防護(hù)措施,避免制動(dòng)器故障時(shí)下降壓壞下面的汽車,在移動(dòng)的過程中遇到不應(yīng)該觸碰的物體電機(jī)需要停止運(yùn)行。(4)設(shè)計(jì)出自動(dòng)控制和手動(dòng)控制一體的控制系統(tǒng),使最終設(shè)計(jì)出的停車庫(kù)有實(shí)際的使用價(jià)值和現(xiàn)實(shí)意義。畢 業(yè) 設(shè) 計(jì)(論 文)任 務(wù) 書3.對(duì)本畢業(yè)設(shè)計(jì)(論文)課題成果的要求〔包括圖表、實(shí)物等硬件要求〕: 詳細(xì)完整的畢業(yè)設(shè)計(jì)說明書一份;相關(guān)圖紙一套;外文參考資料及譯文。 4.主要參考文獻(xiàn): [1] 張啟君.立體車庫(kù)的主要型式及技術(shù)特點(diǎn) [M]. 北京:高等教育出版社,1999.[2] 付翠玉,關(guān)景泰.立體車庫(kù)發(fā)展的現(xiàn)狀與挑戰(zhàn) [M]. 北京:機(jī)械工業(yè)出版社,2005.[3] 中國(guó)重型機(jī)械工業(yè)協(xié)會(huì)停車設(shè)備管理委員會(huì)編. 機(jī)械式立體車庫(kù) [M].北京:海洋出版社, 2001.[4] 陳立德.機(jī)械設(shè)計(jì)基礎(chǔ) [M].北京:高等教育出版社,2008.[5] 任伯森.機(jī)械式立體車庫(kù)[M].北京:海洋出版社,2001.[6] 國(guó)家機(jī)械工業(yè)局.簡(jiǎn)易升降類機(jī)械式停車設(shè)備 [M]. 北京:機(jī)械工業(yè)出版社,1999.[7] 陳立德.機(jī)械制造裝備設(shè)計(jì)[M].北京:高等教育出版社,2008.[8] 國(guó)家機(jī)械工業(yè)局.升降橫移類機(jī)械式停車設(shè)備 [M]. 北京:機(jī)械工業(yè)出版社1999.[9] 王淑英.電器控制與 PLC 控制技術(shù)[M].北京:機(jī)械工業(yè)出版社,2005.[10] 盧金鼎,山靜民. 機(jī)電一體化技術(shù) [M].北京:中國(guó)輕工業(yè)出版社,1996.[11] 中華人民共和國(guó)機(jī)械行業(yè)標(biāo)準(zhǔn).升降橫移類機(jī)械式停車設(shè)備[M].北京: 機(jī)械工業(yè)出版社,2000.[12] 徐顴.機(jī)械設(shè)計(jì)手冊(cè)[M].北京:機(jī)械工業(yè)出版社,1991.[13] 任伯森.機(jī)械式立體停車庫(kù)[M].北京:海洋出版社,2001.[14] 哈爾濱工業(yè)大學(xué)理論力學(xué)教研室.理論力學(xué)[M].北京:高等教育出版社,2005.[15] 王芳卿.立體停車庫(kù)及其控制電器傳動(dòng)[M]. 北京:高等教育出版社,1998.畢 業(yè) 設(shè) 計(jì)(論 文)任 務(wù) 書5.本畢業(yè)設(shè)計(jì)(論文)課題工作進(jìn)度計(jì)劃:2015.12.15 選題審題截止2015.12.16-2016.1.10 完成任務(wù)書、開題2016.2.25-2.16.3.9 畢業(yè)實(shí)習(xí)調(diào)研,完成開題報(bào)告、中英文翻譯、論文大綱2016.3.19-2016.4.25 完成并提交論文草稿,4 月中旬中期檢查2016.4.26-2016.5.6 完成并提交論文定稿2016.5.6-2016.5.13 準(zhǔn)備答辯2016.5.13-2016.5.26 答辯,成績(jī)?cè)u(píng)定,修改完成最終稿所在專業(yè)審查意見:同意通過 負(fù)責(zé)人: 2016 年 1 月 8 日 畢 業(yè) 設(shè) 計(jì)(論 文)開 題 報(bào) 告設(shè)計(jì)(論文)題目: 自動(dòng)化立體停車庫(kù)的設(shè)計(jì) 學(xué)生姓名:專 業(yè):所在學(xué)院:指導(dǎo)教師:職 稱:年 月 日 開題報(bào)告填寫要求1.開題報(bào)告(含“文獻(xiàn)綜述”)作為畢業(yè)設(shè)計(jì)(論文)答辯委員會(huì)對(duì)學(xué)生答辯資格審查的依據(jù)材料之一。此報(bào)告應(yīng)在指導(dǎo)教師指導(dǎo)下,由學(xué)生在畢業(yè)設(shè)計(jì)(論文)工作前期內(nèi)完成,經(jīng)指導(dǎo)教師簽署意見及所在專業(yè)審查后生效;2.開題報(bào)告內(nèi)容必須用黑墨水筆工整書寫或按教務(wù)處統(tǒng)一設(shè)計(jì)的電子文檔標(biāo)準(zhǔn)格式打印,禁止打印在其它紙上后剪貼,完成后應(yīng)及時(shí)交給指導(dǎo)教師簽署意見;3.“文獻(xiàn)綜述”應(yīng)按論文的框架成文,并直接書寫(或打?。┰诒鹃_題報(bào)告第一欄目?jī)?nèi),學(xué)生寫文獻(xiàn)綜述的參考文獻(xiàn)應(yīng)不少于 15 篇(不包括辭典、手冊(cè));4.有關(guān)年月日等日期的填寫,應(yīng)當(dāng)按照國(guó)標(biāo) GB/T 7408—94《數(shù)據(jù)元和交換格式、信息交換、日期和時(shí)間表示法》規(guī)定的要求,一律用阿拉伯?dāng)?shù)字書寫。如“2004年 4 月 26 日”或“2004-04-26”。5、開題報(bào)告(文獻(xiàn)綜述)字體請(qǐng)按宋體、小四號(hào)書寫,行間距 1.5 倍。畢 業(yè) 設(shè) 計(jì)(論文) 開 題 報(bào) 告 1.結(jié)合畢業(yè)設(shè)計(jì)(論文)課題情況,根據(jù)所查閱的文獻(xiàn)資料,每人撰寫不少于1000 字左右的文獻(xiàn)綜述: 一、前言立體停車庫(kù),是用來最大量存取儲(chǔ)放車輛的機(jī)械或機(jī)械設(shè)備系統(tǒng)。隨著經(jīng)濟(jì)的增長(zhǎng),轎車進(jìn)入了每一個(gè)家庭,停車變得十分困難,立體車庫(kù)可以完美的解決這個(gè)問題,尤其對(duì)一些企業(yè),小區(qū)來說更顯得尤為關(guān)鍵。立體停車庫(kù)的種類眾多,目前使用最為廣泛的、最為典型的是升降橫移式立體車庫(kù)。我國(guó)好多的大城市已經(jīng)通過使用立體車庫(kù)有效的解決了停車難的問題?,F(xiàn)代停車產(chǎn)業(yè)的發(fā)展已具有一定規(guī)模,并積極拓展停車設(shè)施的輔助功能,為社區(qū)提供多種服務(wù)。在有些停車設(shè)施的規(guī)劃建設(shè)中,以建筑機(jī)械停車設(shè)施為中心,充分考慮周邊環(huán)境、地形地貌、服務(wù)群體的多種需求,把停車設(shè)施建成區(qū)域服務(wù)中心,開發(fā)其綜合效益。二、選題目的和意義隨著城市的發(fā)展、人口的增長(zhǎng)及人們生活水平的提高, 汽車這一現(xiàn)代化的交通工具與日俱增, 停車難成為困擾城市發(fā)展的一大難題。作為解決城市靜態(tài)交通的有效措施——向空間、向高層發(fā)展的自動(dòng)化立體停車設(shè)備,以其占地面積少、停車率高、布置靈活、高效低耗、性價(jià)比高、安全可靠等優(yōu)點(diǎn),越來越受到人們的青睞。目前市面上常見的機(jī)械式立體停車庫(kù)有:升降橫移類、垂直循環(huán)類、多層循環(huán)類、水平循環(huán)類、平面移動(dòng)類、巷道堆垛類、垂直升降類和簡(jiǎn)易升降類等 8 種,其中升降橫移類以其結(jié)構(gòu)簡(jiǎn)單、操作方便、安全可靠、造價(jià)低等優(yōu)點(diǎn),在國(guó)內(nèi)車庫(kù)市場(chǎng)占有絕對(duì)優(yōu)勢(shì)的市場(chǎng)份額。