【溫馨提示】壓縮包內(nèi)含CAD圖有下方大圖片預(yù)覽,下拉即可直觀呈現(xiàn)眼前查看、盡收眼底縱觀。打包內(nèi)容里dwg后綴的文件為CAD圖,可編輯,無水印,高清圖,壓縮包內(nèi)文檔可直接點開預(yù)覽,需要原稿請自助充值下載,所見才能所得,請見壓縮包內(nèi)的文件及下方預(yù)覽,請細心查看有疑問可以咨詢QQ:11970985或197216396
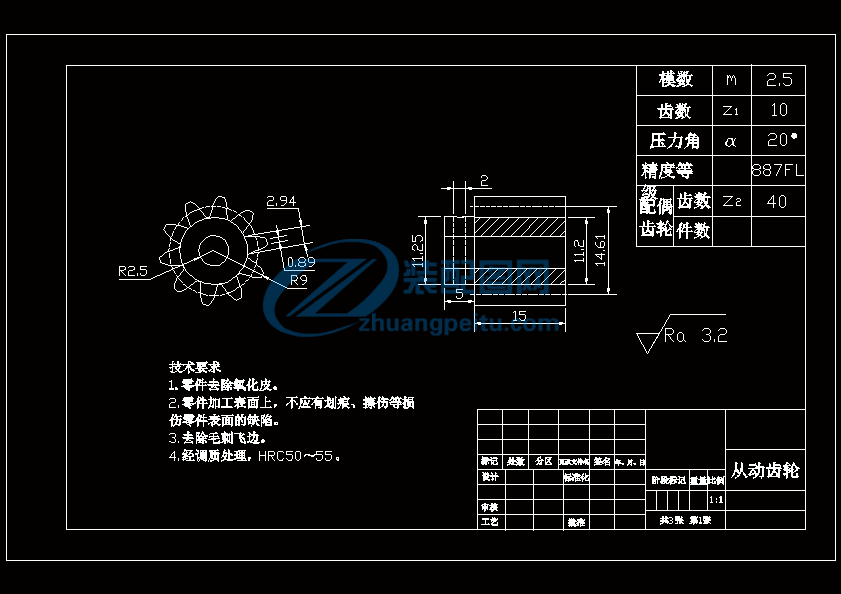
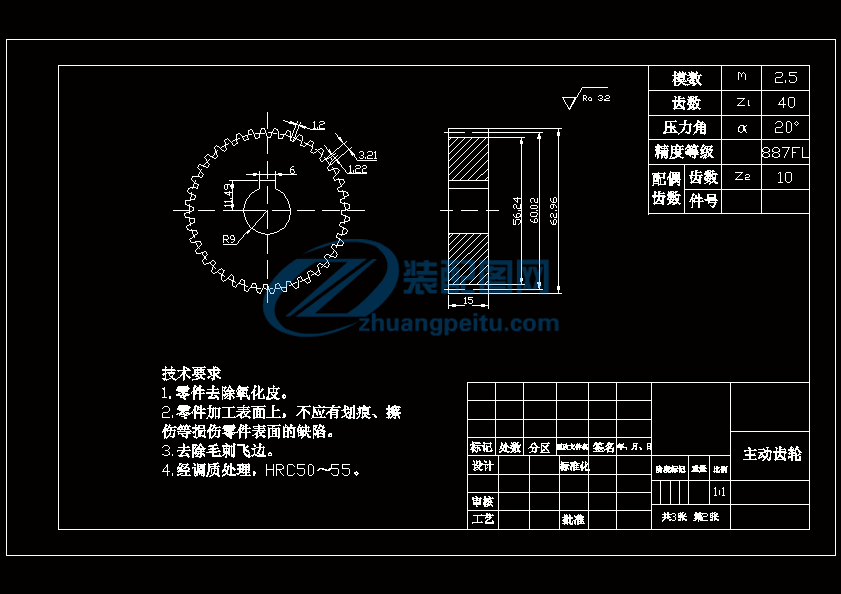
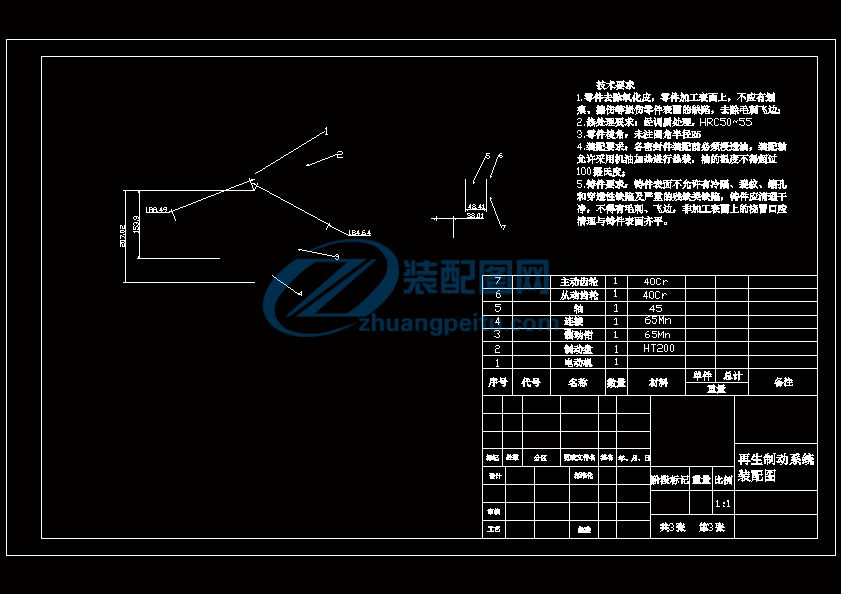

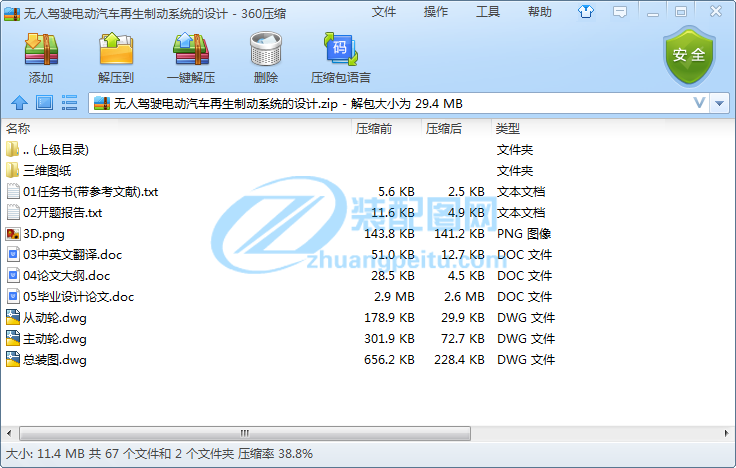
畢 業(yè) 設(shè) 計(論 文)外 文 翻 譯
設(shè)計(論文)題目:
無人駕駛電動汽車再生制動系統(tǒng)的設(shè)
?
計
學生姓名:
專??業(yè):
所在學院:
指導教師:
職??稱:
?
年12月31日
Research of automobile regenerative brake
The automotive industry has for many years identified weight reduction as a way of improving product competitiveness and thus the ability to make profits. One area that has been examined for weight reduction is vehicle with regenerative braking system (RBS). The greatest advantages of electric vehicles (EVs), and hybrid electric vehicles (HEVs) is their ability to recover significant amounts of braking energy using a RBS. Regenerative braking is an effective method to extend brake disc life, minimise disc rotor weight, minimise brake pad wear and to extend the working range of an EV or HEV. Regenerative braking would extend the working range of an EV or HEV provided that any extra energy consumption e.g. from increased vehicle mass and system losses did not outweigh the saving from energy recuperation, also reduce duty levels on the brakes themselves, giving advantages including extended brake rotor and friction material life, but more importantly reduced brake mass, minimise brake pad wear. The objective of this research is to define thermal performance on lightweight disc brake models. Thermal performance was a key factor which was studied using the 3D model in Finite Element Analysis simulations. Ultimately a design method for lightweight brakes suitable for use on any car-sized hybrid vehicle was used from previous analysis. The design requirement, including reducing the thickness, would affect the temperature distribution and increase stress at the critical area. Based on the relationship obtained between rotor weight, thickness, undercut effect and offset between hat and friction ring, criteria have been established for designing lightweight brake discs in a vehicle with regenerative braking.
It has been estimated that up to 70% of the kinetic energy of a passenger car could be dissipated through the friction brakes and the other (up to) 30% of the energy could be recuperated e.g. in the form of electrical power [1]-[2]. The need for conversion from kinetic energy to thermal energy by friction brakes therefore will decrease once regenerative braking is present in the system. The rest of the energy can be converted e.g. to electrical energy via a motor/generator (M/G). For a car with regenerative braking under a single stop braking event, where the energy dissipated via the front disc brakes is estimated as 70% of the total kinetic energy.
