帶凸臺塑料蓋注塑模具設計
27頁 10000字數(shù)+論文說明書+5張CAD圖紙【詳情如下】
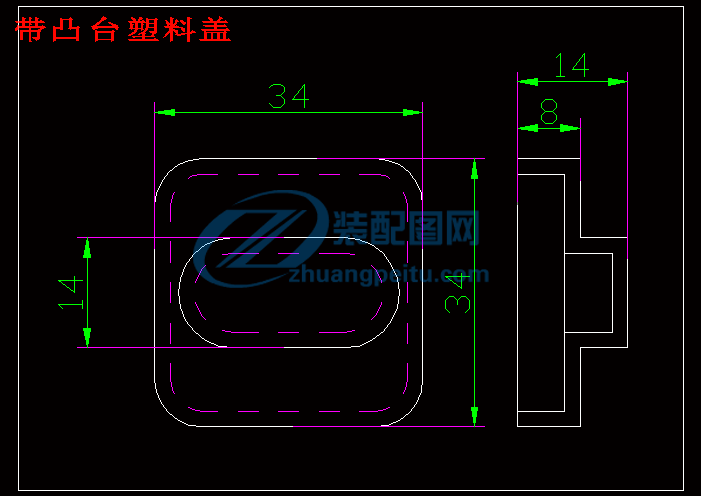
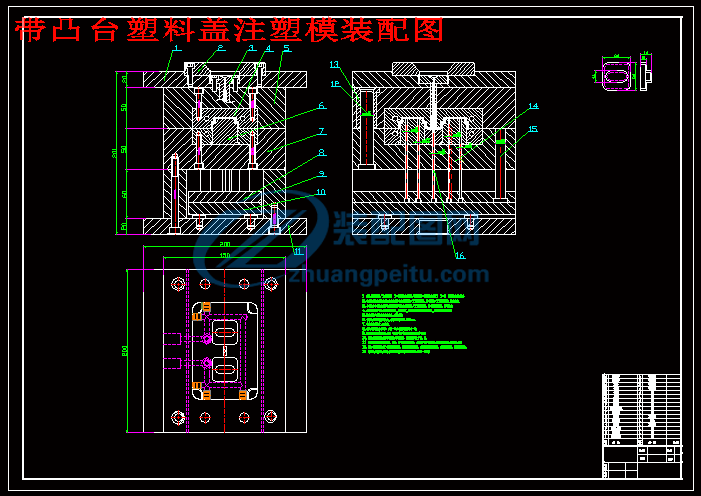
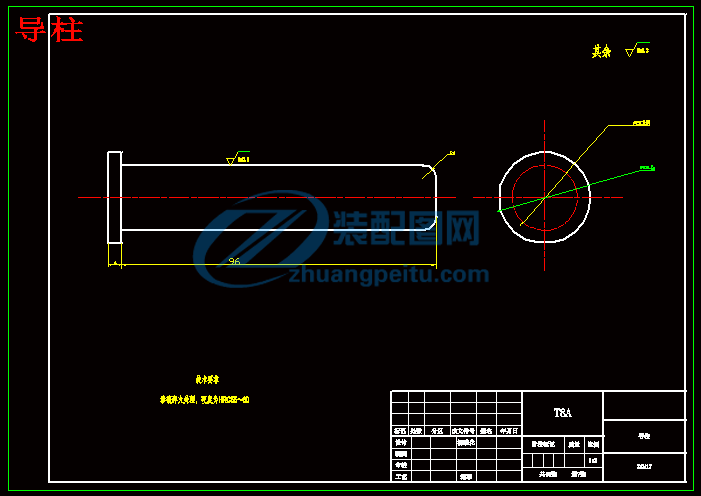
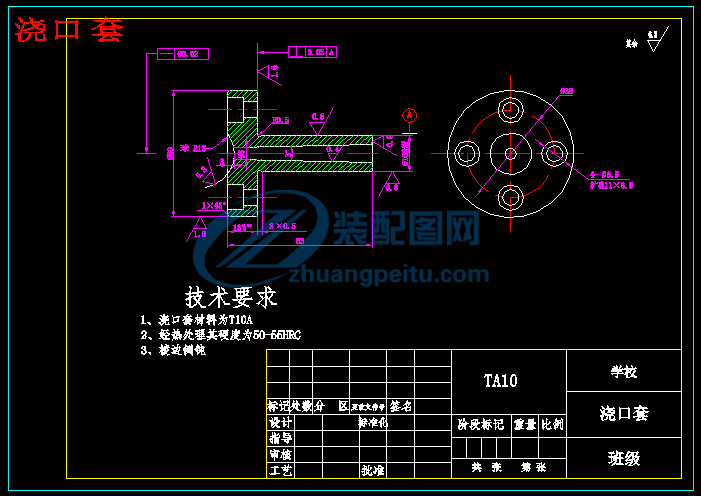
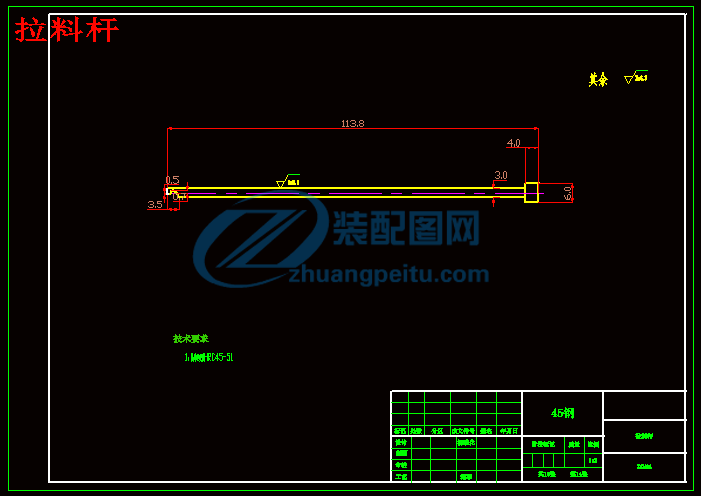
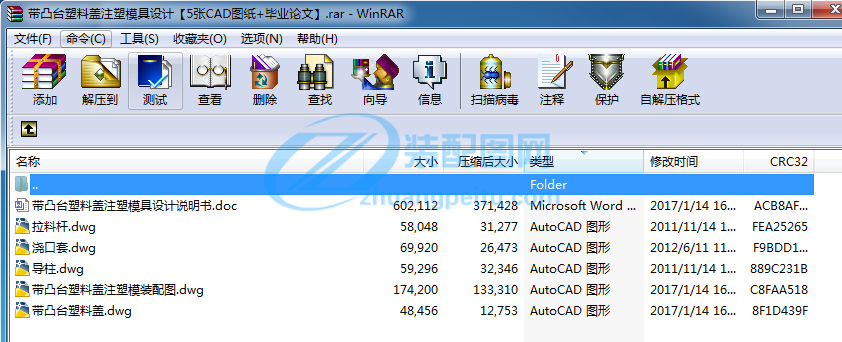
導柱.dwg
帶凸臺塑料蓋.dwg
帶凸臺塑料蓋注塑模具設計說明書.doc
帶凸臺塑料蓋注塑模裝配圖.dwg
拉料桿.dwg
澆口套.dwg
引 言
本說明書為塑料注射模具設計說明書,是根據(jù)塑料模具手冊上的設計過程及相關工藝編寫的。本說明書的內容包括:目錄、課程設計指導書、課程設計說明書、參考文獻等。
編寫本說明書時,力求符合設計步驟,詳細說明了塑料注射模具設計方法,以及各種參數(shù)的具體計算方法,如塑件的成型工藝、塑料脫模機構的設計。
本說明書在編寫過程中,得到老師和同學的大力支持和熱情幫助,在此謹表謝意。
第一章 塑件工藝分析
1.1塑件分析
圖1-1 塑件
此件為聚丙烯(PP)塑件,要求大批量生產。
1.2塑件工藝性分析
(1)PP的性能特點與用途
比重小,強度、剛性、耐熱性均優(yōu)于HDPE,可在100°C左右使用。具有優(yōu)良的耐腐蝕性,良好的高頻絕緣性,不受濕度影響。但低溫變脆,不耐磨,易老化。適于制作一般機械零件、耐腐蝕零件和絕緣零件如板、片、透明薄膜、繩、絕緣零件、汽車零件、閥門配件、日用品等。使用溫度10~120°C。
(2)成型特點
1.結晶性料,吸濕性小,可能發(fā)生熔體破裂,長期與熱金屬接觸易發(fā)生分解
2.流動性極好,溢邊值0.03㎜左右
3.冷卻速度快,澆注系統(tǒng)及冷卻系統(tǒng)散熱應適度
4.成型收縮范圍大,收縮率大,易發(fā)生縮孔、凹痕、變形,取向性強
5.注意控制成型溫度,料溫低取向性明顯,尤其低溫高壓時更明顯。模具溫度低于50°C以下塑件無光澤,易產生熔接痕、流痕;90°C以上時易發(fā)生翹曲、變形
6.塑件應壁厚均勻,避免缺口、尖角,以防止應力集中
(3)PP的注射工藝參數(shù)
(1)注射機:螺桿式
(2)螺桿轉速(n/(r/min )):48
(3)料筒溫度(t/℃):前段200~220
中段180~200
后段160~180
(4)噴嘴形式:直通式
(5)模具溫度(℃):80~90
(6)注射壓力(MPa):70~100
(7)成型時間(s):注射時間20~60;高壓時間0~3;冷卻時間20~90;總周期50~160.