升降橫移類停車庫(kù)指的是采用以載車板升降或橫移存取車輛的機(jī)械式停車設(shè)備的立體停車庫(kù)。由于升降橫移類停車設(shè)備的形式比較多,規(guī)模可大可小,對(duì)場(chǎng)地的適應(yīng)性較強(qiáng),因此,采用這類設(shè)備的停車庫(kù)十分普遍。其工作原理為:每個(gè)車位均有載車板,所需存取車輛的載車板通過升、降、橫移運(yùn)動(dòng)到達(dá)地面層,駕駛員進(jìn)入車庫(kù),存取車輛,完成存取過程。停泊在這類車庫(kù)內(nèi)地面的車只作橫移,不必升降,上層車位或下層車位需通過中間層橫移出空位,將載車板升或降到地面層,駕駛員才可進(jìn)入車庫(kù)內(nèi)將汽車開進(jìn)或開出車庫(kù)。運(yùn)行特點(diǎn): 最下層只能進(jìn)行平移, 頂層只能進(jìn)行升降, 中間層既可平移又可升降。除頂層外, 中間層和底層必須留一空車位, 保證上下車通道的暢通??偟脑瓌t: 升降復(fù)位, 平移不復(fù)位。采用以載車板升降或橫移存取車輛的機(jī)械式停車設(shè)備的立體停車庫(kù)。此類型立體車庫(kù)適用于地面及地下停車場(chǎng) 配置靈活,造價(jià)較低。這種類型立體車庫(kù)的特點(diǎn)是結(jié)構(gòu)簡(jiǎn)單。形式較多,規(guī)??纱罂尚?采用模塊化設(shè)計(jì) ,每單元可設(shè)計(jì)成 2~5 層 、半地下等多種形式 ,車位數(shù)從幾個(gè)到上百個(gè)。對(duì)場(chǎng)地的適應(yīng)性強(qiáng) 約占國(guó)內(nèi)停車市場(chǎng)份額 70%以上。而現(xiàn)有停車位缺口嚴(yán)重?fù)?jù)預(yù)計(jì) 2015年轎車保有量將達(dá)到 2000 萬輛, “十二五”期間轎車保有量將增加 400 萬輛。停車位需求按 1:1.2(100%的基本停車位和 20%的公共停車位)計(jì)算,總需增加停車位 480 萬個(gè)。平均每年需求 96 萬個(gè)車位。如僅考慮 10%進(jìn)機(jī)械式停車庫(kù),這每年需提供機(jī)械式停車庫(kù) 9.6 萬個(gè)車位。因此從現(xiàn)有的停車位的缺口情況和今后市場(chǎng)的需求可以看出,機(jī)械式停車設(shè)備的國(guó)際、國(guó)內(nèi)市場(chǎng)前景十分良好。因而我對(duì)立體停車庫(kù)中的升降橫移停車庫(kù)進(jìn)行分析。三、現(xiàn)如今發(fā)展現(xiàn)況自動(dòng)立體停車裝備系統(tǒng)在世界各地的發(fā)展是極不均衡的,德國(guó)開發(fā)最早,技術(shù)居于領(lǐng)先地位,在二層及多層平面式立體停車庫(kù)系列中,它已發(fā)展了 H 型、U 型和 V型。日本由于國(guó)土面積小而應(yīng)用最廣,自從 1959 年引進(jìn)了建造機(jī)械式立體停車庫(kù)技術(shù)之后,到 1983 年,就已經(jīng)在本土上共建造了 25454 座多種形式的機(jī)械式車庫(kù),平均每座容車量達(dá)到十輛左右,最多的能達(dá)到百輛以上。從上世紀(jì)七十年代末期起,車庫(kù)容量年遞增率為 5%-7%,已經(jīng)趕上了同期汽車擁有量的年遞增率 4%-6%,從技術(shù)特征上看,日本更重視豎式自動(dòng)立體車庫(kù)的發(fā)展,即密集型自動(dòng)立體停車庫(kù)的發(fā)展。進(jìn)入 20 世紀(jì)以來,在國(guó)內(nèi)舉辦了多個(gè)與停車設(shè)備相關(guān)的展覽會(huì),全自動(dòng)立體停車設(shè)備的容車能力及其技術(shù)完備,先進(jìn)程度已被世界廣泛承認(rèn)和接受。國(guó)外停車設(shè)備在國(guó)內(nèi)市場(chǎng)上也開始推廣使用。停車問題是城市發(fā)展中出現(xiàn)的靜態(tài)交通問題。靜態(tài)交通是相對(duì)于動(dòng)態(tài)交通而存在的一種交通形態(tài),二者相互關(guān)聯(lián),相互影響。對(duì)城市中的車輛來說,行駛時(shí)為動(dòng)態(tài),停放時(shí)為靜態(tài)。停車設(shè)施是城市靜態(tài)交通的主要內(nèi)容。隨著城市中各種車輛的增多,對(duì)停車設(shè)施的需求量也在不斷的增加,如果兩者之間失去平衡,停車設(shè)施難以滿足車輛增長(zhǎng)對(duì)停車空間的需求,就會(huì)出現(xiàn)車是停車難的問題。 2000 年以來我國(guó)車市機(jī)動(dòng)車增長(zhǎng)速度平均在 10%—15%,而城市道路平均增長(zhǎng)速度只有2%—3%,特別是大城市的機(jī)動(dòng)車擁有量和交通的增長(zhǎng)遠(yuǎn)遠(yuǎn)超過交通基礎(chǔ)設(shè)施的增長(zhǎng)速度。如北京市,在 20 世紀(jì) 90 年代,小汽車年平均增長(zhǎng)速度達(dá)到 30%左右,尤其是私人轎車增長(zhǎng)更快,1992—1995 年年遞增率達(dá)到 45%以上,是全市機(jī)動(dòng)車平均年遞增率的三倍,有的年份增長(zhǎng)率達(dá)到 100%,但城市道路平均增長(zhǎng)率僅為 1.2%,道路面積增長(zhǎng)率為 3.7%。在國(guó)際上一般認(rèn)為城市道路面積率(城市道路面積與城市總面積之比)應(yīng)當(dāng)在 25%為宜。美國(guó)華盛頓市為 43%,紐約、曼哈頓市為 35%,英國(guó)倫敦市為 23%,日本東京為 13%,北京市僅為 11%。隨著機(jī)動(dòng)車數(shù)量的日益劇增,很多大中城市不僅出現(xiàn)了道路上動(dòng)態(tài)交通的嚴(yán)重堵塞,而且占用道路停車和占用居住區(qū)綠地停車的現(xiàn)象越來越嚴(yán)重,從而進(jìn)一步加劇了交通個(gè)擁擠,破壞了城市的居住環(huán)境。城市的停車難、亂停車的狀況日益嚴(yán)重,已經(jīng)影響到投資環(huán)境和城市形象,引起了各方人士的普遍關(guān)注,專業(yè)的車場(chǎng)管理公司已經(jīng)開始關(guān)注這一問題。從總體上看,城市停車難問題的出現(xiàn)主要體現(xiàn)在停車需求與停車空間不足的矛盾、停車空間擴(kuò)展與城市用地不足的矛盾上。參考文獻(xiàn): [1] 付翠玉,關(guān)景泰, 《立體車庫(kù)發(fā)展的現(xiàn)狀與挑戰(zhàn)》 ,機(jī)械設(shè)計(jì)與制造,2005. [2] 中國(guó)重型機(jī)械工業(yè)協(xié)會(huì), 《停車設(shè)備管理委員會(huì)編》 ,機(jī)械式立體車庫(kù),海洋出版社,2001. [3] 任伯森等, 《機(jī)械式立體車庫(kù)》 ,海洋出版社,2001. [4] 中華人民共和國(guó)機(jī)械工業(yè)部,機(jī)械行業(yè)標(biāo)準(zhǔn) , 《機(jī)械式停車設(shè)備類別、型式與基本參數(shù)》 ,1998. [5] 《機(jī)械設(shè)計(jì)手冊(cè)》①、②、③、④,北京,機(jī)械工業(yè)出版社,2004. [6] 張春雷《電機(jī)選用安裝與故障檢修》 ,北京,中國(guó)電力出版社,2007. [7] 王三民,《機(jī)械原理與設(shè)計(jì)》 ,北京,機(jī)械工業(yè)出版社,2007. [8] 宋曼華等編, 《鋼結(jié)構(gòu)設(shè)計(jì)與計(jì)算》 ,機(jī)械與電子,2001. [9] 程子華, 《PLC 原理與編程實(shí)例分析》 ,國(guó)防工業(yè)出版社,2007. [10] 張還, 《三菱 FX 系列 PLC 設(shè)計(jì)與開發(fā)》 ,北京,機(jī)械工業(yè)出版社,2009. [11] 陳立德, 《機(jī)械設(shè)計(jì)基礎(chǔ)課程設(shè)計(jì)》 ,高等教育出版社,2011. [12] 陳立德, 《機(jī)械設(shè)計(jì)基礎(chǔ)課程設(shè)計(jì)》 ,高等教育出版社,2011. [13] 范欽珊,《材料力學(xué)》 ,清華大學(xué)出版社,2008. [14] 陳立德, 《機(jī)械制造制造技術(shù)基礎(chǔ)課程設(shè)計(jì)》 ,高等教育出版社,2009. [15] 濮良貴, 《機(jī)械設(shè)計(jì)》 ,高等教育出版社,2013. 