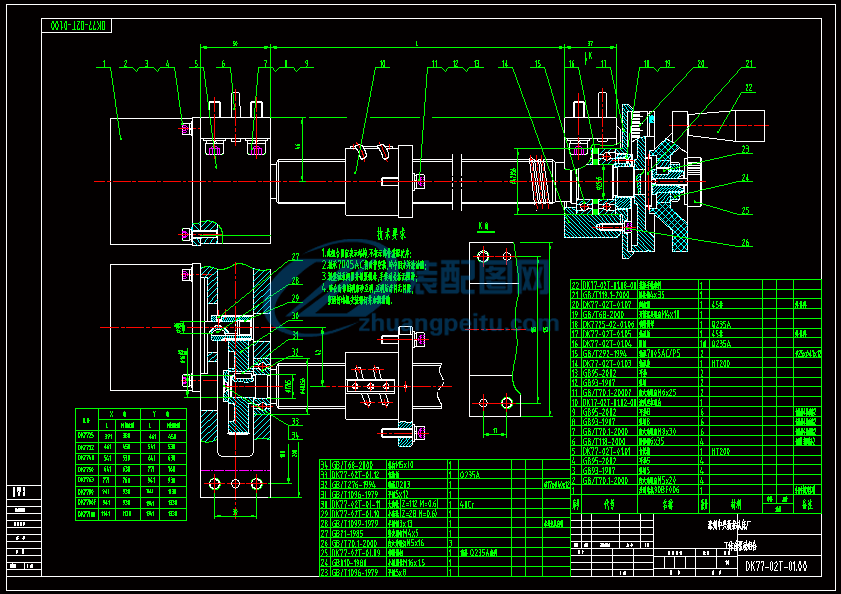
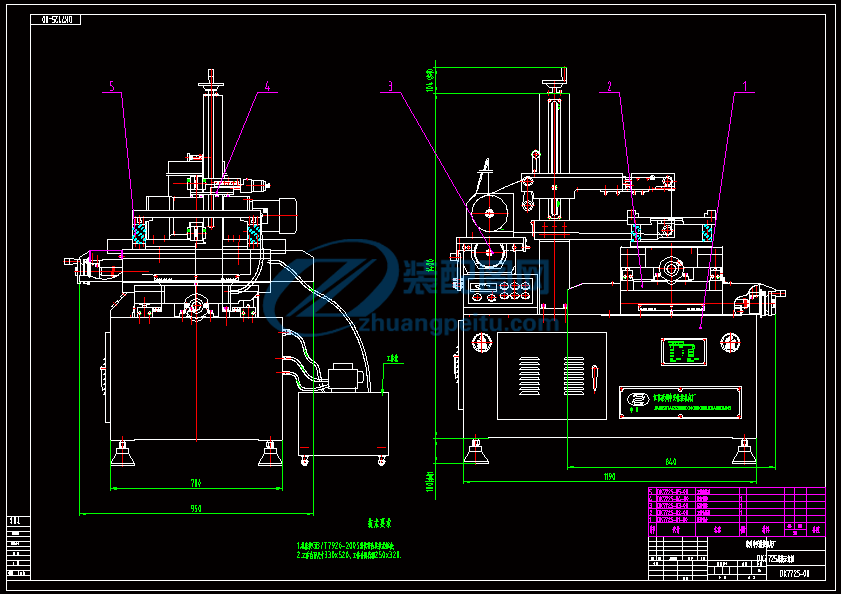
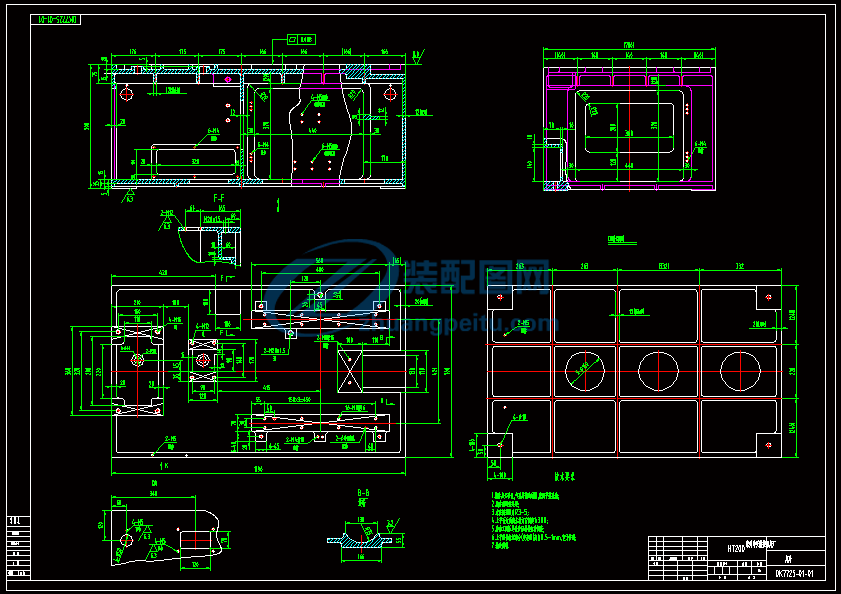
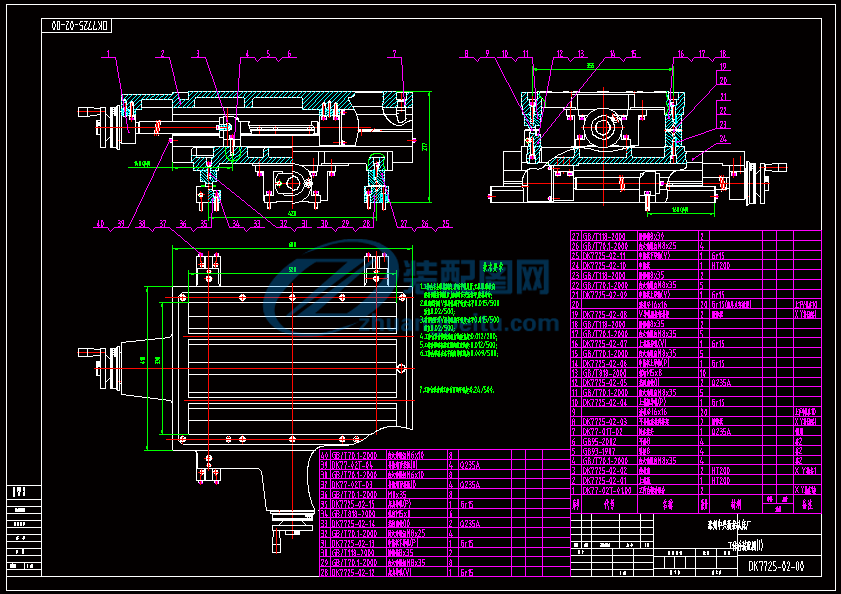
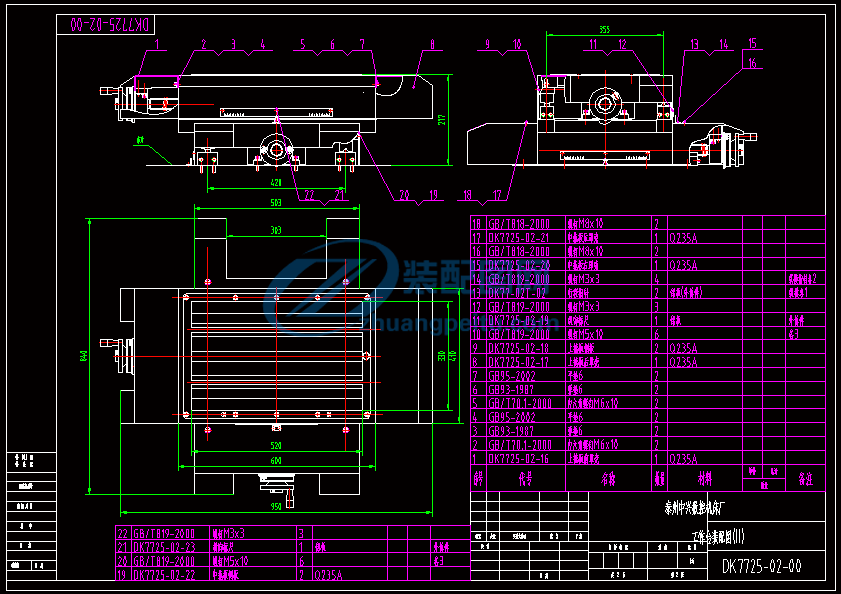
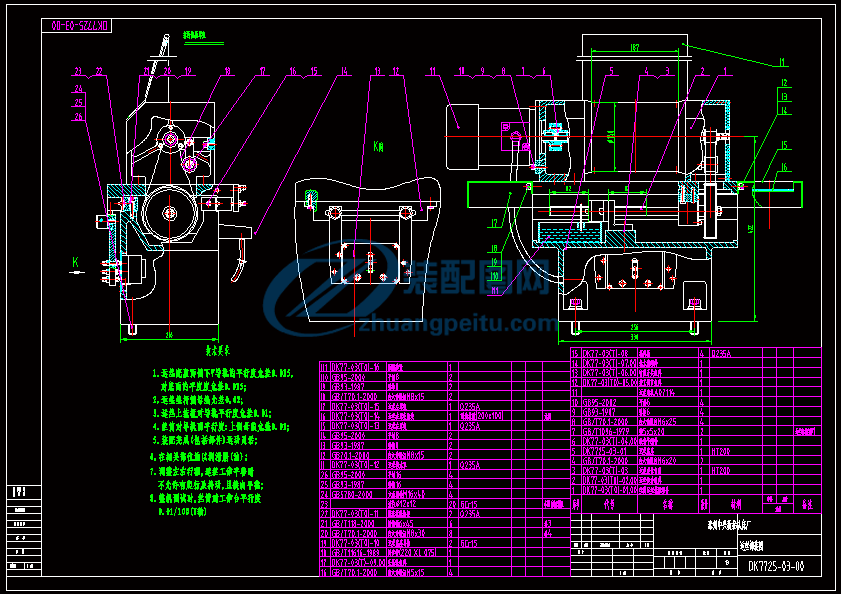
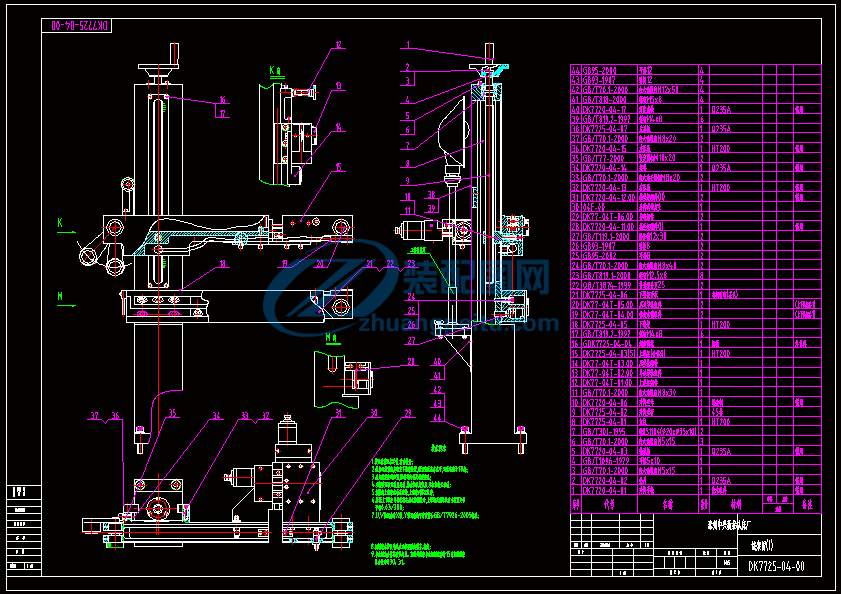
ForewordThank you for purchasing our DK77 series NC wire electrical discharge machines, and sincerely congratulate on your joining in electrical machining industry of our company.We are special manufacturer of electrical machining equipments. We have strong technical strength, leading manufacturing equipment an advanced corporate management, continuously launch high-quality products with specific features and before.- and after – sales high-quality services, and have been well recognized by the customers. Presently we already become one of the largest wire cutting machine production base in China.In order to ensure your machine will create max. economic benefits for you, please read through this manual and carry out maintenance at specified time so that your machine is in the best state for operation for efficiency maximization.Our Operation PhilosophyStriving for Best Quality, Sincere Services and 100% Customer SatisfactionOutline of CNC Wire Cutting MachineTypeTechnology parameters DK7725Worktable size (mm) 330×520Table travel (mm) 250×320Max.workpiece thickness (mm) 400Overall dimensions (mm) 1400×920×1350Wire traveling speed (M/S) 11Electrode-Wire diameter (mm) φ0.10-φ0.20Max.cutting speed (mm2/min) ≥100Machined taper (mm) 0o-12o/80 mmPower input 3N-50HZ 380VTotal power (KVA) ≤2Vertical Incorporate controller Operation PanelWire Cutting machine control systemExplanationJiangshu · Taizhou zhongxing CNC Factory · ChinaOverViewWire-cut electric discharge machine (WEDM) has molybdenum wire as its electrode wire, and operates on the following principle: the electrode, with high-frequency pulse voltage applied to it, melts or even gasifies the local metal on the working surface by utilizing the huge heat produced instantaneously in the spark passage when spark discharge is caused after sparking-through of the liquid media. Then the liquid media executes flushing, the movement of drag plate is controlled via the controller, and thus needed shape and dimension of the workpiece is formed.Principle of electric discharge wire cutting (Fig 1)Users compose a program according to the dimensions