車削件典型軸類零件的數(shù)控車削加工工藝編程設計【原創(chuàng)課程畢業(yè)設計含CAD零件圖帶過程工序卡片及程序】-bc04
車削件典型軸類零件的數(shù)控車削加工工藝編程設計
摘 要
數(shù)控車床技術在當今機械制造業(yè)中的重要地位和巨大效益,已經顯示了其在國家基礎工業(yè)現(xiàn)代化生產中的戰(zhàn)略性作用,而且已成為了傳統(tǒng)機械制造業(yè)實現(xiàn)自動化、柔性化、集成化生產的重要手段和標志。數(shù)控車床的廣泛應用,給機械制造業(yè)的產業(yè)結構、產品種類和檔次以及生產方式帶來了革命性的變化。數(shù)控車床是現(xiàn)代加工車間里面重要的加工設備,現(xiàn)代的CAD/CAM都是建立在數(shù)控技術之上的。掌握現(xiàn)代數(shù)控加工技術知識是現(xiàn)代機械專業(yè)里面必不可少的。在數(shù)控加工過程中,從零件的設計圖紙到零件成品的合格。不僅要考慮到數(shù)控程序的編制,還要考慮到零件加工工藝路線的安排、加工機床型號的選擇、切削刀具的選擇、零件加工的定位裝夾等一系列因素的影響。在開始編程前,必須要對零件設計圖紙和技術要求進行詳細的數(shù)控加工工藝分析。來最終確定哪些是零件的技術關鍵,哪些是數(shù)控加工的難點,以及程序的編制難易程度。
關鍵詞: 數(shù)控加工、仿真加工、曲線加工
目錄
摘 要 3
ABSTRACT 4
1 概述 5
1.1數(shù)控系統(tǒng)的介紹 5
2 加工工藝規(guī)程設計 6
2.1 零件的工藝分析 6
2.1.1零件結構形狀分析 6
2.1.2 零件技術要求分析 6
2.2確定毛坯 8
2.3擬定工藝路線 8
2.3.1確定裝夾方案 8
2.3.2 確定各表面的加工方法,劃分加工階段 10
2.3.3 加工的工序安排 12
2.4機床、夾具、刀具、量具和切削液的選擇 16
2.4.1 機床的選擇 16
2.4.2 夾具的選擇 16
2.4.3 刀具的選擇 17
2.4.4 量具的選擇 17
2.4.5 切削液的選擇 18
2.5確定工序的加工余量 19
2.5.1 加工余量的確定 19
2.6 確定工序的切削用量及工時定額 19
2.6.1切削用量的選擇 19
2.7 本章小結 22
3 數(shù)控程序設計 23
3.1 概述 23
3.2 數(shù)控程序 23
3.3 自動編程與手動編程的比較 29
4 總結 30
4.1加工質量檢測 30
4.2 改善方法 31
參 考 文 獻 32
致謝 33
【詳情如下】【需要咨詢購買全套設計請加QQ1459919609】
任務書.doc
工序卡.doc
工藝過程卡片.doc
截圖
文件清單.txt
程序.txt
車削件典型軸類零件的數(shù)控車削加工工藝編程設計.doc
零件二維圖.dwg
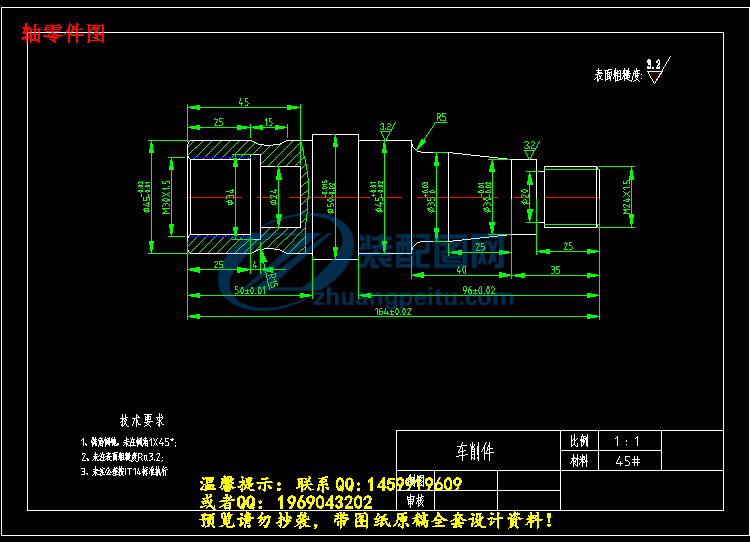
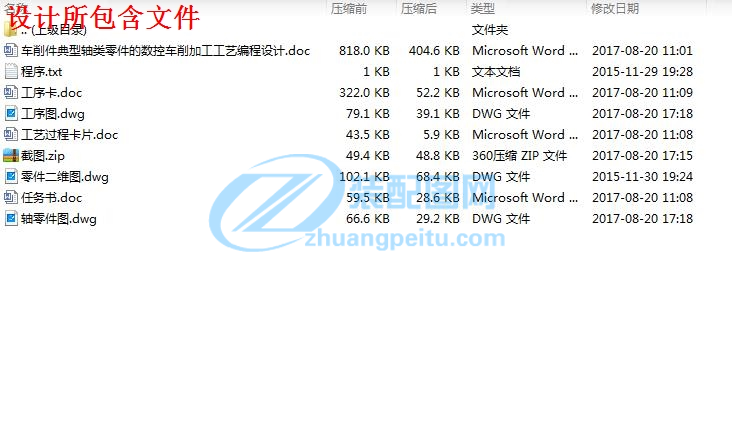
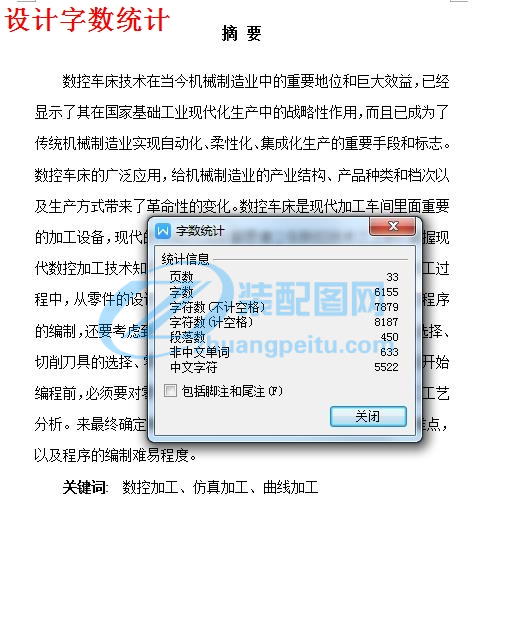

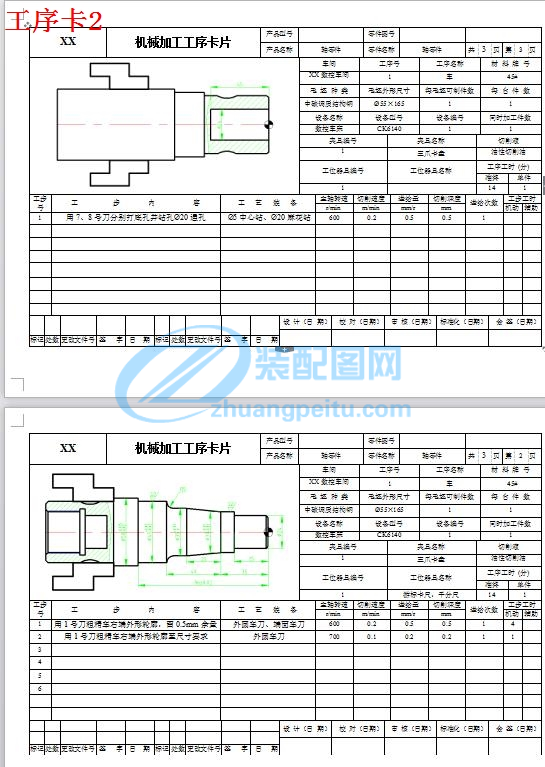
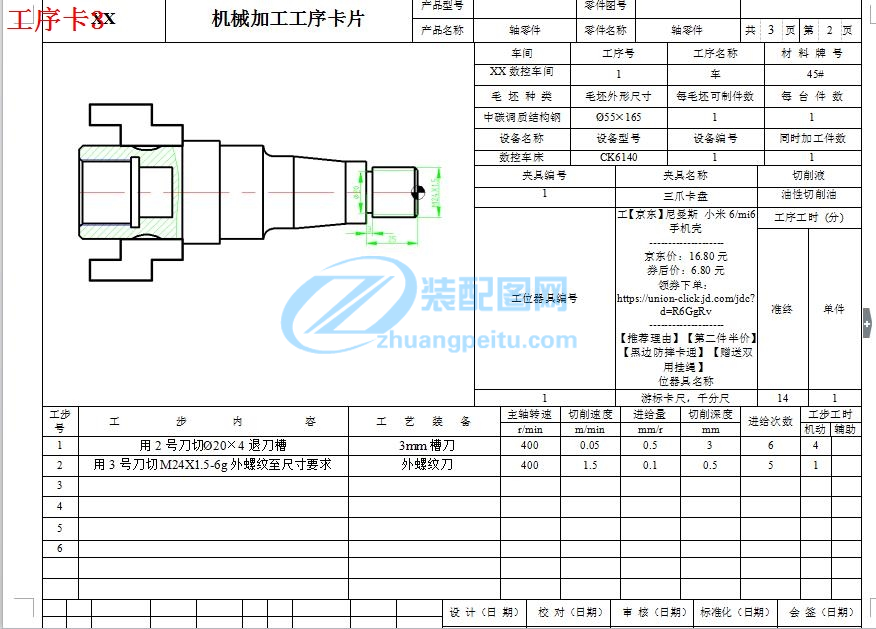
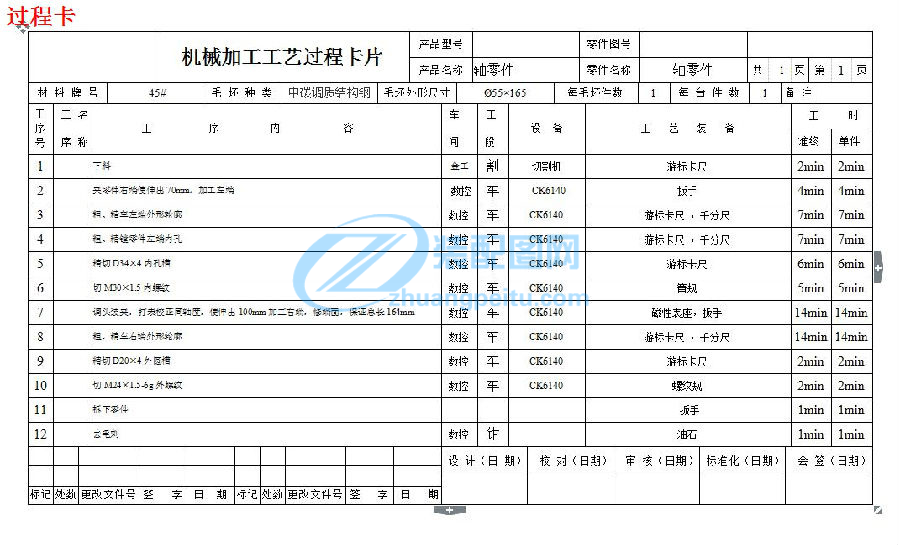
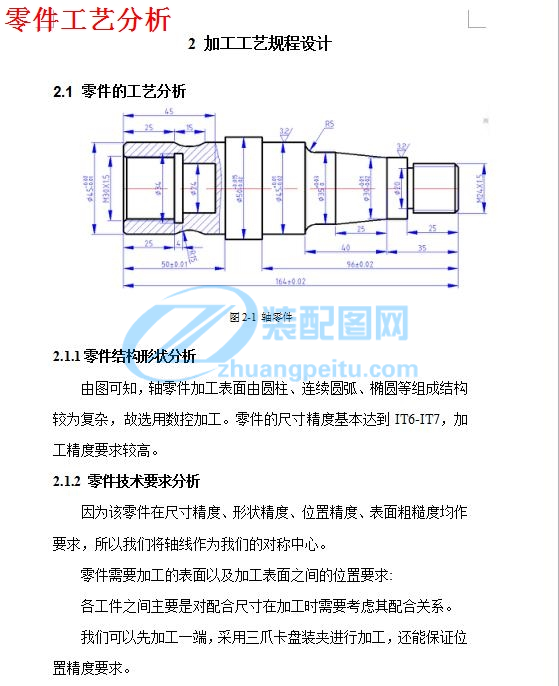
件三 任 務書 學生姓名 專業(yè) 班級 聯(lián)系方式 校內指導教師 職稱 單位 聯(lián)系電話 校外指導教師 職稱 單位 聯(lián)系電話 設計題目 1.畢業(yè)設計課題來源及應達到的目的: 一、題目來源 鑒于機電一體化技術專業(yè)的特點,以及學生頂崗實習的情況,本次畢業(yè)設計題目來源于以下幾方面: 據(jù)所學理論對零件進行機械加工或數(shù)控加工工藝設計與編程; 二、目的 畢業(yè)設計 是培養(yǎng)學生綜合運用本專業(yè)基礎理論,基本知識和基本技能分析解決實際問題的一個重要環(huán)節(jié);是本專業(yè)各個先前教學環(huán)節(jié)的深化和檢驗。通過畢業(yè)設計,使學生充分利用所學的專業(yè)知識,理論聯(lián)系實際, 獨立分析、解決實際工藝問題的能力,為其今后走上工作崗位從事有關實際工作打下一個良好的基礎。 通過畢業(yè)設計可以達到以下目的: (一)培養(yǎng)學生運用所學知識的運用能力,以及解決生產中實際問題的能力; (二)培養(yǎng)學生調查研究與信息收集、整理的能力; (三)培養(yǎng)和提高學生的自學能力和實際應用能力; (四)培養(yǎng)和提高學生的文獻檢索、收集能力; (五)培養(yǎng)和提高學生的設計、報告等編寫能力; (六)培養(yǎng)學生的創(chuàng)新意識、求實的科學作風以及刻苦鉆研的精神。 