畢 業(yè) 設(shè) 計(jì)(論文) 開 題 報(bào) 告 2.本課題要研究或解決的問題和擬采用的研究手段(途徑): 一、研究的主要內(nèi)容:本論文所設(shè)計(jì)的升降橫移式立體車庫(kù),在實(shí)際設(shè)計(jì)過程中可以分為結(jié)構(gòu)框架、上載車板和他的提升系統(tǒng)、下載車板及其橫移系統(tǒng)、安全裝置、控制系統(tǒng)等幾大部分,各個(gè)部分都有著他們各自的作用,通過他們之間的相互配合實(shí)現(xiàn)了車輛的存取,論文主要對(duì)每個(gè)部分進(jìn)行逐步的分析。二、擬采用的研究手段(途徑):(1)方案的總體設(shè)計(jì) 1)傳動(dòng)方案的設(shè)計(jì) 2)傳動(dòng)方案的選用 (2)主框架的設(shè)計(jì) 1)框架結(jié)構(gòu)形式的選用 2)框架結(jié)構(gòu)材料的選用(3)升降與橫向傳動(dòng)系統(tǒng)的設(shè)計(jì) 1)電動(dòng)機(jī)、傳動(dòng)鏈條、軸與軸承的選用 2)軸與軸承的強(qiáng)度校核(4)控制系統(tǒng)和安全防護(hù)系統(tǒng)的設(shè)計(jì) 1)控制系統(tǒng)的設(shè)計(jì) 2)安全防護(hù)系統(tǒng)的設(shè)計(jì) 畢 業(yè) 設(shè) 計(jì)(論文) 開 題 報(bào) 告 指導(dǎo)教師意見:1.對(duì)“文獻(xiàn)綜述”的評(píng)語:查閱了相關(guān)的文獻(xiàn)資料,對(duì)立體車庫(kù)的研究背景與目的、國(guó)內(nèi)外的研究特點(diǎn)以及各種常見結(jié)構(gòu)方案的特點(diǎn)與局限性有了一定的了解。論述基本清楚,符合規(guī)范要求。2.對(duì)本課題的深度、廣度及工作量的意見和對(duì)設(shè)計(jì)(論文)結(jié)果的預(yù)測(cè):本課題具有一定的廣度和深度,工作量適度,通過對(duì)相關(guān)文獻(xiàn)的查閱和實(shí)際調(diào)研,相信可以完成本次設(shè)計(jì)。3.是否同意開題:√ 同意 □ 不同意指導(dǎo)教師: 2016 年 03 月 07 日所在專業(yè)審查意見:同意 負(fù)責(zé)人: 2016 年 03 月 08 日 AUTOMATED PARKING: STATUS IN THE UNITED STATESADVANTAGES AND CRITERIARICHARD S. BEEBE, DIRECTOR PARKING AND TRANSPORTATION PLANNING CONSULTING ENGINEERS GROUP, INC. 55 E. EUCLID AVE., MT. PROSPECT, IL 60056 USA PRESENTED AT WORLD PARKING SYMPOSIUM III ST. ANDREWS, SCOTLAND: JUNE 25, 2001AUTOMATED PARKING – THE ENVIRONMENTAL SOLUTION TO THE URBAN PARKING SHORTAGE ADVANTAGES AND CRITERIA GUIDELINES TO AUTOMATED GARAGE DEVELOPMENT??The current state-of-the-art automated parking systems ? Types ? Capacities ? Operating Systems ? Site Area Criteria ? Financial/Operating Advantages ? Land Area and Savings ? Operation’s Savings ? Cost Features of Vehicle/Patron Security ? Time and Motion ? Environmental Advantages ? Reduced Miles of Interior Travel ? Reduced Emissions Production ? Reduced Noise Generation ? Reduced Construction Products and Impacts of Construction Activity ? System Applications ? Location – Freestanding or Inside Buildings ? Capacity and Structure Design ? User Populations and Specific Needs ? Traffic and Exterior Conditions ? Typical Installations ? Above Ground ? Below Ground ? Site and Operating Statistics ? Movement Toward System Recognition/Criteria for Development ? Parking Interests ? Potential User Interests ? International Media Attention ? Product PromotionHISTORY OF MECHANICAL PARKING IN THE U.S. AND ITS STATUS IN 2001 INTRODUCTION Mechanical parking systems were first introduced in the U.S. using freight elevators about the time of World War I. During the 1920’s and 1930’s a series of other patents were granted but it was not until the late 1940’s that the Bowser, Pigeon Hole and Roto Park systems became operational and installed in numerous locations. Some of these early systems were vertical elevator lift modules that placed cars on upper levels of a structure to be moved by attendant and others mechanical devices that could move vehicles into “slots” in a framework built around a central corridor. Capacities ranged typically from less than 100 spaces to more than 600. All of these “early days” systems shared common characteristic—the use of a site area much smaller than the area needed for a conventional garage. During the next twenty-five