Manuscript received October 9, 2012; revised December 4, 2012. This work was supported in part by the UTM Razak School of Engineering and Advanced Technology under Grant 4J079.
weight reduction as a way of improving product competitiveness and thus achieving commercial success. To achieve reduction in weight, components made of materials such as iron and steel can be replaced with re-designed components made of lighter materials such as polymers and aluminium. One area that has been examined for weight reduction is the brake system, e.g. aluminium and associated composite materials such as ?metal matrix composites? (MMC) for brake rotors have been studied extensively. Although aluminium is increasingly used in modern brake components, the frictional and thermal requirements of a modern automotive brake have limited its use for brake discs [3]. Friction brakes get hot when used and the heat energy is dissipated by forced convection, conduction and radiation from the exposed surfaces of the brake. Over-heating can cause malfunction of the braking system and present a safety hazard. Much theoretical work has been done to calculate accurately the temperature rise during braking for different speeds and designs of brake discs. [3]–[8] so the extent of the thermal loading on brake discs (rotors) is well-known.
Disc brakes are widely used on cars because of their better heat dissipation ability; a direct result of the exposed friction surface. The friction surface of a drum brake is inside and heat dissipation relies upon heat being conducted through the drum so car manufacturers fit drum brakes only on the rear axle of “l(fā)ow” performance cars. Additionally a drum brake provides a very effective parking brake. In commercial vehicles, drum brakes are still widely used across the world, being robust, durable and easy to maintain but in Europe most heavy goods vehicles now use disc brakes [9]. Furthermore, the performance requirement is not just for one isolated brake application, but for a series of high deceleration brake applications which form the part of the performance assessment known as the ?fade? test. So, the front brakes of a typical passenger car have to be designed to provide large amounts of braking torque, and withstand large amounts of heat generated, heat transfer, high temperatures and thermal loading. The size (and weight) of a car?s disc brake therefore depends upon the performance required, specifically the braking torque, energy dissipation and power. It is possible to generate high braking torque from a smaller brake, but the energy and power involved may overload the brake and cause physical damage. Lightweight disc brakes (smaller in size using lighter materials designed for lower duty) have potential for passenger cars with regenerative braking. Regenerative braking is a feature of a hybrid and pure electric power train to recoup some of the energy dissipated during braking [10]. EVs and HEVs have the ability to recover significant amounts of braking energy using the electrical part of the power train as a RBS. However, even with regenerative braking, friction brakes are required to provide the necessary high duty braking performance, e.g. in the event of an emergency stop being required. Regenerative braking therefore has to work alongside a conventional friction system because the braking power in an emergency is too high for a purely electrical regenerative system: this is primarily due to the limited energy transfer rate of electrical energy storage devices. Regenerative braking does however take work off the friction brakes of a vehicle, thereby extending brake disc life, minimising disc rotor weight, minimising brake pad wear and extending the working range of an EV or HEV.
Regenerative braking in an EV cannot be used when the batteries are fully charged, or when the battery is at a high temperature because this could damage the battery. At low vehicle speeds regenerative braking could generate high braking torque causing vehicle instability (if a continuously variable transmission (CVT) is used to keep the M/G at its optimum operating speed); this need to be carefully controlled to avoid poor braking ?feel?. Braking energy recuperation for hybrid vehicles has been investigated by Ehsani et al., [2] using computer simulation to analyse the relationship between the recuperated braking energy from front wheels to the total braking energy available in a typical urban driving cycle. The results showed that 50% - 60% of braking energy could be recovered by regenerative braking in urban driving. Regenerative braking can recover about 45% of total kinetic energy for a city bus。
The design of the connection between the friction ring and the hub is important in a lightweight brake disc. The importance of this connection has been recognised and understood for many years [16] and car brake disc designers pay careful attention to the design of the so-called “top hat” region of the disc. Which friction face is mounted to the top hat, and the design of “undercut” both enable coning to be controlled within acceptable limits. However the lightweight brake disc of the type proposed here has a completely different temperature profile, both in terms of the magnitude of the temperatures reached during braking, and the distribution of temperature in the disc. This is also known from the use of lightweight discs on motorcycles but, again, International Journal of Applied Physics and Mathematics, Vol. 3, No. 1, January 2013 5 7 the duty levels are much different. This work predicts the magnitude and distribution of temperature in a lightweight brake disc for a passenger car and consequently the expected coning. It therefore provides an indication of what design steps must be taken to keep coning to acceptable levels in operation.
