【溫馨提示】壓縮包內(nèi)含CAD圖有下方大圖片預(yù)覽,下拉即可直觀呈現(xiàn)眼前查看、盡收眼底縱觀。打包內(nèi)容里dwg后綴的文件為CAD圖,可編輯,無水印,高清圖,壓縮包內(nèi)文檔可直接點(diǎn)開預(yù)覽,需要原稿請(qǐng)自助充值下載,所見才能所得,請(qǐng)見壓縮包內(nèi)的文件及下方預(yù)覽,請(qǐng)細(xì)心查看有疑問可以咨詢QQ:11970985或197216396
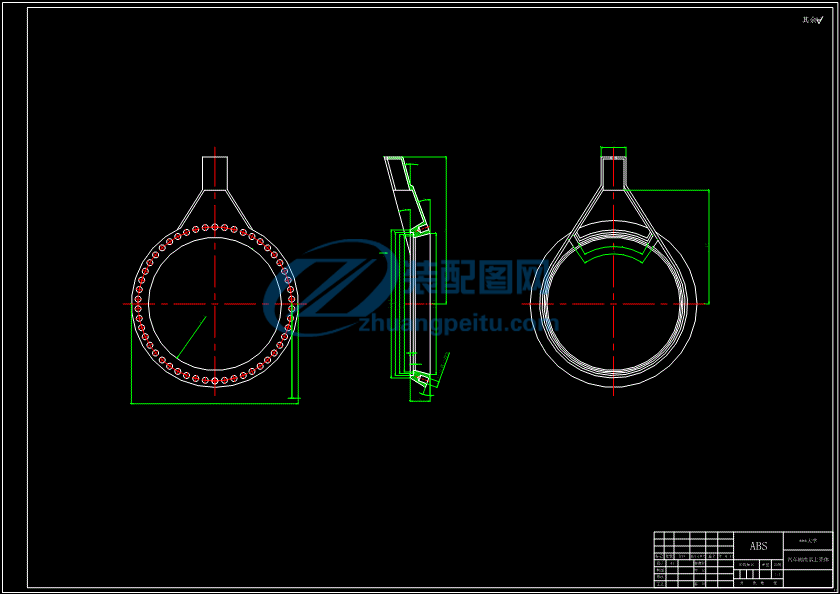
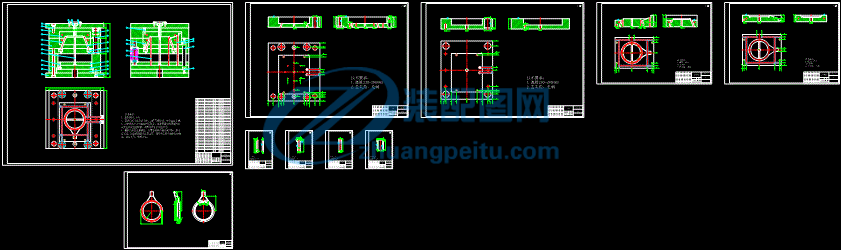
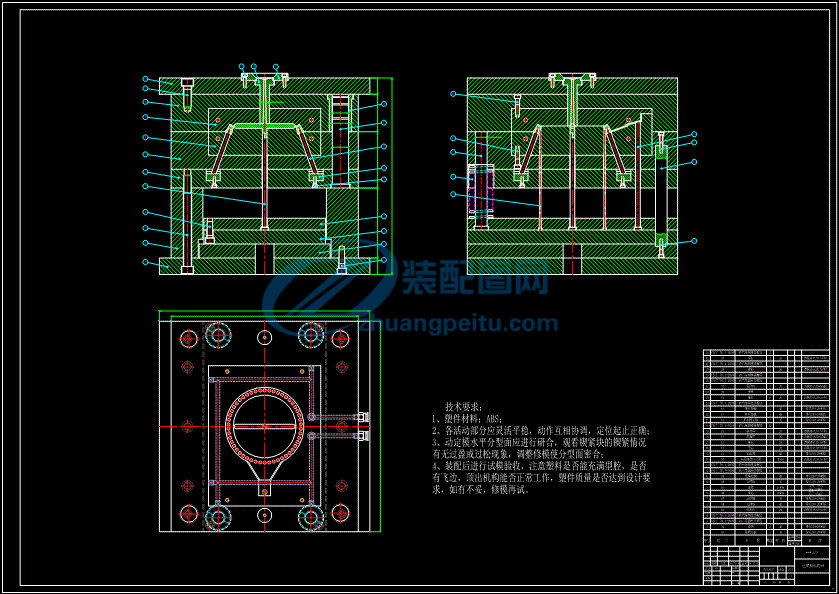
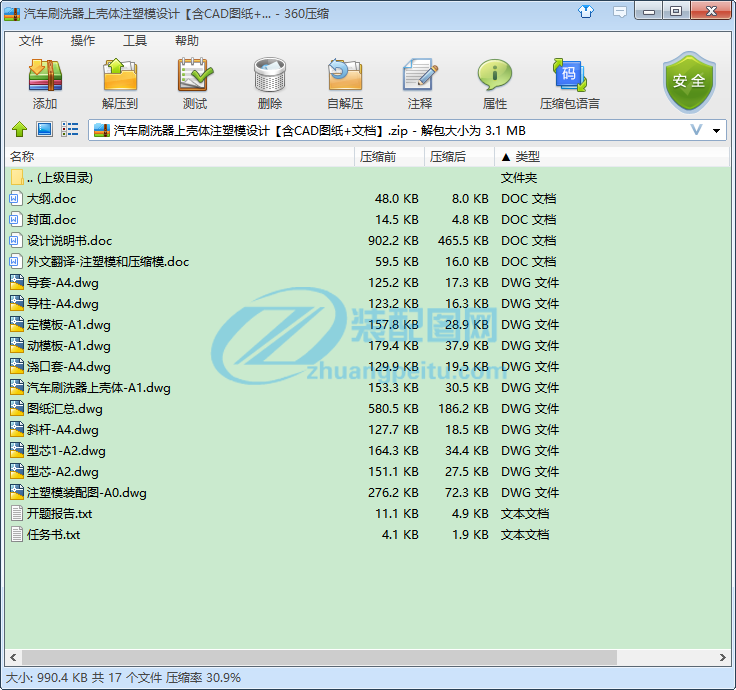
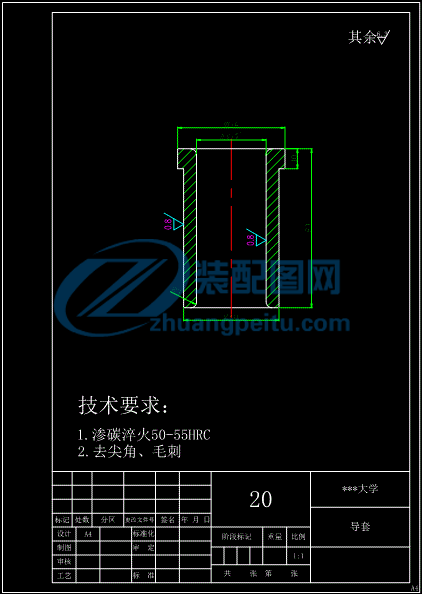
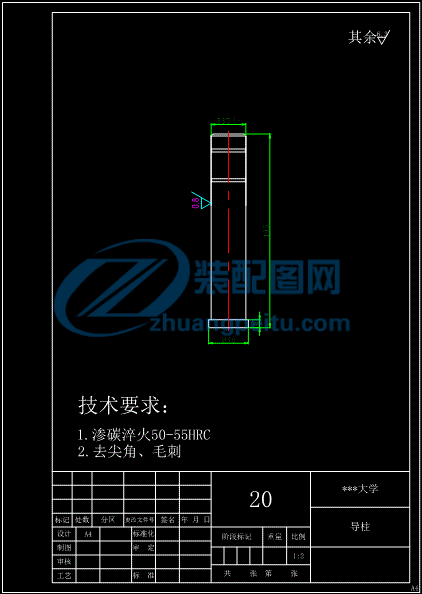
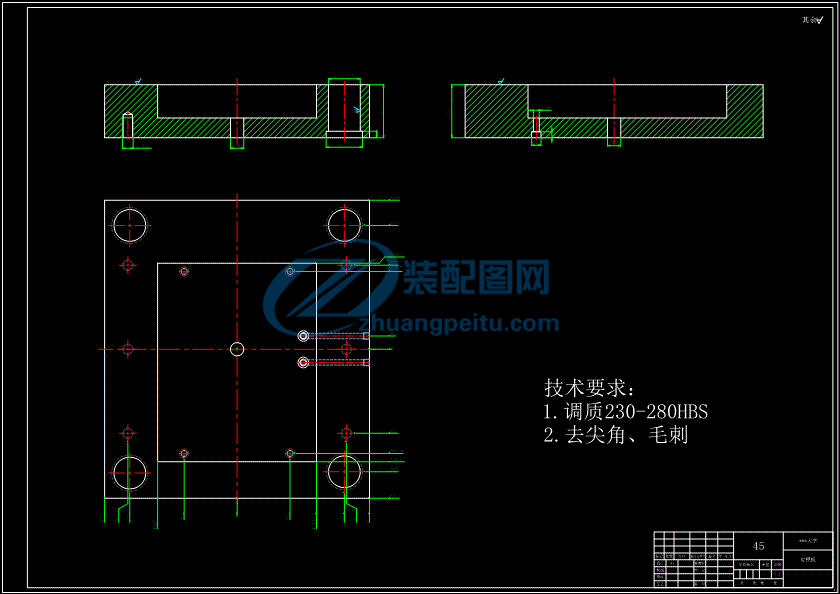
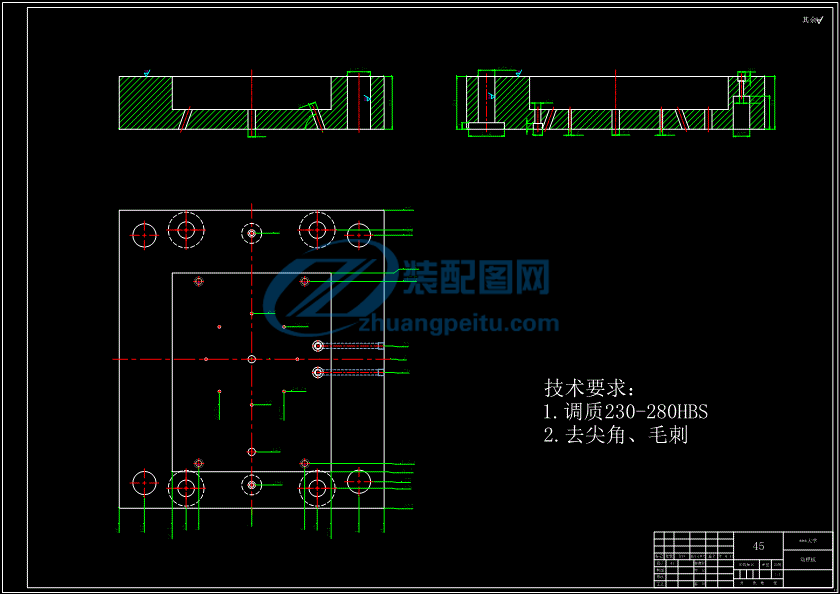
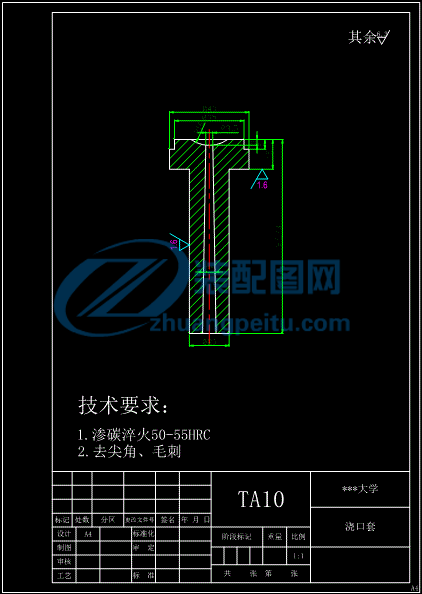
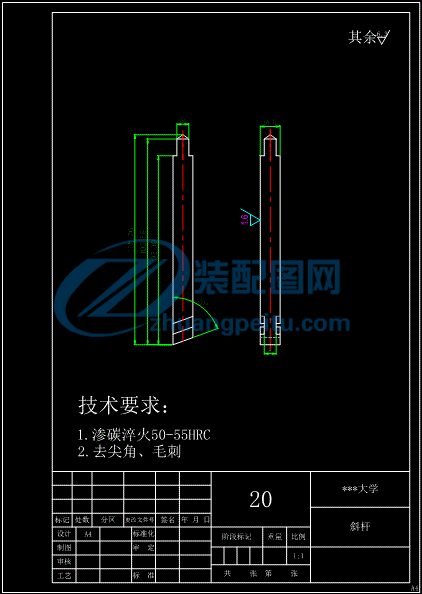
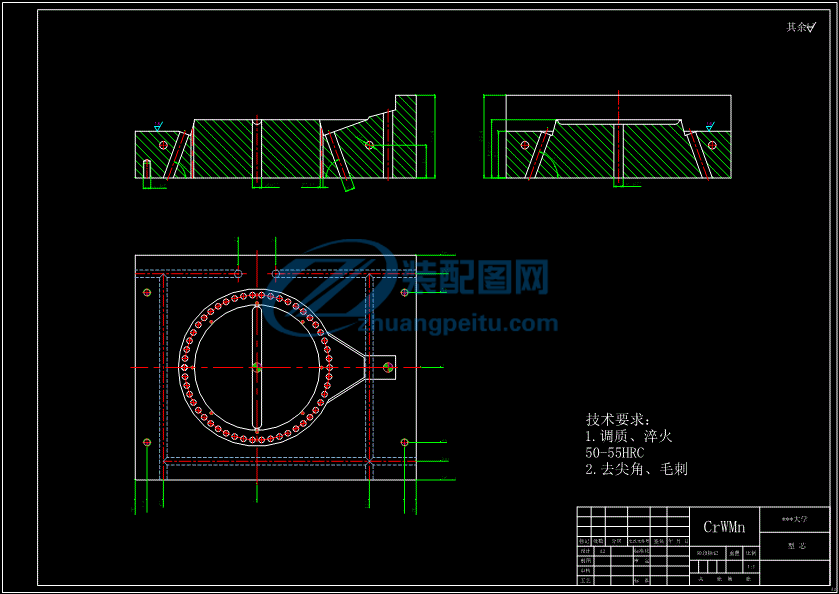
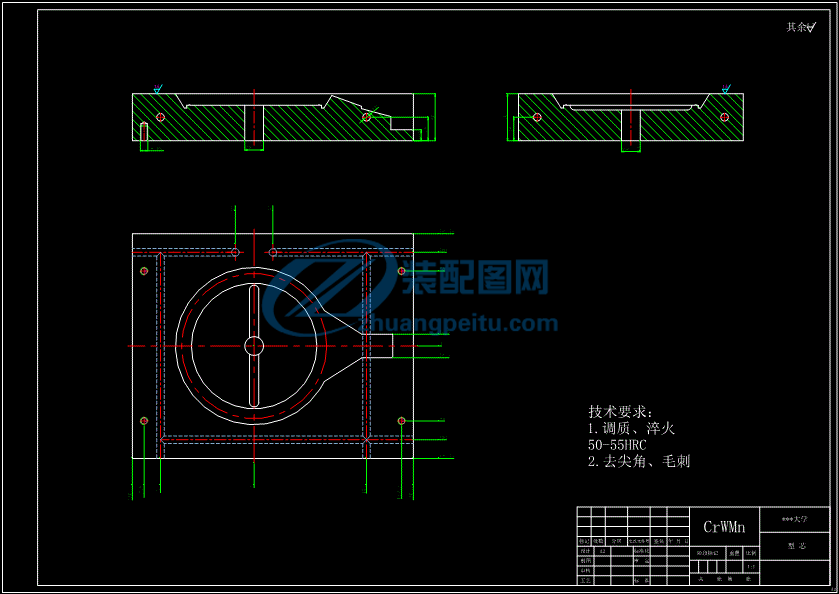
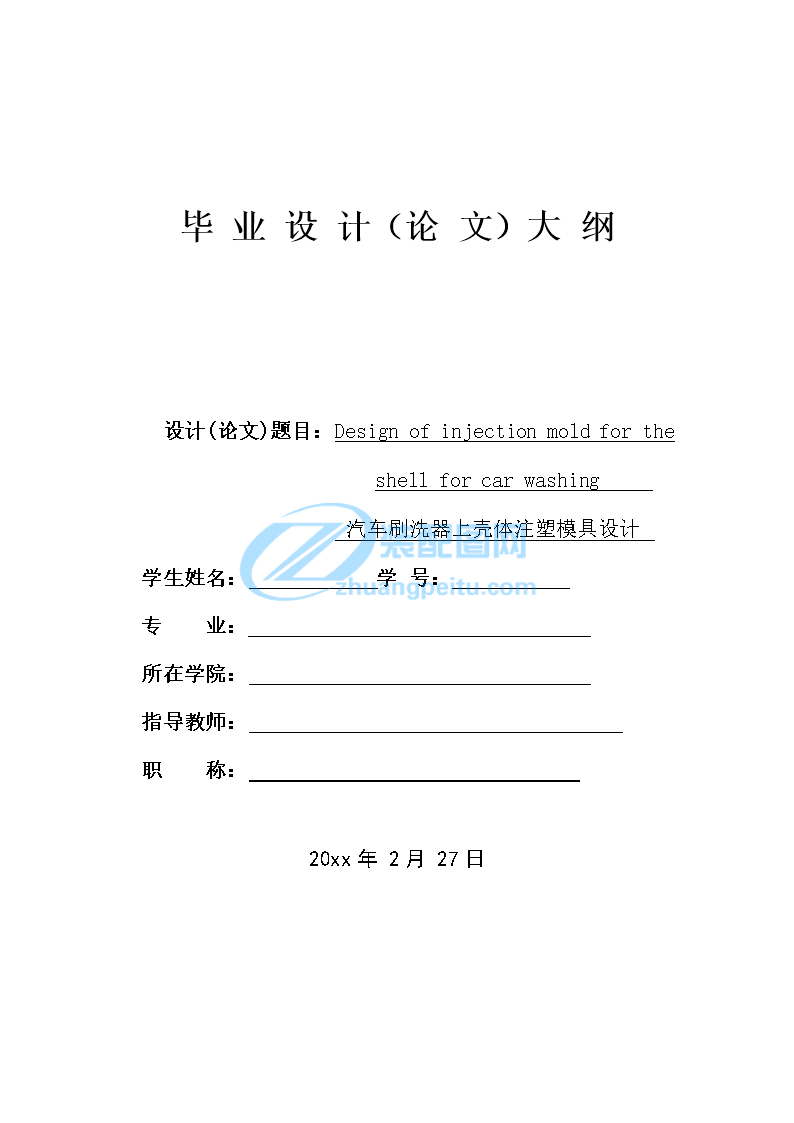
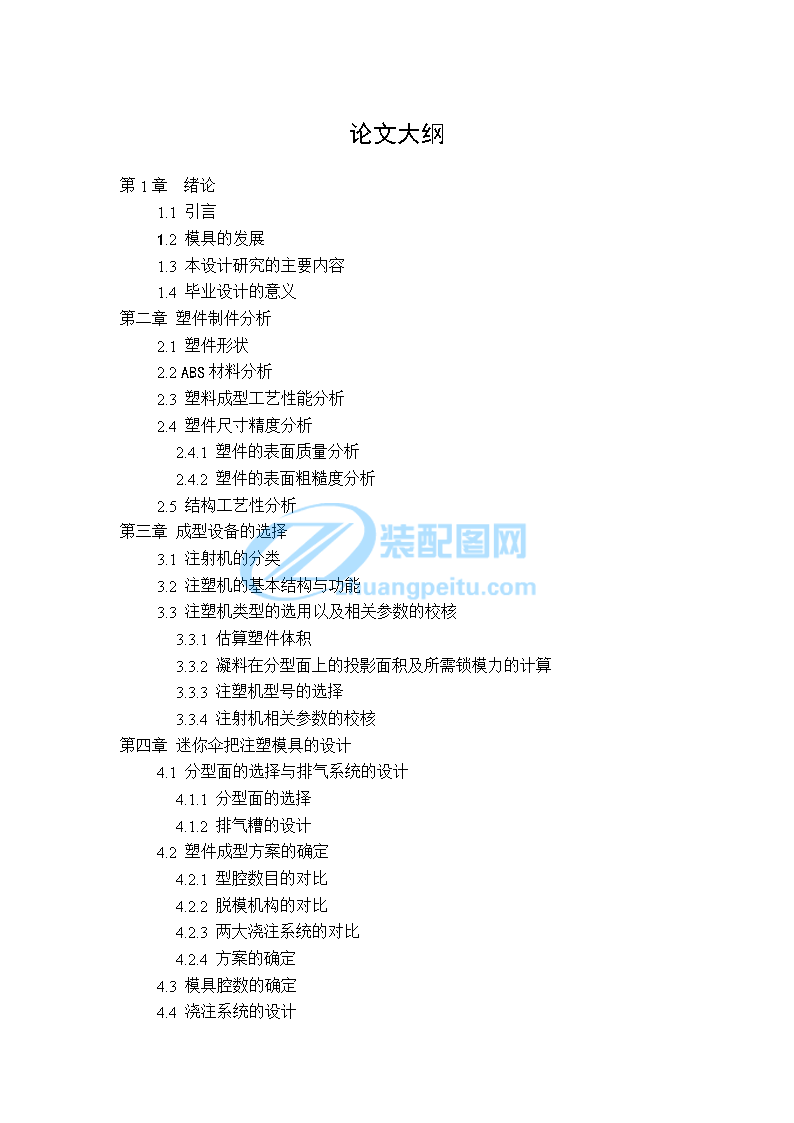

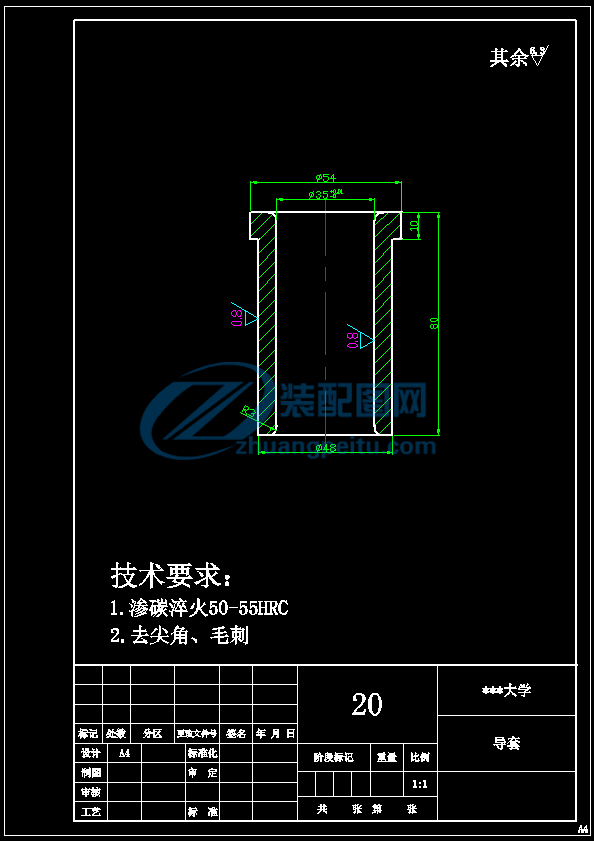
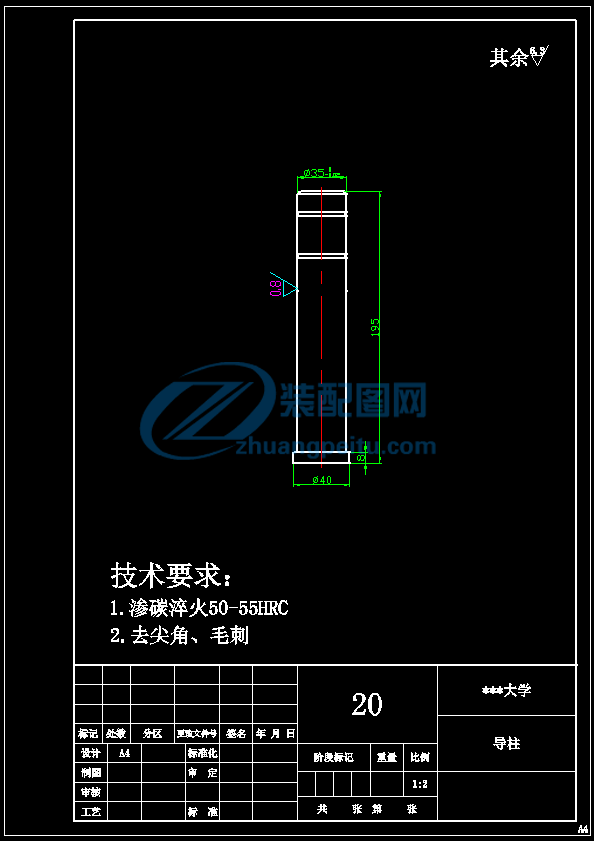
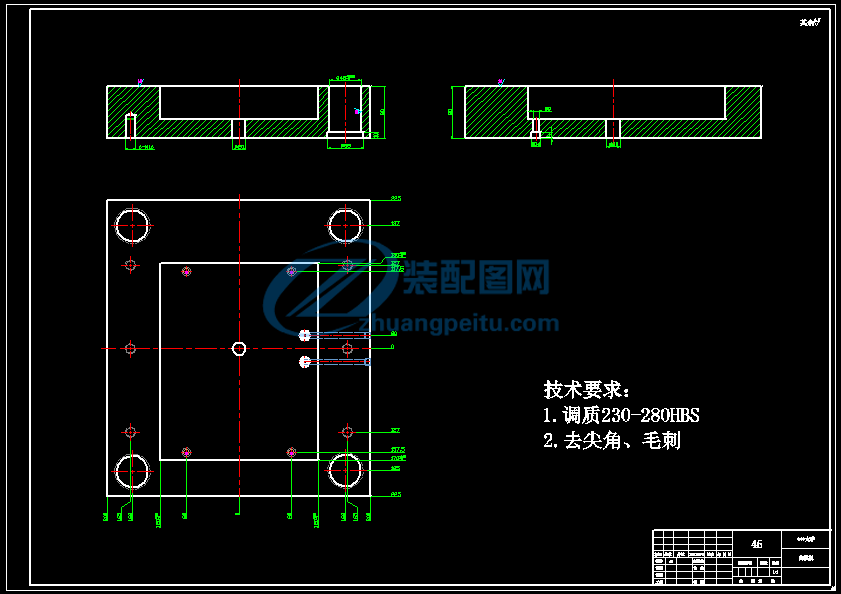
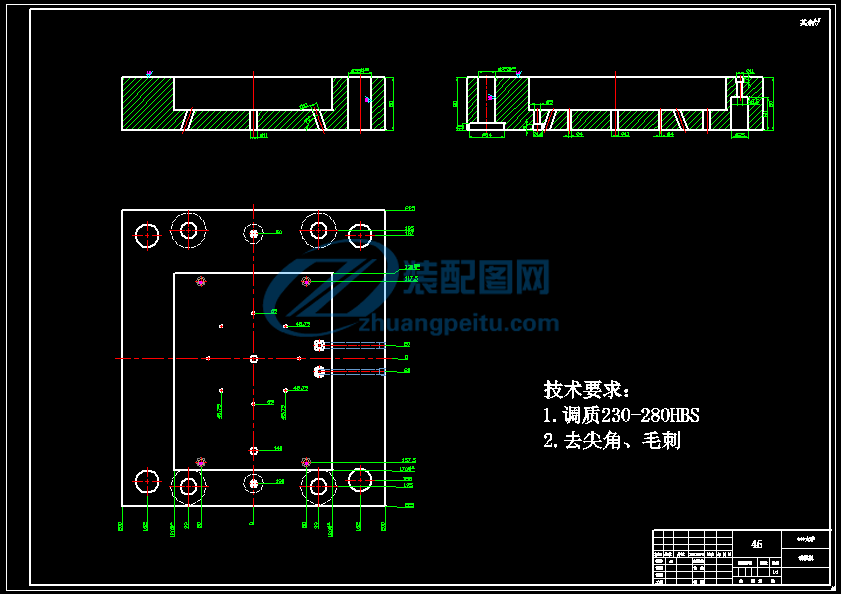
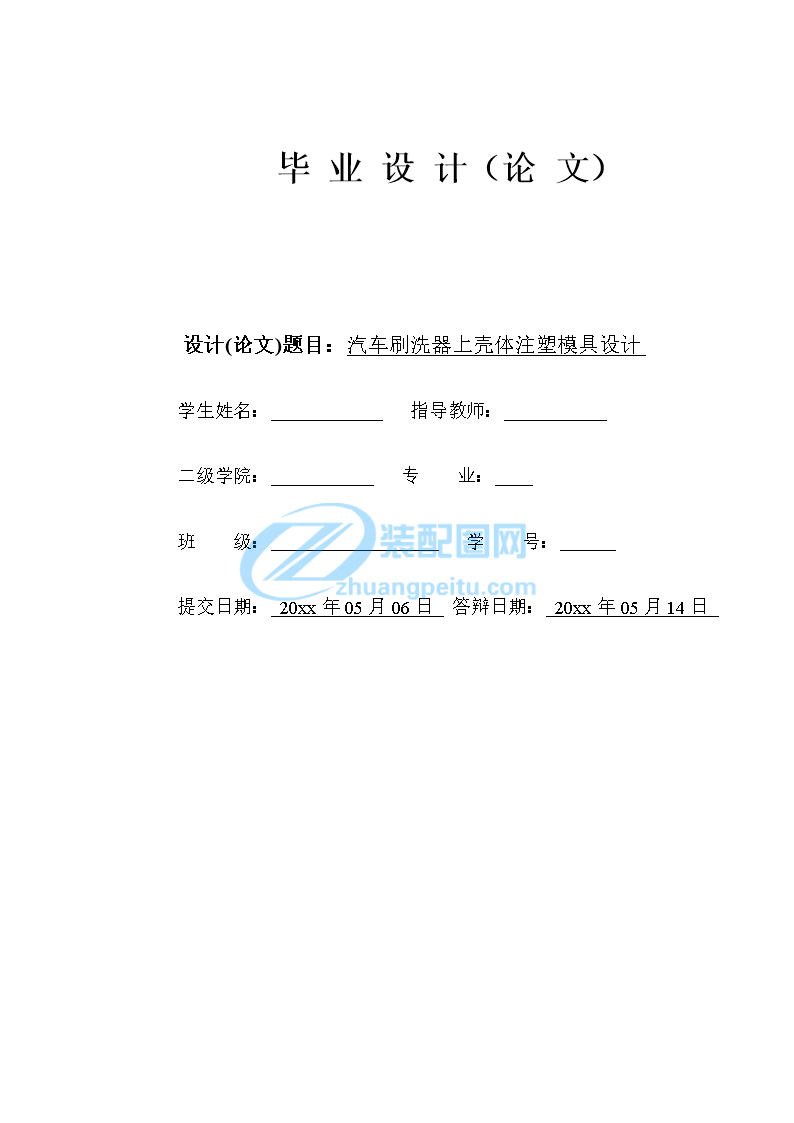