years many of these systems operated for up to twenty years or so—a few remain in operation today. Problems related to the timely delivery of patron vehicles due largely to inoperative elevator and mechanical systems caused many units to be dismantled. For the next twenty-years there was some discussion of “advanced” mechanical garage systems appearing in Europe and Asia, but no major projects which were planned on were constructed in the U.S. During the past decade the constant demand for parking, especially in large urban centers, created a new U.S. interest in these high technology foreign systems—automated, computer-based systems that added speed, reliability and safety to the basic garage types invented fifty years earlier. European and Asian manufacturers have begun to market their systems and establish offices in the U.S. Several U.S. firms also have entered the marketplace and created greater local interest in Automated Parking. System manufacturers or marketers now include such names as TREVI, Klaus, KRUPS, WOHR, Robotic, APS, HK Systems, Stokes, Auto Space, Sky Parking America and others. Some 100 of these projects are now in the planning stage. SYSTEM ADVANTAGES There are obvious advantages for automated parking facilities in almost any urban location. Significant reduction in land area requirements means conservation of land resources and smaller building bulk cubes and costs. Automated garage operation results in far lower vehicle miles of travel, emission volumes and utility services. Reduced personnel and maintenance costs help to offset any higher per-space cost of automated systems. These advantages have created a large scale market potential in the U.S. which needs to be satisfied as quickly as possible. The following basic elements of automated structure construction point out some of these advantages: A. Developmental 1) An important consideration of automated/mechanical parking has always been project cost. For comparison purposes costs must reflect total cost, including land. The higher cost of construction of an automated system can usually be offset by the value of the smaller land area required for automated construction. For example, a site area roughly 100 feet x 120 feet (12,000 square feet) could support a 400 space automated garage. A conventional ramp garage would require a site area at least 120′ x 280′ (or 33,600 square feet). The cost of land, at $100 per square foot, would equal $1,200,000 for the automated site versus $3,600,000 for the conventional garage. This differential translates into a per space allowance of $5,500 for the automated facility. This is usually the primary factor in establishing the need for, and interest in, an automated garage. In densely developed urban areas the availability of large sites for garage construction has become the number one problem. 2) In addition to the land area/cost factor there are other important reasons to consider an automated structure. These include the provision of unusual levels of patron and vehicle security: (This item is particularly appealing to owners of expensive vehicles wishing to protect their investment). Depending upon location, security issues where patrons do not move inside a garage can be a very important consideration to both owners and users. Negative noise and visual impacts of conventional garages are also eliminated. 