結束語
課程設計接近了尾聲.這段時間我認為最重要的就是做好設計的預習,認真的研究老師給的題目,其次,老師對題目的講解要一絲不茍的去聽去想,因為只有都明白了,做起設計就會事半功倍,如果沒弄明白,就迷迷糊糊的去選題目做設計,到頭來一點收獲也沒有。在這段時間里,也暴露了自己很多問題,第一、不夠細心比如由于粗心大意算錯了數(shù)導致設計的零件不能正確的裝配。第二,是在學習態(tài)度上,這次課設是對我的學習態(tài)度的一次檢驗。我的第一大心得體會就是作為一名設計人員,要求具備的首要素質絕對應該是嚴謹。我們這次實習所遇到的多半問題多數(shù)都是由于我們不夠嚴謹。第三,在做人上,我認識到,無論做什么事情,只要你足夠堅強,有足夠的毅力與決心,有足夠的挑戰(zhàn)困難的勇氣,就沒有什么辦不到的。在這次難得的課程設計過程中我鍛煉了自己的思考能力和對UG軟件的使用能力。再次感謝老師的輔導以及同學的幫助,是他們讓我有了一個更好的認識,無論是學習還是生活,生活是實在的,要踏實走路。課程設計時間雖然不長,但我學習了很多的東西,使我眼界打開,感受頗深。
這篇說明書的編寫以及修改的過程,也是我越來越認識到自己知識與經驗缺乏的過程。雖然,我盡可能地收集材料,竭盡所能運用自己所學的知識進行設計說明書的編寫,但還是存在許多不足之處,有待改進。請各位評委老師多批評指正,讓我在今后的學習中學到更多。同時也對這段時間老師給予的幫助表示感謝!
參考文獻
1.李建軍,李德群.模具設計基礎及模具CAD.北京:機械工業(yè)出版社,2005
2.楊占堯,白柳.塑料模具典型結構設計實例.北京:化工工業(yè)出版社,2008
3.大連理工大學工程畫教研室編.《機械制圖》.北京:高等教育出版社,1993
4.宋玉恒. 塑料注射模具設計實用手冊. 北京:航空工業(yè)出版社, 1998
5.楊占堯. 塑料注塑模結構與設計.北京:清華大學出版社,2004
6.歐陽德祥. 塑料成型工藝與模具結構.北京:機械工業(yè)出版社,2008
7.閻亞林. 塑料模具圖冊.北京;高等教育出版社,2004
8.王興天. 注塑技術與注塑機.北京:化學工業(yè)出版社,2005
9.史鐵梁.模具設計指導.北京:機械工業(yè)出版社,2003
10.伍先明.塑料模具設計指導.北京:國防工業(yè)出版社,2008
11.展迪優(yōu).UG NX 7.0快速入門教程.北京:機械工業(yè)出版社,2010
12.肖愛民.模具設計從入門到精通.北京:機械工業(yè)出版社,2010
14.齊衛(wèi)東.塑料模具設計與制造【M】.北京:高等教育出版社,2004
15.歐圣雅.冷沖壓與塑料成型機械【M】.北京:機械工業(yè)出版社,1999
16.孫鳳勤,閆亞林.沖壓與塑壓成型設備【M】.北京:高等教育出版社,2003
17.程培源.模具壽命與材料【M】.北京:機械工業(yè)出版社,2004
18.高為國.模具材料【M】.北京:機械工業(yè)出版社,2004
19.許發(fā)樾.模具標準應用手冊【M】.北京:機械工業(yè)出版社,1994
20.郭廣思.塑料成型技術.北京:機械工業(yè)出版社,2002
1 引 言 本說明書為塑料注射模具設計說明書,是根據(jù)塑料模具手冊上的設計過程及相關工藝編寫的。本說明書的內容包括:目錄、 課程 設計指導書、 課程 設計說明書、參考文獻等。 編寫本說明書時,力求符合設計步驟,詳細說明了塑料注射模具設計方法,以及各種參數(shù)的具體計算方法,如塑件的成型工藝、塑料脫模機構的設計。 本說明書在編寫過程中,得到 老師和同學的大力支持和熱情幫助,在此謹表謝意。 2 第一章 塑件工藝分析 件分析 圖 1件 此件 為聚丙烯( 件 ,要求大批量生產。 件工藝性分析 ( 1) 比重小,強度、剛性、耐熱性均優(yōu)于 在 100° 有優(yōu)良的耐腐蝕性,良好的高頻絕緣性,不受濕度影響。但低溫變脆,不耐磨,易老化。適于制作一般機械零件、耐腐蝕零件和絕緣零件如板、片、透明薄膜、繩、絕緣零件、汽車零件、閥門配件、日用品等。使用溫度 10~ 120° C。 ( 2) 成型特點 濕性小,可能發(fā)生熔體破裂,長期與熱金屬接觸易發(fā)生分解 邊值 右 注系統(tǒng)及冷卻系統(tǒng)散熱應 適度 縮率大,易發(fā)生縮孔、凹痕、變形,取向性強 3 溫低取向性明顯,尤其低溫高壓時更明顯。模具溫度低于 50° 產生熔接痕、流痕; 90° 形 免缺口、尖角,以防止應力集中 ( 3) ( 1)注射機:螺桿式 ( 2)螺桿轉速( n/(r/): 48 ( 3)料筒溫度( t/℃):前段 200~ 220 中段 180~ 200 后段 160~ 180 ( 4) 噴嘴形式:直通式 ( 5) 模具溫度(℃): 80~ 90 ( 6) 注射壓力( 70~ 100 ( 7) 成型時間( s):注射時間 20~ 60;高壓時間 0~ 3;冷卻時間 20~ 90;總周期 50~ 160. 表 1主要性能指標 密度 g/性模量 比容 g 曲強度 水率 %( 24h) 度 95~ 105 收縮率 % 積電阻 率Ω 1016 熔點° C 170~ 176 沖擊韌度Kj*缺口 78 缺口 變形溫度° C 102~ 115 沖擊強度 kJ/m2 30 抗拉屈服強度 7 4 第 2 章 擬定模具結構形式 分型面位置的確定 分開模具取出塑件的面稱為分型面 ;注射模有一個分型面或多個分型面,分型面的位置,一般垂直于開模方向。分型面的形狀有平面和曲面等,但也 有將分型面作傾斜的平面或彎折面,或曲面,這樣的分型面雖加工難,但型腔制造和制品脫模較易。有合模對中錐面的分型面,分型面自然也是曲面。 選擇分型面時,應考慮的基本原則: 5 1) 分型面應選在塑件外形最大輪廓處 當已經初步確定塑件的分型方向后分型面應選在塑件外形最大輪廓處,即通過該方向塑件的截面積最大,否則塑件無法從形腔中脫出。 2) 確定有利的留模方式,便于塑件順利脫模 從制件的頂出考慮分型面要盡可能地使制件留在動模邊,當制件的壁相當厚但內孔較小時,則對型芯的包緊力很小常不能確切判斷制件中留在型芯上還是在凹模內。 這時可將型芯和凹模的主要 部分都設在動模邊,利用頂管脫模,當制件的孔內有管件(無螺紋連接)的金屬嵌中時,則不會對型芯產生包緊力。 3) 保證制件的精度和外觀要求 與分型面垂直方向的高度尺寸,若精度要求較高,或同軸度要求較高的外形或內孔,為保證其精度,應盡可能設置在同一半模具腔內。因分型面不可避免地要在制件中留下溢料痕跡或接合縫的痕跡,故分型面最好不選在制品光亮平滑的外表面或帶圓弧的轉角處。 4) 分型面應使模具分割成便于加工的部件,以減少機械加工的困難。 5) 不妨礙制品脫模和抽芯。 在安排制件在型腔中的方 位時,要盡量避免與開模運動相垂直方向的避側凹或側孔。 6) 有利于澆注系統(tǒng)的合理處置。 7) 盡可能與料流的末端重合,以利于排氣。 本次設計產品的分型面在塑件上一目了然,分型面設在塑件的大口端面處。 綜和以上信息此件分型面位置如下圖: 圖 2件分型面圖 確定型腔數(shù)量及排列方式 6 型腔指模具中成形塑件的空腔,而該空腔是塑件的負形,除去具體尺寸比塑料大以外,其他都和塑件完全相同,只不過凸凹相反而己。 注射成形是先閉模以形成空腔,而后進料成形,因此必須由兩部分或(兩部分以上)形成這一空 腔 —— 型腔。其凹入的部分稱為凹模,凸出的部分稱為型芯。 1) 型腔數(shù)量的確定 其數(shù)目的決定與下列條件有關: ( 1) 塑件尺寸精度 型腔數(shù)越多時,精度也相對地降低, 1、 2 級超精密注塑件,只能一模一腔,當尺寸數(shù)目少時,可以一模二腔。 3、 4 級的精密級塑件,最多一模四腔。 ( 2 )模具制造成本 多腔模的制造成本高于單腔模,但不是簡單的倍數(shù)比。從塑件成本中所占的模具費比例看,多腔模比單腔模具低。 ( 3) 注塑成形的生產效益 多腔模從表面上看,比單腔模經濟效益高。但是多腔模所使用的注射機大,每一注射循環(huán)期長而維持費 較高,所以要從最經濟的條件上考慮一模的腔數(shù)。 ( 4) 制造難度 多腔模的制造難度比單腔模大,當其中某一腔先損壞時,應立即停機維修,影響生產。塑料的成形收縮是受多方面影響的,如塑料品種,塑件尺寸大小,幾何形狀,熔體溫度,模具溫度,注射壓力,充模時間,保壓時間等。影響最顯著的是塑件的壁厚和同何形狀的復雜程度。 本設計根據(jù)塑件結構的特點,考慮型腔布局方式,采用一模兩腔的模具結構,這樣比一模一腔模具的生產效率高,同時結構更為合理。 2)型腔的布局 多型腔模具設計的重要問題之一就是澆注系統(tǒng)的布置方式,由于型腔的排布與 澆注系統(tǒng)布置密切相關,因而型腔的排布在多型腔模具設計中應加以綜合考慮。型腔的排布應使每一個型腔都通過澆注系統(tǒng)從總壓力中心中均等地分得所需的壓力,以保證塑料熔體同時均勻地 充滿每個型腔,使各型腔的塑件內在質量均一穩(wěn)定。這就要求型腔與主流道之間的距離盡可能最短,同時采用平衡的流道和合理的澆口尺寸以及均勻的冷卻等。合理的型腔排布可以避免塑件的尺寸差異、應力形成及脫模困難等問題。 平衡式型腔布局的特點是從主流道到各型腔澆口的分流道的長度、截面形狀及尺寸均對應相同,可以實現(xiàn)均衡進料和同時充滿型腔的目的; 非平衡式型腔布 局的特點是從主流道到各型腔澆口的分流道的長度不相等,因而不利于均衡進料,但可以縮短流道的總長度,為達到同時充滿型腔的目的,各澆口的截面尺寸制作得不相同。 7 要指出的是,多型腔模具最好成型同一尺寸及精度要求的制件,不同塑件原則上不應該用同一副多模腔模具生產。在同一副模具中同時安排尺寸相差較大的型腔不是一個好的設計,不過有時為了節(jié)約,特別是成型配套式塑件的模具,在生產實踐中還使用這一方法,但難免會引起一些缺陷,如有些塑件發(fā)生翹曲、有些則有過大的不可逆應變等。 本設計一模 2 腔, 且壁厚均勻, 故采用平衡式, 布局如 圖 所示: 圖 2腔的布局 8 第 3 章 注塑設備選擇 件質量、體積計算和鎖模力的計算 ( 1)由 模得 塑件的體積: 件的質量: 查塑料模具設計指導附表 9ρ = / 澆注系統(tǒng)凝料體積的估算 可按塑件體積的 計算 由于該模具采用一模 2 腔,所以澆注系統(tǒng)凝料體積為 模具一次注射所需 塑料聚丙烯( 體積 V.=22=量 M。 =ρ V.≈ 件和流道凝料(包括澆口 )在分型面上的投影面積及所需鎖模力 塑件和流道凝料(包括澆口)在分型面上的投影面積及所需鎖模力 A=2=4× m= =25=括澆口)在分型面上的投影面積 括澆口)在分型面上的投影面積 P 型 據(jù)多型腔模的統(tǒng)計分析,大致是每個塑件在分型面上的投影面積 ,因此可用 估算。由塑料模具設計指導書 7 頁表 2 P 型=25 9 擇注射機型號 根據(jù)上面計算得到的 M 和 來選擇一種注射機,注射機的最大注射量(額定注射量 G)和額定鎖模力 F 應滿足 G≥ m/a 式中 a—— 注射系數(shù),無定型塑料取 晶型塑料取 F>析 以上數(shù)據(jù)在塑料成型工藝與模具結構書附錄 主要技術參數(shù)見下表 : 表 3注射機主要技術參數(shù) 理論注射容量 / 8 鎖模力 /00 螺桿直徑 /2 拉桿內間距 /10× 310 注射壓力 /66 移模行程 /70 注射速率 /(g/s) 52 最大模厚 /30 塑化能力 /(g/s) 小模厚 /20 動定模板尺寸 /69× 482 注射重量 /g 35 噴嘴球半徑 /0 噴嘴孔直徑 / 頂出 力 /2 頂出行程 /0 10 第四章 型腔數(shù)量及注射機參數(shù)校核 型腔數(shù)量的校核 1) 型腔數(shù)量的校核 ( 1)由注射機料筒塑化速率校核型腔數(shù)量 n≤ (600式右邊 =41≥ 2 (符和要求) : 式中 K—— 注射機最大注射量的利用系數(shù),一般取 —— 注射機的額定塑化量( g/h 或 h) t—— 成型周期 ,因塑件小,壁厚不大,取 30s 澆注系統(tǒng)所需塑料質量和體積( g 或 單個塑件的質量和體積( g 或 按注射機的最大注射量校核型腔數(shù)量 n≤( ≥ 4 (符和要求) 式中 注射機允許的最大注射量( g/按注射機的額定鎖模力校核型腔數(shù)量 n≤( ≥ 4(符和要求) 式中 N) P 型 一般是注射壓力的 30%— 65%,該處取型腔平均壓力為 30 注射機工藝參數(shù)校核 11 注射量校核 注射量以容積表示 最大注射容積為 38=中 該注射機為 38 晶型塑料取 若注射量過小,注射機的塑化能力得不到發(fā)揮,塑料在料筒內停留時間過長。所以最小注射量容積 38=故每次注射的實際注射 量積 'V 應滿足 ? ,而 'V =合要求。 鎖模力校核 在前面已進行,符合要求 3)最大注射壓力的校核 k′ 式中 k′ —— 安全系數(shù)( k′一般取 實際生產中,該塑件成型時所需注射壓力 0100大與最小模具厚度 模具厚度 H < 中 20 30見表 3而該套模具厚度 H==201合要求 開模行程和推出機構的校核 開模行程校核 H≧ 2+(5~ 10) 式中 取 2701取 202取 101值計算 符合要求 推 出機構校核 該注塑機推出行程為 70于 0, 符合要求 模架尺寸與注射機拉桿內間距校核 該套模具模架的外形尺寸為 200200注塑機拉桿內間距為 310310符合要求 12 第 5 章 澆注系統(tǒng)的設計 流道設置 1) 主流道尺寸 主流道的作用 主流道的模具,一般不用澆口套,而直接開設在定模板上。 澆口套是注射機噴嘴在注射模具上的座墊,在注射時它承受很大的注射機噴嘴端部的壓力同時由 于澆口套末端通過流道澆口與型腔相連接,所以也承受模具型腔壓力的反作用力。為了 防止?jié)部谔滓驀娮於瞬繅毫Χ粔喝肽>邇?,澆口套的結構上要增加臺肩,并用螺釘緊固在模板上,這樣亦可防止模腔壓力的反作用力而把澆口套頂出。 主流道設計要點 (1) 澆口套的內孔(主流道)呈圓錐形,錐度 2°~ 6°。若錐度過大會造成壓力減弱,流速減慢,塑料形成渦流,熔體前進時易混進空氣,產生氣孔;錐度過小,會使阻力增大,熱量損耗大,表面黏度上升,造成注射困難。 (2) 澆口套進口的直徑 d 應比注射機噴嘴孔直徑 等于或小于注射機噴嘴直徑,在注射成型時會造成死角,并積存塑料,注射壓力下降 ,塑料冷凝后,脫模困難。 (3) 澆口套內孔出料口處(大端)應設計成圓角 r,一般為 3 (4) 澆口套與注射機噴在接觸處球面的圓弧度必須吻合。設球面澆口套球面半徑為 射機球面半徑為 r, 其關系式如下: r+ 1口套球面半徑比注射機噴嘴球面半徑大,接觸時圓弧度吻合的好。 (5) 澆口套長度(主流道長度)應盡量短,可以減少冷料回收量,減少壓力損失和熱量損失。 (6) 澆口套錐度內壁表面粗糙度為 m,保證料流順利,易脫模。 (7) 澆口套不能制成拼塊 結構,以免塑料進入接縫處,造成冷料脫模困難。 (8) 澆口套的長度應與定模板厚度一致,它的端部不應凸出在分型面上,否則會造成合模困難,不嚴密,產生溢料,甚至壓壞模具。 (9) 澆口套部位是熱量最集中的地方,為了保證注射工藝順利進行和塑件質量,要考慮冷卻措施。 根據(jù)所選注射機,則主流道小端尺寸為 13 d = 注射機噴嘴尺寸 + (1) = 2 + 流道球面半徑為 噴嘴球面半徑 + ( 1~ 2) =10+( 1~ 2) = 11 面配合高度 h=3— 5 h=3 主流道長度 盡量小于 60標準模架結合該模具結構取 L=25+20=45流道大端直徑 D=d+2(半錐角 °~ 2 °,取 a=2 °) 澆口套總長 L。 =L+2+h=45+2+3=50口套圖如下: 圖 5口套截面圖 14 分流道設計 1)分流道的作用 分流道式指主流道末端與澆口之間的一段塑料熔體的流動通道。其基本作用是在壓力損失最小的條件下,將來自主流道的 熔融塑料,以較快的速度送到澆口處充模。同時,在保證熔體均勻地分配到各型腔的前提下,要求分流道中殘留的熔融塑料最少,以減少冷料的回收。 2) 設計要點 在多種常見截面當中,圓形截面的壓降是最小的。但由于圓形的分流道必須在上下模板上都加工出半圓槽,工藝性不好,故此設計中采用工藝性更為合理而壓降也比較小且塑料熔體的熱量散失流動阻力均不大的 U 形截面或梯形截面。