
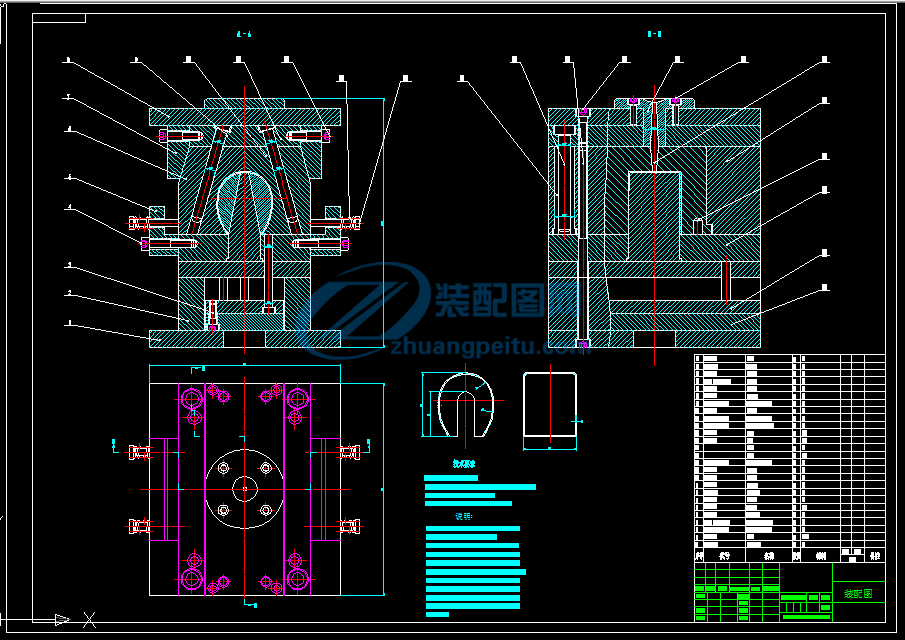
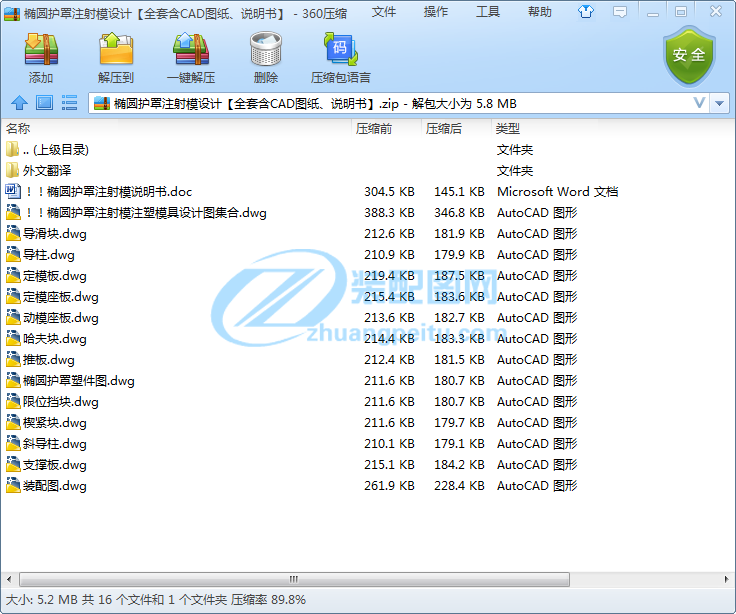
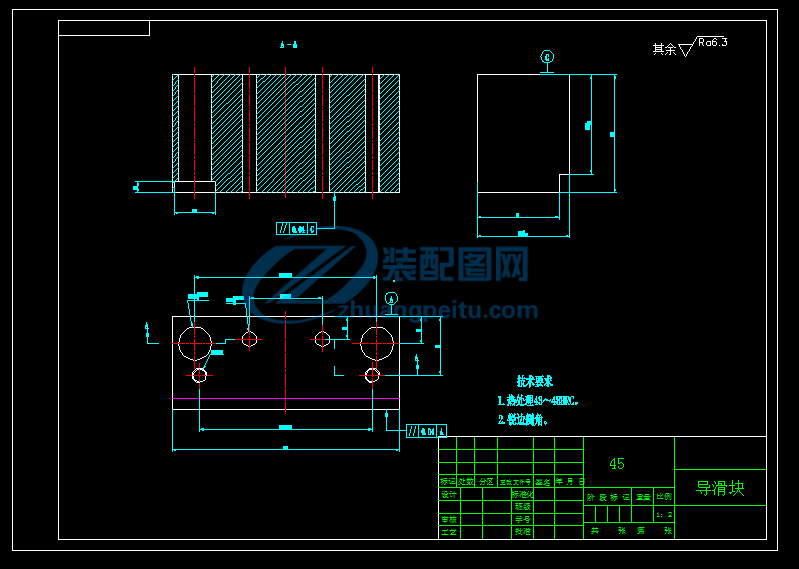
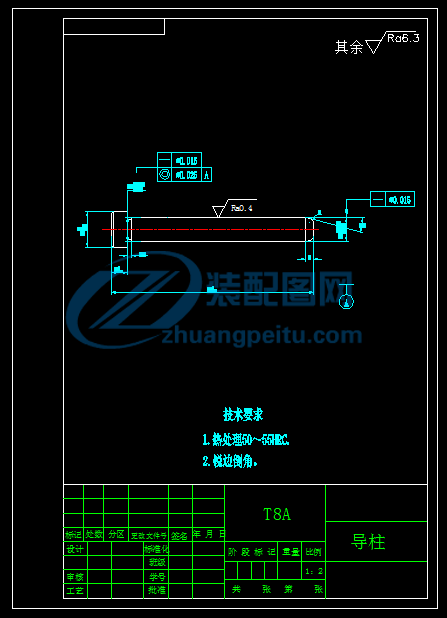
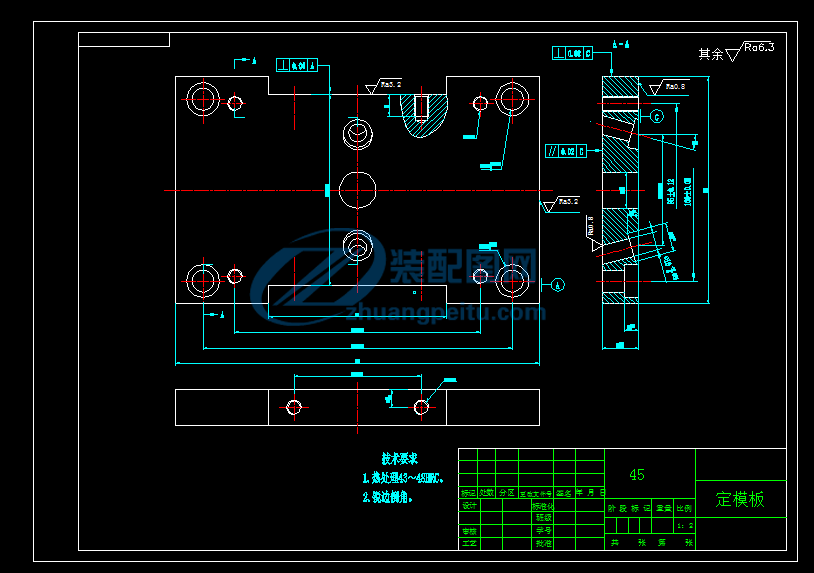
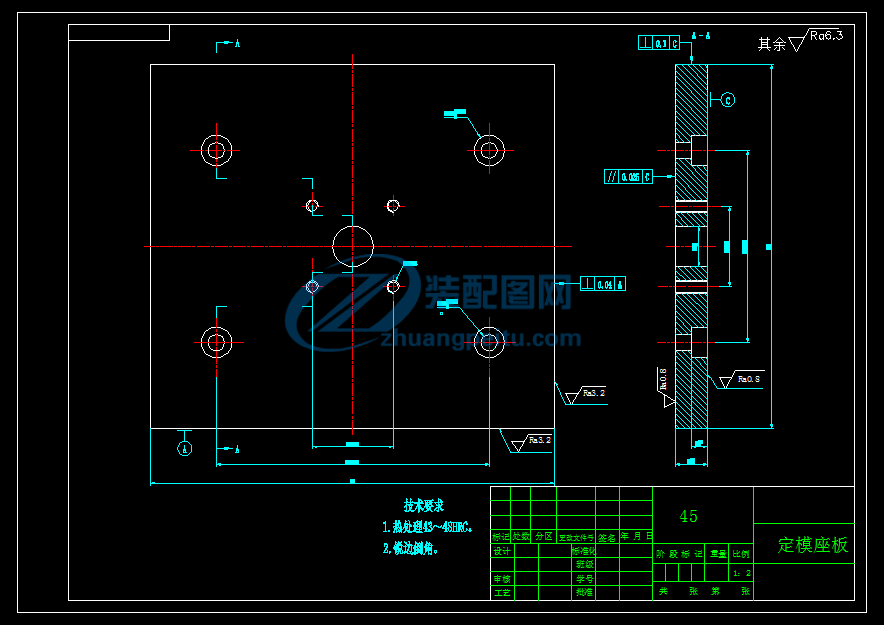
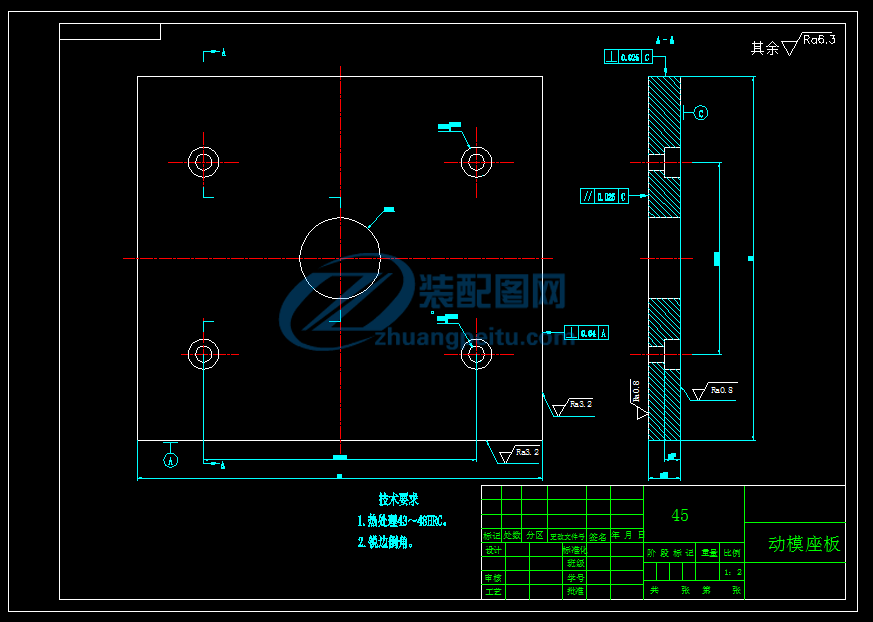
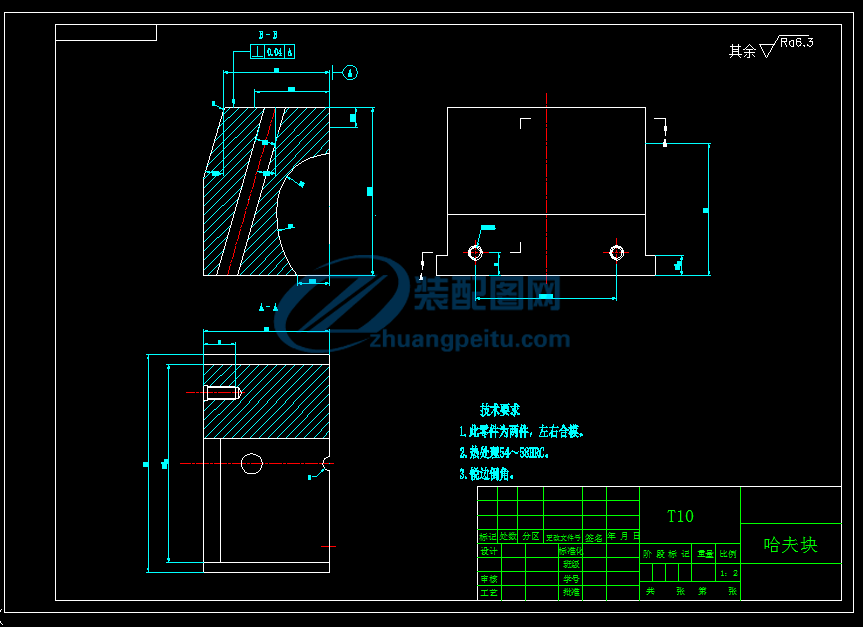
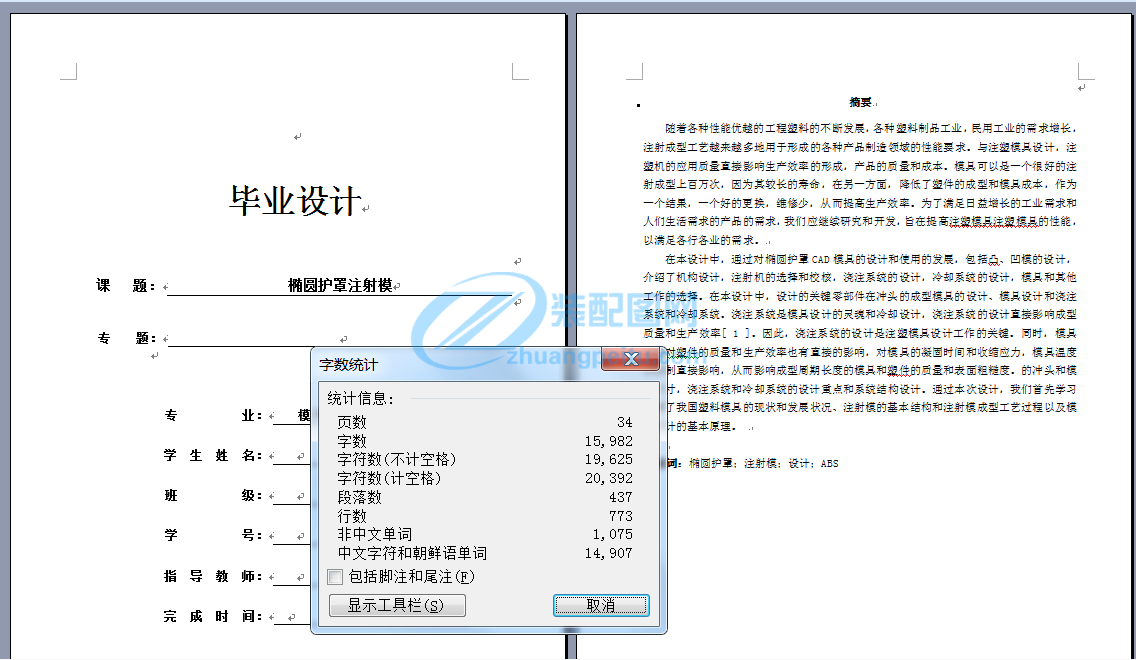
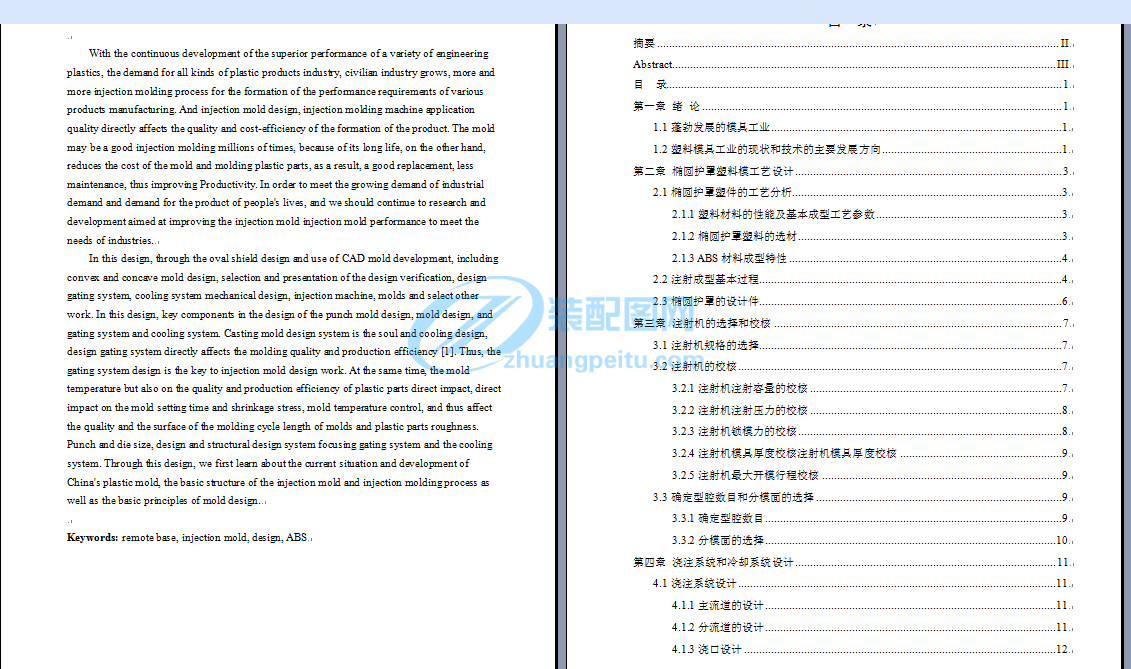
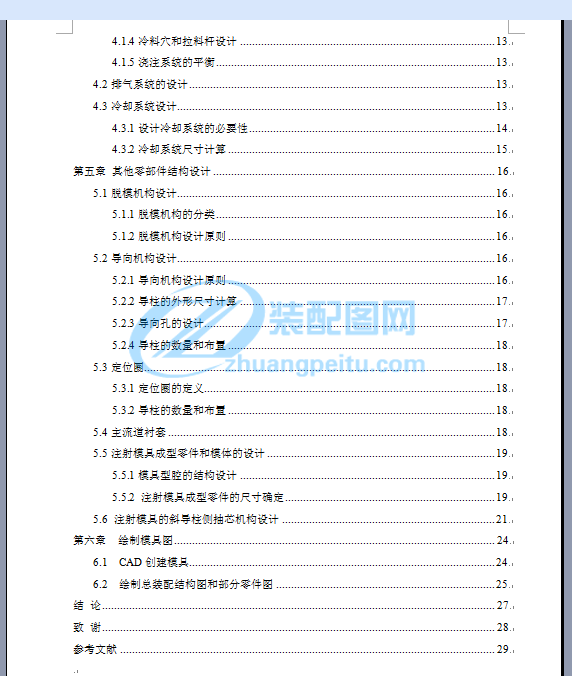
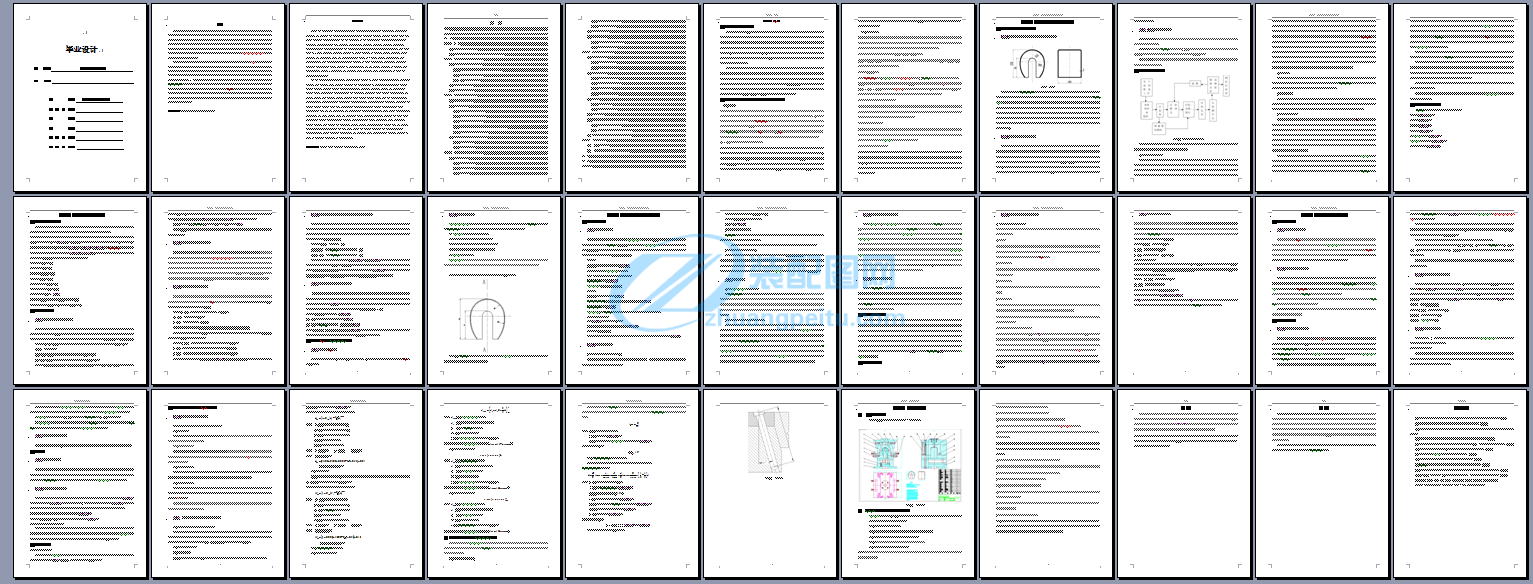
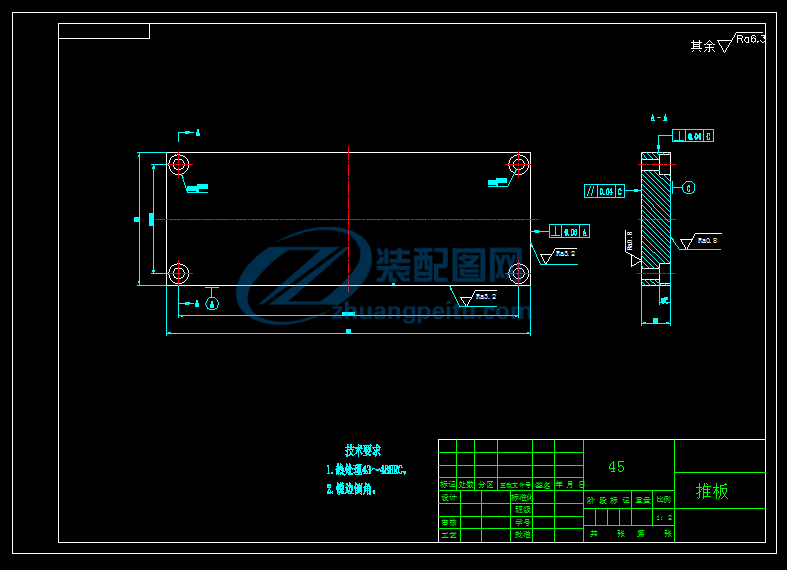
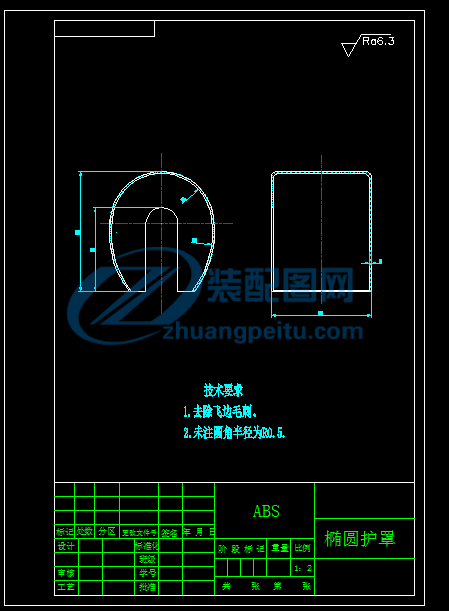
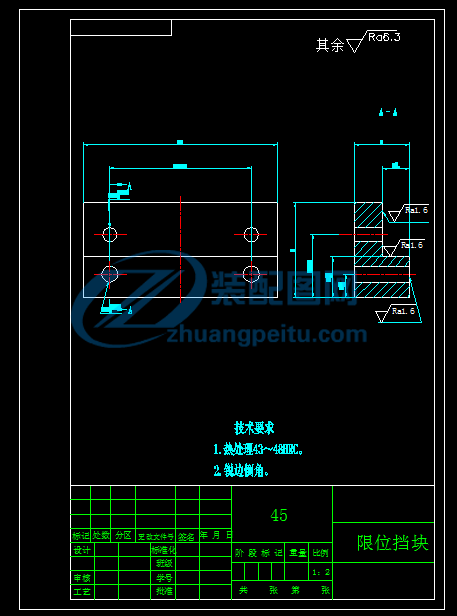

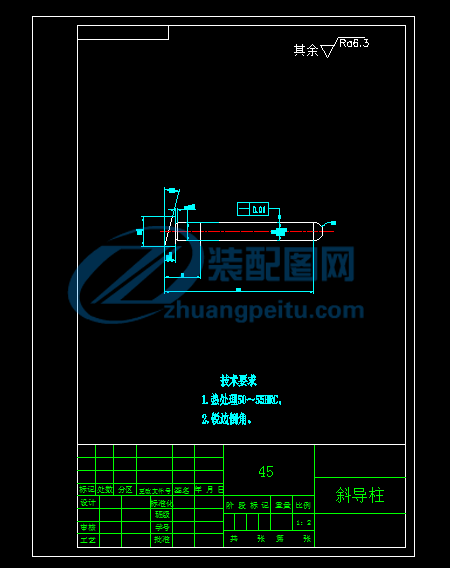
畢業(yè)設計課 題: 橢圓護罩注射模專 題:專 業(yè): 模 具 設 計 與 制 造學 生 姓 名: 班 級: 學 號: 指 導 教 師: 完 成 時 間: 摘要隨著各種性能優(yōu)越的工程塑料的不斷發(fā)展,各種塑料制品工業(yè),民用工業(yè)的需求增長,注射成型工藝越來越多地用于形成的各種產(chǎn)品制造領域的性能要求。與注塑模具設計,注塑機的應用質量直接影響生產(chǎn)效率的形成,產(chǎn)品的質量和成本。模具可以是一個很好的注射成型上百萬次,因為其較長的壽命,在另一方面,降低了塑件的成型和模具成本,作為一個結果,一個好的更換,維修少,從而提高生產(chǎn)效率。為了滿足日益增長的工業(yè)需求和人們生活需求的產(chǎn)品的需求,我們應繼續(xù)研究和開發(fā),旨在提高注塑模具注塑模具的性能,以滿足各行各業(yè)的需求。在本設計中,通過對橢圓護罩 CAD 模具的設計和使用的發(fā)展,包括凸、凹模的設計,介紹了機構設計,注射機的選擇和校核,澆注系統(tǒng)的設計,冷卻系統(tǒng)的設計,模具和其他工作的選擇。在本設計中,設計的關鍵零部件在沖頭的成型模具的設計、模具設計和澆注系統(tǒng)和冷卻系統(tǒng)。澆注系統(tǒng)是模具設計的靈魂和冷卻設計,澆注系統(tǒng)的設計直接影響成型質量和生產(chǎn)效率[ 1 ]。因此,澆注系統(tǒng)的設計是注塑模具設計工作的關鍵。同時,模具溫度對塑件的質量和生產(chǎn)效率也有直接的影響,對模具的凝固時間和收縮應力,模具溫度的控制直接影響,從而影響成型周期長度的模具和塑件的質量和表面粗糙度。的沖頭和模具尺寸,澆注系統(tǒng)和冷卻系統(tǒng)的設計重點和系統(tǒng)結構設計。通過本次設計,我們首先學習了解了我國塑料模具的現(xiàn)狀和發(fā)展狀況、注射模的基本結構和注射模成型工藝過程以及模具設計的基本原理。 關鍵詞:橢圓護罩;注射模;設計;ABSAbstractWith the continuous development of the superior performance of a variety of engineering plastics, the demand for all kinds of plastic products industry, civilian industry grows, more and more injection molding process for the formation of the performance requirements of various products manufacturing. And injection mold design, injection molding machine application quality directly affects the quality and cost-efficiency of the formation of the product. The mold may be a good injection molding millions of times, because of its long life, on the other hand, reduces the cost of the mold and molding plastic parts, as a result, a good replacement, less maintenance, thus improving Productivity. In order to meet the growing demand of industrial demand and demand for the product of people's lives, and we should continue to research and development aimed at improving the injection mold injection mold performance to meet the needs of industries.In this design, through the oval shield design and use of CAD mold development, including convex and concave mold design, selection and presentation of the design verification, design gating system, cooling system mechanical design, injection