3) Automated structures can be built into larger buildings, either above ground or below ground, in significantly less floor area and within a structural framework compatible with that of the primary use. Since there is no need for open areas along perimeter walls to achieve ventilation requirements the parking facility can be enclosed by an architectural fa?ade on those exposures visible to the public, eliminating the negative visual characteristics of a standard garage building. 4) These new systems offer another great benefit to owners and operators. Because of computerized control and report elements complete garage diagnostic review and warning is always on-line. Any potential problem is reported at once to a central control station where attention can be directed at once to the problem. B. Financial 1) The primary financial benefit of automated parking is usually the reduction in land cost. On the theory that an automated structure uses about one-half the land area, the cost savings in land can range from 100 percent to 400 or 500 percent depending upon the value of adjacent property. 2) Owner or operator savings may well be significant since many of these facilities can operate without any staff or with a single attendant. 3) Security aspects of the facility tend to lower insurance costs and maintenance, except for the automated system components, is also reduced. 4) In some locations there may be an added financial incentive. This is the classification of the automated system as machinery and not as structure which can materially reduce property tax burdens. C. Environmental 1) There is a keen awareness developing in the U.S. of environmental hazard created by vehicle operation in congested areas. Vehicle-generated solution can be significantly reduced by reducing miles of travel in the garage. In a typical 600 space conventional garage with twice daily turnover up to 300 miles to travel are eliminated every day. 2) Reduction in miles of travel equals reduction in emissions such as carbon monoxide and nitrates and oxides of nitrogen which are considered major problems in most urban places. 3) Less disruptive but equally important environmental issues, especially in any densely developed area, include light and noise created by vehicles moving into, through and out of a conventional garage. These elements are almost totally removed by use of an automated structure. 4) Another element here is the reduction in the amount of construction activity and disruption due to the reduction in site area and construction volume. CURRENT CONDITIONS IN THE U.S. An Automated Parking Garage was started in the City of Hoboken, New Jersey in January of 1999. This 320 space project was regarded as the first in a long series of new automated garages to be built across the country. At least 40 to 50 garages were “on the list” for construction and Hoboken was considered the beginning of a new era in parking—catching up to the technology in use in Europe and Asia. More than a dozen U.S. and foreign manufacturers have been ready to sell their products and construct facilities. A series of delays and project completion problems have stopped work on the Hoboken garage for the past year. At this time it appears that this garage will not be completed until spring of 2002. The complex series of delays and problems has generated considerable adverse publicity and apprehension on the part of many possible clients. Nevertheless, there is still great interest in these automated garages throughout the U.S. The advantages of automated parking will overcome the problems now occurring in the Hoboken garage.The experience gained in Europe and Asia by major system manufacturers will be the important