三、畢業(yè)設計的基本要求 (一)學生必須充分認識畢業(yè)設計的重要性,嚴格按要求開展畢業(yè)設計工作; (二)畢業(yè)設計任務應包括對實際問題的調查分析; (三)畢業(yè)設計任務必須由學生本人在指導教師指導下獨立進行; (四)畢業(yè)設計必須有進度要求,有明確的階段成果,并定期進行檢查; (五)畢業(yè)設計任務應有工作量要求。 2.畢業(yè)設計課題任務的內容和要求(包括原始數(shù)據(jù)、技術要求、工作要求等): 畢業(yè)設計課題任務的內 容和要求 1. 內容 ( 1)對零件進行工藝分析 ( 2)編寫機械加工工藝過程卡片 ( 3)編寫機械加工工序卡片 (4) 編寫零件加工程序 本次設計要求綜合運用所學的基礎理論、專業(yè)知識與技能完成機電專業(yè)數(shù)控方向的畢業(yè)設計。學生應認真對待本次設計,在老師的指導下,根據(jù)設計任務,合理安排時間和進度,認真地、有計劃地按時完成設計任務,培養(yǎng)良好的工作作風。必須以負責的態(tài)度對待自己所做的技術決定、數(shù)據(jù)和計算結果。注意理論與實踐的結合,以使整個設計在技術上是先進的,在經濟上是合理的,在生產上是可行的。 ( 1)查閱資料,了解課題的背景及現(xiàn)狀,結合具體工作情況合理設計。 ( 2)通過查閱書籍和資料及圖紙,找到能夠實現(xiàn)課題功能的方法,提出設計方 案。 ( 3)設計出流程圖,使其能夠實現(xiàn)課題要求的功能。 ( 4)設計出詳細的工藝規(guī)程,使其能夠實現(xiàn)課題要求的功能。 ( 5)對零件進行必要的數(shù)據(jù)計算。 ( 5)根據(jù)以上工作過程和工作內容,總結設計方案,提煉核心內容,撰寫畢業(yè)設計論文,論文要求思路 清晰、結構完整、內容充實、圖表清楚,格式規(guī)范,字數(shù)在 5000 字以上。 3.對本畢業(yè)設計課題成果的要求〔包括圖表、實物等硬件要求〕: 畢業(yè)設計報告 要求 下內容: ( 1)被加工零件的零件圖 1 張(可置于畢業(yè)設計中) ( 2)機械加工工藝過程卡片 1 張(可置于畢業(yè)設計中) ( 3)機械加工工序卡片 1 張(可置于畢業(yè)設計中) (4) 程序單 1 張(可置于畢業(yè)設計中) ( 5) 畢業(yè)論文 1 份 4.主要參考文獻: 1.《切削用量簡明實用手冊》 黃如林主編 化學工 業(yè)出版社 2.《機械設計綜合課程設計》 王之標、王大康主編 機械工業(yè)出版社 3.《機床制造工藝設計手冊》 王紹俊主編 機械工業(yè)出版社 4.《金屬切削機床》 宋玉鳴主編 中國勞動社會保障出版社 5.《機械制造工藝學課程設計指導》趙家齊編 機械工業(yè)出版社 6.《簡明機械加工工藝手冊》徐圣群主編 上??茖W技術出版社 7.《機械加工工藝師手冊》楊叔子主編 機械工業(yè)出版社 8.《機械設計基礎課程設計指導書》 陳立德主編 高等教育出版社 9. 黃成編著 具設計與加工 北京希望電子出版社 2009 G 文版數(shù)控加工 機械工業(yè)出版社 2009 G 文版標準教程 北京清華大學出版 社 2009 文版從入門到精通 北京清華大學出版社 2009 文版實用教程 關振宇 劉源 主編 人民郵電出版社 用與實力教程 周瑋 主編 人民郵電出版社 5.本畢業(yè)設計課題工作進度計劃: 起 迄 日 期 工 作 內 容 2016 年 3 月 8 日 — 3 月 10 日 2016 年 3 月 11 日 — 3 月 13 日 2016 年 3 月 14 日 — 3 月 15 日 2016 年 3 月 16 日 — 4 月 20 日 2016 年 4 月 21 日 — 5 月 20 日 2016 年 5 月 21 日 — 6 月 1 日 學生畢業(yè)設計動員,指導教師確定,教師調研、資料 準備階段 畢業(yè)設計題目確定階段 查閱資料,確定設計方案(查閱可以實現(xiàn)功能的各種方法和 手段,比較后,說明你采用方案的優(yōu)點。將這個過程寫在論 文中。) 填寫畢業(yè)設計書任務書、學生撰寫論文階段 畢業(yè)設計(論文)審閱階段 論文答辯 專業(yè)教研室審查意見: 負責人: 年 月 日 領導小組意見: 機械加工工序卡片 產品型號 零件圖號 產品名稱 軸零件 零件名稱 軸零件 共 3 頁 第 1 頁 車間 工序號 工序名稱 材 料 牌 號 金工 1 割 45# 毛 坯 種 類 毛坯外形尺寸 每毛坯可制件數(shù) 每 臺 件 數(shù) 中碳調質結構鋼 ?55× 165 1 1 設備名稱 設備型號 設備編號 同時加工件數(shù) 切割機 1 夾具編號 夾具名稱 切削液 工位器具編號 工位器具名稱 工序工時 (分 ) 準終 單件 1 游標卡尺 1 工步號 工 步 內 容 工 藝 裝 備 主軸轉速 切削速度 進給量 切削深度 進給次數(shù) 工步工時 r/m/mm/r 動 輔助 1 下料 游標卡尺 400 80 0 3 設 計(日 期) 校 對(日期) 審 核(日期) 標準化(日期) 會 