stated on the drawings and enter it into the controller. The digital controller save the program into the internal memory after receiving it. The machine starts interpolation operation after receiving machining commands, and sends a feed pulse per operation, which is driven by the power amplifier. For wire feeding system, the wire feeding motor drives the wire spool, and the travel switch drives the spool reciprocating motion. Which moves wire. The wire is near to the workpiece through the guide wheel of wire bracket. Emulsified liquid pump injects the dedicated emulsified liquid into the cutting area of the workpiece. The high-frequency pulse generated by high frequency power supply are connected to the wire and workpiece and ED machine takes place. The stepper motor generates one electric discharge machining action when it advances by one step. The gap between wire and wrokpiece is detected and the detection signal is send to the variable frequency circuit. The feed rate of the PC is controlled according to the frequency generated by the variable frequency circuit. When the gap is increase, the feed rate is also increased and when the gap is reduced, the feed rate is decreased, in order to keep constant discharge gap and thus maintain constant machining current.Wire cutting machine control system was made according to the present market requirement to the machine, synthesizing all control system’s virtue, the newest develop generation products. Consisting of three parts: computer (program and control integration computer or microprocessor controller), the HF(high frequency) and stepping motor drive power source, ce. It adopts 555 integrated circuit and power VMOS ect as resonance circuit and powerful AC circuit. Blasting the features of simple configuration, stable performance, easy operation, high working efficiency, correct and visible parameter selection, powerful output, small consumption of electrode wire, working end to auto disconnect power source, ect characteristic. It is not only suitable for machining extra thick work pieces at high speed, but also for fine machining to obtain low roughness of work piece surface. The control system is the ideal choice for both new and used machines, which will bring great benefits to you.? HF pulse power1.Main technical Data(1). Power :AC220±10V 50±1Hz(2) .Rating Power: 650 W(3). Machining voltage: 55-100V(4). Max.machining