factor in starting new projects in the U.S. this year and next. We welcome the entrance to our mark of the European and Asian manufacturers. The international automated parking industry, although small in number and without demonstrable U.S. projects, needs to overcome the current conditions and forge a new understanding of the advantages of automated systems and the broad advantages and practicalities of their use. The objective today is to outline application options and to establish basic project criteria by which clients and manufacturers can assure the adequacy and functionality of the parking system when installed. Understanding of these new systems from several viewpoints is the essential key to expanding acceptance and installation. Public and private agencies need to become aware of performance, reliability, operation and maintenance cost considerations and patron acceptance. The automated parking industry has formed a trade group known as the Automated/Mechanical Parking Association to promote the benefits of these new systems. The subject of automated parking has not been widely recognized in this country for many years, even within parking and development industries. But the new systems are technologically and operationally far superior to the units built in previous decades. Owners, builders, agencies and patrons can be assured of cost-effective, reliable, safe and efficient services at competitive rates. A significant response to the benefits of these new systems is already forming, and use will accelerate rapidly as national awareness of the compelling reasons for the use of automated/mechanical parking systems gains momentum. We need to explore and expand the increased construction of automated parking facilities in the U.S. The advantages of this technology are just too significant to permit further delay in their development and construction. However, a number of important lessons have been learned that need to be addressed by any automated system manufacturer.APPLICATIONS In order to properly plan, design, construct, manage and operate an automated facility in the U.S. a number of vital issues must be considered. There follows a summary of these particular items: 1. Theoretically, automated parking requires about one-half the land area of a conventional garage to serve the same number of vehicles. However, this theory has several variables such as: ?? The required capacity of the garage ?? Availability of additional land for conventional garage construction ?? Cost of additional land to facilitate conventional garage construction ?? Garage user populations, turnover, rates, access patterns ?? Parking rates and anticipated revenue compared to costs of garage construction and operation. ?? Project costs of the automated facility versus the conventional facility, given the total cost comparison package. The simple fact that adequate land area is not available to construct a conventional garage does not, in any way, mean an automated facility will prove economically feasible in a particular location. 2. Details of the potential site can be very critical. For an automated facility good street access is essential and, in some cases, multiple frontages can be the difference between feasibility and failure. If primary ingress is from a major street, garage vehicle acceptance rates can be very important. Long queue lines awaiting entry affect the acceptance and use of the facility—more importantly, local police may prohibit vehicles standing in the street to gain access. There are standard ratios of entry/exit portals to garage capacity with a sub-set of determinants based on street traffic patterns and interior garage space layouts and vehicle acceptance/delivery times. Project feasibility can be affected by street traffic operations and other external factors adjacent to the garage site. It is, therefore, essential to fully understand the impacts of these conditions on the design of the facility. 