該模具采用梯形分流道。 3)分流道的形狀及尺寸 分流道可開設在動、定模分型面的兩側或其中任意一側。設計要求其截面形狀應盡量使其比表面積(流道表面積 與其體積之比)小,目的是在溫度較高的塑料熔體和溫度相對較低的模具之間提供較小的接觸面積,以減小熱量損失。分流道大多設置在分型面上,分流道截面形狀一般為圓形、梯形、 U 形、半圓形及矩形等。 ( 1)分流道長度長度應盡量短,且少彎折。 綜合型腔布局尺寸確定該模具分流道的長度為: L=43× 2+85=171( 分流道 ( 2)圓形截面的比表面積最小因此取截面為圓(直徑為 4流道,圖形如下: 圖 5分流道圓形截面圖 ( 3) 分流道的表面粗糙度 由于分流道中與模具接觸的外層塑料迅速冷卻,只有中心部位的塑料熔體的流動狀態(tài)較為理想,因此分流道的內表面粗糙度 不要求很低,一般取 15 m,這樣表面稍不光滑,有助于增大塑料熔體的外層流動阻力。避免熔流表面滑移,使中心層具有較高的剪切 速率。 ( 4)分流道的布置形式 分流道在分型面上的布置與前面所述型腔排列密切相關,有多種不同的布置形式,但應遵循兩方面原則:即一方面排列緊湊、縮小模具板面尺寸;另一方面流程盡量短、鎖模力力求平衡。 本模具的流道布置形式采用平衡式,綜合流道截面形狀考慮我選擇 采用在動定模開分流道,分流道圖如下: 圖 5流道布置圖 口的設計 1) 澆口的作用 澆口是分流道和型腔之間的連接部分,也是注射模具澆注系統(tǒng)的最后部分,通過澆口直接使熔融的塑料進入型腔內。澆口的作用是使從流道來的熔融塑料以較快的速度進入并充滿型腔,型腔充滿塑料后,澆口能迅速冷卻封閉,防止型腔內還未冷卻的熱料回流。 澆口設計與塑料制品形狀、塑料制品斷面尺寸、模具結構、注射工藝參數(shù)(壓力等)及塑料性能等因素有關。澆口的截面要小,長度要短,這樣才能增大料流速度,快速冷卻封閉,便于使塑料制品分離,塑 料制品的澆口痕跡亦不明顯。 塑料制品質量的缺陷,如缺料、縮孔、拼縫線、質脆、分解、白斑、翹曲等,往往都是由于澆口設計不合理而造成的。 2) 澆口設計的基本要點 16 1、 盡量縮短流動距離 澆口位置的安排應保證塑料熔體迅速和均勻地充填模具型腔,盡量縮短熔體的流動距離,減少壓力損失,有利于排除模具型腔中的氣體,這對大型塑件更為重要。 2、 澆口應設在塑件制品斷面較厚的部位 當塑件的壁厚相差較大時,若將澆口開設在塑件的薄壁處,這時塑料熔體進入型腔后,不但流動阻力大,而且還易冷卻,以致影響了熔體的流動距離,難以保證其充滿整個型腔。 另外從補縮的角度考慮,塑件截面最厚的部位經常是塑料熔體最晚固化的地方,若澆口開設在薄壁處,則厚壁處極易因液態(tài)體積收縮得不到收縮而形成表面凹陷或真空泡。因此為保證塑料熔體的充分流動性,也為了有利于壓力有效地傳遞和比較容易進行因液態(tài)體積收縮時所需的補料,一般澆口的位置應開設在塑件壁最厚處。 3、 必須盡量減少或避免熔接痕 由于成型零件或澆口位置的原因,有時塑料充填型腔時造成兩股或多股熔體的匯合,匯合之處,在塑件上就形成熔接痕。熔接痕降低塑件的強度,并有損于外觀質量,這在成型玻璃纖維增強塑料的制件時尤為嚴重。有時 為了增加熔體的匯合,匯合之處,在塑件上就形成熔接痕。熔接痕降低塑件的強度,并有損于外觀質量,這在成型玻璃纖維增強塑料的制件時尤其嚴重。一般采用直接澆口、點澆口、環(huán)形澆口等可以避免熔接痕的產生,有時為了增加熔體匯合處的溶接牢度,可以在溶接處外側設一冷料穴,使前鋒冷料引如其內,以提高熔接強度。 在選擇澆口位置時,還應考慮熔接的方位對塑件質量及強度的不同影響。 4、 應有利于型腔中氣體的排除 要避免從容易造成氣體滯留的方向開設澆口。如果這一要求不能充連接。 3) 澆口的類型 澆口的形式多種多樣,但常用的澆口有如下 11 種: 直接澆口、側澆口、扇形澆口、平縫澆口、環(huán)形澆口、盤形澆口、輪輻澆口、爪形澆口、點澆口、潛伏澆口、護耳澆口等。 本設計采用側澆口,截面為圓形,側澆口尺寸計算如下: ~ A 有 ≈ 2108b= 17 t≈ L=面圖如下: 圖 5口截面圖 18 第 6 章 成型零件的設計與計算 所謂成型零件的工作尺寸是指成型零件上直接構成型腔腔體的部位的尺寸,其直接對應塑件的形狀與尺寸。鑒于影響塑件尺寸精度的因素多且復雜,塑件本身精度也難以達到高精度,為了計算簡便,規(guī)定: 塑件的公差 塑件的公差規(guī)定按單向極限制,制品外輪廓尺寸公差取負值“ ?? ”,制品叫做腔尺寸公差取正值“ ?? ”,若制品上原有公差的標注方法與上不符,則應按以上規(guī)定進行轉換。而制品孔中心距尺寸公差按對稱分布原則計算,即取±△ /2。模具制造公差 實踐證明,模具制造公差可取塑件公差的 ~61 ,即δ z= ?)61~31( ,現(xiàn)取 3? 。而且按成型加工過程中的增減趨向取“ +”、“ -”符號,型腔尺寸不斷增大,則取“ +δ z” ,型芯尺寸不斷減小則取“ -δ z”,中心距尺寸取“ 2z?? ”。 模具的磨損量 實踐證明,對于一般的中小型塑件,最大磨損量可取塑件公差的 1/6,對于大型塑件則取 6? 以下。另外對于型腔底面(或型芯端面),因為脫模方向垂直,故磨損量δ c=0。 塑件的收縮率 塑件成型后的收縮率與多種因素有關 ,通常按平均收縮率計算。 =( 1% + 3%) / 2 = 2% 課本附錄 %、 % 模具在分型面上的合模間隙 由于注射壓力及模具分型面平面度的影響,會導致動模、定模注射時存在著一定的間隙。一般當模具分型的平面度較高、表面粗糙度較低時,塑件產生的飛邊也小。飛邊厚度一般應小于是 件尺寸可按公差 14486準中的 5級精度選取。 2 ? 19 型腔的徑向尺寸與深度 根據(jù)公式 : 式中△在塑料成型工藝與模具結構書 18頁表 1 ??????? ???043)1( 徑向尺寸 ???? 011 )43(=( 2% - 3 =向尺寸 ???? 011 )43(=( 2% - 3 =腔深度尺寸計算 根據(jù)公式 : ???????? ???0S 32)1(H ???? 011 )32( = (17 +17 * 2% - 2/3 * 0+ = 型腔圖: 20 圖 6腔圖 型芯的徑向尺寸與深度 根據(jù)公式 : l M= 043)1(?????? ??? 小頭徑向尺寸 0111 )43( m ??????= ( 2% +0 = 頭徑向尺寸 0222 )43(m ??????=( 2% +0 據(jù)公式: h M= 032)1(???????? ??? 21 型芯高度尺寸 h 2M= 032)1(???????? ??? = ( 2% + 2/3× 0 =圖 6芯圖 具型腔側壁的確定 模具型腔在成型過程中受到塑料熔體的高壓作用,用具有足夠的強度和剛度。但是對型腔的壁厚做出精確的力學計算是非常困難的,一般在工廠中經常用經驗數(shù)據(jù)對型腔壁厚進行簡化設計。根據(jù)課本塑料成型工藝與模具結構 99 頁表 3的數(shù)值壁厚 s=20架的確定 根據(jù)型腔的布局可看出,型腔分布尺寸為為 165× 165,有根 據(jù)型腔側壁最小壁厚為 20,再考慮到導柱、導套及連接螺釘布置應占據(jù)的位置和采用推件板推出等各方面的問題,由塑料成型工藝與模具結構書 199 頁確定選用 、模架尺寸為 250250標準模架,即可符合要求。 22 圖 6架 第 7 章 合模導向機構設計 向與定位機構設計 1)合模導向機構的總體設計 導向機構對于塑料模具是必不可少的部件,因為模具在閉合時有一定的方向和位置,所以必須設有導向機構。 導向機構的主要作用:定位、導向、承受一定側壓等作用。 a. 定位作用 為避免模具裝配時方位 搞錯而損壞模具,并且在模具閉合后使型腔保持正確的形狀,不至因為位置的偏移而引起塑件壁厚不均。 b. 導向作用 動定模合模時,首先導向機構接觸,引導動定模正確閉合,避免凸?;蛐托鞠冗M入型腔以保證不損壞成型零件。 c. 承受一定側壓力 塑料注入型腔過程中會產生單向側壓力,或由于注射機精度的限制使導柱在工作中承受一定的側壓力,此時,導柱能承擔一部分側壓力。 