current: 6.5A(5). Max.cutting thickness:≥1015mm(6). Max.machining rate: ≥ 120mm2/min(7). Pulse configuration I.rectangular wave pulseti 5μs 10μs 20μs 40μs 80μsto 20-40μs 40-100μs 80-200μs 160-400μs 320-400μsII. groups wave pulseti/to 40μs/10-20μs150μs/150μs2.Main configuration and work principleDrawing pulse power unit structure flow chart (Fig 2)The pulse supply unit is mainly consists of rectifier circuit, main oscillator circuit and power amplifier circuit, pulse duration regulation circuit, space regulation circuit.(Please refer to Fig)Rectifier circuit: DC voltages are generated via the transformer and rectifier diode.Main oscillating circuit: 555 oscillators compose main oscillator stage, which generates pulse waveform. Pulse width “ti” can be adjusted with pulse width selector and pulse interval “to” is adjusted with 220kΩ potentiometer, it can meet to different demands for machining. Power amplifier circuit: The power amplifier circuit composed of seven fine and powerful IRFP250 VMOS tubes. It amplifies the pulse waveforms generated by main oscillator circuit and then sends the waveforms to electrode wire and work pieces so that current is provided for machining. High frequency power supply of our company provides seven power amplifier boards. Users can select different machining current values according to their demands. The features of VMOS are swift switch speed, voltage driving and big output current. Therefore , this pulse power source has the advantage of simple circuit, stability, reliance, convenient maintenance and better performance than traditional high frequency pulse power source in all aspects. Especially for machining extra thick work pieces, it working stability and reliance, the consumption of electrode wire is small.Test current of single power amplifier board:a. mean shortcircuiting current 1μ=0.6-0.8Ab. machining current I =0.4-0.6A? installation and online (1) installation The Power source is supply by AC 22V, in order to reduce the high frequency output loss and raise production rate, the nearer the power source, to the machine the better.