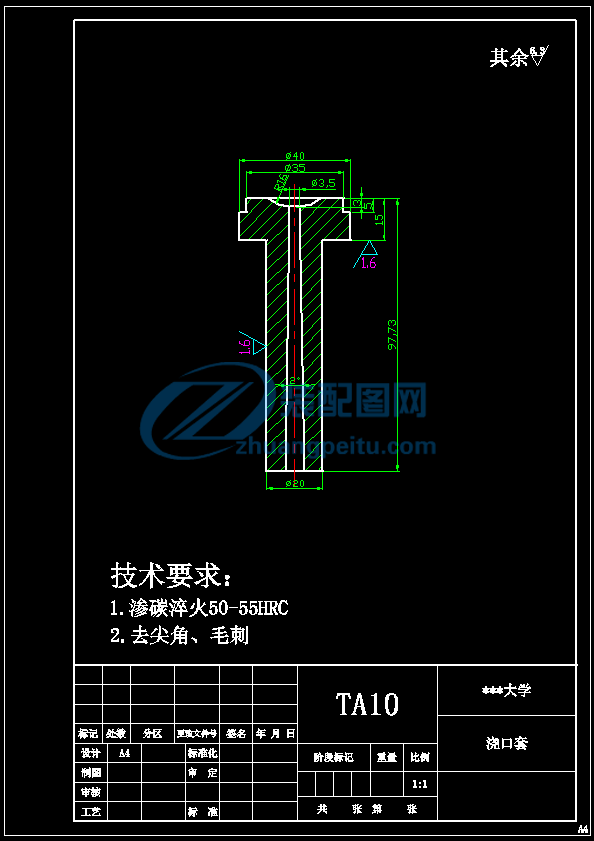
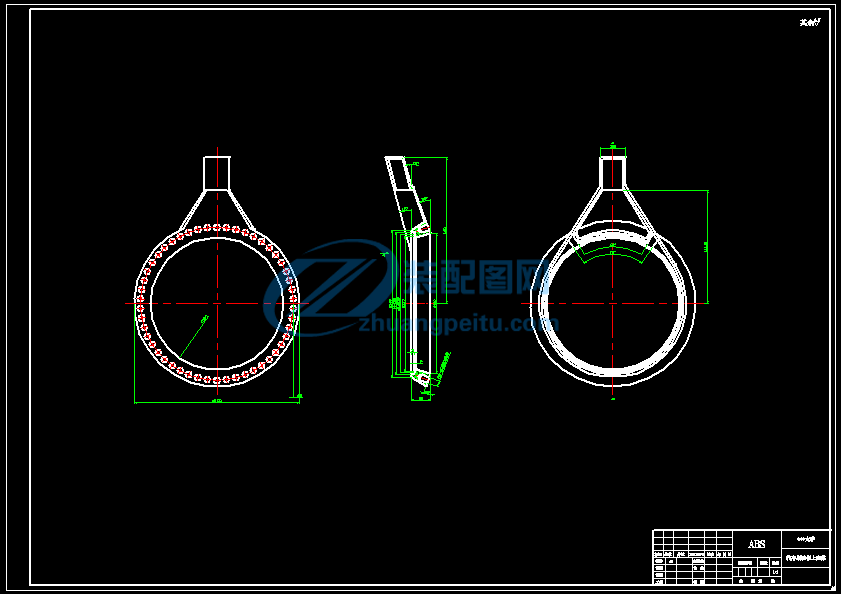
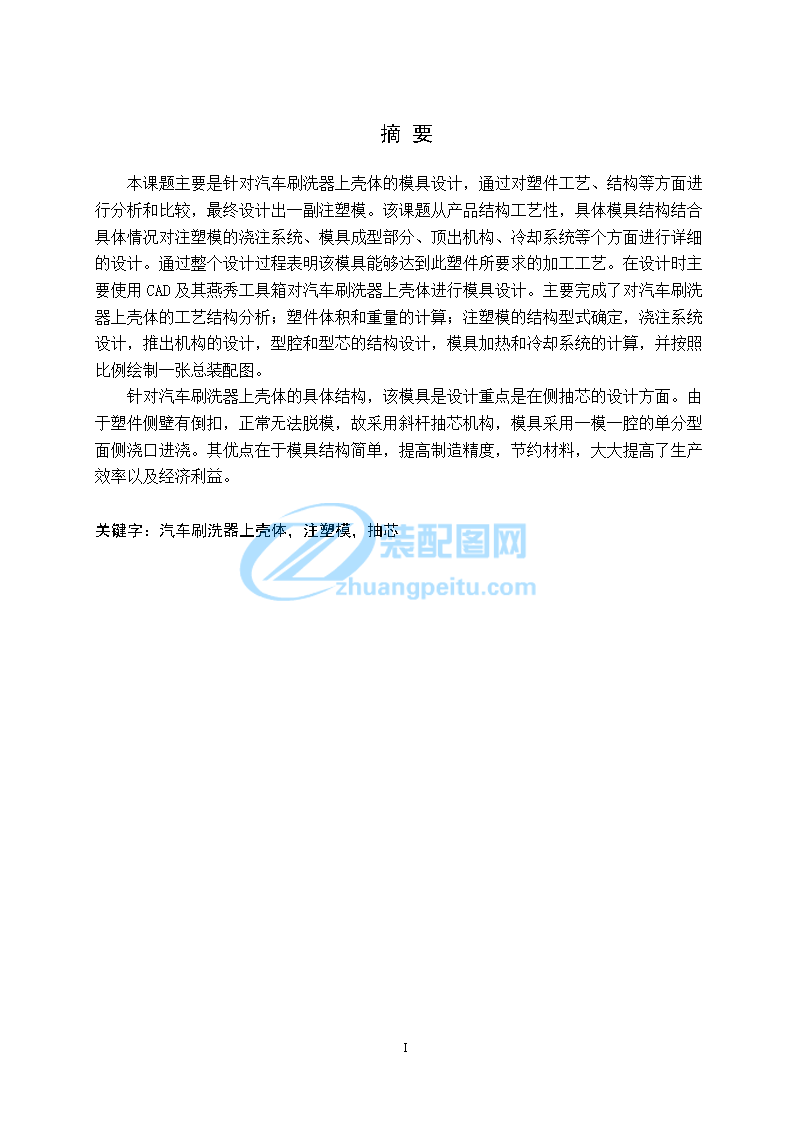
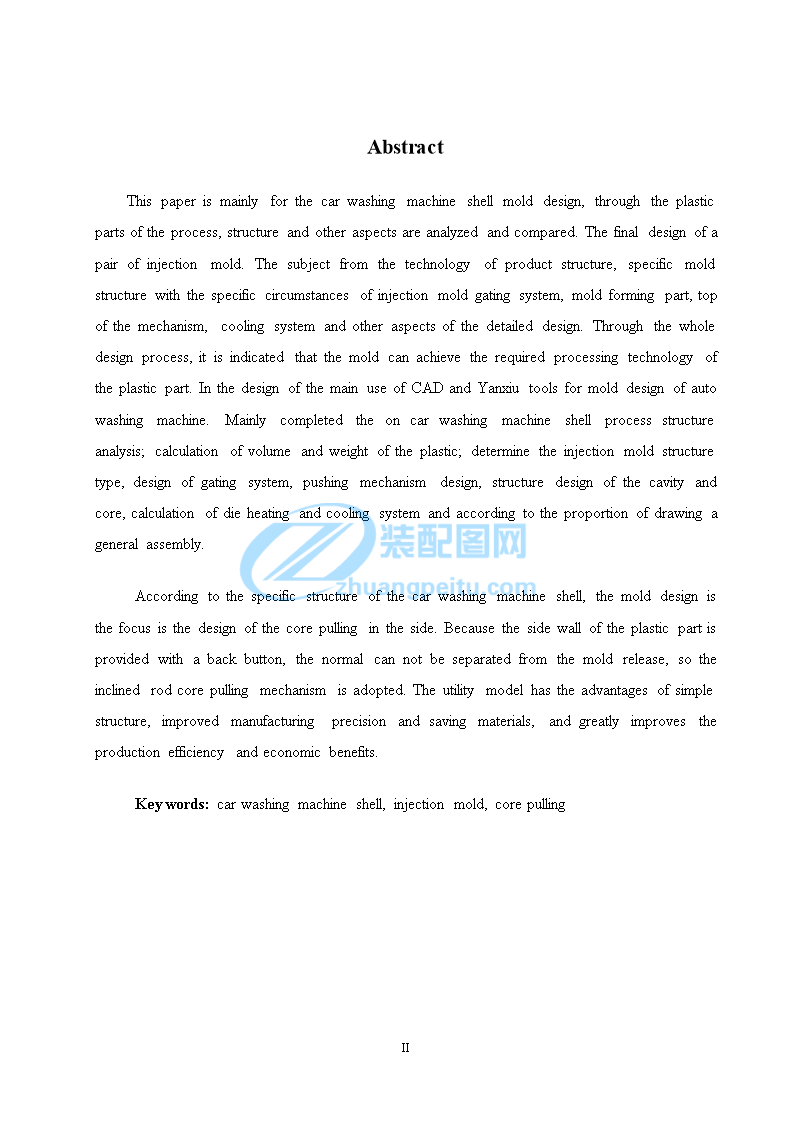
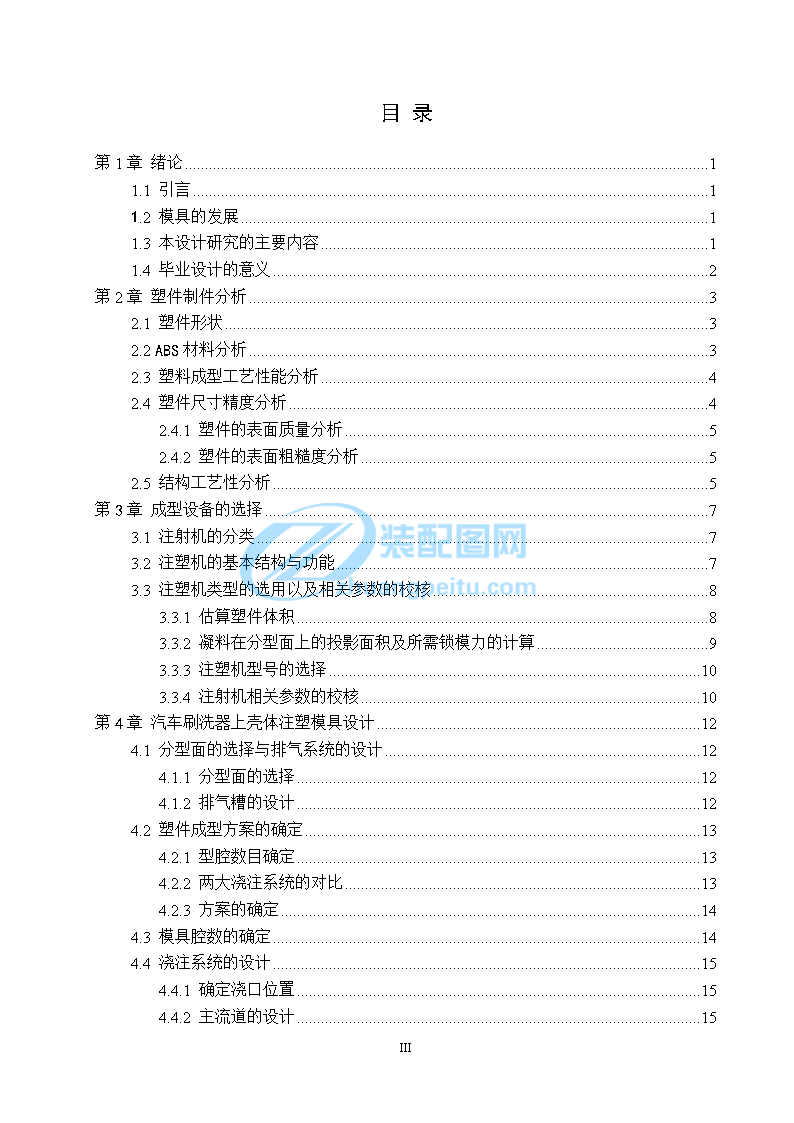
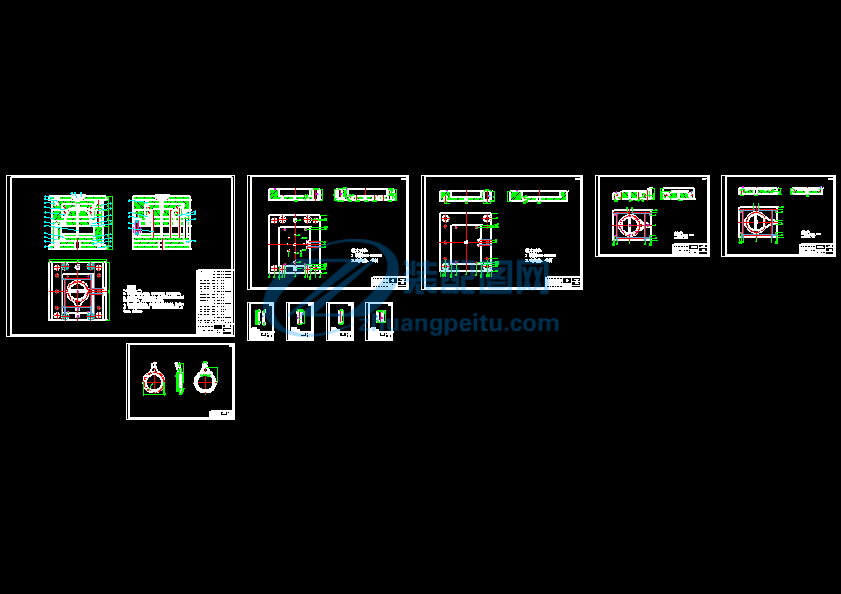
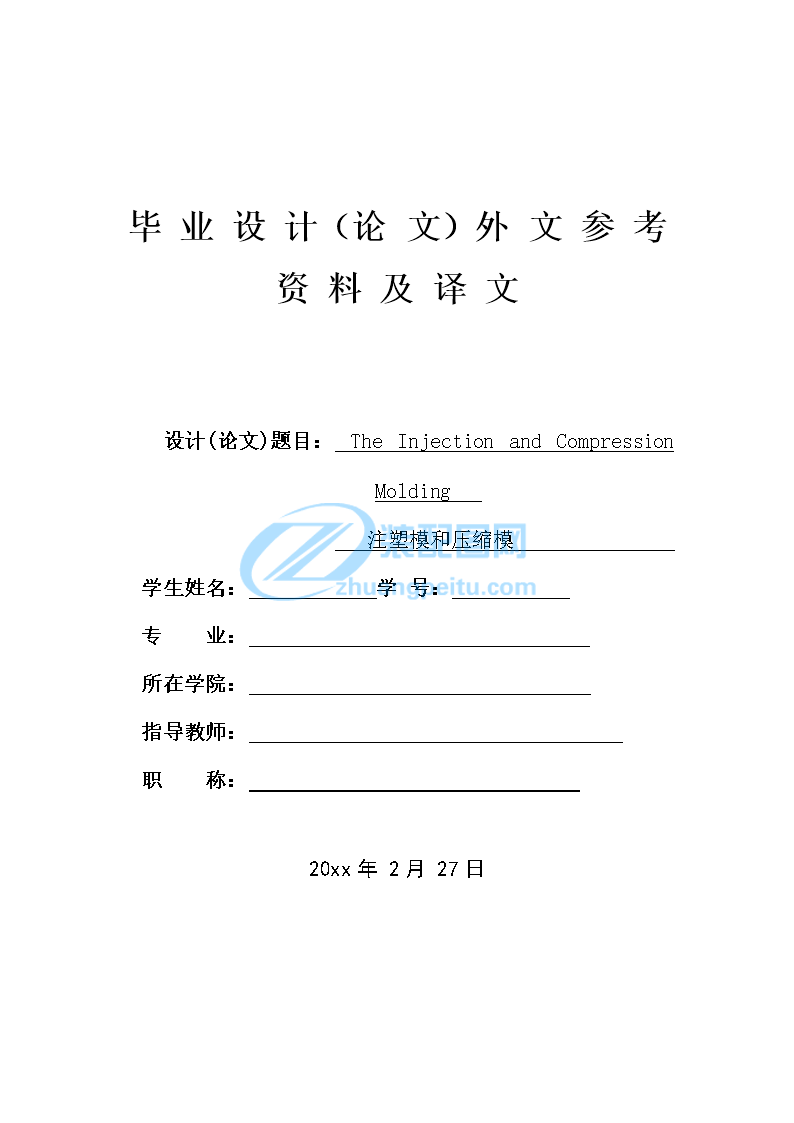
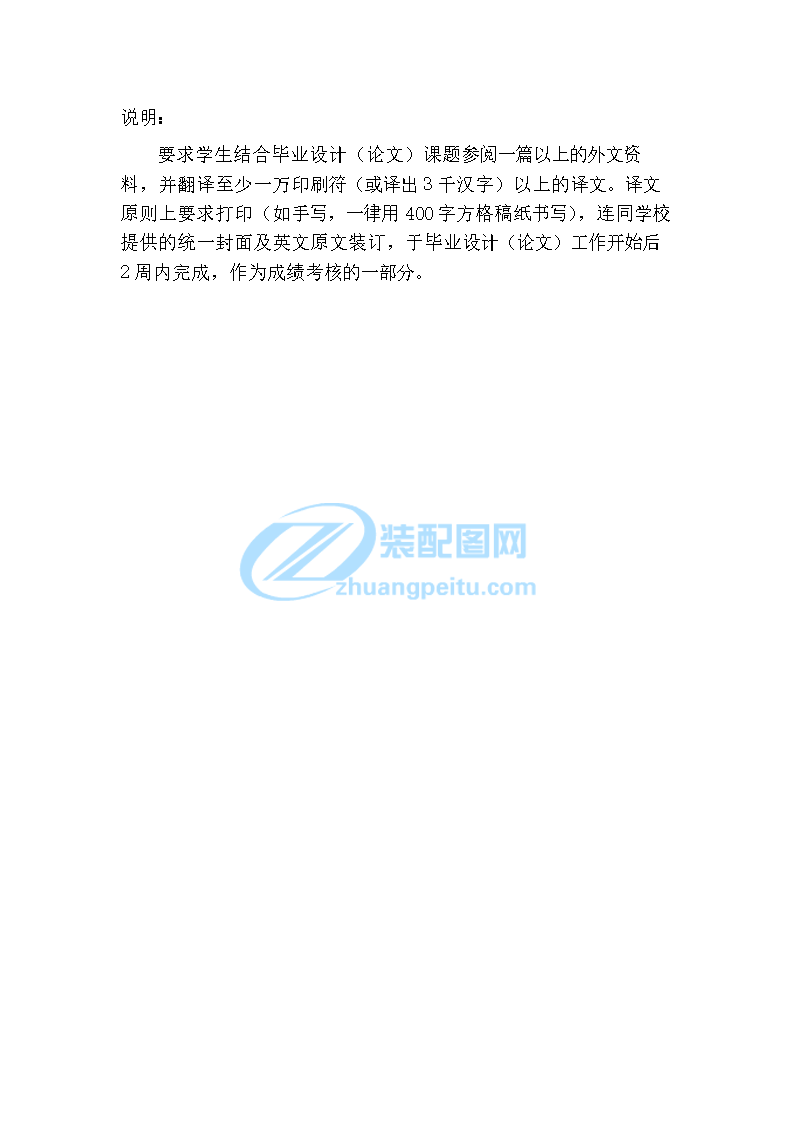
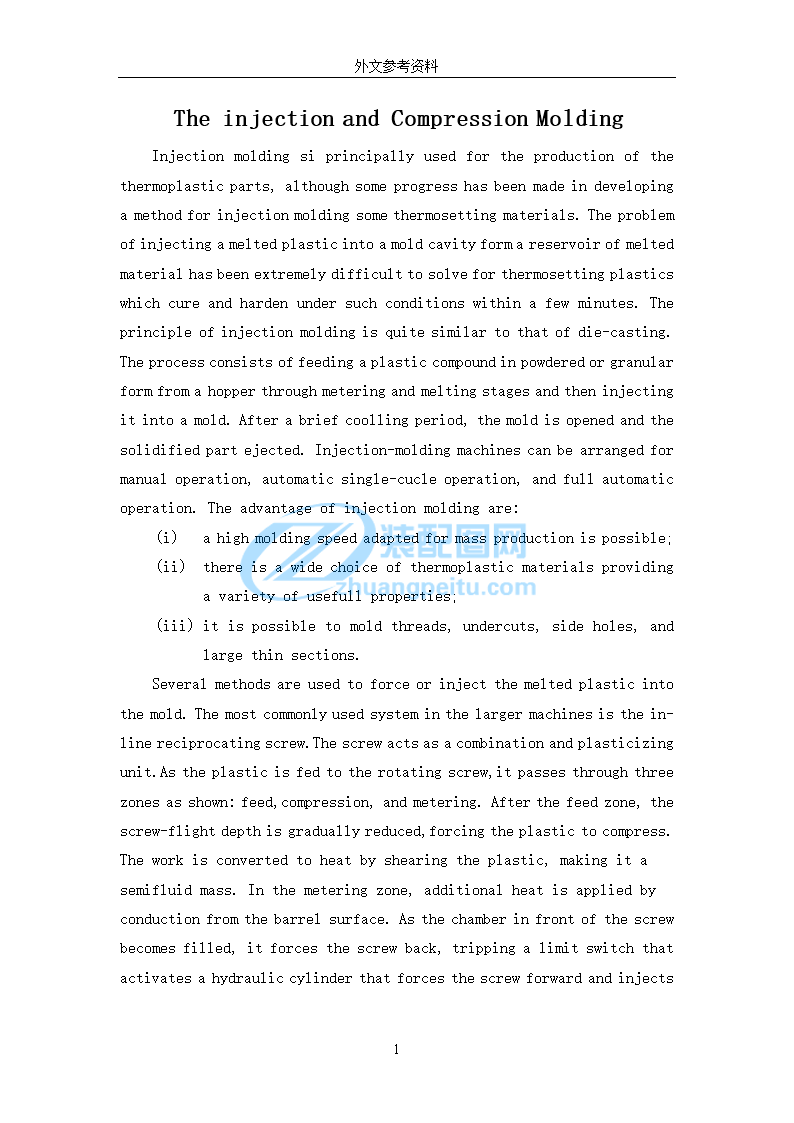
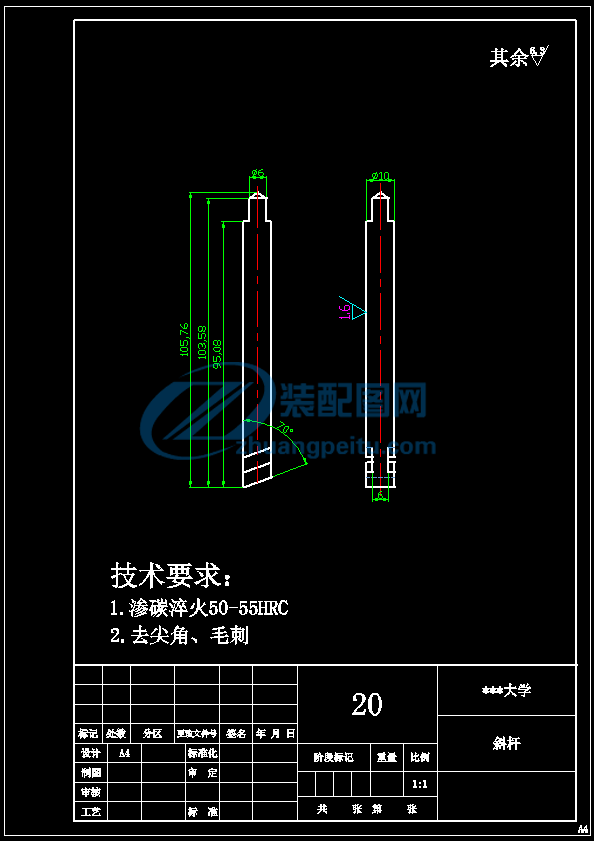
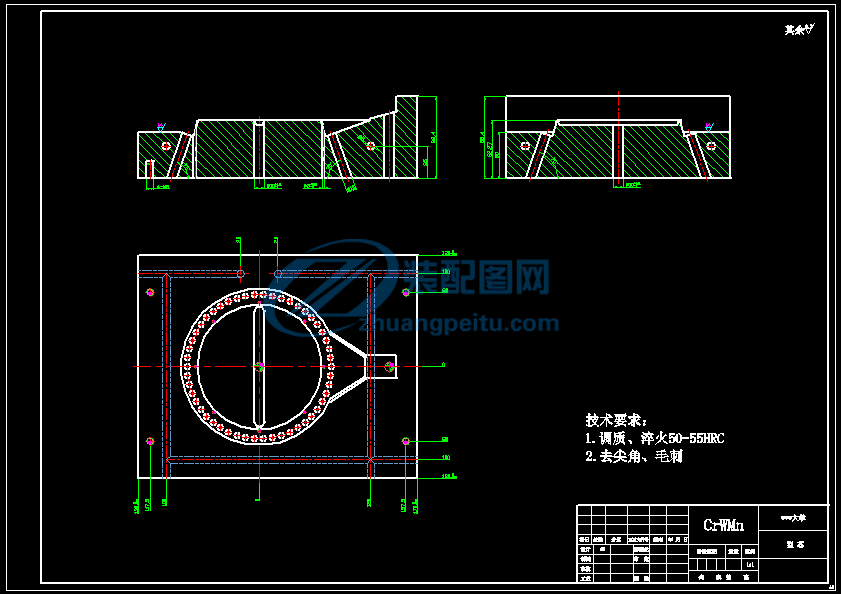
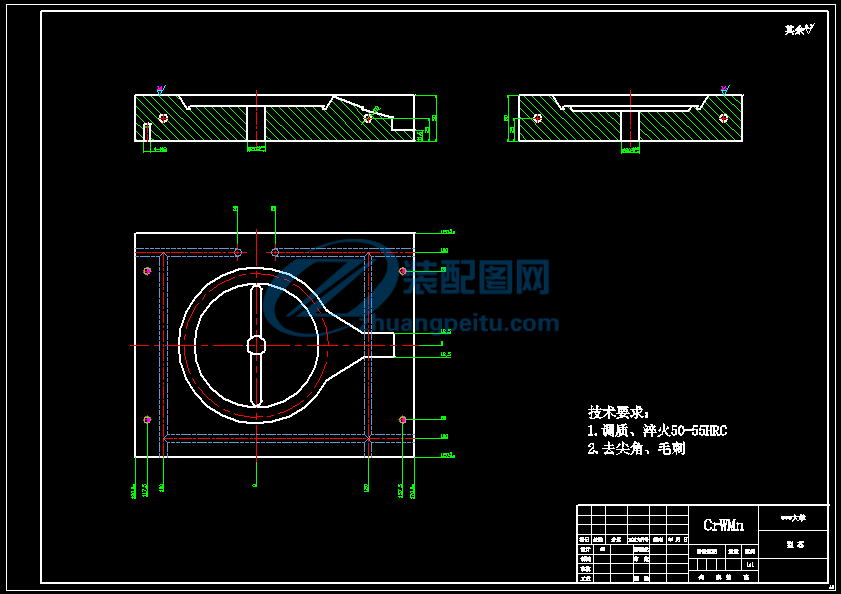
畢 業(yè) 設(shè) 計(jì)(論 文)外 文 參 考 資 料 及 譯 文
設(shè)計(jì)(論文)題目: The Injection and Compression Molding
注塑模和壓縮模
學(xué)生姓名: 學(xué) 號(hào):
專 業(yè):
所在學(xué)院:
指導(dǎo)教師:
職 稱:
20xx年 2月 27日
說明:
要求學(xué)生結(jié)合畢業(yè)設(shè)計(jì)(論文)課題參閱一篇以上的外文資料,并翻譯至少一萬印刷符(或譯出3千漢字)以上的譯文。譯文原則上要求打?。ㄈ缡謱?,一律用400字方格稿紙書寫),連同學(xué)校提供的統(tǒng)一封面及英文原文裝訂,于畢業(yè)設(shè)計(jì)(論文)工作開始后2周內(nèi)完成,作為成績(jī)考核的一部分。
外文參考資料
The injection and Compression Molding