2)導柱的設計 導柱的長度必須比凸模端面要高出 6~ 8 毫米。以免導柱未導正方向而凸模先進入型腔與其相碰而損壞。 柱的端部做成錐形或球形的 先導部分,使導柱能順利進入導柱孔。 導柱應具有硬而耐磨的表面、堅韌而不易折斷的內芯,因此,多采用 23 低碳鋼經滲碳淬火處理。 或碳素工具鋼( 淬火處理硬度 55,導柱滑動部位按需要可設油槽。 配合部分光潔度要求 6 級,此外,導柱的選擇還應跟椐模架來確定。由于模架較大 (200× 200)所以設計成四導柱,此模架導柱簡圖如下所示 : 圖 7柱圖 24 3)導套的設計 導套可以直接開設在模板上,且設計為通孔, 這種形式的孔加工簡單,適用于生產批量小,精度要求較高的模具。 對導套的結構主要有四點要求,分述如下: (1)、形狀為了使導柱進入導套比較順利,在導套的前端倒圓角,導柱孔最好打通,否則導柱進入未打通的導柱孔時,孔內空氣無法逸出而產生壓力,給導柱的進入造成阻力。 (2) 材料可用淬火銅或銅等耐磨材料制造,但其硬度應低于導柱硬度,這樣可以改善磨擦,以防止導柱或導套拉毛。 (3) 導套的精度與配合一般 A 型用二級精度過度配合, B 型用二級精度靜配合。 (4) 光潔度配合部分光潔度要求七級。 導套的選擇應根據(jù)模板的 厚度來確定,材料為 到 55,或采用20 鋼滲碳 ,淬硬到 由于模具的結構不同,該模架上用的導套如下圖: 圖 7套圖 25 4)導柱、導套的布置 根據(jù)模具的形狀的大小,在模具的空閑位置開設導柱孔和導套孔,常見的導柱有 2 至 4 根不等,其布置原則必須保證定模只能按一個方向合模,此設計常用四根相同的導柱布置在定動模固定板的四角。 第 8章 脫模機構設計 脫模機構設計 1) 在注射成型 的每一循環(huán)中,塑件必須由模具 型腔中脫出,脫出塑件的機構稱為脫模機構或頂出機。 ( 1)脫模機推出力應施于塑件剛性和強度最大的部位,作用面積也應盡可能大一些,以防塑件變形或損壞。 ( 2)力求良好的塑件外觀,在選擇頂處位置時,應盡量設在塑件內部或對塑件外觀影響不大的部位。在采用推桿脫模時尤其要注意這個問題。 (3)結構合理可靠,脫模機構應工作可靠,運動靈活,制造方便,更換容易且具有足夠的剛度和強度。 2)脫模機構的分類 脫模機構可按動力來源分類也可按模具結構分類 (1) 按動力來源分類。分為手動脫模、機械脫模、液壓脫模、氣動脫模,本設 計采用液壓脫模。即在注射機上設有專用的頂出油缸,并開模到一定距離后,活塞的動作實現(xiàn)脫模。 按模具結構分類。分為簡單脫模機構、雙脫模機構、順序脫模機構、二級脫模機構、澆注系統(tǒng)脫模機構等。本設計采用的推出機構是推件板推出機構。 推件板推出機構。 其特點是推出力大,且推出力的作用面積大而均勻,運動平穩(wěn),塑件上沒有推出痕跡。 設計時注意事項。為了減小推出過程中推件板和型芯的摩擦,可采用在推件板和型芯間留有 采用 3錐度起到輔助定位作用,防止推件板偏心而引起溢料。 綜合 分析用推桿推出機構,綜合該模架和塑件的考慮我選用一個塑件用 4個推桿,推桿直徑為 6推桿其簡圖如下: 26 圖 8桿 結束語 課程 設計接近了尾聲 真的研究老師給的題目,其次,老師對題目的講解要一絲不茍的去聽去想,因為只有都明白了,做起設計就會事半功倍,如果沒弄明白,就迷迷糊糊的去選題目做設計,到頭來一點收獲也沒有。在這段時間里,也暴露了自己很多問題,第一、不夠細心比如由于粗心大意算錯了數(shù)導致設計的零件不能正確的裝配。第二,是在學習態(tài)度上 ,這次課設是對我的學習態(tài)度的一次檢驗。我的第一大心得體會就是作為一名設計人員,要求具備的首要素質絕對應該是嚴謹。我們這次實習所遇到的多半問題多數(shù)都是由于我們不夠嚴謹。第三,在做人上,我認識到,無論做什么事情,只要你足夠堅強,有足夠的毅力與決心,有足夠的挑戰(zhàn)困難的勇氣,就沒有什么辦不到的。在這次難得的 課程 設計過程中我鍛煉了自己的思考能力和對次感謝老師的輔導以及同學的幫助,是他們讓我有了一個更好的認識,無論是學習還是生活,生活是實在的,要踏實走路。 課程 設計時間雖然不長,但我學習了很多的東西 ,使我眼界打開,感受頗深。 這篇說明書的編寫以及修改的過程,也是我越來越認識到自己知識與經驗缺乏的過程。雖然,我盡可能地收集材料,竭盡所能運用自己所學的知識進行設計說明書的編寫,但還是存在許多不足之處,有待改進。請各位評委老師多批評指正,讓我在今后的學習中學到更多。同時也對這段時間老師給予的幫助表示感謝 ! 27 參考文獻 德群 械工業(yè)出版社, 2005 柳 北京 :化工工業(yè)出版社, 2008 《機械制圖》 等教育出版社, 1993 塑料注射模具設計實用手冊 . 北京 :航空工業(yè)出版社 , 1998 塑料注塑模結構與設計 華大學出版社, 2004 塑料成型工藝與模具結構 械工業(yè)出版社, 2008 塑料模具圖冊 高等教育出版社, 2004 注塑技術與注塑機 學工業(yè)出版社, 2005 模具設計指導 械工業(yè)出版社, 2003 塑料模具設計指導 防工業(yè)出版社, 2008 X 速入門教程 械工業(yè)出版社, 2010 模具設計從入門到精通 械工業(yè)出版社, 2010 塑料模具設計與制造【 M】 等教育出版社, 2004 冷沖壓與塑料成型機械【 M】 械工業(yè)出版社, 1999 亞林 M】 等教育出版社, 2003 模具壽命與材料【 M】 械工業(yè)出版社, 2004 模具材料【 M】 械工業(yè)出版社, 2004 模具標準應用手冊【 M】 械工業(yè)出版社, 1994 塑料成型技術 械工業(yè)出版社, 2002 1 引 言 本說明書為塑料注射模具設計說明書,是根據(jù)塑料模具手冊上的設計過程及相關工藝編寫的。本說明書的內容包括:目錄、 課程 設計指導書、 課程 設計說明書、參考文獻等。 編寫本說明書時,力求符合設計步驟,詳細說明了塑料注射模具設計方法,以及各種參數(shù)的具體計算方法,如塑件的成型工藝、塑料脫模機構的設計。 本說明書在編寫過程中,得到 老師和同學的大力支持和熱情幫助,在此謹表謝意。 2 第一章 塑件工藝分析 件分析 圖 1件 此件 為聚丙烯( 件 ,要求大批量生產。 件工藝性分析 ( 1) 比重小,強度、剛性、耐熱性均優(yōu)于 在 100° 有優(yōu)良的耐腐蝕性,良好的高頻絕緣性,不受濕度影響。但低溫變脆,不耐磨,易老化。適于制作一般機械零件、耐腐蝕零件和絕緣零件如板、片、透明薄膜、繩、絕緣零件、汽車零件、閥門配件、日用品等。使用溫度 10~ 120° C。 ( 2) 成型特點 濕性小,可能發(fā)生熔體破裂,長期與熱金屬接觸易發(fā)生分解 邊值 右 注系統(tǒng)及冷卻系統(tǒng)散熱應 適度 縮率大,易發(fā)生縮孔、凹痕、變形,取向性強 3 溫低取向性明顯,尤其低溫高壓時更明顯。模具溫度低于 50° 產生熔接痕、流痕; 90° 形 免缺口、尖角,以防止應力集中 ( 3) ( 1)注射機:螺桿式 ( 2)螺桿轉速( n/(r/): 48 ( 3)料筒溫度( t/℃):前段 200~ 220 中段 180~ 200 后段 160~ 180 ( 4) 噴嘴形式:直通式 ( 5) 模具溫度(℃): 80~ 90 ( 6) 注射壓力( 70~ 100 ( 7) 成型時間( s):注射時間 20~ 60;高壓時間 0~ 3;冷卻時間 20~ 90;總周期 50~ 160. 表 1主要性能指標 密度 g/性模量 比容 g 曲強度 水率 %( 24h) 度 95~ 105 收縮率 % 積電阻 率Ω 1016 熔點° C 170~ 176 沖擊韌度Kj*缺口 78 缺口 變形溫度° C 102~ 115 沖擊強度 kJ/m2 30 抗拉屈服強度 7 4 第 2 章 擬定模具結構形式 分型面位置的確定 分開模具取出塑件的面稱為分型面 ;注射模有一個分型面或多個分型面,分型面的位置,一般垂直于開模方向。分型面的形狀有平面和曲面等,但也 有將分型面作傾斜的平面或彎折面,或曲面,這樣的分型面雖加工難,但型腔制造和制品脫模較易。有合模對中錐面的分型面,分型面自然也是曲面。 