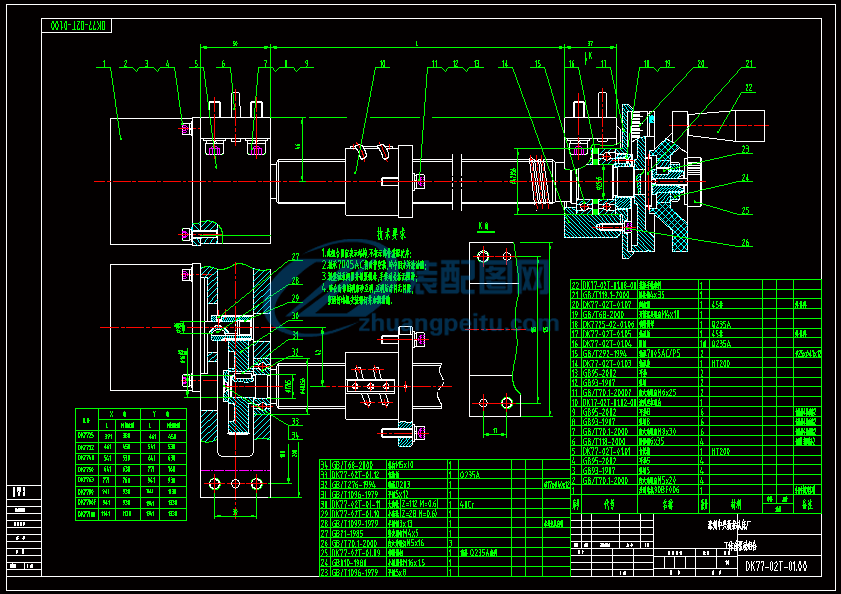
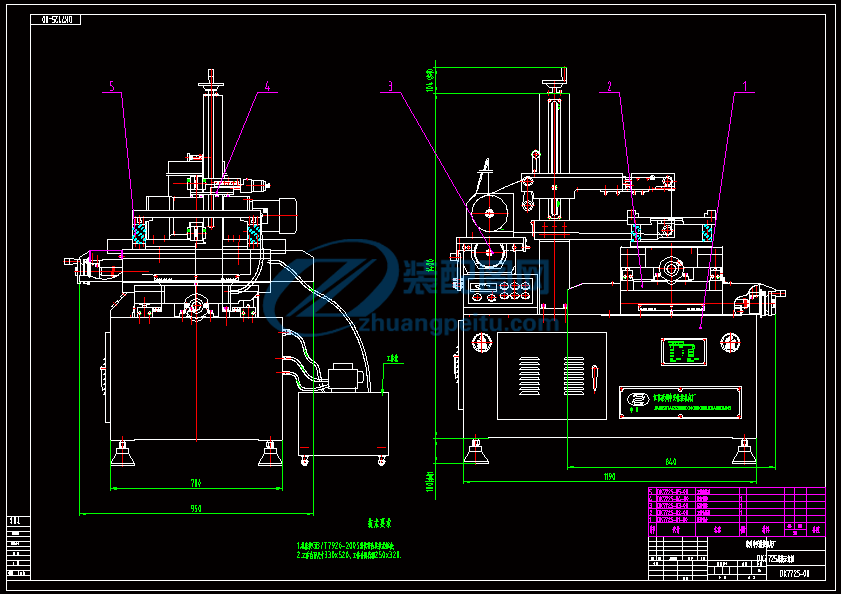
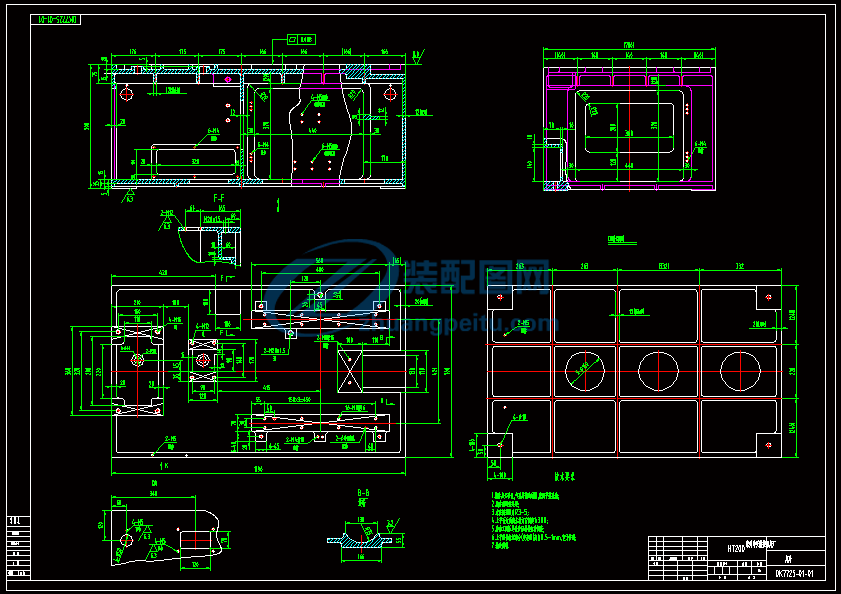
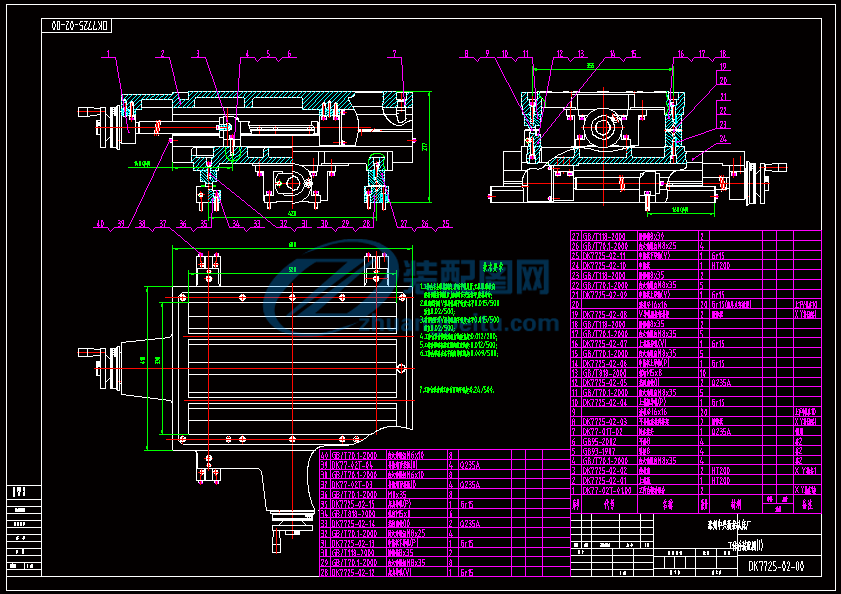
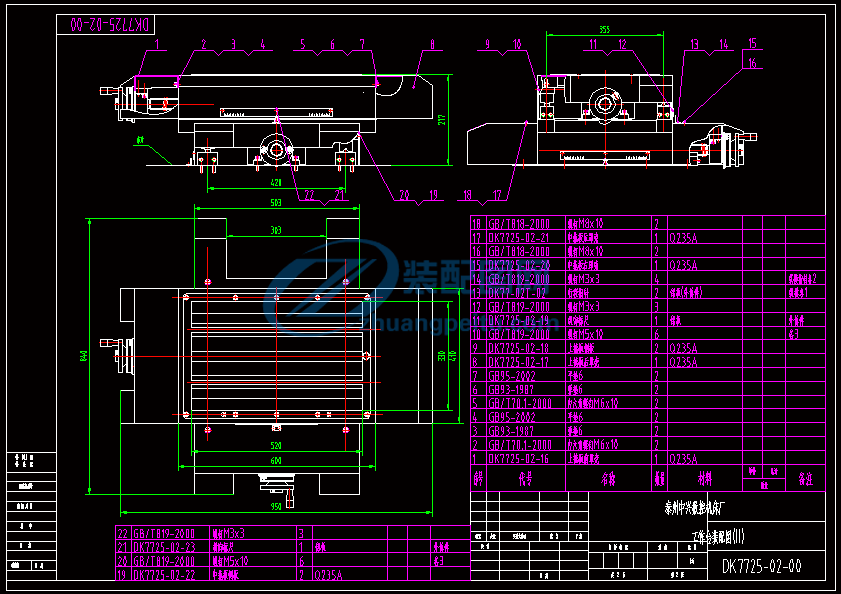
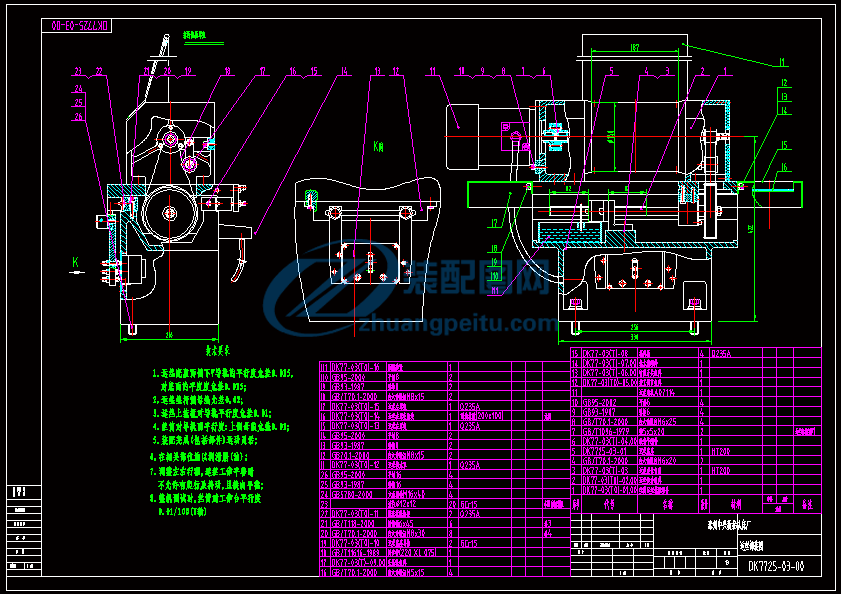
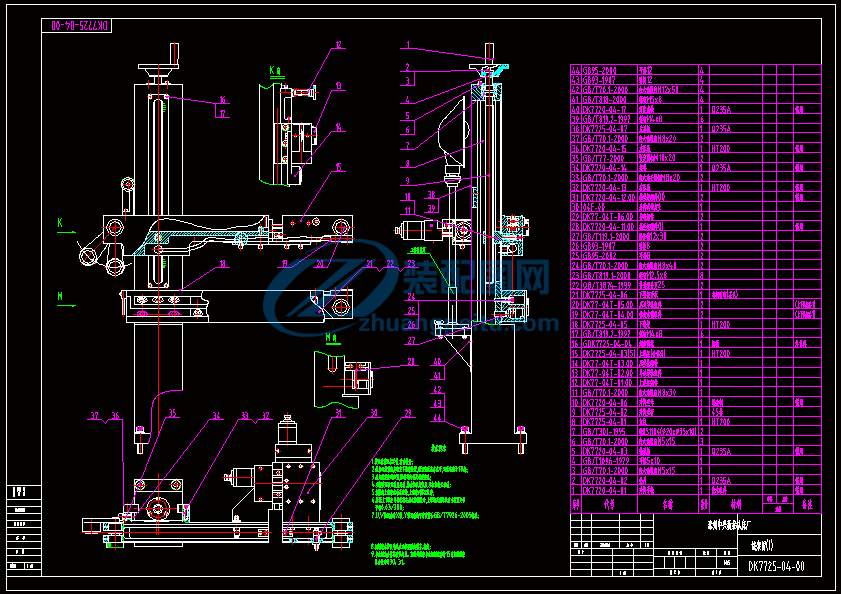
. Main uses of the machine toolThe machine tool is mainly used in processing various kinds of precise, complicated, special shaped, super-hardened (quenched steel, hard alloy) metal parts in medium and small size such as various dies and prototype. It’s numerically controlled with the advantage of high automation and adoptability and widely used in tool workshops and tryout manufacturing workshops in apparatus, Instrument, automotive, motorcycle, household appliance and daily article industries..Outline of the machine toolDK77 Series electro-discharge numerically-controlled machine tool is constituted of machine body (basement), coordinate worktable, molly wire, wire rack, work liquid circulation system and electrical and numerical control system. Coordinate worktable is controlled by numerical control system, making work piece make precise traverse and longitudinal movement as per the given rail track. The electrode wire from wire reel penetrates work piece up and down through wire rack, making back and forth straight movement at high speed. When processing, pulse electro-discharges go between electrode generates high temperature, melting the metal and forming erosion and resulting in processing purpose.Incorporated in the sliding arm of reel rack, the taper device (custom-made) can make the electrode wire to work U and V direction deviation. The interaction of four X, Y and U, V axes in vertical and horizontal direction can cut up and low special shaped surfaces or tapered parts.1. Machine bodyThe body is a case-type casting piece, incorporating electrical and workliquid cases on 2 sides or internally.2. Coordinate worktableThe worktable is mainly constituted of table pulling plate, middle pulling plate, precise screw pair and gearbox. The vertical and horizontal movement of pulling plate is realized by a rolling guide rail structure driven by step-by-step motor.The gaps of screw nuts of precise ball screw had been properly set before leaving factory, no dismantle is recommended.DK7725 machine tool uses precise thread screw.3.Wire movementThe wire-moving device realizes the straight reciprocating motion of electrode wire and its circulation application. The wire storage reel constituted of hollow cylinder which is isolated from the principal axis. The wire motion motor is connected with the wire storage reel by coupling. The revolution of the wire storage reel given electrode wire the speed of 11 meters per second which is transmitted to the precise screw pair by synchro belt wheel, realizing even wire release and reciprocating motion. The precise screw pair utilizes principal and assistant screw nuts to regulate gaps and has the security structure of exceeding travel range and nut drop. The frequent direction alternation of wire reel is controlled by a group of travel switches with the advantages of simple