Injection molding si principally used for the production of the thermoplastic parts, although some progress has been made in developing a method for injection molding some thermosetting materials. The problem of injecting a melted plastic into a mold cavity form a reservoir of melted material has been extremely difficult to solve for thermosetting plastics which cure and harden under such conditions within a few minutes. The principle of injection molding is quite similar to that of die-casting. The process consists of feeding a plastic compound in powdered or granular form from a hopper through metering and melting stages and then injecting it into a mold. After a brief coolling period, the mold is opened and the solidified part ejected. Injection-molding machines can be arranged for manual operation, automatic single-cucle operation, and full automatic operation. The advantage of injection molding are:
(i) a high molding speed adapted for mass production is possible;
(ii) there is a wide choice of thermoplastic materials providing a variety of usefull properties;
(iii) it is possible to mold threads, undercuts, side holes, and large thin sections.
Several methods are used to force or inject the melted plastic into the mold. The most commonly used system in the larger machines is the in-line reciprocating screw.The screw acts as a combination and plasticizing unit.As the plastic is fed to the rotating screw,it passes through three zones as shown: feed,compression, and metering. After the feed zone, the screw-flight depth is gradually reduced,forcing the plastic to compress. The work is converted to heat by shearing the plastic, making it a semifluid mass. In the metering zone, additional heat is applied by conduction from the barrel surface. As the chamber in front of the screw becomes filled, it forces the screw back, tripping a limit switch that activates a hydraulic cylinder that forces the screw forward and injects the fluid plastic into the closed mold.An antiflowback valve prevents plastic under pressure from escaping back into the screw flights.