It can be concluded that stainless steel is a suitable material for a lightweight brake disc in terms of mechanical and thermal strength, provided that the tribological characteristics are suitable (e.g. it might be advantageous to use different pad materials). Stainless steel is suitable to be used for disc thicknesses less than 8 mm because stainless steel has three times the tensile strength of cast iron (Table IV). For disc thicknesses of 8 mm or greater cast iron is suitable because of its high thermal conductivity and low Young?s modulus, which limit the amount of disc damage caused by the heat flux generated by friction. When choosing the best disc material, aside from the properties which have been referred to in Table I, the heat capacity of the material has been shown to be as significant as the thermal conductivity. Disc material with higher heat capacity can decrease both the maximum surface temperature and the maximum stress applied to the disc surface. But stainless steel seems to be a good material for a lightweight disc, and it is better than Al-MMC because of its higher MOT. A disc made of stainless steel is designed to minimise stresses and distortion.
The contribution made by this research work to the field of vehicle braking is twofold. Firstly, the friction brakes can be downsized on a car with regenerative braking. Reducing the mass of the brake disc must consider temperatures, stresses, wear, deformation and durability. Second the example developed in this research illustrates that it is possible to reduce the brake disc mass by using a lightweight solid disc. The paper also presents a design approach for a lightweight brake disc based on mathematical and numerical (CAE) analysis with than associated experimental investigation. Cooperative braking with regenerative braking and mechanical braking plays an important role in electric vehicles for energy-saving control. Based on the parallel and the series cooperative braking models, a combined model with a predictive control strategy to get a better cooperative braking performance is presented. The balance problem between the maximum regenerative energy recovery efficiency and the optimum braking stability is solved through an off-line process optimization stream with the collaborative optimization algorithm (CO). To carry out the process optimization