construction, sensitive action, low noise and long service life. When direction alternation switch fails, the travel switch cuts off power and machine tool stops.4.Wire rackThe wire rack is constituted of column, fixed arm, sliding arm and guide wheels with good rigidity. The front part of the wire rack is equipped with hardly alloy power input block, guide wheel with power input block isolated form wire rack arm. The structure adopts fully open wire penetration method. The electrode wire goes from wire storage reel to the principal guide wheel in the head of wire rack through up and low spraying mouths and then return to wire storage reel. The workpiece is fixed between up spraying mouth and low spraying mouth. The vertical degree of up and low spraying mouths should be checked before operation.There is a water valve in the work tank with 2 taps to regulate the work liquid volume of up and low spraying mouths.Rotation of the column makes the screw up or down. The sliding arm can move up and down to regulate the space between up and low principal guide wheel so as to process workpiece.5.Work liquid tankThe pump sends work liquid to the spraying mouths in the wire rack arm through the valve, when processing, the liquid sprays to the processing area through up and low spraying mouths and then returns to the tank through the receiving groove in the worktable, and then in circulation use after filtering. The tank should be cleaned periodically and kept in hygienic conditions.Work liquid is synthesized of special cutting emulsified soap and running water with ratio 1:20.6.Auxiliary partsa) Fixture The fixture constituted of clamping frame and press screw fixes plate type or column type workpiece with T screw in the worktable. The cable supplying power to workpiece is held on one side of the frame and isolated from worktable.b) Handle Up and down the screw by the handle to adjust the span of up and lower wheels.c) Tightener the wire should be tightened after a period of operation or rewinding. d) Vertical meter After the linkage of electrode wire, put vertical meter on benchmark of the clamping frame, slowly rotate the handle in X and Y direction and check if the distance from up side and low side of vertical meter to the electrode wire is equal.e) Wire positioner Fix the mo-wire spool on the wire positioner. Fix one end of the wire on one terminal of the wire storage and then start the motor to wind the wire, Fix the another end of the wire on the another terminal of the wire storage after the completion of winding..Attention matters in operating the machine tool1 During processing, the charge of workpiece and electrode wire would be dangerous to operators. So the guard covers of all parts must be in position. No touch or accession to the processing area during operation.2 the ground wiring of the machine must be reliable.3 Calculate the coordinate point and program procedure according to the design requirement and actual condition with consideration of clamping method, wire diameter and reasonable cutting in positon.4 Serious proof reading the compiled program, for complicated workpiece, it’s better make