簽(日期) 標記 處數(shù) 更改文件號 簽 字 日 期 標記 處數(shù) 更改文件號 簽 字 日 期 械加工工序卡片 產品型號 零件圖號 產品名稱 軸零件 零件名稱 軸零件 共 3 頁 第 2 頁 車間 工序號 工序名稱 材 料 牌 號 1 車 45# 毛 坯 種 類 毛坯外形尺寸 每毛坯可制件數(shù) 每 臺 件 數(shù) 中碳調質結構鋼 ?55× 165 1 1 設備名稱 設備型號 設備編號 同時加工件數(shù) 數(shù)控車床 1 夾具編號 夾具名稱 切削液 1 三爪卡盤 油性切削油 工位器具編號 工位器具名稱 工序工時 (分 ) 準終 單件 1 游標卡尺,千分尺 14 1 工步號 工 步 內 容 工 藝 裝 備 主軸轉速 切削速度 進給量 切削深度 進給次數(shù) 工步工時 r/m/mm/r 動 輔助 1 用 1號刀粗精車左端外形輪廓, 留 外圓車刀、端面車刀 600 4 2 用 1號刀粗精車左端外形輪廓 至尺寸要求 外圓車刀 700 1 設 計(日 期) 校 對(日期) 審 核(日期) 標準化(日期) 會 簽(日期) 標記 處數(shù) 更改文件號 簽 字 日 期 標記 處數(shù) 更改文件號 簽 字 日 期 械加工工序卡片 產品型號 零件圖號 產品名稱 軸零件 零件名稱 軸零件 共 3 頁 第 3 頁 車間 工序號 工序名稱 材 料 牌 號 1 車 45# 毛 坯 種 類 毛坯外形尺寸 每毛坯可制件數(shù) 每 臺 件 數(shù) 中碳調質結構鋼 ?55× 165 1 1 設備名稱 設備型號 設備編號 同時加工件數(shù) 數(shù)控車床 1 夾具編號 夾具名稱 切削液 1 三爪卡盤 油性切削油 工位器具編號 工位器具名稱 工序工時 (分 ) 準終 單件 1 14 1 工步號 工 步 內 容 工 藝 裝 備 主軸轉速 切削速度 進給量 切削深度 進給次數(shù) 工步工時 r/m/mm/r 動 輔助 1 用 7、 8號刀分別打底孔并鉆孔 ?20通孔 ?5中心鉆、 ?20麻花鉆 600 設 計(日 期) 校 對(日期) 審 核(日期) 標準化(日期) 會 簽(日期) 標記 處數(shù) 更改文件號 簽 字 日 期 標記 處數(shù) 更改文件號 簽 字 日 期 械加工工序卡片 產品型號 零件圖號 產品名稱 軸零件 零件名稱 軸零件 共 3 頁 第 2 頁 車間 工序號 工序名稱 材 料 牌 號 1 車 45# 毛 坯 種 類 毛坯外形尺寸 每毛坯可制件數(shù) 每 臺 件 數(shù) 中碳調質結構鋼 ?55× 165 1 1 設備名稱 設備型號 設備編號 同時加工件數(shù) 數(shù)控車床 1 夾具編號 夾具名稱 切削液 1 三爪卡盤 油性切削油 工位器具編號 工位器具名稱 工序工時 (分 ) 準終 單件 1 游標卡尺,千分尺 14 1 工步號 工 步 內 容 工 藝 裝 備 主軸轉速 切削速度 進給量 切削深度 進給次數(shù) 工步工時 r/m/mm/r 動 輔助 1 用 4號刀粗鏜右端內孔 ,留 內孔鏜刀、內徑百分表 500 6 4 2 用 4號刀精鏜右端內孔 至尺寸要求 內孔鏜刀、內徑百分表 700 1 3 4 5 6 設 計(日 期) 校 對(日期) 審 核(日期) 標準化(日期) 會 簽(日期) 標記 處數(shù) 更改文件號 簽 字 日 期 標記 處數(shù) 更改文件號 簽 字 日 期 械加工工序卡片 產品型號 零件圖號 產品名稱 軸零件 零件名稱 軸零件 共 3 頁 第 2 頁 車間 工序號 工序名稱 材 料 牌 號 1 車 45# 毛 坯 種 類 毛坯外形尺寸 每毛坯可制 件數(shù) 每 臺 件 數(shù) 中碳調質結構鋼 ?55× 165 1 1 設備名稱 設備型號 設備編號 同時加工件數(shù) 數(shù)控車床 1 夾具編號 夾具名稱 切削液 1 三爪卡盤 油性切削油 工位器具編號 工位器具名稱 工序工時 (分 ) 準終 單件 1 游標卡尺,千分尺 14 1 工步號 工 步 內 容 工 藝 裝 備 主軸轉速 切削速度 進給量 切削深度 進給次數(shù) 工步工時 r/m/mm/r 動 輔助 1 用 5號刀切 ?34× 4退 刀槽 3400 6 4 2 用 6號刀切 尺寸要求 內 螺紋刀 400 1 3 4 5 6 設 計(日 期) 校 對(日期) 審 核(日期) 標準化(日期) 會 簽(日期) 標記 處數(shù) 更改文件號 簽 字 日 期 標記 處數(shù) 更改文件號 簽 字 日 期 械加工工序卡片 產品型號 零件圖號 產品名稱 軸零件 零件名稱 軸零件 共 3 頁 第 2 頁 車間 工序號 工序名稱 材 料 牌 號 1 車 45# 毛 坯 種 類 毛坯外形尺寸 每毛坯可制件數(shù) 每 臺 件 數(shù) 中碳調質結構鋼 ?55× 165 1 1 設備名稱 設備型號 設備編號 同時加工件數(shù) 數(shù) 控車床 1 夾具編號 夾具名稱 切削液 1 三爪卡盤 油性切削油 工位器具編號 工位器具名稱 工序工時 (分 ) 準終 單件 1 