(2) online Pulse power source and stepping motors drive power source is combined together, it has a common input connector. (see attach diagram)Parameter choice and operation method(1).Operation panel as follows diagram(Fig 3)operation panel diagram(2).Operation method and explanation a.Voltmeter indication: working voltage of HF power source cut-machining.b.Ammeter indication: indicates the current change of pulse power supply during machining.c.Voltmeter indication: working voltage of stepping motors driving power source.d.duration of pulse selector switch: it is a group of interlocking keys and indicates pulse width of various machining vaveforms. The value on each key is a pulse width(μs).when all the keys are pushed up, it is level 0.f.Commissioning switch: this switch needn’t be pressed during normal cutting. It is used only during the commissioning of pulse power supply.g.pulse interval adjusting knob: it is used for adjusting the interval time of pulse power supply in order to better remove the eroded substances and prevent wire breaks during cutting. h.power selection switch: used for selecting number of power amplifier tubes. The number on corresponding switch indicates the number of power amplifier tubes put into operation. This switch is pressed up to be turned on and down to turned off.? Operation and SericeBefore cutting working ,Turn on HF power and stepping motor drive power. Voltmeter indicator, the running of the fan behind the controller indicates the AC 200V voltage on.test pulse power supply whether normal, steps of adjust as followsa. selection appropriate duration of HF and appropriate power value .choice scope 1-13 setb.turn on commissioning switchc. Make work piece and electrode wire short to connect, look into sparks and current is normal or notd. the change of data should be done quickly when the wire storage roller changes its direction(for it shutoff HF pulse source),otherwise easy result in to burn out electrode wire Pulse power supply has three parameters: pulse width “ti”, pulse interval “to” and number of power amplifier tubes “n”. they have direct decisive effects on machining process. Therefore the key to use of pulse power is to select proper parameters according to the conditions of machined workpiece.(1) selection of pulse width(ti)The larger the pulse width is, larger energy of single pulse is, and higher cutting efficiency is. as the discharge gap is large, machining is stable, but the surface roughness is high. If low surface roughness must be obtained, narrow pulse width should be selected, so that energy of single pulse is low. But due to small discharge gap, poor machining stability will be caused. Therefore, users should select proper pulse width according different requirements and afore said characteristics.