The clamping force that a machine is capable of exerting is part of the size designation and is measured in tons. A rule-of-thumb can be used to determine the tonnage required for a particular job. It is based on two tons of clamp force per square inch of projected area. If the flow pattern is difficult and the parts are thin,this may have to go to three or four tons.
Many reciprocating - screw machines are capable of handing thermosetting plastic materials.Previously these materials were handled by compression or transfer molding.Thermosetting materials cure or polymerize in the mold and are ejected hot in the range of 375℃~410℃.Thermoplastic parts must be allowed to cool in the mold in order to remove them without distortion.Thus thermosetting cycles can be faster.Of course the mold must be heated rather than chilled,as with thermoplastics.
The design plastic injection mold first must have the certain,understanding to the plastic, the plastic principal constituent is a polymer. Like we often said the ABS plastic then is the propylene nitrile, the pyprolylene, the styrene three kind of monomers uses the emulsion, the main body or aerosol gathers the legitimate production,enable it to have three kind of monomers the high performance and may the compression molding, injects under the certain temperature and the pressure to the mold cavity, has the flow distortion, the obtaining cavity shape, after guarantees presses cooling to go against becomes the plastic product. The polymer member assumes the chain shape structure generally, the linear molecule chain and a chain molecule thought is the thermoplastic, may heat up the cooling processing repeatedly, but passes through heats up many members to occur hands over the association response, including forms netted the build molecular structure plastic usually is this, cannot duplicate injects the processing, also is the thermosetting plastics which said.