游標卡尺,千分尺 14 1 工步號 工 步 內 容 工 藝 裝 備 主軸轉速 切削速度 進給量 切削深度 進給次數(shù) 工步工時 r/m/mm/r 動 輔助 1 用 1號刀粗精車右端外形輪廓, 留 外圓車刀、端面車刀 600 4 2 用 1號刀粗精車右端外形輪廓 至尺寸要求 外圓車刀 700 1 3 4 5 6 設 計(日 期) 校 對(日期) 審 核(日期) 標準化(日期) 會 簽(日期) 標記 處數(shù) 更改文件號 簽 字 日 期 標記 處數(shù) 更改 文件號 簽 字 日 期 械加工工序卡片 產品型號 零件圖號 產品名稱 軸零件 零件名稱 軸零件 共 3 頁 第 2 頁 車間 工序號 工序名稱 材 料 牌 號 1 車 45# 毛 坯 種 類 毛坯外形尺寸 每毛坯可制件數(shù) 每 臺 件 數(shù) 中碳調質結構鋼 ?55× 165 1 1 設備名稱 設備型號 設備編號 同時加工件數(shù) 數(shù)控車床 1 夾具編號 夾具名稱 切削液 1 三爪卡盤 油性切削油 工位器 具編號 工位器具名稱 工序工時 (分 ) 準終 單件 1 游標卡尺,千分尺 14 1 工步號 工 步 內 容 工 藝 裝 備 主軸轉速 切削速度 進給量 切削深度 進給次數(shù) 工步工時 r/m/mm/r 動 輔助 1 用 2號 刀切 ?20× 4退刀槽 3400 6 4 2 用 3號刀切 尺寸要求 外 螺紋刀 400 1 3 4 5 6 設 計(日 期) 校 對(日期) 審 核(日期) 標準化(日期) 會 簽(日期) 標記 處數(shù) 更改文件號 簽 字 日 期 標記 處數(shù) 更改文件號 簽 字 日 期 機械加工工藝過程卡片 產品型號 零件圖號 產品名稱 軸零件 零件名稱 軸零件 共 1 頁 第 1 頁 材 料 牌 號 45# 毛 坯 種 類 中碳調質結構鋼 毛坯外形尺寸 ?55×165 每毛坯件數(shù) 1 每 臺 件 數(shù) 1 備 注 工 序 號 工 名 序 稱 工 序 內 容 車 間 工 段 設 備 工 藝 裝 備 工 時 準終 單 件 1 下料 金工 割 切割機 游標卡尺 2 夾零件右端使伸出 70工左端 數(shù)控 車 手 4 粗、精車左端外形輪廓 數(shù)控 車 標卡尺 ,千分尺 7 粗、精鏜零件左端內孔 數(shù)控 車 標卡尺 ,千分尺 7 精切 4內孔槽 數(shù)控 車 標卡尺 6 切 數(shù)控 車 規(guī) 5 調頭裝夾, 打表校正同軸度 ,使伸出 100 修端面,保證總長 164控 車 性表座 , 扳手 144 粗、精車右端外形輪廓 數(shù)控 車 標卡尺 ,千分尺 144 精切 4外圓槽 數(shù)控 車 標卡尺 20 切 數(shù)控 車 紋規(guī) 21 拆下零件 扳手 12 去毛刺 數(shù)控 鉗 油石 1 計(日 期) 校 對(日期) 審 核(日期) 標準化(日期) 會 簽(日期) 標記 處數(shù) 更改文件號 簽 字 日 期 標記 處數(shù) 更改文件號 簽 字 日 期 用1號刀粗、號刀鉆零件左端內孔;用4號刀粗、總長60伸出100測 1 目錄 目錄 ..................................................................................................... 1 摘 要 ................................................................................................... 3 ....................................................................................... 4 1 概述 ................................................................................................. 5 控系統(tǒng)的介紹 .................................................................. 5 2 加工工藝規(guī)程設計 ........................................................................ 6 件的工藝分析 ................................................................. 6 件結構形狀分析 ................................................... 6 件技術要求分析 .................................................. 6 定毛坯 .............................................................................. 