選擇分型面時,應考慮的基本原則: 5 1) 分型面應選在塑件外形最大輪廓處 當已經初步確定塑件的分型方向后分型面應選在塑件外形最大輪廓處,即通過該方向塑件的截面積最大,否則塑件無法從形腔中脫出。 2) 確定有利的留模方式,便于塑件順利脫模 從制件的頂出考慮分型面要盡可能地使制件留在動模邊,當制件的壁相當厚但內孔較小時,則對型芯的包緊力很小常不能確切判斷制件中留在型芯上還是在凹模內。 這時可將型芯和凹模的主要 部分都設在動模邊,利用頂管脫模,當制件的孔內有管件(無螺紋連接)的金屬嵌中時,則不會對型芯產生包緊力。 3) 保證制件的精度和外觀要求 與分型面垂直方向的高度尺寸,若精度要求較高,或同軸度要求較高的外形或內孔,為保證其精度,應盡可能設置在同一半模具腔內。因分型面不可避免地要在制件中留下溢料痕跡或接合縫的痕跡,故分型面最好不選在制品光亮平滑的外表面或帶圓弧的轉角處。 4) 分型面應使模具分割成便于加工的部件,以減少機械加工的困難。 5) 不妨礙制品脫模和抽芯。 在安排制件在型腔中的方 位時,要盡量避免與開模運動相垂直方向的避側凹或側孔。 6) 有利于澆注系統(tǒng)的合理處置。 7) 盡可能與料流的末端重合,以利于排氣。 本次設計產品的分型面在塑件上一目了然,分型面設在塑件的大口端面處。 綜和以上信息此件分型面位置如下圖: 圖 2件分型面圖 確定型腔數(shù)量及排列方式 6 型腔指模具中成形塑件的空腔,而該空腔是塑件的負形,除去具體尺寸比塑料大以外,其他都和塑件完全相同,只不過凸凹相反而己。 注射成形是先閉模以形成空腔,而后進料成形,因此必須由兩部分或(兩部分以上)形成這一空 腔 —— 型腔。其凹入的部分稱為凹模,凸出的部分稱為型芯。 1) 型腔數(shù)量的確定 其數(shù)目的決定與下列條件有關: ( 1) 塑件尺寸精度 型腔數(shù)越多時,精度也相對地降低, 1、 2 級超精密注塑件,只能一模一腔,當尺寸數(shù)目少時,可以一模二腔。 3、 4 級的精密級塑件,最多一模四腔。 ( 2 )模具制造成本 多腔模的制造成本高于單腔模,但不是簡單的倍數(shù)比。從塑件成本中所占的模具費比例看,多腔模比單腔模具低。 ( 3) 注塑成形的生產效益 多腔模從表面上看,比單腔模經濟效益高。但是多腔模所使用的注射機大,每一注射循環(huán)期長而維持費 較高,所以要從最經濟的條件上考慮一模的腔數(shù)。 ( 4) 制造難度 多腔模的制造難度比單腔模大,當其中某一腔先損壞時,應立即停機維修,影響生產。塑料的成形收縮是受多方面影響的,如塑料品種,塑件尺寸大小,幾何形狀,熔體溫度,模具溫度,注射壓力,充模時間,保壓時間等。影響最顯著的是塑件的壁厚和同何形狀的復雜程度。 本設計根據(jù)塑件結構的特點,考慮型腔布局方式,采用一模兩腔的模具結構,這樣比一模一腔模具的生產效率高,同時結構更為合理。 2)型腔的布局 多型腔模具設計的重要問題之一就是澆注系統(tǒng)的布置方式,由于型腔的排布與 澆注系統(tǒng)布置密切相關,因而型腔的排布在多型腔模具設計中應加以綜合考慮。型腔的排布應使每一個型腔都通過澆注系統(tǒng)從總壓力中心中均等地分得所需的壓力,以保證塑料熔體同時均勻地 充滿每個型腔,使各型腔的塑件內在質量均一穩(wěn)定。這就要求型腔與主流道之間的距離盡可能最短,同時采用平衡的流道和合理的澆口尺寸以及均勻的冷卻等。合理的型腔排布可以避免塑件的尺寸差異、應力形成及脫模困難等問題。 平衡式型腔布局的特點是從主流道到各型腔澆口的分流道的長度、截面形狀及尺寸均對應相同,可以實現(xiàn)均衡進料和同時充滿型腔的目的; 非平衡式型腔布 局的特點是從主流道到各型腔澆口的分流道的長度不相等,因而不利于均衡進料,但可以縮短流道的總長度,為達到同時充滿型腔的目的,各澆口的截面尺寸制作得不相同。 7 要指出的是,多型腔模具最好成型同一尺寸及精度要求的制件,不同塑件原則上不應該用同一副多模腔模具生產。在同一副模具中同時安排尺寸相差較大的型腔不是一個好的設計,不過有時為了節(jié)約,特別是成型配套式塑件的模具,在生產實踐中還使用這一方法,但難免會引起一些缺陷,如有些塑件發(fā)生翹曲、有些則有過大的不可逆應變等。 本設計一模 2 腔, 且壁厚均勻, 故采用平衡式, 布局如 圖 所示: 圖 2腔的布局 8 第 3 章 注塑設備選擇 件質量、體積計算和鎖模力的計算 ( 1)由 模得 塑件的體積: 件的質量: 查塑料模具設計指導附表 9ρ = / 澆注系統(tǒng)凝料體積的估算 可按塑件體積的 計算 由于該模具采用一模 2 腔,所以澆注系統(tǒng)凝料體積為 模具一次注射所需 塑料聚丙烯( 體積 V.=22=量 M。 =ρ V.≈ 件和流道凝料(包括澆口 )在分型面上的投影面積及所需鎖模力 塑件和流道凝料(包括澆口)在分型面上的投影面積及所需鎖模力 A=2=4× m= =25=括澆口)在分型面上的投影面積 括澆口)在分型面上的投影面積 P 型 據(jù)多型腔模的統(tǒng)計分析,大致是每個塑件在分型面上的投影面積 ,因此可用 估算。由塑料模具設計指導書 7 頁表 2 P 型=25 9 擇注射機型號 根據(jù)上面計算得到的 M 和 來選擇一種注射機,注射機的最大注射量(額定注射量 G)和額定鎖模力 F 應滿足 G≥ m/a 式中 a—— 注射系數(shù),無定型塑料取 晶型塑料取 F>析 以上數(shù)據(jù)在塑料成型工藝與模具結構書附錄 主要技術參數(shù)見下表 : 表 3注射機主要技術參數(shù) 理論注射容量 / 8 鎖模力 /00 螺桿直徑 /2 拉桿內間距 /10× 310 注射壓力 /66 移模行程 /70 注射速率 /(g/s) 52 最大模厚 /30 塑化能力 /(g/s) 小模厚 /20 動定模板尺寸 /69× 482 注射重量 /g 35 噴嘴球半徑 /0 噴嘴孔直徑 / 頂出 力 /2 頂出行程 /0 10 第四章 型腔數(shù)量及注射機參數(shù)校核 型腔數(shù)量的校核 1) 型腔數(shù)量的校核 ( 1)由注射機料筒塑化速率校核型腔數(shù)量 n≤ (600式右邊 =41≥ 2 (符和要求) : 式中 K—— 注射機最大注射量的利用系數(shù),一般取 —— 注射機的額定塑化量( g/h 或 h) t—— 成型周期 ,因塑件小,壁厚不大,取 30s 澆注系統(tǒng)所需塑料質量和體積( g 或 單個塑件的質量和體積( g 或 按注射機的最大注射量校核型腔數(shù)量 n≤( ≥ 4 (符和要求) 式中 注射機允許的最大注射量( g/按注射機的額定鎖模力校核型腔數(shù)量 n≤( ≥ 4(符和要求) 式中 N) P 型 一般是注射壓力的 30%— 65%,該處取型腔平均壓力為 30 注射機工藝參數(shù)校核 11 注射量校核 注射量以容積表示 最大注射容積為 38=中 該注射機為 38 晶型塑料取 若注射量過小,注射機的塑化能力得不到發(fā)揮,塑料在料筒內停留時間過長。所以最小注射量容積 38=故每次注射的實際注射 量積 'V 應滿足 ? ,而 'V =合要求。 鎖模力校核 在前面已進行,符合要求 3)最大注射壓力的校核 k′ 式中 k′ —— 安全系數(shù)( k′一般取 實際生產中,該塑件成型時所需注射壓力 0100大與最小模具厚度 模具厚度 H < 中 20 30見表 3而該套模具厚度 H==201合要求 開模行程和推出機構的校核 開模行程校核 H≧ 2+(5~ 10) 式中 取 2701取 202取 101值計算 符合要求 推 出機構校核 該注塑機推出行程為 70于 0, 符合要求 模架尺寸與注射機拉桿內間距校核 該套模具模架的外形尺寸為 200200注塑機拉桿內間距為 310310符合要求 12 第 5 章 澆注系統(tǒng)的設計 流道設置 1) 主流道尺寸 主流道的作用 主流道的模具,一般不用澆口套,而直接開設在定模板上。 澆口套是注射機噴嘴在注射模具上的座墊,在注射時它承受很大的注射機噴嘴端部的壓力同時由 于澆口套末端通過流道澆口與型腔相連接,所以也承受模具型腔壓力的反作用力。