machine, molds and select other work. In this design, key components in the design of the punch mold design, mold design, and gating system and cooling system. Casting mold design system is the soul and cooling design, design gating system directly affects the molding quality and production efficiency [1]. Thus, the gating system design is the key to injection mold design work. At the same time, the mold temperature but also on the quality and production efficiency of plastic parts direct impact, direct impact on the mold setting time and shrinkage stress, mold temperature control, and thus affect the quality and the surface of the molding cycle length of molds and plastic parts roughness. Punch and die size, design and structural design system focusing gating system and the cooling system. Through this design, we first learn about the current situation and development of China's plastic mold, the basic structure of the injection mold and injection molding process as well as the basic principles of mold design.Keywords: remote base, injection mold, design, ABS目錄目 錄摘要 .IIAbstractIII目 錄1第一章 緒 論11.1 蓬勃發(fā)展的模具工業(yè) 11.2 塑料模具工業(yè)的現(xiàn)狀和技術的主要發(fā)展方向 1第二章 橢圓護罩塑料模工藝設計32.1 橢圓護罩塑件的工藝分析 32.1.1 塑料材料的性能及基本成型工藝參數(shù) 32.1.2 橢圓護罩塑料的選材 32.1.3 ABS 材料成型特性 .42.2 注射成型基本過程 42.3 橢圓護罩的設計件 6第三章 注射機的選擇和校核73.1 注射機規(guī)格的選擇 73.2 注射機的校核 73.2.1 注射機注射容量的校核 73.2.2 注射機注射壓力的校核 83.2.3 注射機鎖模力的校核 83.2.4 注射機模具厚度校核注射機模具厚度校核 93.2.5 注射機最大開模行程校核 93.3 確定型腔數(shù)目和分模面的選擇 93.3.1 確定型腔數(shù)目 93.3.2 分模面的選擇 10第四章 澆注系統(tǒng)和冷卻系統(tǒng)設計114.1 澆注系統(tǒng)設計 114.1.1 主流道的設計 114.1.2 分流道的設計 114.1.3 澆口設計 124.1.4 冷料穴和拉料桿設計 134.1.5 澆注系統(tǒng)的平衡 134.2 排氣系統(tǒng)的設計 134.3 冷卻系統(tǒng)設計 134.3.1 設計冷卻系統(tǒng)的必要性 144.3.2 冷卻系統(tǒng)尺寸計算 15第五章 其他零部件結構設計165.1 脫模機構設計 165.1.1 脫模機構的分類 165.1.2 脫模機構設計原則 165.2 導向機構設計 165.2.1 導向機構設計原則 165.2.2 導柱的外形尺寸計算 175.2.3 導向孔的設計 175.2.4 導柱的數(shù)量和布置 185.3 定位圈 185.3.1 定位圈的定義 185.3.2 導柱的數(shù)量和布置 185.4 主流道襯套 185.5 注射模具成型零件和模體的設計 195.5.1 模具型腔的結構設計 195.5.2 注射模具成型零件的尺寸確定 .195.6 注射模具的斜導柱側抽芯機構設計 .21第六章 繪制模具圖246.1 CAD 創(chuàng)建模具 246.2 繪制總裝配結構圖和部分零件圖 .25結 論27致 謝28參考文獻29第一章 緒論第一章 緒 論1.1 蓬勃發(fā)展的模具工業(yè)從第二十世紀到 80 年代初,工業(yè)發(fā)達國家的模具工業(yè)已從機床產(chǎn)業(yè)中分離出來,和一個獨立的工業(yè)部門的發(fā)展,其產(chǎn)值已超過機床工業(yè)的價值。在以下的發(fā)展模具技術,模具行業(yè)也被廣泛應用在汽車,航空,電子,電器的投資,儀器儀表,輕工,行業(yè)中塑料和其他日常必需品。在發(fā)達國家,人們認為,沒有死亡,沒有高質量的產(chǎn)品。和模具,享受到“關鍵 ”產(chǎn)業(yè)發(fā)展; “一個企業(yè)的心”;“富裕社會動態(tài)”等聲譽。改革開放以來,在中國模具工業(yè)的發(fā)展也很迅速。近年來,每年以 15%的增長率快速發(fā)展。模具企業(yè)也如雨后春筍,蓬勃發(fā)展,迅速成長。隨著模具工業(yè)規(guī)模的不斷擴大,中國的模具技術水平也有較大的提高可以大,責任,體現(xiàn)了現(xiàn)代模具精密模具的設計制造水平,模具零件的已達到國際先進水平。雖然中國模具工業(yè)有了長足的進步,一些模具已達到國際先進水平,但無論是數(shù)量和質量還不能滿足國內(nèi)市場的需求,大型,精密,復雜模具每年仍需進口 1000000000 美元。為了降低模具工業(yè)與發(fā)達國家的差距,死在我國正朝著大型,精密,復雜模具的開發(fā);加強模具標準件的應用;幾方面對 CAD/CAM/CAE 技術的推廣,大力發(fā)展。