8 定工藝路線 ...................................................................... 8 定裝夾方案 ........................................................... 8 定各表面的加工方法,劃分加工階段 ............ 10 工的工序安排 .................................................... 12 床、夾具、刀具、量具和切削液的選擇 .................... 17 床的選擇 ............................................................ 17 具的選擇 ............................................................ 17 具的選擇 ............................................................ 18 具的選擇 ............................................................ 18 削液的選擇 ........................................................ 19 2 定工序的加工余量 ........................................................ 20 工余量的確定 .................................................... 20 定工序的切削用量及工時定額 ................................... 20 削用量的選擇 ..................................................... 20 章小結 ........................................................................... 23 3 數(shù)控程序設計 .............................................................................. 24 述 ................................................................................... 24 控程序 ........................................................................... 24 動編程與手動編程的比較 ........................................... 30 4 總結 ............................................................................................... 31 工質量檢測 .................................................................... 31 善方法 ........................................................................... 32 參 考 文 獻 ..................................................................................... 33 致謝 ................................................................................................... 34 3 摘 要 數(shù)控車床技術在當今機械制造業(yè)中的重要地位和巨大效益,已經顯示了其在國家基礎工業(yè)現(xiàn)代化生產中的戰(zhàn)略性作用,而且已成為了傳統(tǒng)機械制造業(yè)實現(xiàn)自動化、柔性化、集成化生產的重要手段和標志。數(shù)控車床的廣泛應用,給機械制造業(yè)的產業(yè)結構、產品種類和檔次以及生產方式帶來了革命性的變化。數(shù)控車床是現(xiàn)代加工車間里面重要的加工設備 ,現(xiàn)代的 是建立在數(shù)控技術之上的。掌握現(xiàn)代數(shù)控加工技術知識是現(xiàn)代機械專業(yè)里面必不可少的。在數(shù)控加工過程中,從零件的設計圖紙到零件成品的合格。不僅要考慮到數(shù)控程序的編制,還要考慮到零件加工工藝路線的安排、加工機床型號的選擇、切削刀具的選擇、零件加工的定位裝夾等一系列因素的影響。