為了 防止?jié)部谔滓驀娮於瞬繅毫Χ粔喝肽>邇龋瑵部谔椎慕Y構上要增加臺肩,并用螺釘緊固在模板上,這樣亦可防止模腔壓力的反作用力而把澆口套頂出。 主流道設計要點 (1) 澆口套的內孔(主流道)呈圓錐形,錐度 2°~ 6°。若錐度過大會造成壓力減弱,流速減慢,塑料形成渦流,熔體前進時易混進空氣,產生氣孔;錐度過小,會使阻力增大,熱量損耗大,表面黏度上升,造成注射困難。 (2) 澆口套進口的直徑 d 應比注射機噴嘴孔直徑 等于或小于注射機噴嘴直徑,在注射成型時會造成死角,并積存塑料,注射壓力下降 ,塑料冷凝后,脫模困難。 (3) 澆口套內孔出料口處(大端)應設計成圓角 r,一般為 3 (4) 澆口套與注射機噴在接觸處球面的圓弧度必須吻合。設球面澆口套球面半徑為 射機球面半徑為 r, 其關系式如下: r+ 1口套球面半徑比注射機噴嘴球面半徑大,接觸時圓弧度吻合的好。 (5) 澆口套長度(主流道長度)應盡量短,可以減少冷料回收量,減少壓力損失和熱量損失。 (6) 澆口套錐度內壁表面粗糙度為 m,保證料流順利,易脫模。 (7) 澆口套不能制成拼塊 結構,以免塑料進入接縫處,造成冷料脫模困難。 (8) 澆口套的長度應與定模板厚度一致,它的端部不應凸出在分型面上,否則會造成合模困難,不嚴密,產生溢料,甚至壓壞模具。 (9) 澆口套部位是熱量最集中的地方,為了保證注射工藝順利進行和塑件質量,要考慮冷卻措施。 根據(jù)所選注射機,則主流道小端尺寸為 13 d = 注射機噴嘴尺寸 + (1) = 2 + 流道球面半徑為 噴嘴球面半徑 + ( 1~ 2) =10+( 1~ 2) = 11 面配合高度 h=3— 5 h=3 主流道長度 盡量小于 60標準模架結合該模具結構取 L=25+20=45流道大端直徑 D=d+2(半錐角 °~ 2 °,取 a=2 °) 澆口套總長 L。 =L+2+h=45+2+3=50口套圖如下: 圖 5口套截面圖 14 分流道設計 1)分流道的作用 分流道式指主流道末端與澆口之間的一段塑料熔體的流動通道。其基本作用是在壓力損失最小的條件下,將來自主流道的 熔融塑料,以較快的速度送到澆口處充模。同時,在保證熔體均勻地分配到各型腔的前提下,要求分流道中殘留的熔融塑料最少,以減少冷料的回收。 2) 設計要點 在多種常見截面當中,圓形截面的壓降是最小的。但由于圓形的分流道必須在上下模板上都加工出半圓槽,工藝性不好,故此設計中采用工藝性更為合理而壓降也比較小且塑料熔體的熱量散失流動阻力均不大的 U 形截面或梯形截面。該模具采用梯形分流道。 3)分流道的形狀及尺寸 分流道可開設在動、定模分型面的兩側或其中任意一側。設計要求其截面形狀應盡量使其比表面積(流道表面積 與其體積之比)小,目的是在溫度較高的塑料熔體和溫度相對較低的模具之間提供較小的接觸面積,以減小熱量損失。分流道大多設置在分型面上,分流道截面形狀一般為圓形、梯形、 U 形、半圓形及矩形等。 ( 1)分流道長度長度應盡量短,且少彎折。 綜合型腔布局尺寸確定該模具分流道的長度為: L=43× 2+85=171( 分流道 ( 2)圓形截面的比表面積最小因此取截面為圓(直徑為 4流道,圖形如下: 圖 5分流道圓形截面圖 ( 3) 分流道的表面粗糙度 由于分流道中與模具接觸的外層塑料迅速冷卻,只有中心部位的塑料熔體的流動狀態(tài)較為理想,因此分流道的內表面粗糙度 不要求很低,一般取 15 m,這樣表面稍不光滑,有助于增大塑料熔體的外層流動阻力。避免熔流表面滑移,使中心層具有較高的剪切 速率。 ( 4)分流道的布置形式 分流道在分型面上的布置與前面所述型腔排列密切相關,有多種不同的布置形式,但應遵循兩方面原則:即一方面排列緊湊、縮小模具板面尺寸;另一方面流程盡量短、鎖模力力求平衡。 本模具的流道布置形式采用平衡式,綜合流道截面形狀考慮我選擇 采用在動定模開分流道,分流道圖如下: 圖 5流道布置圖 口的設計 1) 澆口的作用 澆口是分流道和型腔之間的連接部分,也是注射模具澆注系統(tǒng)的最后部分,通過澆口直接使熔融的塑料進入型腔內。澆口的作用是使從流道來的熔融塑料以較快的速度進入并充滿型腔,型腔充滿塑料后,澆口能迅速冷卻封閉,防止型腔內還未冷卻的熱料回流。 澆口設計與塑料制品形狀、塑料制品斷面尺寸、模具結構、注射工藝參數(shù)(壓力等)及塑料性能等因素有關。澆口的截面要小,長度要短,這樣才能增大料流速度,快速冷卻封閉,便于使塑料制品分離,塑 料制品的澆口痕跡亦不明顯。 塑料制品質量的缺陷,如缺料、縮孔、拼縫線、質脆、分解、白斑、翹曲等,往往都是由于澆口設計不合理而造成的。 2) 澆口設計的基本要點 16 1、 盡量縮短流動距離 澆口位置的安排應保證塑料熔體迅速和均勻地充填模具型腔,盡量縮短熔體的流動距離,減少壓力損失,有利于排除模具型腔中的氣體,這對大型塑件更為重要。 2、 澆口應設在塑件制品斷面較厚的部位 當塑件的壁厚相差較大時,若將澆口開設在塑件的薄壁處,這時塑料熔體進入型腔后,不但流動阻力大,而且還易冷卻,以致影響了熔體的流動距離,難以保證其充滿整個型腔。 另外從補縮的角度考慮,塑件截面最厚的部位經常是塑料熔體最晚固化的地方,若澆口開設在薄壁處,則厚壁處極易因液態(tài)體積收縮得不到收縮而形成表面凹陷或真空泡。因此為保證塑料熔體的充分流動性,也為了有利于壓力有效地傳遞和比較容易進行因液態(tài)體積收縮時所需的補料,一般澆口的位置應開設在塑件壁最厚處。 3、 必須盡量減少或避免熔接痕 由于成型零件或澆口位置的原因,有時塑料充填型腔時造成兩股或多股熔體的匯合,匯合之處,在塑件上就形成熔接痕。熔接痕降低塑件的強度,并有損于外觀質量,這在成型玻璃纖維增強塑料的制件時尤為嚴重。有時 為了增加熔體的匯合,匯合之處,在塑件上就形成熔接痕。熔接痕降低塑件的強度,并有損于外觀質量,這在成型玻璃纖維增強塑料的制件時尤其嚴重。一般采用直接澆口、點澆口、環(huán)形澆口等可以避免熔接痕的產生,有時為了增加熔體匯合處的溶接牢度,可以在溶接處外側設一冷料穴,使前鋒冷料引如其內,以提高熔接強度。 在選擇澆口位置時,還應考慮熔接的方位對塑件質量及強度的不同影響。 4、 應有利于型腔中氣體的排除 要避免從容易造成氣體滯留的方向開設澆口。如果這一要求不能充連接。 3) 澆口的類型 澆口的形式多種多樣,但常用的澆口有如下 11 種: 直接澆口、側澆口、扇形澆口、平縫澆口、環(huán)形澆口、盤形澆口、輪輻澆口、爪形澆口、點澆口、潛伏澆口、護耳澆口等。 本設計采用側澆口,截面為圓形,側澆口尺寸計算如下: ~ A 有 ≈ 2108b= 17 t≈ L=面圖如下: 圖 5口截面圖 18 第 6 章 成型零件的設計與計算 所謂成型零件的工作尺寸是指成型零件上直接構成型腔腔體的部位的尺寸,其直接對應塑件的形狀與尺寸。鑒于影響塑件尺寸精度的因素多且復雜,塑件本身精度也難以達到高精度,為了計算簡便,規(guī)定: 塑件的公差 塑件的公差規(guī)定按單向極限制,制品外輪廓尺寸公差取負值“ ?? ”,制品叫做腔尺寸公差取正值“ ?? ”,若制品上原有公差的標注方法與上不符,則應按以上規(guī)定進行轉換。而制品孔中心距尺寸公差按對稱分布原則計算,即取±△ /2。模具制造公差 實踐證明,模具制造公差可取塑件公差的 ~61 ,即δ z= ?)61~31( ,現(xiàn)取 3? 。而且按成型加工過程中的增減趨向取“ +”、“ -”符號,型腔尺寸不斷增大,則取“ +δ z” ,型芯尺寸不斷減小則取“ -δ z”,中心距尺寸取“ 2z?? ”。 模具的磨損量 實踐證明,對于一般的中小型塑件,最大磨損量可取塑件公差的 1/6,對于大型塑件則取 6? 以下。另外對于型腔底面(或型芯端面),因為脫模方向垂直,故磨損量δ c=0。 塑件的收縮率 塑件成型后的收縮率與多種因素有關 ,通常按平均收縮率計算。 =( 1% + 3%) / 2 = 2% 課本附錄 %、 % 模具在分型面上的合模間隙 由于注射壓力及模具分型面平面度的影響,會導致動模、定模注射時存在著一定的間隙。一般當模具分型的平面度較高、表面粗糙度較低時,塑件產生的飛邊也小。飛邊厚度一般應小于是 件尺寸可按公差 14486準中的 5級精度選取。 