1.2 塑料模具工業(yè)的現(xiàn)狀和技術的主要發(fā)展方向(1)現(xiàn)狀近年來,國外的塑料模具的發(fā)展速度也迅速增長,在許多國家(日本,德國,瑞士,等)的塑料模具行業(yè)的發(fā)展比沖壓模具,塑料模具生產(chǎn)的經(jīng)濟總量占整個模具行業(yè) 1 / 2。大量的塑料模具生產(chǎn)國外主要采用一模多腔,多層模具和多層多腔,多站多腔和其他類型的模具,多層模具已發(fā)展到 64×64 腔,還開發(fā)了特殊的注射成型機的多層模具,每個塑料飲料瓶,杯一些鞋模具的使用多站多腔模具,多達 32 腔飲料瓶模具。日本和一些歐洲國家和美國的注塑模具生產(chǎn)的鋁,因為鋁的導熱系數(shù)比鋼,是鋼的三倍,注塑周期可縮短為 25 ~ 30%,和模具的重量大大降低。塑料模具的發(fā)展是隨著塑料工業(yè)的發(fā)展,在我國起步比較晚,但是,發(fā)展很快,尤其是在最近幾年,無論在質量上有了很大的發(fā)展,技術和制造能力,取得了巨大的成就。中國 30 年的發(fā)展歷程,走過 90 年國外塑料模具的發(fā)展,現(xiàn)在有相當規(guī)模。1987 我有塑料產(chǎn)量已達到 2970000 噸,在世界排名第五?,F(xiàn)在,中國的塑料工業(yè)已形成完整的具有相當規(guī)模,系統(tǒng)設計技術,塑料模具的設計與制造技術的 CAD 技術的發(fā)展和應用,caabs技術,具有相應的。塑料生產(chǎn),成型,塑料機械及設備。模具&;模具工業(yè)和科學研究等,具有一定規(guī)模的發(fā)展。(2)發(fā)展趨勢隨著人類社會的不斷進步不斷發(fā)展和高新技術,人們對產(chǎn)品的要求越來越高,因此我們必須大力發(fā)展模具設計技術。也是塑料模具設計技術世界給予了高度的重視和關注,并投入大量的研究和開發(fā)。國際塑料模具的發(fā)展未來主要對以下幾個方面:在模具設計和制造中全面推進 CAD/CAM/CAE 技術CAD/CAM /CAE 技術是模具技術發(fā)展中的一個重要里程碑證明了 CAD/CAM/CAE技術是模具設計制造的發(fā)展方向。注射模 CAD 實用塑料模具模具流或 C 流軟件和塑料模具模具冷卻或 C -酷軟件已商品化,邁向實用模具CAD 方向。中國政府也十分重視注塑模具 CAD 的實踐過程。組織了一個“研究注塑模具的 CAD / CAM / CAE 集成系統(tǒng)的八五個“國家重點科技攻關項目 “”。目前,美國的 PSP 公司以及專家系統(tǒng),可以幫助模具設計者解決問題的專家知識的注塑模具。塑料模具專用材料的研究與開發(fā)目前,塑料模具鋼的種類有:基本型,預硬化和時效硬化型,熱處理淬火,馬氏體時效鋼模具及粉末冶金鋼。在“八五” 期間,國家組織了許多鋼鐵廠單位塑料模具鋼特殊系列的研究和發(fā)展,這將進一步擴大和提高塑料模具鋼。控制模具及塑料工程密切配合機械技術和電子技術的發(fā)展,越來越多的使用數(shù)控加工方法,計算機程序控制的數(shù)字顯示,實現(xiàn)高層次,多工位加工,使塑膠模具的生產(chǎn)質量和效率的新飛躍。激光成形技術是在塑料模具型腔加工中取得了巨大的成功。模具拋光自動化,智能化模具表面加工是模具加工未能很好解決的難題之一。顯著的模具和工件表面質量的服務生活質量的模具表面的影響,我國仍處于手工研磨和拋光,不僅效率低(約占整個模具周期的 1/3),工人勞動強度大,質量不穩(wěn)定,制約了我國模具處理到一個更高的水平。因此,在拋光的自動化,智能化是重要的發(fā)展趨勢。日本已開發(fā)的數(shù)控磨床,自動拋光可實現(xiàn)三維曲面模具。第二章 橢圓護罩塑料模工藝設計第二章 橢圓護罩塑料模工藝設計2.1 橢圓護罩塑件的工藝分析2.1.1 塑料材料的性能及基本成型工藝參數(shù)圖 2-1 工件圖塑料是聚合物的高彈態(tài)正常溫度。它是基于樹脂(聚合物)為主要成分,添加各種添加劑可以改善加工性能和使用性能,在一定的溫度,壓力,溶劑效應,利用模具可成型為塑件必須的形狀和大小,可保持一類材料的形成正常的溫度和壓力下,品種,和不同的塑料有不同的表現(xiàn)。塑料普遍具有重量輕,密度小的優(yōu)點,比強度高,電,熱,聲和優(yōu)良的絕緣性能,耐腐蝕性強、耐磨性強的光學性能,優(yōu)良的。在許多方面的塑性成形工藝特點的性能,一些操作相關的一些特征,直接影響成型方法和工藝參數(shù)的選擇。熱塑性塑料的成型工藝參數(shù),包括收縮特性,流動性,相容性,吸濕性和熱靈敏度和熱力學性質,結晶度和取向[1]2.1.2 橢圓護罩塑料的選材塑料材料是根據(jù)材料的選擇和使用,作為橢圓護罩,他不需要一個很大的負載,其工作溫度不高,所以要求的耐熱性不高。根據(jù)要求和條件似乎使用范圍,結構材料,一般的塑料可以滿足他們的要求,所以選擇在材料橢圓護罩材料。為塑料材料,一般的結構主要有高,低密度聚乙烯,聚丙烯,聚碳酸酯,有機玻璃,ABS,HIPS,玻璃纖維增強樹脂和環(huán)氧-丙烯酸酯共聚物丙烯晴等。但基于通過塑料件注射模具的設計,并根據(jù)在優(yōu)良的初步選擇注塑成型材料,低密度聚乙烯,聚丙烯,ABS,聚碳酸酯和其他四種材料作為原材料制造樹脂螺釘。2.1.3 ABS 材料成型特性①無定形塑料,液體培養(yǎng)基中,吸濕性小,一般不需要很大程度上干,也可以得到塑件的表面質量更好。②材料的溫度高,模溫高,原料分解 270 度的高溫,高精度要求的塑件,模具溫度應 50-60 度高光澤,高,耐熱塑料零件,模具溫度應 60-80 度。③如果出現(xiàn)水印,需要提高物料的流動性,采取高模量和高的材料的溫度,溫度,或改變澆口位置的方法。2.2 注射成型基本過程圖 2.1. 注射成型基本過程生產(chǎn)準備工作一般,為了使注塑生產(chǎn)的順利進行,確保產(chǎn)品質量,在生產(chǎn)前的預處理,滾筒洗衣機,預熱插入和選擇脫模劑的制備。1,原材料的預處理原料的預處理包括三個方面:一是檢查質量,成型材料的分析。這一部分包括測試材料的水分含量,外觀和顏色,無雜質,顆粒,并測試其熱穩(wěn)定性,流動性,收縮率指標。