the machine tool idly operate once. Or test-cut thin piece to check the complied program one by one.5 When clamping workpiece, make sure that the area to be cut should be within the range of effective movement of the machine tool. For special requirements, it’s necessary to precisely regulate the position of workpiece and worktable to avoid waste. For processing taper, precisely calculate the travel of taper device to avoid the damage of taper device.6 When processing special shaped cavities, concave and convex dies, wire penetration hole should be drilled before in proper position.7 Check the tension of wire. If loose, tighten the electrode wire with attached tool.8 Before operation, guard cover should be put on, and the wire storage reel and the power door should be closed. During processing, the cover must not be removed to avoid personal injury. The machine tool will stop when the power door is open.9 When starting , first start the wire motor, when the operation of wire reel is in normal condition, start the work liquid pump and then open high frequency switch. Stop the machine in reversal order..Fully play the efficiency of the machine tool1 Main factors affecting the accuracy of wire cutting and detail measures to raise cutting accuracy.During cutting, the change of the electro-discharge gap between electrode wire and workpiece, and the deformation of workpiece can also cause non-negligible effect on the cutting accuracy besides the movement accuracy of the machine tool.(Ⅰ)Accuracy of machine tool: although all the accuracy of the machine tool is in conformity with requirements before leaving factory, it is still necessary for customer to check and adjust the accuracy of the machine tool before processing precise workpiece.a. Check guide wheel: Before processing, carefully check whether the V groove in the guide rail is worn out or not (see fig). Because there exists electro-erosion and sliding friction between electrode wire and guide rail during processing, there will be the worn out in the V groove after a period of working, which may cause the vibration of electrode wire, affect the processing accuracy and break the electrode wire. The guide wheel should be replaced at this time. In addition, attention should be paid to removing the eroded articles in the V groove.b. Check the power input block: The block of electrode wire is made of hard alloy. Check whether there exists groove in the block or not. If the electrode wire has been inlaid in the groove, change working position of the block or replace the block.c. Check the gap between screw pairs in X and Y direction: Due to the long time reciprocating movement, the gap between screw pairs would change. Therefore, check and regulate it before processing precise workpiece.