Since is the chain shape structure, that plastic when processing contracts the direction also is with the polymer molecular chain under the stress function the orientation and the cooling contraction related, must be more than in the flow direction contraction its vertical direction in contraction. The product contraction also with the product shape, the runner, the temperature,guarantees presses factor and so on time and internal stress concerns.In the usual book provides the shrinkage scope is broad, considers is product wall thickness, the structure and the determination casts the temperature pressure size when the practical application and the orientation. The common product if does not have the core strut, the contraction correspondingly wants big. The plastic casts the mold basically to divide into the static mold and to move the mold.
Injection molding is principally used for the production of thermolplastic part ,although some progress has been made in developing a method for injection molding some thermosetting materials .The problem of injecting a melted plastic into a mold cavity from a reservoir of melted material has been extremely difficult to solve for thermosetting plastics which cure and harden under such conditions within a few minutes 。The principle of injection molding is quite similar to that of die-casting . Plastic powder is loaded into the feed hopper and a certain amount feeds into the heating chamber when the plunger draws back . This plastic powder under heat and pressure in the heating chamber becomes a fluid. Heating temperatures range from 265 to 500F . After the mold is closed , the plunger moves forward some of the fluid plastic into the mold cavity under pressures ranging from 12000 to 30000 psi . Since the mold is cooled by circulating cold water , the plastic hardens and the part may be ejected when the plunger draws back and the mold opens .Injection-molding machines can be arranged for manual operation, automatic single-cycle operation , and full automatic operation . Typical machines produce molded parts weighing up to 22 ounces at the rate of four shots per minute , and it is possible on some machines to obtain a rate of six shots per minute . The molds used are similar to the dies of a die-casting machine with the exception that the surfaces are chromium-plated . The advantages of injection molding are :
1. A high molding speed adapted for mass production is possible.
2. There is a wide choice of thermoplastic materials providing a variety of useful properties.
3. It is possible to mold threads , undercuts , side holes ,and large thin sections.
The importance of Injecting the mold are :
⑴、Plastics have the density small, the quality light, the specific tenacity big, the insulating property good, the dielectric loss low, the chemical stability strong, the formation productivity high and the price inexpensive and so on the merits, obtained day by day the widespread application in the national economy and people's daily life each domain, as early as in the beginning of 1990s, the plastic annual output already surpassed the steel and iron and the non-ferrous metal annual output sum total according to the volume computation.In mechanical and electrical (for example so-called black electrical appliances), domains and so on measuring appliance, chemical, the automobile and astronautics aviation, the plastic has become the metal the good substitution material, had the metal material plastic tendency.
⑵、Take the automobile industry as the example , as a result of the automobile lightweight, the low energy consumption development request, the automobile spare part material constitution occurred obviously has modelled the band steel the change, at present our country automobile plastic accounts for 5% which the automobile was self-possessed to 6%, but overseas has reached 13%, forecast according to the expert, the automobile plastic bicycle amount used will also be able further to increase.On modern vehicles, regardless of is outside installs the assorted items, the internal installation assorted items, the function and the structural element, all may use the plastic material, outside installs the assorted items to have the bumper, the fender, the wheel hub cap, the air deflector and so on; After the internal installation assorted items have in the display board, the vehicle door the board, the vice-display board, the sundry goods box lid, the chair, the guard shield and so on; The function and the structural element have the fuel tank, the radiator header, the spatial filter hood, the fan blade and so on.Statistics have indicated, our country in 2000 automobile output more than 200 ten thousand, the vehicle amounted to 1,380,000 tons with the plastic.Looked from the domestic and foreign automobile plastic application situation that, the automobile plastic amount used already became one of weight automobile production technical level symbols.
⑶、Injection of a molding formation as plastic workpiece most effective formation methods because may by one time take shape each kind of structure complex, the size precise and has the metal to inlay a product, and the formation cycle is short, may by mold multi-cavities, the productivity be high, when mass productions the cost isvery inexpensive, easy to realize the automated production, therefore holds the extremely important status in the plastic processing profession.Statistics have indicated, plastic mold composition all molds (including metal pattern) 38.2%, the plastic product gross weight about 32% is uses in injecting the formation, 80% above engineering plastics product all must use the injection formation way production. 4. counts according to the customs, our country in 2000 altogether imported mold 977,000,000 US dollars, in which plastic molding forms altogether 550,000,000 US dollars, occupied for 56.3%,2001 years altogether to import mold 1,112,000,000 US dollars, in which plastic molding forms altogether 616,000,000 US dollars, accounted for 55.4%.From the variety, the import volume biggest is the plastic molding forms.
⑷、Counts according to the customs, our country in 2000 altogether imported mold 977,000,000 US dollars, in which plastic molding forms altogether 550,000,000 US dollars, occupied for 56.3%, 2001 years altogether to import mold 1,112,000,000 US dollars, in which plastic molding forms altogether 616,000,000 US dollars, accounted for 55.4%.From the variety, the import volume biggest is the plastic molding forms.
In compression molding the palstic material as powder or preforms is placed into a heated steel mold cavity,Since the parting surface is in a horizontal plane ,the upper half of the mold descends vertically.It closes the mold cavity and pressures for a predetermined period.A pressure of from 2 to 3 tons square inch and a temperaure at approximately 350F converts the plastic to a semiliquid which flows to all parts of the mold cavity.Usually from 1 to 15 minutes is required for curing,altough a recently developed alkyd plastic will cure in less than 25 secends. The mold is then opended and the molded part removed.If metal insers are desired in the parts,they should be placed in the mold cavity on pins or in the holes before the plastic is loaded.Also, the preforms should be preheated before loading into the mold cavity to eliminate gases,inprove flow,and decrease curing time.Dieletric heating is a convenient method of heating the preforms.
Since the plastic material is placed directly into the mold cavity,the mold itself can be simpler than those used for other molding precesses.Gates and sprues are unnecessary.This also results in a saving in material,because trimmed-off gates and sprues would be a complete loss of the thermosetting plastic.The press require the full attention of one operator.However,several smaller presses can be operated by one operator. The presses are conveniently located so the operator can easilymove from one to the next.By the time he gets around to a particular press again,that mold will be ready to open.the thermosetting plastics which harden under heat and pressure are suitable for compression molding and transfer molding.It is not practical to moid shermoplastic materials by these methods,since the molds would have to be alternately heated and cooled.In order to harden and eject thermoplastic parts form the mold,cooling would be necessary.
Types of molds for compression molding.The molds used for compression molding are classified into four basic types, namely ,positive molds,landed positive mold,flash-type molds,and semipositive molds.In a positive mold the plunger on the upper mold enters the lower mold cavity.since there are no lands or stops on the lower die ,the plunger completely trap the plastic material and descends with full pressure on the charge.A dense part with good electrical and physical properties is produced.The amount of plastic placed in the die cavity must be accurately measured,since it determines the thickness of the part .A landed positive mold is similar to a positive mold except that lands are added to stop the travel of the plunger at predetermined point.In this case,the lands absorb some of the pressure that should be exerted on the parts.The thickness of the parts will be accurately controlled,but the density may vary cansideraby.In a flash-type mold,flash redges are added ti the top and bottom molds.As the upper mold exerts pressure on the plastic,excess material is forced out between the flash ridges where it forms flash.This flash is further compressed.becomes hardened,and finally stops the downard thavel of the upper mold.A slight excess of the plastic material is always chared to ensure sufficient pressurs to produce a dense molded part.This type of mold is widely used because it is comparatively easy to construct and it controls thickness and density within colse limits.The semipositive mold is a combination od the flash type and landed posive molds.In addition to the flash ridges,a land is employed to restrict the travel of the upper mold.