粉狀物料,在注塑之前還需要制成顆粒劑。二是,著色。根據(jù)塑件成型的部分項目需要時,成型材料中添加一個顏色或色劑材料,所需的顏色。粉狀或粒狀熱塑性塑料的著色,第二章 橢圓護罩塑料模工藝設計5與直接法和間接法兩種方法實現(xiàn)。前者稱為著色的方法,它是天然的彩色塑料著色劑和簡單的混合細粉可直接用于成型,或其他然后用于成型塑化。該方法比較簡單,容易操作。與間接染色法相比是比較困難的,它需要被稱為“塑料粒子、彩色塑料顆粒高的顏料濃度色母比例稱重放入攪拌機,攪拌,然后發(fā)送到成型設備的使用。其步驟簡單,容易著色著色部分分散均勻,色澤鮮艷,無色素的粉塵污染,并能實現(xiàn)著色過程自動化。但是由于天然彩色塑料顆粒和簡單的混合,沒有混合功能或成型設備的混合功能差的需要,所以當形成顏色均勻性高的產(chǎn)品不需要為基礎的成型材料著色。三,預熱和干燥。材料的吸濕性和粘性的水阻力,預熱干燥按水分的要求允許的注射成型工藝,以在材料和揮發(fā)水分太多出去,成型后的產(chǎn)品出現(xiàn),防止泡沫和裂紋缺陷,而且可以避免在注水時間的退化的發(fā)生。但是,吸濕性和粘性的水不結實的材料,如包裝儲存也不好的預熱和干燥。2,清洗桶如果你需要在塑料品種產(chǎn)量的變化,在熱分解或降解反應出現(xiàn)的時間形成過程中發(fā)現(xiàn)的材料和顏色更換或清洗更換,需要注射機料筒。通常,桶注塞式機存儲量大,必須拆卸和清洗機筒,螺桿機筒,可用于清潔空氣噴射的方法。3,預熱插入這一步是用一個塑料部件,主要用于插入,因為金屬和塑料收縮率不同,導致插入周圍的塑料易收縮應力和裂縫,為了防止這種現(xiàn)象的發(fā)生,在成形前可插入的預熱溫度,減少它融化的塑料在成型,避免或抑制插入周圍的塑性收縮應力和裂紋的發(fā)生。4,脫模劑的選擇常用的釋放劑,硬脂酸鋅,液體石蠟(白油)和硅油。除了硬脂酸鋅不能用于聚胺,三釋放劑一般使用塑料,特別是硅油脫模效果是最好的,只要模具應用時間,可長期釋放,但價格昂貴。硬脂酸鋅通常用于高溫模具和液體介質中使用低模具溫度石蠟。此外,不軟產(chǎn)品含有橡膠或透明使用脫模劑產(chǎn)品,否則會影響產(chǎn)品的透明度。加料:計量將粒料和粉料加入料斗,通過料斗進入注射機料筒,物料一般是在注射機的料筒中塑化。通過對塑化計量的計算設定好后,物料在設定的計量中塑化完全,即粒料和粉料變成塑料熔體后,注射模閉合,注射機注射充模。注射成型,注射成型一般分為模流,壓力和流量的回補縮的三個階段。模流指的過程中熔體注射將塑化好進入模腔。在注射過程中,注射壓力是隨時間而變化的,流動的時期,噴射壓力和噴嘴處的壓力急劇上升,而腔(柵極端子)壓力接近于零,所以注射壓力主要是用來克服阻力,熔體在模腔中的思想。在填充過程中,熔體流入模腔,模腔壓力急劇上升,注入壓力和噴嘴的壓力也將增加到最大,然后停止變化,在注射壓力對熔體中扮演兩個角色的時候,一是要克服在模具型腔中的流動阻力的液體,兩一定程度的壓實融化。包裝料,包裝進料階段是指從熔體充滿型腔螺桿機筒內(nèi)到目前為止重新開始。保壓壓力是指熔體的注射壓力,模腔繼續(xù)壓實過程,進給保持過程中,在冷卻腔注射機逐漸開始由于成型收縮率與美聯(lián)儲的行動出現(xiàn)熔體?;亓魇侵冈跈C筒柱塞或螺桿后退(即,除保壓后) ,熔體對回澆口和流道方向流動。冷卻:冷卻從大門到產(chǎn)品發(fā)布,凍結時間整形的日期,這是注射成型過程的最后階段。需要注意的問題,在這個階段中模腔壓力,冷卻部分的密度,熔體在模和脫模條件等。的后處理部分:產(chǎn)品從模具中出現(xiàn),由于塑料成型過程中熔體的流動行為的影響的溫度和壓力是非常復雜的,再加上不均勻的熔體流動前沿和填充的范圍塊模具冷卻后率往往會出現(xiàn)一些不均勻的結晶,取向和收縮率的部分,導致產(chǎn)生相應的結晶,取向和收縮應力,除了脫模后變形導致實際的結果,也可能使機械零件能量轉換的光學性能,和表面質量,甚至開裂,為了解決一系列的問題,我們必須在相應的后處理部分。當注射過程完成后,我們將產(chǎn)品發(fā)布,放電,清洗模具,可總回筒重新塑化注射成型周期,開始循環(huán)。2.3 橢圓護罩的設計件該塑件經(jīng)測量所得,其基本幾何值為:密度:p=0.9g/cm3;體積:V=21cm3;質量:M=18.9g;長度:L=150mm;塑件平均寬度:B=60mm;投水平投影面積:S=73.4cm2;制件表面積:S=194.3cm2第三章 注射機的選擇和校核3.1 注射機規(guī)格的選擇注塑機是用于塑料注塑成型的主要設備,按其形態(tài)可分為立式,臥式,矩形型三種注射機。通過塑料在塑化筒在分可分為兩種,活塞式和螺桿式注塑機。在這里,我們確定的初始注射機的規(guī)格通過腔的假設的數(shù)目。初步設計模腔個數(shù)為兩個,ABS 材料的密度 p 為 p=0.9g/cm3(0.9~0.91) 。通過測量所得出塑件的體積( V)和質量(M)以及水平投影面積(S)分別為 V=21cm3、M=18.9g 、S=73.4cm2。一模設計兩個模腔,那么每次注射機的注射量必須大于:2M= 2×21cm3=42cm3。根據(jù)注射機的最大注射量初步選擇型號為 XS?Z?60 的注射機,其工藝參數(shù)如下:螺桿直徑/mm:φ38 注射容量 cm3:60注射壓力/105Pa:122 鎖模力/10KN:500最大成型面積/cm2:130 模板最大行程/mm:180定位孔直徑/mm: 55mm模具厚度/mm:(最大):200(最?。?0噴嘴:(球半徑/mm):12(孔直徑/mm):φ43.2 注射機的校核3.2.1 注射機注射容量的校核模具設計時,必須是得在一個注射成型周期內(nèi)所需注射的塑件料溶體的容量或質量在注射機額定注射量的 80%以內(nèi),且在一個注射成型周期內(nèi),需注射入模具內(nèi)的塑料溶體的容量和質量,應為制件和澆注系統(tǒng)兩部分容量和質量之和,即 V=nVn+Vj 或M=nMn+Mj式中:V(M)——一個成型周期內(nèi)所需要注射的塑料容積和質量,cm3 或 g;n—— 型腔數(shù)目;Vn(Mn)——單個塑件的容量或質量,cm3 或 g;Vj(Mj )——澆注系統(tǒng)凝料的容量和質量,cm3 或 g;第三章 注射機的選擇和校核故應使 0.8Vn+Vj≤0.8Vg 或 M=0.8Mn+Mj≤0.8Mg 式中: Vg(Mg)——注射機額定注射量,cm3 或 g;將數(shù)據(jù)代入以上不等式(取其中之一的質量不等式來對注射量進行校核)得:M=nMn+Mj=2×18.9+5.5=43.3g≤0.8Mg=0.8×60=48g 滿足要求上式中的:Mj=M 主流道+M 橫澆道+M 分流道+M 澆口+M 拉料鉤≈5.5g材料 ABS 是非熱敏性材料,所以只需對其進行最大注射量即可,不必對其進行最小注射量的校核。