(Ⅱ)The size of electro-discharge gap between electrode wire and workpiece has close relations with material, cutting speed and wrokliquid composites.a. The change of electro-discharge gap: Due to the different material or heat treatment methods and thickness, the electro-discharge gap would be different during processing. The different chemical, mechanical and physical functions of the materials and the processing conditions of chips removal and de-ionizing capability would also affect the electro-discharge gap.b. The relation between size of electro-discharge gap and cutting speed (current): In given processing scope, the higher cutting speed, the smaller electro-discharge gap. But the cutting speed should not exceed electro-erosion speed, otherwise it’ll result in short circuit and stop cutting. During cutting, stable processing current will make processing voltage consistent, and then the electro-discharge gap constant. Therefore, suitable pulse width, pulse interval and other electro-parameters should be chosen. Generally, rough processing with big pulse width while fine processing with small pulse width. Stable processing current makes processing speed consistent, and guaranteeing processing accuracy.c. The relation between the size of electro-discharge gap and the work liquid. Different work liquid composites have different resistance. The clips removal and de-ionizing capability also affects the size of the gap.(Ⅲ) Deformation of work piece and counter measures.The general processing route for steel work piece processed by wire cutting is: material cutdown-forging–heattreat-roughmachining- guenching & reheating-grinding-wine cutting-manual finishing. The work piece will have two bigger deformation during such process. The first deformation occurs during the heat treatment of the entire work piece after rough machining and the remaining stress inside the material will greatly increase. The wire cutting of work piece after heat treatment will damage the relative balance of the residual stress due to the bigger cutting, causing the second deformation and great affection on cutting accuracy.For example, as shown in the figure for the work piece after quenching, during the cutting of program section a-b, the work piece will result in the deformation shown in the figure by dual dotted lines.There is big difference between the finished work piece and electrode wire rack. If there is residual pulling stress inside the material, the slit will be wide. If there is residual pressing stress inside the material, the slit will be narrow.The right figure shows the deformation of work piece with hole cut During the cutting of rectangular opening, the residual stress inside the material may cause the rectangular opening deformed into drum shape or saddle shape.Such deformation will more seriously affect the processing accuracy than machine tool during cutting. The deformation can be visible and even make the material blast during cutting.After the testing in lab and analysis of all deformation factors, the measures to prevent material deformation can be as follows:(1) Choose the material with small deformation, good quenching, high yield limit alloy tool steel such as CrWMn, Cr12Mo, GCr15 etc. for processing concave and convex die.(2) Forging should be done strictly according to specification with proper starting and final forging temperature. After forging, heat retreat is necessary to reduce the residual stress as much as possible.