stream, the optimal Latin hypercube design (Opt LHD) is presented to discrete the continuous design space. To solve the poor real-time problem of the optimization, a high-precision predictive model based on the off-line optimization data of the combined model is built, and a predictive control strategy is proposed and verified through simulation. The simulation results demonstrate that the predictive control strategy and the combined model are reasonable and effective.
Facing the pressure of energy and environment, in the world,the development of electric vehicles and automobile energy saving and recycling has formed a broad consensus,, its further development of automotive technology will be the development of powerful impetus.
譯文:
汽車再生制動器的研究
在汽車產(chǎn)業(yè),多年前就已經(jīng)確認把減輕汽車質(zhì)量作為提高產(chǎn)品競爭力和盈利的手段,在汽車上裝載再生制動系統(tǒng)被一部分地區(qū)檢驗為減輕汽車質(zhì)量行之有效的方法。電動汽車和混合動力電動汽車的最大優(yōu)點是它們能夠通過再生制動系統(tǒng)回收大量的制動能量,再生制動器能夠有效的延長制動盤的使用壽命,減輕制動盤轉(zhuǎn)子的質(zhì)量,盡量減少剎車片的磨損以及使電動汽車和混合動力電動汽車被廣泛使用。再生制動系統(tǒng)會擴展電動汽車或混合動力電動汽車的適用范圍。再生制動器能夠通過減少任何額外能量的損耗來達到幫助電動汽車和混合動力電動汽車擴大適用范圍的目的,在這同時也會減少自身負載,有延長制動轉(zhuǎn)子和摩擦材料使用壽命的優(yōu)勢,但更重要的是,減輕了制動器的質(zhì)量,減少了剎車片的磨損。本研究的目的是確定輕型盤式制動器的熱性能,熱性能是利用三維有限元分析模型的關(guān)鍵因素,最后一個,輕型制動器的設(shè)計適用于任何尺寸的混合動力汽車,這項研究需要減少轉(zhuǎn)子厚度,因為它會影響溫度的分布范圍且增加臨界區(qū)域基于轉(zhuǎn)子的質(zhì)量、厚度、倒底效應(yīng)、以及帽和摩擦環(huán)之間的偏移量的關(guān)系的應(yīng)力,汽車再生制動系統(tǒng)中輕型制動盤的設(shè)計標準已經(jīng)建立。
據(jù)估計,客車中多達百分之七十的動能都會通過摩擦制動器被浪費掉,而另外的百分之三十的能量能夠以電能的形式被回收,從動能轉(zhuǎn)化到熱能需要摩擦制動器,所以這將會減少系統(tǒng)中的一次再生制動,其余的能量能夠通過電機\發(fā)動機來轉(zhuǎn)化為電能,當一輛裝有再生制動器的車處于緊急制動的情況下時,仍會有大約總動能百分之七十的能量被前盤式制動器給浪費掉。
把減輕重量作為一種提高產(chǎn)品競爭力的方法,從而實現(xiàn)商業(yè)上的成功。為了達到減輕重量的目的,鐵和鋼制作的車身部件會被一些重新設(shè)計過的由聚合物或鋁制成的部件所取代。用鋁和相關(guān)復合材料例如金屬基復合材料來制作制動盤已經(jīng)被廣泛的研究。雖然鋁越來越多的用于現(xiàn)代汽車的制動部件,但現(xiàn)代汽車制動的摩擦性能和熱性能要求限制了鋁在制動盤上的應(yīng)用。摩擦制動器在工作時產(chǎn)生熱量,熱量通過強制對流、傳導和輻射從制動器的暴露表面上消散。過熱會導致制動系統(tǒng)的故障,并出現(xiàn)安全隱患。許多有關(guān)于制動過程中處于不同溫度和制動器設(shè)計類型之下的準確的溫度上升量的理論工作已經(jīng)完成,因此,制動盤的熱負荷程度已經(jīng)是是眾所周知的了。
盤式制動器因為它更好的散熱性能而被廣泛應(yīng)用于轎車上,雖然會直接導致摩擦表面的磨損。鼓式制動器的摩擦表面是內(nèi)部散熱,散熱是靠熱傳導,因此,汽車制造商只能在低性能汽車的后橋上安裝鼓式制動器。另外,鼓式制動器能提供一個非常有效的停車制動。在世界各地,鼓式制動器仍被廣泛應(yīng)用于商用車上,因為其結(jié)實耐用且易于維護,但在歐洲重型車輛上現(xiàn)在仍使用盤式制動器。此外,性能要求不是一個孤立的制動器運用,而是一系列高減速制動的應(yīng)用形式的饋效評估,被稱為“褪色”的測試部分。因此,典型的客車前輪制動器的設(shè)計必須要提供一個很大的制動力矩,且能承受高溫、傳熱和熱負荷等要求。一輛汽車盤式制動器的大小取決于性能要求,特別是制動力矩和能量耗散功率。一個小的制動器也有可能產(chǎn)生一個較大的制動力矩,但是它所涉及到的能量和功率可能會超載并造成部件的損傷。