3.2.2 注射機注射壓力的校核注射壓力的校核是校驗注射機的最大注射壓力能否滿足制品的成型要求。只有在注射壓力,注射機的額定的一部分以最大注射壓力注射壓力的內(nèi)部調整,注射壓力,注射機大于所需配件。注射壓力時所需的成型,隨著塑料品種的關系,注射機的類型,噴嘴的形狀,形狀零件的澆注系統(tǒng)和其它因素的復雜性??勺⑸涞膲毫κ切枰鶕?jù)確定的塑料成型工藝參數(shù)數(shù)據(jù)建模。根據(jù)塑料成型工藝參數(shù),注塑壓力表檢查 ABS 材料(70 ~ 120MPa)之間,額定注射壓力注射機的選用是 119mpa,注射壓力之間設置,以滿足生產(chǎn)工藝的要求。3.2.3 注射機鎖模力的校核當塑料熔體壓力腔,將產(chǎn)生一個沿軸向推力大的注塑機,大小的推力的鎖模力必須小于注射機,否則將溢流跑料現(xiàn)象鎖模不緊的注射成型中出現(xiàn)。型腔內(nèi)塑料熔體的壓力(MPa )值可根據(jù)以下經(jīng)驗公式算得:P=KPo式中:P —— 型腔內(nèi)塑料熔體的壓力 (MPa)Po —— 注射壓力( MPa)K —— 壓力損耗系數(shù) 0.2~0.4將數(shù)據(jù)代入上式得:P=KPo=(0.2~0.4)×119MPa=23.8MPa~47.6MPa在該次設計中,并基于 ABS 這種塑料上我們?nèi)⌒颓恢腥垠w的平均壓力為:P=30MPa再由公式 T=PS 計算推力大小。式中:T —— 塑料熔體在注射機軸向上的推力( MPa)P —— 型腔內(nèi)塑料熔體的壓力,在此我們?nèi)?P=30MPaS —— 制件與澆注系統(tǒng)在分型面上的投影面積(cm2 )將數(shù)據(jù)代入該公式得:T=PS=30MPa×73.4cm2≈220.2KN≤500KN 滿足要求經(jīng)校核合格。93.2.4 注射機模具厚度校核注射機模具厚度校核最大的注塑機的規(guī)定的最小厚度是指模板關閉達到所需的夾緊力動態(tài)模板,模板之間的最大和最小距離后。因此,模具厚度的設計必須在模具的最大和最小厚度規(guī)定范圍內(nèi)的注射機,否則將不可能獲得的夾緊力的規(guī)定,當模具厚度時,可以加墊。根據(jù)要求模具的厚度必須滿足 HminHHmax式中:H —— 模具厚度 mmHmin —— 注射機允許的最小模具厚度 mmHmax —— 注射機允許的最大模具厚度 mm根據(jù)我們已選擇的注射機得到 Hmin=70mm;Hmax=300mm。根據(jù)已選擇的中小型標準模架中的模板規(guī)格 Bo×L 為 250×250 的模架,根據(jù)模架的布置方式,則模具閉合高度H 為:H=32+A+B+C+h4+2h1。將數(shù)據(jù)代入式中得:H=220mm 將上述的數(shù)據(jù)代入HminHHmax 得:70220300 滿足不等式 HminHHmax,符合要求。3.2.5 注射機最大開模行程校核模具開模后為了便于取出書簡,要求有足夠的開模距離,而注射機的開模行程是有限的,所以我們在設計是必須進行注射模開模行程的校核,在我們所選擇的這個規(guī)格的注射機中開模最大行程為 180mm。注射機的開模行程應大于模具開模時取出塑件(包括澆注系統(tǒng))所需要的開模距離,即是必須滿足下式:Sk≥H1+H2+(5 ~ 10)式中:Sk —— 注射機行程 Sk=300mmH1 ——脫模距離(頂出距離)H1=5mmH2 ——塑件高度+澆注系統(tǒng) H2=10+50=60mm所以 H1+H2+(5 ~ 10)=5+50+10=65≤Sk=300mm 能滿足要求。通過上述校核得出該規(guī)格的注射機滿足要求,因此,確定選擇型號為:XS?Z?60 的注射機。3.3 確定型腔數(shù)目和分模面的選擇3.3.1 確定型腔數(shù)目根據(jù)上面計算結果,N 能取到 2 個。所以取 N = 2。符合設計要求,所以確定型腔數(shù)第三章 注射機的選擇和校核目為 2 個。 )3.3.2 分模面的選擇分模面為定模與動模的分界面。用于取出塑料件或澆注系統(tǒng)凝料的面合理地選擇分型面是使塑件能完好的成形的先決條件。選擇分型面要考慮以下問題:① 使塑件在開模后留在動模上;②分型面的痕跡不影響塑件的外觀;③澆注系統(tǒng),特別是澆口能合理的安排;④使推桿痕跡不露在塑件外觀表面上;⑤使塑件易于脫模。由于對塑件的結構形狀特殊,根據(jù)分型面的選擇,應符合以上原則。然后綜合塑件形狀的思考,和模具的總體設計,制造,加工要求,我選擇用一個平面的分型面。按照塑件結構,可以有兩種分型面方案,如圖 3.1 所示:11方案 1 開模后塑件全部留在動模側,符合分型面設計原則,簡化了模具結構,且縮短了流道,節(jié)約材料,提高經(jīng)濟效益。第四章 澆注系統(tǒng)和冷卻系統(tǒng)設計第四章 澆注系統(tǒng)和冷卻系統(tǒng)設計4.1 澆注系統(tǒng)設計4.1.1 主流道的設計主流道的設計通常設計成圓錐形,塑件所選擇的塑料為 ABS 材料,該塑料的流動性較差,所以我們選擇的錐角度數(shù) α =3°~6°,以便于凝料從主澆道中拔出,內(nèi)壁的粗糙度一般為 Ra=0.63μm 為防止主流道與噴嘴處溢料,主流道對接處緊密對接,主流道對接處應制成半球形凹坑。