在開始編程前,必須要對零件設計圖紙和技術要求進行詳細的數(shù)控加工工藝分析。來最終確定哪些是零件的技術關鍵,哪些是數(shù)控加工的難點,以及程序的編制難易程度。 關鍵詞 : 數(shù)控加工 、仿真加工、曲線加工 4 is to of in of to is to be as In of In of of by is It is is 5 1 概述 控系統(tǒng)的介紹 數(shù)控系統(tǒng)一般由輸出 /輸入( I/0)裝置、數(shù)字控裝置、驅動控制裝置、機床電器邏輯控制裝置四部分組成,機床本體為被控對象。 數(shù)控就是用數(shù)字信息對機械運動和工作過程進行控制的技術,所謂的數(shù)字化裝備,其技術范圍覆蓋很廣,包括( 1)機械制造技;( 2)信息處理、加工及傳輸技術;( 3)自動控制技術;( 4)伺服驅動技術;( 5)傳感器技術; (6)軟件技術等。 效率、 質量是先進制造技術的主體。高速、高精加工技術可極大地提高效率、提高產品的質量和檔次,縮短生產周期和提高市場競爭能力。為此日本先端技術研究會將其列為 5 大現(xiàn)在制造技術之一,國際生產工程學會( 其確定為 21 世紀的中心研究方向之一。 6 2 加工工藝規(guī)程設計 件的工藝分析 圖 2零件 件結構形狀分析 由圖可知, 軸零件加工 表面由圓柱、 連續(xù) 圓弧、橢圓等組成結構較為復雜,故選用數(shù)控加工。 零件的尺寸精度基本達到 工精度要求較高。 件技術要求分析 因為該零件在尺寸精度、形狀精度、位置精度、表面粗糙度均作要求,所以我們將軸線作為我們的對稱中心。 零件需要加工的表面以及加工表面之間的位置要求 : 各工件之間主要是對配合尺寸在加工時需要考慮其配合關系。 我們可以先加工一端,采用三爪卡盤裝夾進行加工,還能保證位置精度要求。 技術要求: 7 1 銳邊倒棱 圓弧過渡光滑 3 未注公差按 級加工 4 銳邊倒棱去毛刺 5 未注倒角為 8 定毛坯 該零件毛坯選用 45 號鋼。機械加工余量小,零件沒有熱處理,故選擇毛坯尺寸為 ?55×165 定工藝路線 定裝夾方案 1.( 1)粗基準的選擇 因為 零件 歸為軸類零件,一般以平面作為粗基準。同時以未加工表面作為粗基準,但本零件各面均需加工,所以應以加工余量最小的面為粗基準,利用三爪卡盤夾緊可削除五個自由度,再以右圓柱面定位可削除自由度。 ( 2)精基準的選擇 想要保證零件的加工精度以及裝夾準確方便,就要按照“基準重合”原則和“基準統(tǒng)一”原則去做。 2.具體裝夾 工序一:以左端毛坯外圓為粗基準,加工右端,采用三爪卡盤裝夾參考圖 2 工序二:以左端 ?45 外圓為精基準,加工左端,采 用三爪卡盤裝夾參考圖 2 工序三:以 左 端 ?45 為精基準, 車 內孔及內 螺紋 ,采用三爪卡盤裝夾參考圖 2 9 圖 2 2序 四 :以左端外圓為粗基準,加工右端,采用三爪卡盤裝夾參考圖 2 工序 五 :以左端 ?24 外圓為精基準,加工左端,采用三爪卡盤裝夾參考圖 2 工序 六 :以 左 端 ?24 為精基準, 車 退刀槽及外 螺紋 ,采用三爪卡盤裝夾參考圖 2 10 圖 2 2 確定各表面的加工方法,劃分加工階段 同時 要確定構成零件各個表面的加工方法 。 ( 1 ) 選擇加工方法的具體做法就是 按照 被加工表面的加工要求、材料性質等,選擇合適的加工方法及加工路線 進行加工 。 ( 2 )所選擇的加工方法要能 確定 加工表面的幾何形狀精度和表面相互位置 是否達到 要求 。 11 以將整個工藝路線劃分為以下二個階段: ( 1)粗加工階段 任務是切除毛坯的大部分余量(毛坯大致已經成型),并制出精基準。 ( 2)精加工階段 任務是達到各主要表面達到圖樣規(guī)定要求。這一階段的主要問題是確保加工質量。 12 工的工序 安排 零件 的加工工序 ( 1) 圖 2序Ⅰ: 1、 夾零件右端使伸出 70工左端 ,百分表找正 2、 用 1 號刀粗精車左端外形輪廓, 留 量 3、 用 1 號刀粗精車左端外形輪廓 至尺寸要求 ( 2) 13 圖 2序Ⅰ: 1、 用 7、 8 號刀分別打底孔并鉆孔 ?20 通孔 ( 3) 圖 2序Ⅰ: 1、 用 4 號刀粗鏜左端內孔 ,留 量 14 2、 用 4 號刀精鏜左端內孔 至尺寸要求 ( 4) 圖 2序Ⅰ: 1、 用 5 號刀切 ?34× 4 退刀槽 2、 用 6 號刀切 螺紋 至尺寸要求 ( 5) 15 圖 2序Ⅰ: 1、 調頭裝夾,取總長 60伸出 100工右端 2、 用 1 號刀粗精車右端外形輪廓, 留 量 3、 用 1 號刀粗精車右端外形輪廓 至尺寸要求 ( 6) 圖 2 16 工序Ⅰ: 1、 用 2 號刀切 ?20× 4 退刀槽 2、 用 3 號刀切 螺紋 至尺寸要求 17 床、夾具、刀具、量具和切削液的選擇 床的選擇 根據(jù)我校實際情況可以選用 控車床。 具的選擇 由于夾具確定了零件在機床坐標系中的位置,即加工原點的位置,因而首先要求夾具能保證零件在機床坐標系中的正確坐標方向,同時協(xié) 調零件與機床坐標系的尺寸。