(2) selection of pulse interval(to)Since it is difficult to remove the chips for thick workpieces, pulse interval should be increased. So that enough time is allowed for chip removal and less eroded substances are generated, which can prevent wire breaks and provide stable machining. Generally, the pulse interval is proportional to the workpiece thickness. Method: adjust the potentiometer knob counterclockwise to minimum to/ti=4 and then clockwise to maximum 7.(3) selection of power amplifier tube numberPower amplifier tubes are used in parallel. The more power amplifier tubes are, the large the machining current is and higher the machining efficiency is. However, for the same pulse width, larger machining current will lead to poorer roughness. When narrow pulse width of 5μm is used for fine machining, more power amplifier tubes should be used when the workpiece is thick in order to ensure machining stability. For example, when cutting 50mm thick workpiece, more than 5 tubes should be used, as less tubes will lead to less energy of single pulse and the discharge gap will also be narrow. In this case, shortcircuiting will possibly happen and stable machining is impossible. If the user only needs high speed but does not have high roughness requirement, it can use more tubes only for the machining.Method: to turn on the power amplifier tube switch, push it up; and to turn it off, push it down Please refer to the table below.selection of HF power data Work piece material Thickness/mmPulse widthTi/μsPower value1-13 Machining current I/AMachining Efficiencymm2/min20 5-10 1-3 1.5-1.8 45-6550 5-15 2-5 1.8-2.0 50-80100 5-20 3-6 1.8-2.2 58-95200 10-40 5-8 1.8-2.5 55-90300 20-45 5-9 1.8-2.5 60-80400 20-50 5-10 2.0-2.8 62-72500 25-55 5-11 2.2-3.0 60-70600 30-60 5-11 2.5-3.2 52-60700 35-65 6-12 2.8-3.5 50-58800 40-70 7-12 3.0-4.0 45-55The metal alloy of iron900-1000 40-80 8-13 3.0-4.5 42-50? Precautions and Maintenance(1) pulse power supply unit should be grounded correctly and steadily.(2) there are 3 axial fans inside controller ,which should be often checked and cleaned in or set to ensure the normal operation because the poor air ventilation will harm the power value and VMOS.(3) in order to increase machining accuracy. Steady discharge gap is required. In case of great fluctuations of mains voltage, we recommend the regulated 3-phase AC stabilized voltage supply is used.