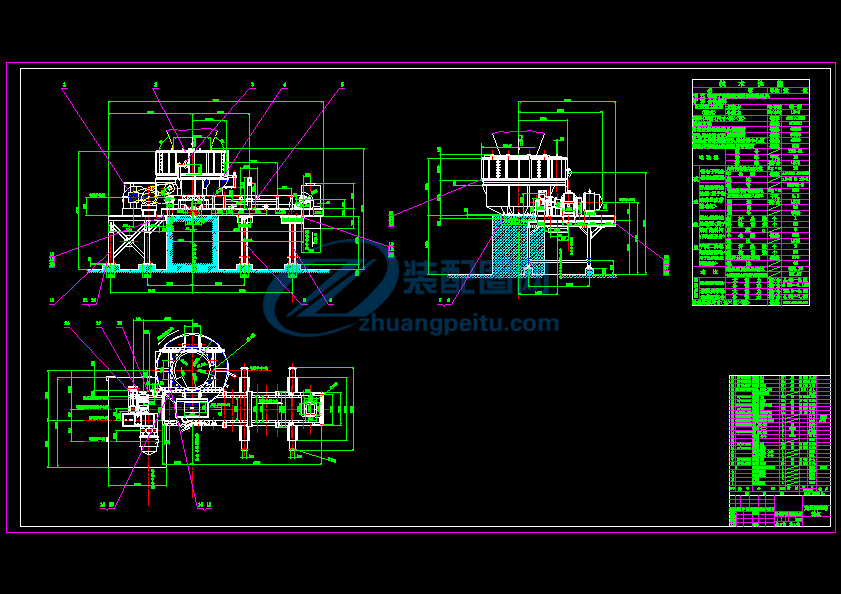
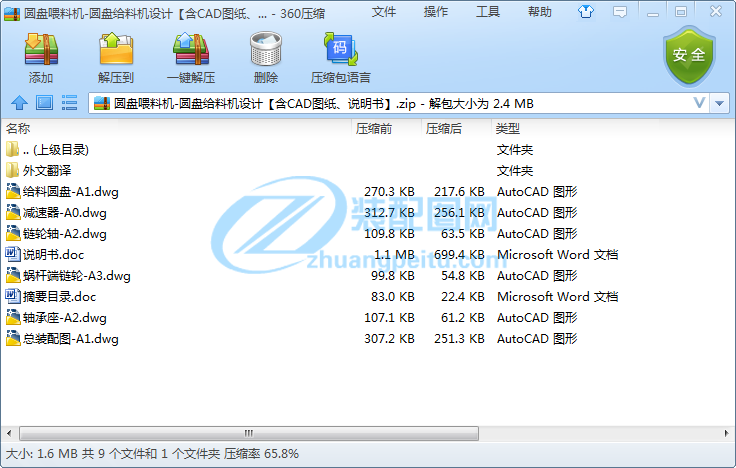
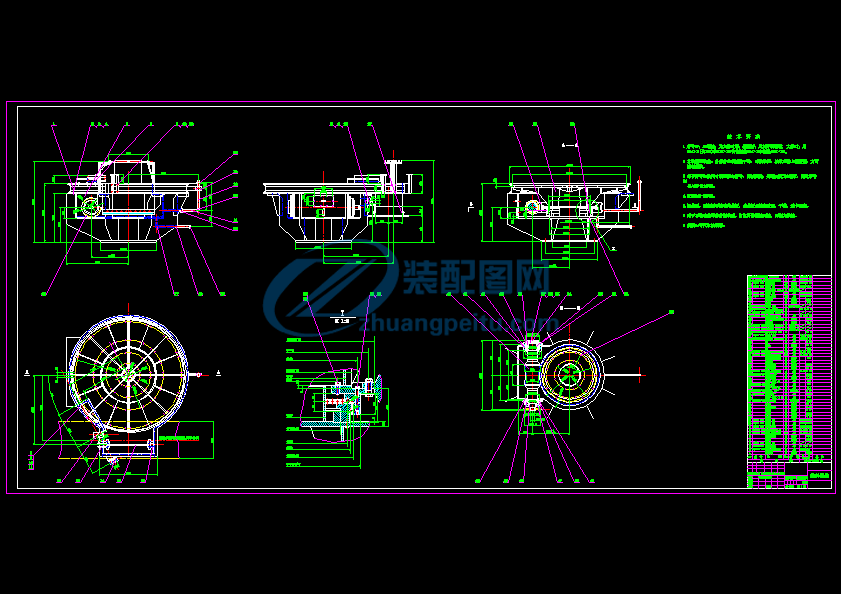