輕型制動盤(尺寸小,使用較輕的材料,產(chǎn)生的負荷較小)能在裝有再生制動系統(tǒng)的客車上使用。再生制動系統(tǒng)是混合動力電動汽車和純電動汽車的一個明顯特征,用它來回收一些在制動過程中浪費的能量。電動汽車和混合動力電動汽車能利用再生制動系統(tǒng)回收大量的制動能量并把它們轉(zhuǎn)化為電能儲存起來。但是,即使是有了再生制動系統(tǒng),摩擦制動器仍然是必須的,要靠它來在某些情況下例如車輛的緊急??慨a(chǎn)生高制動性,所以,再生制動系統(tǒng)不得不與常規(guī)摩擦制動系統(tǒng)一起工作,因為對一個純粹的再生制動系統(tǒng)來說,緊急制動情況下的功率太高了,這主要是因為電能儲存設(shè)備的能量轉(zhuǎn)移率的限制。再生制動系統(tǒng)不僅減輕了摩擦制動器的工作壓力,從而延長了制動盤的用壽命,減輕了轉(zhuǎn)子的質(zhì)量,盡量減少了制動片的磨損,而且還擴大了電動汽車和混合動力電動汽車的工作范圍。
電動汽車中的再生制動器在電池已經(jīng)完全充電或者電池處于很高的溫度的情況下是不允許使用的,因為這會對電池造成損害。汽車在低車速的情況下制動時,也有可能產(chǎn)生一個高的扭轉(zhuǎn)力矩,導致汽車的操控穩(wěn)定性下降。在使用無級變速器來保證電機\發(fā)電機處于最佳的運行轉(zhuǎn)速的情況下,這就需要小心的操控來避免制動不良情況的發(fā)生。Ehsan在研究從混合動力汽車中回收制動能量。他通過電腦仿真分析一個城市驅(qū)動循環(huán)中回收的制動能量與總制動能量之間的關(guān)系。他的研究結(jié)果表明,在一個城市驅(qū)動循環(huán)體系中,有百分之五十到百分之六十的制動能量是能夠被再生制動器回收的,再生制動器能夠回收的能量大約占一輛城市公交總制動能量的百分之四十五。
在一個輕型制動盤中,摩擦環(huán)與輪轂之間的鏈接的設(shè)計是至關(guān)重要的,這個連接點的重要性在許多年前已經(jīng)被大眾認識到了。汽車制動盤設(shè)計人員在設(shè)計制動盤上所謂“頂帽”地區(qū)的時候都是十分小心翼翼的。在摩擦面上安裝頂帽以及切凹槽的設(shè)計都使錐旋被控制在一個可接受的范圍內(nèi)。但是,這里提出的這種類型的制動盤有一個完全不同的溫度分布,它表現(xiàn)在制動過程中溫度所能達到的范圍以及溫度在制動盤上的分布狀況。這種情況也出現(xiàn)在了安裝在摩托車上的輕型制動盤上。國際應(yīng)用物理和數(shù)學雜志3卷上指出,在負荷是不相同的情況下,它對于一輛客車上制動盤的溫度范圍和分布情況給出了一個預(yù)計,并對錐旋也進行了預(yù)估。所以該雜志提出一個建議,那就是必須采取措施來保持錐旋在操作中處于可接受的范圍內(nèi)。
可以得出結(jié)論,就機械強度和熱強度而言,不銹鋼是一種適合用來制作輕型制動盤的材料,它會比用其它材料制作而成的襯墊更加的優(yōu)越,此外它的摩擦學特性也完全合乎標準。不銹鋼適合用于制作厚度低于8毫米的制動盤,因為不銹鋼的拉伸強度是鑄鐵的三倍。由于它的高導熱率和較低的彈性模量使它適合用于制造厚度低于8毫米的制動盤或者更大的鑄鐵盤。這也會限制由摩擦所產(chǎn)生的熱通量引起的制動盤的損傷。當選擇最合適用來制作制動盤的材料的時候,除了已經(jīng)被羅列的這么一些特性以外,材料的熱容量也被證明與材料的熱傳導率同樣重要。制動盤的材質(zhì)如果能擁有更高熱容量的話,就可以最大限度的降低最高的表面溫度以及作用于制動盤表面的最大應(yīng)力。不銹鋼似乎是一個很好的制造輕型制動盤的材料,因為它更高的MOT,所以它比鋁基復合材料更加適用于制作制動盤。人們通過設(shè)計不銹鋼制成的制動盤來盡量減少應(yīng)力和變形。
這項研究工作在汽車的制動領(lǐng)域的貢獻是雙重的。首先,當汽車上裝載有再生制動器以后,摩擦制動器的體積和質(zhì)量都能夠得以縮小,要減輕制動盤的質(zhì)量不需要考慮溫度、應(yīng)力、磨損、變形和耐久性等因素。其次,在這項研究中開發(fā)的例子說明采用輕型固體式制動盤來減輕制動盤的質(zhì)量是可行的。文中還提出一種基于數(shù)學和數(shù)值的分析與之相關(guān)的實驗研究的設(shè)計方法。再生制動和機械制動的協(xié)同制動在電動汽車節(jié)能控制中起著重要的作用?;诓⒙?lián)和串聯(lián)的協(xié)同制動模型,提出了一種基于預(yù)測控制策略的組合模型,得到了較好的協(xié)同制動性能。最大的再生能量回收效率和最佳的制動穩(wěn)定性之間的平衡問題,解決了通過離線過程優(yōu)化流的協(xié)同優(yōu)化算法(合作)。開展流程優(yōu)化流,最佳拉丁超立方體設(shè)計(選擇鏟運機)提出了離散的連續(xù)的設(shè)計空間。為了解決優(yōu)化問題的實時性問題,建立了基于組合模型離線優(yōu)化數(shù)據(jù)的高精度預(yù)測模型,并通過仿真驗證了預(yù)測控制策略。仿真結(jié)果表明,預(yù)測控制策略和組合模型是合理的和有效的。
面對能源和環(huán)境的壓力,發(fā)展電動汽車,實現(xiàn)汽車節(jié)能與能量回收,在國際上已經(jīng)形成了廣泛共識,,它的進一步發(fā)展將會對汽車技術(shù)的發(fā)展產(chǎn)生強大的推動力。