(4) in order to avoid overcurrent caused duo to improper operations, do not change over the pulse width switch. If this switch must be changed over during machining, it should be changed over when pulse is stopped for reversing of wire feeding motor.(5) the commissioning switch cannot be pressed during normal machining, otherwise wire burning will be caused when wire feeding motor is reversed.(6) in order to reduce the high frequency output loss and raise production rate, the nearer the power source to the machine the better.In order to ensure long and normal operation of pulse power supply, surrounding environment should be kept clean and reduce the dust or oil stains attached to the circuit elements and PCBs as much as possible. Therefore good ventilation and heat dissipation should be ensured during operation as there are many power elements in the machine. If the machine is not in used for a long period. It must be turned on and checked periodically, and should be stored in dry and well-ventilated place with correct cover put on it ? Common fault analysis and service(1) no indication on the voltage meter;a.fuse broken, short circuit of rectifying bridge or other circuit;b.Mal-contact or wire broken in the voltage selection switch;c.some damage on rectifying bridge;d.interal damage of high frequency current meter.(2) no high frequency Phenomena of this fault is that no cutting operations occur when the wire feed motor and high frequency power supply are turned on and programs are entered. This fault is due to following possible causes:a.operationb.high frequency switch malfunction on the machine panel. check if the terminals are connected correctly.c.check if there is DC24V.if there is , check the relay for the high frequency primary oscillating board. d.interal faults of high frequency power supply unit. (3) abnormal increment of machining currenta.damage of VMOS. Check one by one and replace the damaged one;(if no spare tubes are available for the replacement presently turn off this tube switch, and the pulse power supply can still be used).b.faults of oscillating circuit;c.damage of the diode linking with the output end of high frequency power source;(4) No pulse voltageNo pulse voltage will lead to no outputs. In this case, first check if the power amplifier tube switch has been turned on. If it is turned on already but there are no outputs, use an oscillograph to check if the resonator in primary oscillating circuit generates pulse waveforms.