故夾具選用三爪自定心卡盤如圖( 2三爪卡盤裝夾工件時可自動定心,不需找正。但需要注意的是,用三爪卡盤夾緊工件時,為保證足夠的夾緊力,一般要留有 20 圖( 2三爪卡盤 18 具的選擇 加工 零件 的刀具選擇: 1) 切削端面:選用 93°外圓車刀。 2) 外圓柱面車削:選用 93°外圓車刀。 3) 切槽加工:采用刀寬為 3切槽刀。 4) 切 外 螺紋:選用 60°螺紋刀。 5)鉆孔加工:選用 ?24底 鉆,利用尾座手動完成。 6)粗鏜左端孔:選用內 孔鏜刀。 7)精鏜左端孔:選用內孔鏜刀。 8) 內切槽 :選用 3切槽 刀。 9)切螺紋:選用 60°內螺紋車刀。 具的選擇 ( 1) 游標卡尺 1 把: 規(guī)格 0 精度 來測量所需加工零件的尺寸 ( 2) 千分尺 1 把:規(guī)格 0 精度 來測量所需加工零件的尺寸 ( 3)外徑百分表 1 個 :用來矯正需加工零件軸件的長度 ( 4)內徑百分表 1 個:來測量所需加工零件的內徑的尺寸 ( 5) 簧規(guī) 1 個 :用于測量 外 螺紋 ( 6) 塞規(guī) 1 個 :用于測量 內 螺紋 19 削液 的選擇 合理選用切削液,可以有效地減小切削過程中的摩擦 阻力 , 加快散熱速度 , 減少 切削力、切削溫度和 延緩 刀具磨損,提高刀具耐用度和切削效率, 使 已加工表面質量 得到提高并且能 降低產品的加工成本。 本零件的加工的切削液采用水溶液。 20 定工序的加工余量 工余量的確定 零件 外輪廓 粗加工時加工余量為單邊 定工序的切削用量及工時定額 切削用量一般包括切削深度,進給量及切削速度三項,確定方法是先確定切削深度、進給量在確定切削速度。 削用量的選擇 對于不同的加工方 法,需要選用不同的切削用量。切削用量的選擇應先確定零件加工精度和表面粗糙度,充分發(fā)揮刀具切削性能,提高切削效率,保證合理的刀具耐用度; 粗、精加工時切削用量的選擇原則如下: (1) 首先選取盡可能大的背吃刀量;其次要根據(jù)機床動力和剛性的限制條件等,選取盡可能大的進給量;最后根據(jù)刀具耐用度確定最佳的切削速度。 (2) 首先根據(jù)粗加工后的余量確定背吃刀量;其次根據(jù)已加工表面的粗糙度要求,選取較小的進給量。 具體見表 2 21 表 2軸零件 刀具 及切削用量的選擇 序號 加工面 工藝裝備 主軸轉速 ? ?1??進給速度 ? ?1/ ??1 夾零件右端使伸出 70工左端,百分表找正 三爪卡盤、百分表 2 粗車 左 端面和φ 45、φ 50 外圓 外圓車刀、端面車刀 600 精車車 左 端面和φ 45、φ 50外圓 外圓車刀、端面車刀 700 粗鏜φ 24 內孔 內孔車刀 、 游標卡尺 500 精鏜φ 24 內孔至尺寸要求 內孔車刀 、 游標卡尺 800 車 內孔 退刀槽(梯形兩邊 ),矩形槽 3 刀 400 22 7 車 左 端 內 尺寸要求 內 螺紋車刀 400 調頭裝夾, 打表校正同軸度 ,使伸出100工右端 , 修端面,保證總長164 粗車 右 端面和φ 45、φ 35 外圓 外圓車刀、端面車刀 600 0 精車 右 端面和φ 45、φ 35 外圓 外圓車刀、端面車刀 700 1 車退刀槽 (梯形兩邊 ),矩形槽 3 刀 400 2 車 右 端 外 尺寸要求 螺紋車刀 400 23 章小結 本章節(jié)主要從零件 的結構和外型入手進行有效的分析,得出所選毛坯的依據(jù)。再查閱有關資料,設計出零件加工的毛坯工序。在工藝規(guī)程的制定上,將方案進行比較,選取一個高效和節(jié)約成本的加工方案。 24 3 數(shù)控程序設計 述 數(shù)控編程是指從零件圖樣到獲得數(shù)控加工程序的全部工作過程。編程工作主要包括 :分析零件圖樣和制訂工藝方案;數(shù)學處理;編寫零件加工程序;程序檢驗。 控程序 夾 右 端加工 左 端 圖 3序Ⅰ簡圖 25 工序Ⅰ簡圖 程序 序初始化 1 號 外圓 車刀 軸正轉,轉速 600r/卻液開 速定位到加工循環(huán)起點 圓粗車復合循環(huán)加工,背吃刀量 2刀量 1 余量 量 r 向進刀 向進刀 角 向進刀 弧 向進刀 向進刀 向進刀 向 退 刀 至安全點 4 號 內孔 車刀 26 軸正轉,轉速 600r/卻液開 速定位到加工循環(huán)起點 孔 粗車復合循環(huán)加工,背吃刀量 2刀量 1 余量 量 r 向進刀 向進刀 角 向進刀 向進刀 向進刀 向 退 刀 至安全點 二號切槽刀 , 主軸正轉,轉速450r/卻液開 速定位到加工循環(huán)起點 向進刀 向進刀 向退刀 刀安全距離 27 6 號 內 螺紋刀 , 轉速 500r/卻液開 速定位到加工循環(huán)起點 紋切削循環(huán)指令螺距 29 X 進刀至 進刀至 30 X 進刀至 30 精加工 刀安全距離 序結束 圖 3序Ⅱ簡圖 28 工序Ⅱ簡圖 程序 1 號 外圓 車刀 , 主軸正轉,轉速 600r/卻液開 速定位到加工循環(huán)起點 圓粗車復合循環(huán)加工,背吃刀量 2刀量 1 余量 量 r 向進刀 向進刀 角 向進刀 向進刀 向進刀 工錐度 向進刀 弧 向進刀 向進刀 刀安全距離 二號切槽刀 軸正轉,轉速 450r/卻液 29 開 速定位到加工循環(huán)起點 向進刀 向進刀 向退刀 刀安全距離 三號螺紋刀 , 主軸正轉,轉速500r/卻液開 速定位到加工循環(huán)起點 紋切削循環(huán)指令螺距 23 X 進刀至 進刀至 進刀至 加工 刀安全距離 序結束 30 動編程與手動編程的比較 手工編程對于外形較簡單的零件簡便易行,但對于很多復雜的零件,如:非圓外輪廓、沖模、凸輪或多維空間曲面等,其編程周期長、精度差、易出錯 ,甚至無法編程。