3. The true and total cost of the parking facility—both the automated system and any shell enclosure building—must be properly defined. This leads to a number of questions concerning the project, the project team and the project proposal. For example: ?? Is the automated system manufacturer the contractor or a sub-contractor. ?? If the system manufacturer is the contractor (bidder) he/she must submit all required data and bid realistic costs to include the total price of bid package requirements. ?? If the manufacturer is a sub-contractor will he/she provide project cost data to more than one prime contractor. ?? In most instances the cost of the system and the cost of the shell building should be separated with individual unit costs and payment schedules. ?? Details of the owner’s project bid announcement should describe all project components and cost issues, as well as the total package of compliance items necessary for project acceptance. Bidders should review all background information and particularly the project planning or feasibility studies, to understand the required revenue stream necessary to fund the project and cover potential costs, and then to submit realistic bid data that can ensure feasibility of the completed garage. TYPICAL INSTALLATIONS Within the U.S. there are a wide variety of locations and parking facility needs that will attract the installation of automated parking structures. This variety of project types is one of the principal reasons why the market is strong for a number of different system manufactures. Some of the projects now being studied for automated parking facilities provide an interesting directory of potential developments: ? A 400 space garage on an L-shaped site. The garage will support a ten story residential building (120 units) above. ? A 164 space garage to be built underground as part of the foundation for a twelve story residence towers. ? An 800 space garage on the main shopping street in a large city—half of the spaces are to be for short-term parking. ? Two 75 space garages to be constructed in a five building apartment complex to reduce the amount of parking inside residence building. ? A 3,000 space garage as part of a large, mixed-use development with long-term and short-term parking requirements. ? A 56 space garage to serve a small resort hotel. ? A 4,000 space garage to provide on-site storage for rental car facility at a large airport. ? A 130 space garage to store new vehicle in a vehicle sales agency. SYSTEM CRITERIA There are two distinct sets of project criteria to be considered in the process of constructing an automated parking facility. The first Criteria Package is directed to ensuring that Manufacturers address all critical compliance issues and define system characteristics as required by the project plans and specifications. The second Criteria Package is directed to potential Owners as a means of ensuring that contractor bid submissions comply fully with project requirements. These criteria are very important in establishing the detail of the project; how it will be designed and constructed; how much it