2 ? 19 型腔的徑向尺寸與深度 根據(jù)公式 : 式中△在塑料成型工藝與模具結構書 18頁表 1 ??????? ???043)1( 徑向尺寸 ???? 011 )43(=( 2% - 3 =向尺寸 ???? 011 )43(=( 2% - 3 =腔深度尺寸計算 根據(jù)公式 : ???????? ???0S 32)1(H ???? 011 )32( = (17 +17 * 2% - 2/3 * 0+ = 型腔圖: 20 圖 6腔圖 型芯的徑向尺寸與深度 根據(jù)公式 : l M= 043)1(?????? ??? 小頭徑向尺寸 0111 )43( m ??????= ( 2% +0 = 頭徑向尺寸 0222 )43(m ??????=( 2% +0 據(jù)公式: h M= 032)1(???????? ??? 21 型芯高度尺寸 h 2M= 032)1(???????? ??? = ( 2% + 2/3× 0 =圖 6芯圖 具型腔側壁的確定 模具型腔在成型過程中受到塑料熔體的高壓作用,用具有足夠的強度和剛度。但是對型腔的壁厚做出精確的力學計算是非常困難的,一般在工廠中經常用經驗數(shù)據(jù)對型腔壁厚進行簡化設計。根據(jù)課本塑料成型工藝與模具結構 99 頁表 3的數(shù)值壁厚 s=20架的確定 根據(jù)型腔的布局可看出,型腔分布尺寸為為 165× 165,有根 據(jù)型腔側壁最小壁厚為 20,再考慮到導柱、導套及連接螺釘布置應占據(jù)的位置和采用推件板推出等各方面的問題,由塑料成型工藝與模具結構書 199 頁確定選用 、模架尺寸為 250250標準模架,即可符合要求。 22 圖 6架 第 7 章 合模導向機構設計 向與定位機構設計 1)合模導向機構的總體設計 導向機構對于塑料模具是必不可少的部件,因為模具在閉合時有一定的方向和位置,所以必須設有導向機構。 導向機構的主要作用:定位、導向、承受一定側壓等作用。 a. 定位作用 為避免模具裝配時方位 搞錯而損壞模具,并且在模具閉合后使型腔保持正確的形狀,不至因為位置的偏移而引起塑件壁厚不均。 b. 導向作用 動定模合模時,首先導向機構接觸,引導動定模正確閉合,避免凸模或型芯先進入型腔以保證不損壞成型零件。 c. 承受一定側壓力 塑料注入型腔過程中會產生單向側壓力,或由于注射機精度的限制使導柱在工作中承受一定的側壓力,此時,導柱能承擔一部分側壓力。 2)導柱的設計 導柱的長度必須比凸模端面要高出 6~ 8 毫米。以免導柱未導正方向而凸模先進入型腔與其相碰而損壞。 柱的端部做成錐形或球形的 先導部分,使導柱能順利進入導柱孔。 導柱應具有硬而耐磨的表面、堅韌而不易折斷的內芯,因此,多采用 23 低碳鋼經滲碳淬火處理。 或碳素工具鋼( 淬火處理硬度 55,導柱滑動部位按需要可設油槽。 配合部分光潔度要求 6 級,此外,導柱的選擇還應跟椐模架來確定。由于模架較大 (200× 200)所以設計成四導柱,此模架導柱簡圖如下所示 : 圖 7柱圖 24 3)導套的設計 導套可以直接開設在模板上,且設計為通孔, 這種形式的孔加工簡單,適用于生產批量小,精度要求較高的模具。 對導套的結構主要有四點要求,分述如下: (1)、形狀為了使導柱進入導套比較順利,在導套的前端倒圓角,導柱孔最好打通,否則導柱進入未打通的導柱孔時,孔內空氣無法逸出而產生壓力,給導柱的進入造成阻力。 (2) 材料可用淬火銅或銅等耐磨材料制造,但其硬度應低于導柱硬度,這樣可以改善磨擦,以防止導柱或導套拉毛。 (3) 導套的精度與配合一般 A 型用二級精度過度配合, B 型用二級精度靜配合。 (4) 光潔度配合部分光潔度要求七級。 導套的選擇應根據(jù)模板的 厚度來確定,材料為 到 55,或采用20 鋼滲碳 ,淬硬到 由于模具的結構不同,該模架上用的導套如下圖: 圖 7套圖 25 4)導柱、導套的布置 根據(jù)模具的形狀的大小,在模具的空閑位置開設導柱孔和導套孔,常見的導柱有 2 至 4 根不等,其布置原則必須保證定模只能按一個方向合模,此設計常用四根相同的導柱布置在定動模固定板的四角。 第 8章 脫模機構設計 脫模機構設計 1) 在注射成型 的每一循環(huán)中,塑件必須由模具 型腔中脫出,脫出塑件的機構稱為脫模機構或頂出機。 ( 1)脫模機推出力應施于塑件剛性和強度最大的部位,作用面積也應盡可能大一些,以防塑件變形或損壞。 ( 2)力求良好的塑件外觀,在選擇頂處位置時,應盡量設在塑件內部或對塑件外觀影響不大的部位。在采用推桿脫模時尤其要注意這個問題。 (3)結構合理可靠,脫模機構應工作可靠,運動靈活,制造方便,更換容易且具有足夠的剛度和強度。 2)脫模機構的分類 脫模機構可按動力來源分類也可按模具結構分類 (1) 按動力來源分類。分為手動脫模、機械脫模、液壓脫模、氣動脫模,本設 計采用液壓脫模。即在注射機上設有專用的頂出油缸,并開模到一定距離后,活塞的動作實現(xiàn)脫模。 按模具結構分類。分為簡單脫模機構、雙脫模機構、順序脫模機構、二級脫模機構、澆注系統(tǒng)脫模機構等。本設計采用的推出機構是推件板推出機構。 推件板推出機構。 其特點是推出力大,且推出力的作用面積大而均勻,運動平穩(wěn),塑件上沒有推出痕跡。 設計時注意事項。為了減小推出過程中推件板和型芯的摩擦,可采用在推件板和型芯間留有 采用 3錐度起到輔助定位作用,防止推件板偏心而引起溢料。 綜合 分析用推桿推出機構,綜合該模架和塑件的考慮我選用一個塑件用 4個推桿,推桿直徑為 6推桿其簡圖如下: 26 圖 8桿 結束語 課程 設計接近了尾聲 真的研究老師給的題目,其次,老師對題目的講解要一絲不茍的去聽去想,因為只有都明白了,做起設計就會事半功倍,如果沒弄明白,就迷迷糊糊的去選題目做設計,到頭來一點收獲也沒有。在這段時間里,也暴露了自己很多問題,第一、不夠細心比如由于粗心大意算錯了數(shù)導致設計的零件不能正確的裝配。第二,是在學習態(tài)度上 ,這次課設是對我的學習態(tài)度的一次檢驗。我的第一大心得體會就是作為一名設計人員,要求具備的首要素質絕對應該是嚴謹。我們這次實習所遇到的多半問題多數(shù)都是由于我們不夠嚴謹。第三,在做人上,我認識到,無論做什么事情,只要你足夠堅強,有足夠的毅力與決心,有足夠的挑戰(zhàn)困難的勇氣,就沒有什么辦不到的。在這次難得的 課程 設計過程中我鍛煉了自己的思考能力和對次感謝老師的輔導以及同學的幫助,是他們讓我有了一個更好的認識,無論是學習還是生活,生活是實在的,要踏實走路。 課程 設計時間雖然不長,但我學習了很多的東西 ,使我眼界打開,感受頗深。 這篇說明書的編寫以及修改的過程,也是我越來越認識到自己知識與經驗缺乏的過程。雖然,我盡可能地收集材料,竭盡所能運用自己所學的知識進行設計說明書的編寫,但還是存在許多不足之處,有待改進。請各位評委老師多批評指正,讓我在今后的學習中學到更多。同時也對這段時間老師給予的幫助表示感謝 ! 27 參考文獻 德群 械工業(yè)出版社, 2005 柳 北京 :化工工業(yè)出版社, 2008 《機械制圖》 等教育出版社, 1993 塑料注射模具設計實用手冊 . 北京 :航空工業(yè)出版社 , 1998 塑料注塑模結構與設計 華大學出版社, 2004 塑料成型工藝與模具結構 械工業(yè)出版社, 2008 塑料模具圖冊 高等教育出版社, 2004 注塑技術與注塑機 學工業(yè)出版社, 2005 模具設計指導 械工業(yè)出版社, 2003 塑料模具設計指導 防工業(yè)出版社, 2008 X 速入門教程 械工業(yè)出版社, 2010 模具設計從入門到精通 械工業(yè)出版社, 2010 塑料模具設計與制造【 M】 等教育出版社, 2004 冷沖壓與塑料成型機械【 M】 械工業(yè)出版社, 1999 亞林 M】 等教育出版社, 2003 模具壽命與材料【 M】 械工業(yè)出版社, 2004 模具材料【 M】 械工業(yè)出版社, 2004 模具標準應用手冊【 M】 械工業(yè)出版社, 1994 塑料成型技術 械工業(yè)出版社, 2002