其半徑為:R2=R1+(1~2)mm式中:R1——注射機噴嘴球半徑 R1= 12mm將數(shù)據(jù)代入上式得澆口套半徑為:R2= R1+(1~2)mm=12+(1~2)=13~14mm澆口套半徑為:R2=13mm小端直徑:d1=d2+(0.5~1)mm式中:d2——注射機噴嘴直徑 d=4mm所以小端直徑 d1= d2+(0.5~1)mm=4+(0.5~1) = 4.5~5mm取小端直徑為:d1=5mm錐角取為 3°且主澆道的縱截面為梯形橫截面,所以大端直徑:d= d1+2×(L×tan3°)當 L=60mm 時大端直徑 d 為:d= d1+2×(L×tan3°)=5+2(47.5×0.052)≈9.94mm凹坑深:h=(3~5)mm為減小料流轉向過渡的阻力,主流道大端呈圓角過渡,其圓角半徑為:r=1~3mm4.1.2 分流道的設計1、分流道截面形狀的選擇[8]分流道的截面形狀有圓形、半圓形、矩形、梯形、V 形等多種。其中圓形截面最理想,使用越來越多。本次用圓形截面。13分流道的尺寸由公式:d=Tmax+1.5式中:Tmax ——塑件最大壁厚d=5+1.5 =6.5mm2、分繞道的布置形式分澆道的布置形式,取決于型腔的布局,其遵循的原則應是排列緊湊,能縮小模板尺寸,減小流程,鎖模力力求平衡。分繞道的布置形式有平衡式和非平衡式兩種,本次設計采用平衡式布置。3、分流道的表面粗糙度[7]分流道的表面不要求太光潔,表面粗糙度通常取為 Ra=1.25~2.5μm,這可以增加對外層塑料熔體的流動阻力,使外層塑料冷卻皮層固定,形成絕熱層,有利于保溫。但為了保證脫模和分型,我們又必需保證表面的粗糙度不能過大以至于表面出現(xiàn)凹凸不平的現(xiàn)象,從而給脫模和分型都帶來難度。所以我們在此選擇分流道的表面粗糙度為Ra=1.5μm。4.1.3 澆口設計1、分流道與澆口的連接形式分流道與澆口的連接形式通常有斜面和圓弧連接等兩種連接方式,根據(jù)我們的型腔布局和分流裝置,流道和澆口與連接的寬度方向的選擇將是更好的地方。但當寬度的連接,由于傾斜將使分流到逐漸變窄,從而快速冷卻的不同階段,產(chǎn)生的壓力損失,和圓弧過渡界面偏寬,所以上述缺陷是可以解決的,所以選擇并聯(lián)連接的道路和門中連接圓弧過渡的寬度。2、澆口形狀的選擇及其尺寸確定澆口是連接流道與型腔之間的一段細短通道,是澆注系統(tǒng)的關鍵部分,起著調節(jié)控制料流速、補料時間及防止倒流等作用。澆口的形狀、尺寸和進料位置等對塑件成型質量的影響很大,塑件上的一些缺陷,例如:縮孔、缺料、白斑、熔接痕、質脆、分解和翹曲等多數(shù)都是因為澆口設計的不合里而產(chǎn)生的。所以在設計澆口時我們一定要結合塑料性能、塑件形狀、截面尺寸、模具結構及注射工藝參數(shù)等因素周全考慮。在設計澆口時要求其熔料教快進入并充滿型腔,同時在充滿型腔后能適時冷卻封閉,因此澆口截面要小,長度要短,以便增大流速,快速冷卻封閉,其便于塑件與澆口凝料分離,不留明顯的澆口痕跡,從而保證塑件外觀形狀?;谶@些因素并根據(jù)型腔的排樣方式,選擇潛伏第四章 澆注系統(tǒng)和冷卻系統(tǒng)設計澆口。4.1.4 冷料穴和拉料桿設計冷料穴往往與 Z 的冷料拉式桿,球頭形冷料,與錐頭拉桿和冷材料等三種冷料拉桿。Z 型拉桿的冷料,底鉤狀,塑膠成型,在冷料洞和拉桿鉤圈在一起,拉桿固定在推桿固定板上。當模具打開時,拉桿采用鉤在冷料拉洞穴,使骨料脫垂?jié)部诘墓潭J?,將凝料與塑件一起引入動態(tài)模型??傖尫胚@寒冷的材料更容易,和快速釋放和推桿的搭配使用,可以釋放與塑料零件,提高生產(chǎn)速度。和球頭形冷料,致力于推板脫模機構,在我們的設計中,在噴射脫模機構的選擇,所以不應該選擇冷材料。與錐頭拉桿,拉桿材料冷不冷料球頭形的變體形式,這種拉桿一般不配備冷料,是依靠錐頭夾持力的收縮,將骨料拔出固定模具澆口。冷料這種形式的可靠性高的前兩類,容易出現(xiàn)總不能釋放現(xiàn)象,并具有高收縮塑料件的要求。效果不佳的苛刻的條件??傊?,設計往往選擇 Z 型拉桿冷材料。大直徑與直徑相等的直桿拉,通過模具的選擇決定了它的長度。4.1.5 澆注系統(tǒng)的平衡模具是一模多腔的設計,但模具型腔數(shù),并根據(jù)模具型腔的布局,模具型腔與主流道的距離是一致的,和他們的布局是一個圓圈的形狀,路徑長度,融入到各型腔的所有相同的主流渠道,不發(fā)生因通道長度或由于模腔的流道由近而遠,在澆注系統(tǒng)的范圍將段速度,或模腔壓力范圍,導致形成不一致的現(xiàn)象。所以根據(jù)型腔布置,系統(tǒng)可以實現(xiàn)平衡澆注,不再需要人工平衡澆注系統(tǒng)。4.2 排氣系統(tǒng)的設計排氣系統(tǒng)是指在注塑成型過程中注射成型過程中的氣體(氣體來源:原本在腔,空氣溶解在熔體中的氣體,水蒸汽,氣體的分解產(chǎn)生的塑料)裝置排除。它通常是開在最后溶液流入。在本設計中,由于塑件的體積小,在形成的過程中產(chǎn)生的氣體會不會很大,因此,我們不能有排氣系統(tǒng)的特殊設計,我們可以直接使用的分型面和配合間隙推桿排氣。在子表面排氣使用,我們需要一些臨別表面粗糙度,因此,在分型面的磨削,砂輪必須指向橫向線,以保證熔體填充過程中,氣體可以被排除在分型面。此外,為較好的排氣型表面的緣故,可與動模板和在同一時間的模板,寬 2mm,在固定模板槽高 1mm,從而加強了分模面排氣功能。154.3 冷卻系統(tǒng)設計4.3.1 設計冷卻系統(tǒng)的必要性1 設計冷卻系統(tǒng)的必要性在注射成型中,模具溫度直接影響著塑件的質量和生產(chǎn)效率。對質量的影響主要表現(xiàn)在以下幾個方面:1,變形模具溫度穩(wěn)定,冷卻速度的平衡,可以減少塑件的變形。對于均勻的厚度和形狀復雜的零件,往往是由于不均勻的收縮和翹曲變形,網(wǎng)站必須調整部分設計合理的冷卻系統(tǒng)溫度,冷卻水溫度保持平衡,使熔化和凝固腔體能。2,尺寸精度溫度控制系統(tǒng)來保持模具溫度,可以降低產(chǎn)品的成型收縮率的波動,從而提高塑料件尺寸精度穩(wěn)定性。3,機械性能對于結晶性塑料,結晶度越高,塑性應力開裂傾向越大,降低模具溫度有利于減小應力開裂。4,表面質量模具溫度太低會造成工件輪廓清晰,產(chǎn)生明顯的焊縫,從而導致增加的表面粗糙度。提高模具溫度可以提高零件的表面質量,使其表面光滑,粗糙度降低。以上的通過對模具溫度的要求是矛盾的,因此在穩(wěn)定模具的選擇,必須根據(jù)使用的主要性能的主要要求。