12
譯 文
注塑模和壓縮模
盡管成型某些熱固性材料的方法取得了一定進(jìn)步,但注塑模主要(還是)用來生產(chǎn)熱塑性塑件(這主要是因?yàn)椋峁绦运芰先垠w的過程中,也會(huì)出現(xiàn)這種情況,這個(gè)問題一直非常難解決。住宿成型要換里和鑄造十分相似。住宿成型的工藝過程包括:首先把料斗中的粉狀或粒狀的塑料混合物依次輸送到定量去和熔化區(qū),然后再注射到模具型腔中,經(jīng)過短時(shí)冷卻后,開模,推出成型塑件。注塑機(jī)分為手動(dòng),半自動(dòng)及全自動(dòng)操作。住宿模具有以下優(yōu)點(diǎn):
(i) 較高的成型速度使大批量生產(chǎn)成為可能;
(ii) 為成形具有不同使用性能的熱塑性材料提供了較寬的選擇;
(iii) 可成型帶有螺紋的塑件、側(cè)向凹陷的塑件、帶有側(cè)孔的塑件和較大的薄壁件。
熔融塑料注入模具中通常有幾種方式。在大型注塑機(jī)上采用往復(fù)螺桿式的注入方式。螺桿同時(shí)具有注射和塑化的功能。樹脂原料進(jìn)入旋轉(zhuǎn)的螺桿時(shí),要經(jīng)過三個(gè)區(qū)域:喂入?yún)^(qū)、壓實(shí)區(qū)和塑化區(qū)經(jīng)過喂入?yún)^(qū)后,為壓實(shí)樹脂原料,螺桿螺旋部分的深度逐漸降低,同時(shí)傳遞樹脂原料間因剪切作用而產(chǎn)生的熱量,使原料呈現(xiàn)半流動(dòng)狀態(tài)。在計(jì)量區(qū),螺缸表面的加熱裝置對(duì)熔體進(jìn)一步加熱。當(dāng)熔體充滿螺桿前部區(qū)域時(shí),螺桿在熔體壓力的作用下后退,觸動(dòng)限位開關(guān)使液壓缸工作,在液壓力的作用下推動(dòng)螺桿向前運(yùn)動(dòng),將熔融塑料注射到閉合的模具型腔中。防倒流閥能夠阻止受壓熔體倒流進(jìn)螺桿的螺旋區(qū)。
注塑機(jī)的鎖模系統(tǒng)所提供的鎖模力由(塑件在分型面的投影)尺寸決定,鎖模力以噸為單位。通常靠經(jīng)驗(yàn)來決定塑件所需要的鎖模力總噸數(shù),一般在塑件投影面積上每平方英寸需要作用兩噸鎖模力。如果熔體流動(dòng)困難或塑件較薄,鎖模力應(yīng)提高到三到四噸。
許多螺桿式注塑機(jī)能生產(chǎn)熱固性塑料。以前,熱固性塑料由擠出模具或傳遞模具生產(chǎn)。熱固性塑料熔體在模具內(nèi)固化或發(fā)生聚合反應(yīng),并在溫度為375℃~410℃范圍內(nèi)推出熱塑性塑料熔體必須在模具冷卻成型,以保證推出時(shí)不發(fā)生變形。這種熱硬化性循環(huán)速度很快。當(dāng)然,生產(chǎn)熱塑性塑件時(shí),模具必須被加熱,而不是冷卻。
設(shè)計(jì)塑料注射模具首先要對(duì)塑料有一定的了解,塑料的主要成分是聚合物。如我們常說的ABS 塑料便是丙烯腈、丁二烯、苯乙烯三種單體采用乳液、本體或懸浮聚合法生產(chǎn),使其具有三種單體的優(yōu)越性能和可模塑性,在一定的溫度和壓力下注射到模具型腔,產(chǎn)生流動(dòng)變形,獲得型腔形狀,保壓冷卻后頂出成塑料產(chǎn)品。聚合物的分子一般呈鏈狀結(jié)構(gòu),線型分子鏈和支鏈型分子認(rèn)為是熱塑性塑料,可反復(fù)加熱冷卻加工,而經(jīng)過加熱多個(gè)分子發(fā)生交聯(lián)反應(yīng),連結(jié)成網(wǎng)狀的體型分子結(jié)構(gòu)的塑料通常是一此次性的,不能重復(fù)注射加工,也就是所說的熱固性塑料。
既然是鏈狀結(jié)構(gòu),那塑料的在加工時(shí)收縮的方向也是跟聚合物的分子鏈在應(yīng)力作用下取向性及冷卻收縮有關(guān),在流動(dòng)方向上的收縮要比其垂直方向上的收縮多。產(chǎn)品收縮也同制品的形狀、澆口、熱脹冷縮、溫度、保壓時(shí)間及內(nèi)應(yīng)力等因素有關(guān)。通常書上提供的收縮率范圍較廣,在實(shí)際應(yīng)用中所考慮的是產(chǎn)品的壁厚、結(jié)構(gòu)及確定注塑時(shí)溫度壓力的大小和取向性。 一般產(chǎn)品如果沒有芯子支撐,收縮相應(yīng)要大些。 塑料注塑模具基本分為靜模和動(dòng)模。
注射模主要是用來生產(chǎn)熱塑性的零件,盡管有些工藝已經(jīng)發(fā)展為可以用注射模來生產(chǎn)熱固性材料的零件。在從一個(gè)熔化的熔料箱中把熔料注入型腔中,是相當(dāng)難解決在這種情況下熱固性塑料在幾分鐘內(nèi)凝固的問題。注射模的工作原理跟鍛造模十分相似。當(dāng)柱塞向后拉時(shí),塑料粉末被載入加料斗,還有一定數(shù)量的塑料進(jìn)入了加熱腔。塑料粉末在加熱腔中受到熱力和壓力的作用下熔化。加熱的溫度范圍在265~500華氏度之間。壓力在12000~30000PMa之間作用下,柱塞向前移動(dòng),把熔化的塑料注入模具的型腔中。由于模具被流通的冷水冷卻,塑料凝固成型,當(dāng)柱塞向后拉出和開模,塑件脫模。注射機(jī)可以設(shè)計(jì)為人工、斗自動(dòng)、全自動(dòng)操作。以每分鐘注射四次的速率,典型注射機(jī)生產(chǎn)的塑件可重達(dá)22盎司,某些注射機(jī)可達(dá)到每分鐘注射六次。除了表面電鍍外, 這類模具的用途與鑄造模相似。注射模的優(yōu)點(diǎn)是:1、 高速注射模適用于大批量生產(chǎn)是可能的;2、 熱塑性材料的廣泛選擇產(chǎn)生了各種有用的特性。3、 螺紋模具,飛邊,側(cè)孔大的薄壁結(jié)構(gòu)的應(yīng)用成為可能。
注塑模重要性有:
⑴、塑料具有密度小、質(zhì)量輕、比強(qiáng)度大、絕緣性好、介電損耗低、化學(xué)穩(wěn)定性強(qiáng)、成型生產(chǎn)率高和價(jià)格低廉等優(yōu)點(diǎn),在國(guó)民經(jīng)濟(jì)和人民日常生活的各個(gè)領(lǐng)域得到了日益廣泛的應(yīng)用,早在二十世紀(jì)九十年代初,塑料的年產(chǎn)量按體積計(jì)算已經(jīng)超過鋼鐵和有色金屬年產(chǎn)量的總和。在機(jī)電(如所謂的黑色家電)、儀表、化工、汽車和航天航空等領(lǐng)域,塑料已成為金屬的良好代用材料,出現(xiàn)了金屬材料塑料⑵、以汽車工業(yè)為例,由于汽車輕量化、低能耗的發(fā)展要求,汽車零部件的材料構(gòu)成發(fā)生了明顯的以塑代鋼的變化,目前我國(guó)汽車塑料占汽車自重的5%至6%,而國(guó)外已達(dá)13%,根據(jù)專家預(yù)測(cè),汽車塑料的單車用量還將會(huì)進(jìn)一步增加。在現(xiàn)代車輛上,無論是外裝飾件、內(nèi)裝飾件,還是功能與結(jié)構(gòu)件,都可以采用塑料材料,外裝飾件有保險(xiǎn)杠、擋泥板、車輪罩、導(dǎo)流板等;內(nèi)裝飾件有儀表板、車門內(nèi)板、副儀表板、雜物箱蓋、座椅、后護(hù)板等;功能與結(jié)構(gòu)件有油箱、散熱器水室、空濾器罩、風(fēng)扇葉片等。據(jù)統(tǒng)計(jì),我國(guó)2000年汽車產(chǎn)量200多萬輛,車用塑料達(dá)138萬噸。從國(guó)內(nèi)外汽車塑料應(yīng)用的情況看,汽車塑料的用量現(xiàn)已成為衡量汽車生產(chǎn)技術(shù)水平的標(biāo)志之一。
⑶、作為塑料制件最有效的成型方法之一的注塑成型由于可以一次成型各種結(jié)構(gòu)復(fù)雜、尺寸精密和帶有金屬嵌件的制品,并且成型周期短,可以一模多腔,生產(chǎn)率高,大批生產(chǎn)時(shí)成本低廉,易于實(shí)現(xiàn)自動(dòng)化生產(chǎn),因此在塑料加工行業(yè)中占有非常重要的地位。據(jù)統(tǒng)計(jì),塑料模具約占所有模具(包括金屬模)的38.2%,塑料制品總重量的大約32%是用于注射成型的,80%以上的工程塑料制品都要采用注射成型方式生產(chǎn)。
⑷、根據(jù)海關(guān)統(tǒng)計(jì),我國(guó)2000年共進(jìn)口模具9.77億美元,其中塑膠模具共5.5億美元,占56.3%,2001年共進(jìn)口模具11.12億美元,其中塑膠模具共6.16億美元,占55.4%。從品種上來說,進(jìn)口量最大的是塑膠模具。
在壓縮成型過程中,塑料原料是以粉狀或錠料形式放置在加熱的金屬模具型腔中。因?yàn)榉中兔媸撬矫?,上模就垂直下行。閉合模具后,預(yù)成型加壓加熱作用一段時(shí)間。在壓力為2~3t/in和溫度為華氏溫度350的作用下,是塑料呈半液態(tài),充滿模具型腔。雖然近年來開發(fā)的酚醛樹脂可在25S內(nèi)塑化,但塑料通常的塑化需要1~15min。最后開模取出塑件。如果零件中含有金屬嵌件,應(yīng)在注入塑料前,講嵌件放入型腔定位孔中。錠料在裝入模腔前預(yù)熱出去氣體,增強(qiáng)流動(dòng)性,以便于充滿模具和縮短塑化時(shí)間。電介質(zhì)加熱時(shí)加熱錠料的便利方法。
因?yàn)樗芰鲜侵苯蛹尤肽>咝颓恢械模詨嚎s模比其他模塑料工藝的模具簡(jiǎn)單,不需要澆道和澆口,可以節(jié)省原料,因?yàn)榍謇頋驳篮蜐部?,?duì)熱固性塑料來說是極大的浪費(fèi)。用于壓縮模塑的壓力機(jī)通常是垂直液壓機(jī)。較大的壓力機(jī)要求操作者全神貫注地操作;然而,一個(gè)操作者可以同時(shí)操作幾臺(tái)小型壓力機(jī),因此壓力機(jī)要合理放置以便操作者能夠方便你從一臺(tái)到另一臺(tái)進(jìn)行操作,操作者要保證當(dāng)他再次繞道特定壓力機(jī)前時(shí),模具恰好準(zhǔn)備開模。熱固性塑料在加熱和加壓作用下固化,這個(gè)特性決定其適合壓縮模和傳遞模。因?yàn)閴嚎s模要交替的加熱和冷卻,所以熱塑性塑料實(shí)際上不是用于壓縮成型。為了使熱塑性塑料之間硬化并從型腔中頂出,就需要將塑件冷卻。
壓縮模的類型。 用于壓縮的模具可分為四種基本類型,分別是:不溢式壓縮模、擋環(huán)不溢式壓縮模、溢式壓縮模和半溢式壓縮模。在不溢式壓縮模中,柱塞式凸模隨上模進(jìn)入下模模腔成型,因?yàn)橄履]有擋環(huán)或限位裝置,柱塞式凸模繼續(xù)下行以全部壓力施加在塑料上,這樣就成產(chǎn)出具有良好電性能和物理性能的致密塑件。加入模腔的塑料劑量須精確計(jì)量,以為其影響零件的壁厚。擋環(huán)不溢式壓縮模與不溢式壓縮模類似,只是在預(yù)定點(diǎn)處增加了擋環(huán),使柱塞式凸模在預(yù)定點(diǎn)停止運(yùn)動(dòng),在這種模具中擋環(huán)吸收了原應(yīng)作用在零件上的部分壓力。這種壓縮??删_控制零件的壁厚,但是塑件密度的變化是相當(dāng)大的。在溢式壓縮模中,溢料會(huì)增加上下模的尺寸。當(dāng)上模對(duì)塑料施壓時(shí),多余的塑料會(huì)從分型面處溢出。對(duì)溢料進(jìn)一步施壓,他就硬化最后在上模形成飛邊。生產(chǎn)致密塑件通常需要使用的計(jì)算量稍多的原料來增加壓力。這種類型的模具之所以在生產(chǎn)中廣泛采用,是因?yàn)樗雽?duì)比較容易制造,并能夠控制塑件的厚度和致密度,使其更接近要求。半溢式壓縮模是溢式壓縮模和不溢式壓縮模的組合類型,除了飛邊外,采用的擋環(huán)可限制上模的移動(dòng)。