(3) Heat treatment, quenching and heat retreat should be strictly controlled according to the reasonable process parameter with correct operation. Heating temperature after quenching should be the low limit. Cooling should be even. Reheating should be in time with up limit temperature and enough duration to eliminate the residual stress after heat treatment as much as possible.(4) Measure in process:a. Correct course order of cooling and heating, preparing for the final heat treatment so as to reduce stress and deformation. For high precise parts, conduct timely low temperature heating after cutting to stabilize the size.b. When cutting convex die, don’t cut in from outside but from outside but from the pre-made wire hole. At the same time, the part to be cut should not be close to the edge of work piece so as to make the work piece have enough strength. Otherwise it would cause the deformation and affect the cutting accuracy.Normally the size of B should be 14~18mm, if the profile size of convex die is quite big or quenching penetration is poor, the size of B should be bigger accordingly.c. It’s better to adopt twice cutting method for wire cutting the parts after heat treatment and grinding. The deformation of work piece after wire cutting should be about 0.03mm in general. Therefore, when first cutting, leaving 0.12~0.2mm unilaterally (moly wire diameter 0.18mm), and roughly processing at high speed. After first cutting, the original statues of stress balance was damaged, but new balance is reached. Then the second fine processing in this condition will improve the accuracy.d. When processing concave die, roughly cutting the cavity unilaterally leaving 0.6~1mm before heat treatment. Such die blank will go through full deformation in heat treatment. The stress balance will not be damaged due to the slight cutting, almost resulting in no deformation. For the concave die made from poor quenching penetration material, this method is good to improve and keep the quenching hardness and depth of the cavity and improve the die performance.e. It’s better to start form the place near the gravity center with reasonable clamping position, thus resulting in slight deformation when cutting to the end.f. When cutting bigger work piece, put on more clamping plates or supporting blocks in proper position to reduce the deformation due to the gravity falling.g. For small size work piece or half finished parts with long cantilever, there are more factors affecting the accuracy. It’s better to cut work piece while measure it, adjust program when necessary so as to reach the design requirements.2. Analysis of processed surface by wire cuttingMetallographic analysis and micro-hardness test of the surface indicates that there’s a non-continuous quenching hardness layer with different thickness (5~30/μm) and higher hardness than original (about HV 1000). There is a low hardness layer of 2~4μm thickness with possible shallow cracks within the quenching hardness layer. Therefore, the skin layer with Hardness of 0.001mm on the processed surface is not wearable. In order to improve the die performance, it’s necessary to leave proper quantity for manual grinding when cutting the die with small fitting gaps. The other way is to cut the convex and concave die without gap, and then remove the non-wearable layer of the cavity by punching machine. 