溫度對生產(chǎn)效率的調節(jié)作用:熔體在注塑模具溫度一般在 200℃~60℃,冷卻,在這期間釋放的熱量僅為 5%的輻射,對流的方式散發(fā)到大氣中去,該熱剩余的 95%將由冷卻介質帶走,因此,冷卻時間,注塑模具主要由冷卻介質的冷卻效果的決定,并在注射周期循環(huán),冷卻時間模具占 2/3,整個循環(huán),因此,冷卻時間縮短了模具注塑模具的生產(chǎn)效率提高的最有效和最關鍵的地方。第四章 澆注系統(tǒng)和冷卻系統(tǒng)設計模具溫度控制系統(tǒng)包括兩個方面:冷卻系統(tǒng)和加熱系統(tǒng),但由于我國塑料材料的選擇是ABS 塑料,要求塑料模具溫度(一般<80℃),因此在設計中我們只需要一個冷卻系統(tǒng)的設計。4.3.2 冷卻系統(tǒng)尺寸計算塑料件達到釋放溫度一定需要足夠的時間。溫度,塑件的尺寸這時間和跨出(厚度)和材料的性質和其他有關。如果假定溫度的中心部分的塑料部件達到熱畸變溫度可以釋放,所以冷卻時間是使塑件注射成型溫度的溫度下降到的熱量所需時間的中心溫度變形溫度,那么我們可根據(jù)公式求得:t2=n×m2式中:t2 —— 固化時間(s);m —— 塑件的厚度(cm);n —— 塑料經(jīng)驗參數(shù) ABS 取 338t2=338×0.52=84.5s該制件開模時是靠頂出裝置頂出,設開模時間為 t3 為 t3=15s。根據(jù)查表得注射時間t1=2.9s。制品的周期: t=t1+t2+t3=2.9s+84.5s+15s=102.4s 每次注射所需的塑料質量 m 為: m=mg+mj=18.9×2+9=46.8g式中: mg —— 塑件的質量(g)mj —— 凝料的質量(g)每小時注射次數(shù)為:3600÷84.5≈42(次)單位時間的注射量:W=46.8g×42≈19.65kg用 20℃的水作為冷卻介質,設定其出口溫度為 24℃。那么模具冷卻時所需冷卻介質的體積流量(忽略模具因空氣對流、熱輻射以及與注射機接觸所散發(fā)的熱量):第五章 其它零部件結構設計第五章 其他零部件結構設計5.1 脫模機構設計5.1.1 脫模機構的分類注塑成型后,由凸模和凹模脫出的機構稱為塑件脫模機構。脫模機構包括一系列的發(fā)射部分和輔助部分,可以有不同的釋放行為。由于在塑件的尺寸和形狀的變化,因此,物種是千變?nèi)f化的脫模機構。根據(jù)動力機構的運動可分為:幾種分型方法手動脫模脫模,電機,液壓與氣動脫模。通過推進機構的運動特性可分為:一次推出(簡單脫模機構) 、二次推出、順序脫模、點澆口自動脫模和帶螺紋塑件脫模等幾類。5.1.2 脫模機構設計原則①脫模機構的種類繁多,設計也復雜,并且要求釋放在塑料零件的損壞,變質及外觀形狀影響的時間,所以在設計中必須要求模具的大小和作用位置粘塑件的正確分析,側選擇更合適的和適當?shù)拿撃C撃N恢?,使塑料穩(wěn)定擠壓。同時啟動的位置也應盡量選擇隱藏的地方內(nèi)表面的塑料件,使塑件不留痕跡的外表面的發(fā)射。②使推出機構簡單可靠,模具應在可移動的塑料模具零件左,塑料部件使用注塑機運動部件或液壓活塞桿的女士推出頂桿。③推出機構結構運動必須準確,靈活可靠,無鎖的干擾現(xiàn)象。該機構本身應具有足夠的剛度,強度和耐磨性。5.2 導向機構設計5.2.1 導向機構設計原則導向機構主要是用來保證動模和定模模兩部分或兩對定位準確的其他部分,扮演一個角色。該類型的結構(如圖 5.1 所示) 。一種導柱主要適用于簡單的模具和小批量生產(chǎn),一般不需要配置導套的使用。B 型導柱適用于高精密塑件和模具生產(chǎn)批量大的要求,通常有一個導套配套使用,以磨損,更換導套繼續(xù)保持定位精度。安裝在模具上的安裝孔可與導柱安裝孔具有相同的尺寸和加工的另一邊,從而保證同軸度。①為了確保導柱能起到很好的導向、定位并且保護型芯的作用,我們一般將導柱的江陰職業(yè)技術學院長度設計得要比型芯的長度長出(5~10mm)左右,以免在導柱未導正時凸模先進入凹模型腔與其碰撞而損壞。②導柱的直徑視模具大小而定。但必須滿足足夠的抗彎強度,并且表面要耐磨,芯部要堅韌,因此導柱的材料多半回采用低碳鋼(20)滲碳淬火,或是碳素工具鋼(T8, T10)淬火處理,硬度一般要求在 50~55HRC。③導柱端部設計成錐形或半球形,以便導柱能順利的進入導向孔。④導柱與導向孔通常采用間隙配合 H7 / f 6 或 H8/ f 8,而與安裝孔之間采用 H7 /m6或 H7 / k6,配合部分表面粗糙度為 R a =0.8μm。同時必須要采用適當?shù)姆椒ǚ乐箤е鶑陌惭b孔中脫出。⑤導柱直徑尺寸按模具模板外形尺寸確定,模板尺寸也,導柱間中心距應越大,導柱直徑就越大。5.2.2 導柱的外形尺寸計算本設計中導柱的材料選擇為碳素工具鋼 T8,淬火處理,硬度為 55HRC,導柱的長度要高出凸模(5~10mm)在本設計中取 6.5mm,其端部設計成半球形。由于我們所設計的塑件精度要求不高,為簡化設計和降低成本,我們選擇 A 型導柱。模板外形尺寸選擇為250×250,導柱直徑一般選擇為 15~35mm,在設計中我們將導柱直徑選為 20mm。導柱的長度 L 為:L=L1+L2+8式中:L —— 導柱的總長度 mmL1 —— 動模板的厚度 mmL2 —— 型芯的高度 mm5.2.3 導向孔的設計我們選擇了 A 型導柱,它沒有配套的導套,所以不需設計導套機構,而只需要在模板上加工設計一個導孔即可。導向孔設計要點:①導向孔在設計時必須要設計成為一個通孔,如是盲孔必須在導向孔的底部開設通氣孔,否則當導柱進入了盲孔后,導向孔中的空氣將會無法排除,而無法排除的空氣將會產(chǎn)生反壓力,給導柱運動造成阻力。②為了能讓導柱順利進入導套中,在導套的前端應設計成為倒圓角。導套的材料采19用淬火鋼或銅等耐磨材料,其硬度必須比導柱低,以改善摩擦和防止導套或導柱拉毛。③導套孔的滑動部分按 H8/ f 8 間隙配合,導套外徑按 H7 /m6 過渡配合。④導套安裝固定方式可用臺階式導柱,利用軸肩防止開模時拔出導套,也可采用直導套,用螺釘起止動作用。在本設計中選擇了后種導套的安裝方式。5.2.4 導柱的數(shù)量和布置注射模的導柱一般取 4 根,其數(shù)量和布置形式根據(jù)模具的機構形式和尺寸來確定。5.3 定位圈5.3.1 定位圈的定義定位圈是主要用于與注塑機定位孔配合的,為了便于模具在注塑機的安裝以及主流道襯套與注塑機的噴嘴孔精確定位,而在模具(一般是在定模)上安裝的一種定位裝置。