will cost; how it will be operated and if it will produce revenue to retire its debt.MANUFACTURER CRITERIA PACKAGE A. System Definition and Operating Characteristics ? Type of system – pallet, comb, plate or other. ? Type of frame/slot arrangement and frame connection to building shell details ? Basic operating features of the system – technology description ? Basic operating speeds for vehicle intake and delivery; elapsed time in seconds ? System use of turntable or vehicle thru in/out movement patterns ? Entry/exit bay details – Singing, signals, vehicle/pedestrian controls and alarms – Capacity – Design formats – Pallet, plate or comb movement throughout the garage – Elapsed time of vehicle intake movement from bay to carrier to slot/from slot to carrier to bay for retrieval ? Average cycle time in/out per vehicle ? Control system functions via sensors, cameras or other devices and oversight of actual internal parking maneuvers ? Testing schedules and maintenance/warranty assumptions. B. System Design Features ? Redundancies ? Security systems ? Stand-by power ? Sensors-motion detection ? Weather conditioning ? Component cleaning – methods and frequency ? Diagnostics and form of response to service/repair orders and alarms ? Spare parts inventory, location, re-order details ? Maintenance inspection program-schedules, procedures, reports ? Major component replacement program ? Life-cycle data and costs C. System Performance Standards ? Define system development, prior testing, patients, etc. and current status ? Describe completed system installations with detail of type, size, exact location, operating features and owner/operator references ? Describe the system warranty to be provided with purchase ? Describe subsequent system maintenance agreements and terms (one-year to multi-year) ? Describe typical operating and maintenance costs for system and for per-space cost comparison analysis ? Describe system-wide performance testing and acceptance at completion ? Describe system training program and training manuals ? Describe system operations manuals and patron use instruction materials ? Describe patron access control systems and total system (patron use) report formats and detail or report transfer to owner ? Describe administration, marketing and activity/revenue/customer use assistance; reporting—formats, responsibilities, techniques, final forms. OWNERS CRITERIA PACKAGE A. Contractural Items ? Check plans against all applicable codes and utility services requirements. ? Check plans for shell building and erection details, system and sub-system interface, functional operation of the total system as a unified facility. ? Check overall schedule, task completion dates and sign-off requirements. ? Check all contractor references, sub-contractor references, equipment suppliers and major parts descriptions and availability. ? Check bonds, insurance coverages, contract language amendments or exceptions re: claims, performance standards, auditing, payouts, etc. ? Check provision for full-scale warranty, maintenance, training services for minimum multi-year period. ? Check provision for periodic owner inspections and subsequent pay request authorizations based on certified percentage of completion by outside experts. ? Require computer software escrow. ? Check provision for all system operation, maintenance, performance, training and other manuals and practices. ? Check system activity records production, operational audits, management coordination with manufacturer. B. Systems Operations ? Check uti