7.Operation system of machine toolNo. Name Purpose1 Impact block Adjust the travel of wire reel2 Worktable plate Electrical operation3 Water valve Work liquid flow4 Handle on worktable Horizontal and vertical position5 Power panel Power switch and socket6 Rolling handle Space between up/low guide wheel.Lubrication system of machine toolNo. Lubrication parts Time Method Lubrication1 Horizontal feeding screw pair Once/shift oilgun No.30 oil2 Vertical feeding screw pairs Once/shift oilgun No.30 oil3 Horizontal feeding screw pairs Once/shift oilgun No.30 oil4 Vertical feeding gear group Once/shift oilgun No.30 oil5 Screw pair of wire storage reel Once/shift oilgun No.30 oil6 Guide rail of pulling plate of wire reel Once/shift oilgun No.30 oilNote:1.Replace the high-speed grease on rolling bearing in wire rack guide rail once for 2 weeks.2.Replace grease on other rolling bearings once for half year.3.Bearing in motor according to the general lubrication regulation of motor..Hoist and installation of machine toolHoist the packed Machine tool from the gravity center or move on rolling wood.Open the packed machine tool in installation workshop. Do not open with heavy impact on the body to avoid the damage of machine parts.First, remove the cover of package box and then walls of box.Remove auxiliary parts box from the package, remove rustproof oil from the surface of the machine and apply new layer of oil.Pre-install the machine after it is in the installation site, put adjustable supporting iron under the supporting rack of machine body and remove angle iron.Clean workable and put level meter on the worktable, check the vertical and horizontal level of the machine (installation level 0.04/1000).Check accuracy of all items after machine combination.The floor for the machine tool should be concrete basement away from vibration and the electromagnetic interference source..Maintenance and service of machine toolIt’s necessary condition for keeping machine accuracy and service life and improving productivity to clean, lubricate and maintain the machine tool. Following items should be attended in the operation.1.Input lubrication on time according to the lubrication requirements.2.Manually move rotation parts to check the flexibility before starting the machine tool.3.The machine tool should work in the condition with temperature between 5-35oC, relative humidity of 40-75% (no condensing dew and hanging drop) and atmosphere pressure of 86-11.0Kpa. It’ll better to work at constant temperature at 20oC for good performance.4.Clean the machine and apply oil on wearing parts after completion of processing. Periodically overall-cleaning the machine.5.Stop the work at once if fault found and send for mechanical people.6.Carefully read and understand the manual before operation..Wearing partsName Quantity Installation PositionWire storage real 1 Wire movement Guide wheel 2 Wire rackSynchro bell 1 Wire movement Conducting block 3 Wire rack