它除了能保證澆口套和噴嘴孔的精確定位外,還具有防止?jié)部谔讖哪?nèi)脫出的功能。5.3.2 導柱的數(shù)量和布置定位圈與注塑機上的定位孔上的配合長度的選擇。對于小型模具一般選擇 8~10mm;對于大型模具取 10~15mm。定位圈的外徑 D 比注塑機上的孔位徑小 0.2~0.3mm,以便于裝模。根據(jù)定位圈的選擇要求和所設計的模具大小我們選擇的定位圈規(guī)格如下:定位圈與注塑機上的定位孔配合長度選為 L=10mm;直徑:D=DO ?0.2(DO:注塑機定位孔的直徑為 100mm)D=DO?0.2=100?0.2=99.8mm在本設計中,一方面由于模具是小型模具,且精度要求并不高;另一方面,從設計的工作量,以及模具中澆注系統(tǒng)的主流道較短等幾方面綜合考慮看來,定位圈與定模的安裝搭配方式,我們可以選擇最常用型的安裝方式,其剖面圖(如圖 5.2 所示)5.4 主流道襯套主流道襯套選擇:根據(jù)實用注射模設計手冊查的,主流道襯套尺寸是根據(jù)使用情況所決定的。而主流道襯套的常用材料為 T8A,HRC55, 其剖面圖(如圖 5.3 所示)5.5 注射模具成型零件和模體的設計江陰職業(yè)技術學院5.5.1 模具型腔的結構設計型腔的結構形式大致可以分為以下幾種:(1)整體式整體式型腔由整塊材料加工而成的型腔。它的優(yōu)點是:強度和剛度都比較高,不易變形,塑件不產(chǎn)生的拼接縫跡。(2)整體組合式型腔是由一片材料,與肩或螺栓固定在模板。它的主要優(yōu)點是易于處理,尤其是在多腔模具型腔,單一的處理中,分別設置在模板,所以容易確保每個腔同軸度和尺寸精度,成型加工部分。(3)局部組合式型腔由整塊材料制成,但局部鑲有成型嵌件的局部組合式型腔。局部組合式型腔多于型腔較深或形狀較為復雜,整體加工比較困難或局部需要淬硬的模具。(4)完全組合式完全組合式是由多個螺栓拼塊組合而成的型腔。它的特點是,便于機加工,便于拋光研磨和局部熱處理。節(jié)約優(yōu)質鋼材。這種形式多用于不容易加工的型腔或成型大面積塑件的大型型腔上。塑料注射模具的型腔螺栓部分不是很復雜時,可以用電火花。這里是一個選擇的積分型腔是由兩塊半塊一起形成。5.5.2 注射模具成型零件的尺寸確定(1)塑料制品的成型收縮率的計算塑料制件從模具中取出的特征尺寸稱為收縮塑料。影響塑料品種的收縮的基本因素,塑料,形式,規(guī)模大的特點,在進料口分布,成型條件。塑性收縮的數(shù)據(jù)是基于測量的標準樣品。收縮率的計算檢查表 ABS 0.3% ~ 0.8%,平均收縮率:0.6%。(2)型腔尺寸計算(a)徑向尺寸ABS 的一般精度等級為 6 級。同時得出塑料制件的尺寸公差。又由于塑件的外徑D=24.00㎜,所以查表得 Δ=0.45mm,按照平均收縮率計算凹模徑向尺寸公式:21????ZscpMLS??????431式中 L M ——凹模的徑向尺寸,mmScp——塑料的平均收縮率,%Ls ——塑件徑向公稱尺寸,㎜Δ——塑件公差值, ㎜δz——凹模制造公差,㎜已知 L s =24.00㎜ S cp =0.006 Δ=0.45 ㎜所以 δz=Δ/3=0.15㎜??21.045.306.240. ?????M=23.81+0.21=24.02㎜(b)深度尺寸ABS 的一般精度等級為 6 級。同時得出塑料制件的尺寸公差。又由于塑件的深度尺寸 Hs =42.00㎜ ,所以查表得 Δ=0.55㎜,按照平均收縮率計算凹模深度尺寸公式: ????zscpMHS??????321式中 H M ——凹模的深度尺寸, ㎜Scp——塑料的平均收縮率,%Hs ——塑件高度公稱尺寸, ㎜Δ——塑件公差值, ㎜δz——凹模深度制造公差,㎜已知 H s =42.00㎜ S cp =0.006 Δ=0.55 ㎜所以 δz=Δ/3=0.18㎜ ????18.05.320.46.1?????M=41.89+0.81=42.70㎜(3)螺紋型芯的尺寸計算(a)中徑尺寸的計算 02243???????????SdM式中 ——螺紋型芯中徑尺寸;Md2江陰職業(yè)技術學院——塑件內(nèi)螺紋中徑基本尺寸;2dS ——塑件平均收縮率;△ ——塑件中徑公差;δ ——螺紋型芯中徑制造公差, δ=0.02;根據(jù)公式計算得螺紋型芯的中徑尺寸: 。mdM02.2714??(b)外徑尺寸的計算 ??0????S式中 ——螺紋型芯外徑尺寸;Md——塑件內(nèi)螺紋外徑基本尺寸;S ——塑件平均收縮率;△ ——塑件中徑公差;δ ——螺紋型芯中徑制造公差, δ=0.03;根據(jù)公式計算得螺紋型芯的外徑尺寸: 。mdM03.16??(c)內(nèi)徑尺寸的計算 ??011????S式中 ——螺紋型芯內(nèi)徑尺寸;Md——塑件內(nèi)螺紋內(nèi)徑基本尺寸;S ——塑件平均收縮率;△ ——塑件中徑公差;δ ——螺紋型芯中徑制造公差, δ=0.03;根據(jù)公式計算得螺紋型芯的內(nèi)徑尺寸: 。mdM03.1??5.6 注射模具的斜導柱側抽芯機構設計斜導柱的斜導柱側抽芯機構的重要組成部分。確定涉及斜導柱主要包括斜導柱的結構形式和安裝形式,斜導柱直徑,拔角的選擇,斜導柱長度和加工精度的選擇,斜導柱的材料及熱處理等。(1)斜導柱傾斜角 α斜導柱角是決定抽芯工作成效的重要工作。在關系到斜導柱承受拉力和實際達到的彎曲力的傾斜角度的大小,而且還關系到斜導柱的有效長度和抽芯距和開模行程。計算公式為:23HStg??式中 α——斜導柱的抽拔角;S ——抽芯距, S=13.5mm;H——斜導柱完成抽芯距所需的開模行程,H=50mm。根據(jù)公式計算 α:取 α ?15?(2)圓柱形斜導柱總長度的計算斜導柱的總長度取決于抽芯距、斜導柱直徑和傾斜角。圓柱形斜導柱總長度: dSdhDL ?????????? 41~3sinta2tncostan2???式中 L ——斜導柱總長度,mm;D ——斜導柱臺肩直徑,D =16mm;α——斜導柱抽拔角,α= ?15;h ——斜導柱固定板厚度,h =20mm;δ——斜導柱與側滑塊斜孔的配合間隙, δ=0.025mm;d ——斜導柱工作部分直徑,d=10mm;S ——抽芯距, S=13.5mm。根據(jù)公式計算 L:L = 76.35 + 3 = 79.35mm,取 L=80mm最終斜導柱結構如圖 3.6 所示。江陰職業(yè)技術學院圖 3.6 斜導柱