據(jù)統(tǒng)計。手工編程所需要時間與機床加工時間之比約為 30:1,因此快速準確地編制程序就成為數(shù)控機床發(fā)展和應用中的一個重要環(huán)節(jié),計算機自動編程正是針對這個問題而產生和發(fā)展起來的。 自動編程實際上是計算機輔助編程,也就是用電子計算機代替手工編程。 自動編程的優(yōu)點是效率高,程序正確性好。但自動編程需要具備自動編程系統(tǒng)或編程軟件作為支持,并要求編程人員具有一定的工藝分析和手工編程能力。自動編程較適合形狀復雜零件的加工程序編制,如模具加工、多軸聯(lián)動等加工場合。 31 4 總結 工質量檢測 在整個加工過 程中,遇到了許許多多的問題,有機床上的問題,有加工方面的問題,這些問題在老師和同學的幫助下都一一解決了,以下就是加工質量問題的分析: 首先,因為受條件限制,只能選擇 通型數(shù)控車床,其加工精度本身就不夠。 其次,夾具和刀具也會影響零件的加工精度。在加工過程中,如果夾具沒有裝夾平衡,在加工過程中就會出現(xiàn)徑向或者端面跳動的情況,從而導致產生誤差。刀具在加工過程中發(fā)熱以及刀片裝夾不穩(wěn)定都會導致刀片磨損,從而導致加工出來的工件產生誤差或者粗糙度偏大。 再者,對刀的精確也是影響加工精度的因素。我們 在加工過程中,完全采用手工對刀,靠眼睛去觀察,這樣或多或少會產生誤差,從而影響零件的精度。 最后,冷卻液也能影響到零件的加工精度。在加工時,工件與道具摩擦會產生大量的熱,從而導致工件熱變形,同時也會加劇刀具的損壞程度。因此,選擇合理的冷卻液以及冷卻方式顯得非常重要,他們會直接影響加工精度。除上述原因之外,還有些原因,如:機床主軸本身有擺動情況、機床有振動、刀刃太長,刀具硬度不夠等等都會影響到加工精度和光澤度。 32 善方法 對車床進行定期保養(yǎng),發(fā)現(xiàn)有磨損的零件及時進行更換。定期調校車床的精度,提高對刀精 度,把誤差盡可能地降低到最小。 加工時,盡量選擇剛度大、刀刃短的刀具來使用。同時,在加工的過程中,優(yōu)先采用高轉速,快進給;小切深,大切寬的工藝參數(shù),從而達到降低切削力的目的。 33 參 考 文 獻 [1] 李業(yè)農.數(shù)控機床及編程加工技術 .北京高等教育出版社. [2] 劉穎. 機械制造工藝學 [M].清華大學出版社. [3] 上海市金屬切削技術協(xié)會.金屬切削手冊 [M].上海科學技術出版社, 2002. [4] 楊叔子.機械加工工藝師手冊 [M].機械工業(yè)出版社, 2000. [5] 陳 旭東.機床夾具設計.清華大學出版社出版社. [6] 都克勤.機床夾具結構圖冊 [M] .貴州人民出版社, 1983. 4. [7] 胡建新.機床夾具 [M] .中國勞動社會保障出版社, 2001. 5. [8] 馮 道.機械零件切削加工工藝與技術標準實用手冊 [M] .安徽文化音像出版社, 2003. [9] 王先逵.機械制造工藝學 [M].機械工業(yè)出版社, 2000. [10] 馬賢智.機械加工余量與公差手冊 [M].中國標準出版社, 1994. 12. [11] 劉文劍.夾具工程師手冊 [M].黑龍江科學技術出版社, 1987. [12] 王光斗.機床夾具設計手冊 [M].上??茖W技術出版社, 2002. 8. 34 致謝 本設計是在我在指導老師的精心指導和大力支持下完成的,這篇設計的每個細節(jié)和每個數(shù)據(jù),都離不開老師的細心指導,而老師嚴謹?shù)闹螌W精神,精益求精的工作作風和寬容的教學態(tài)度都深深地感染和激勵著我。并在此同時您還在思想上、學習上給予了我無微不至的關懷,在此謹向指導老師致以誠摯的謝意。 我也要感謝我的母校,回想我在學院的兩年多的時間里,感謝各位老師對我的栽培,他們不僅在學習方面給了我很大的幫助。而且,他們嚴謹細致 、一絲不茍的作風一直是我工作、學習中的榜樣;他們循循善誘的教導和不拘一格的思維方式給予我無盡的啟迪,這些都將使我終生受益。 借此機會對他們表示深深的感謝,并祝福他們在以后的人生旅途中永遠幸??鞓?。我在這里生活和學習了兩年多的時間,我們同學、朋友們無論是在學習還是在生活及其它各個方面都給了我很多的幫助和支持。在畢業(yè)設計的編寫過程當中,我認真地聽取他們的意見,使畢業(yè)設計說明書表述更加清晰,內容更加完善。 同時感謝自己的家人 ,謝謝你們。也謝謝那么多提供我資料的人。