(5)stepper motor is out of stepfollowing two electrical faults may cause stepper motor to be out of step a.one of the stepper motors lose phase, so that the hand -wheel wobbles, mostly due to the interface or drive faults. Check the controller output, interface board and then stepper motors.b.the preset length can be reached sometimes and cannot be reached sometimes. The most possible cause is the 24V power supply has low voltage. Replace the capacitor or damage of rectifying bridge.? vertical controller and incorporate connector 1. operation panel ( reference Fig 3)2. Signals of output 30 pins aviation interface(connect to machine-tool of taper of five –phase and ten-step)1 2 3 4 5 6 7 8 9 10workpiece Sample(+) U1 U2 U3 +24V X1 X2 X311 12 13 14 15 16 17 18 19 20X4 X5 +24V Turn off machine Cutting off +24V Y1 Y221 22 23 24 25 26 27 28 29 30Y3 Y4 Y5 V1 V2 V3 +24V Electrode wire Sample(-)3. 5 pins aviation interface definition: (1) 1,2 output (2) 3,4 power source (3) 5 earthing? attach diagram1 : Transformer of HF Power supply (definition of 20 pins rectangle interface)1 2 3 4 5 6 7 8 9 10220V 12V 1L+ 15V11 12 13 14 15 16 17 18 19 20220V 12V 1L- 15V2 :Resistance of HF Power supply (definition of 20pins rectangle interface)1 2 3 4 5 6 7 8 9 10Power amplifying switch 1L-11 12 13 14 15 16 17 18 19 201L+(V- meter +) Electrode-wire(Ammeter-) 12V 15V3 :Driver of stepping motors (definition of 20 pins rectangle interface)1 2 3 4 5 6 7 8 9 10X1 X2 X3 X4 X5 24V+ U1 U2 U311 12 13 14 15 16 17 18 19 20Y1 Y2 Y3 Y4 Y5 24V- V1 V2 V34 :definition of 14 pins interface 1 2 3 4 5 6(40μs) 7(20μs)12V 12V Fine machining Duration of pulse duration of pulse Switch8(10μs) 9(5μs) 10(80μs) 11 12 13 14duration of pulse Switch Duration pulse common- terminal commissioning5 :definition of 25 pins interface and computer25 pins interface Computer 15pins(YH adapter) Computer 25pins(YH adapter) Computer25pins(HL adapter)1 Cutting off 9 132 X1 44 13 X2 24 24 X3 25 35 X4 9 226 X5 23 217 Y1 13 48 Y2 8 59 Y3 6 610 Y4 20 2511 Y5 5 2412 Earthing 1 2013 +12V 10 1414 Turn off machine 2 1715 Turn off machine 3 1516 Cutting off 10 1817 centering 1118 VP+ 6 1619 VP- 8 1920 U1 17 721 U2 7 822 U3 18 923 V1 16 1024 V2 4 1125 V3 19 12