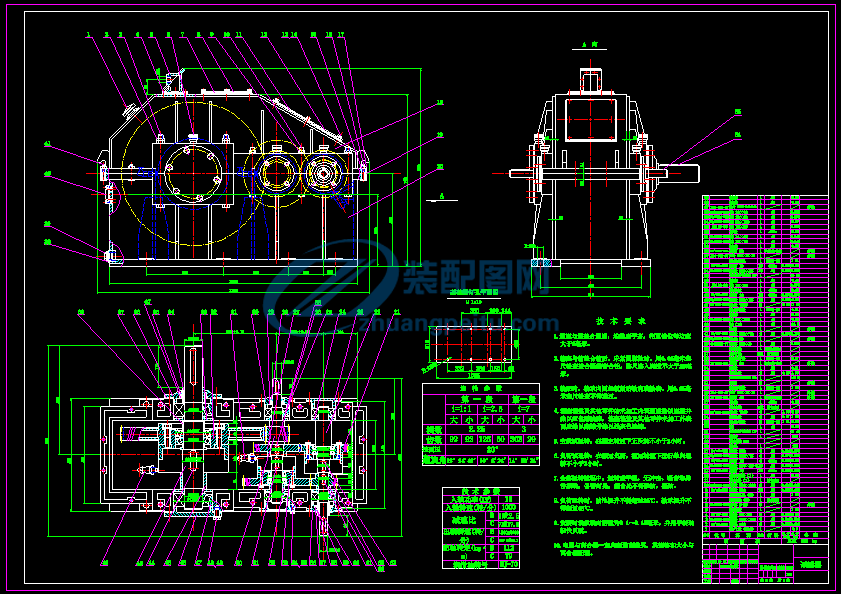
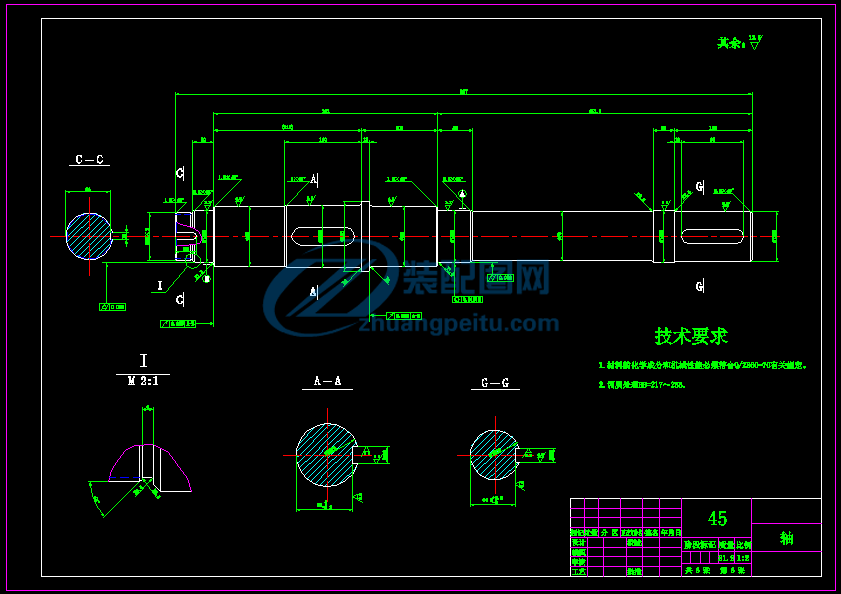
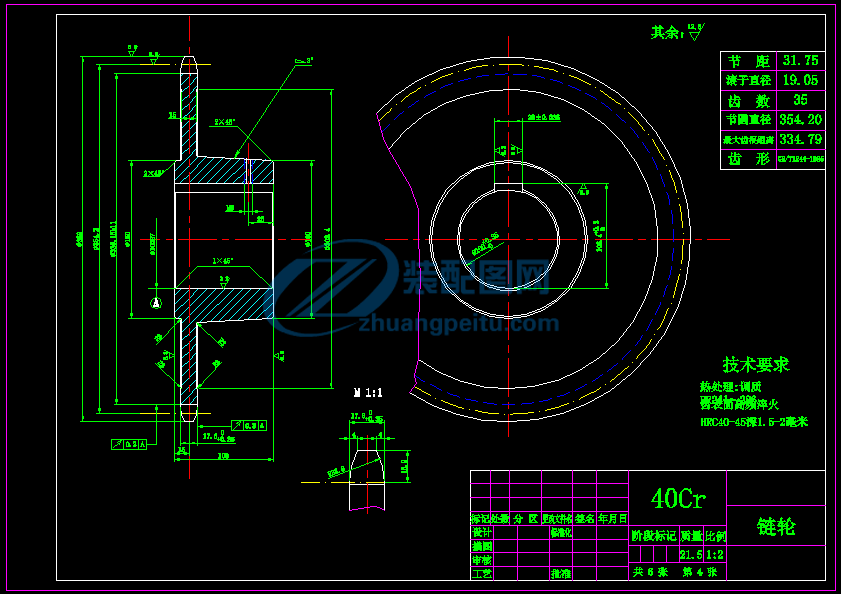
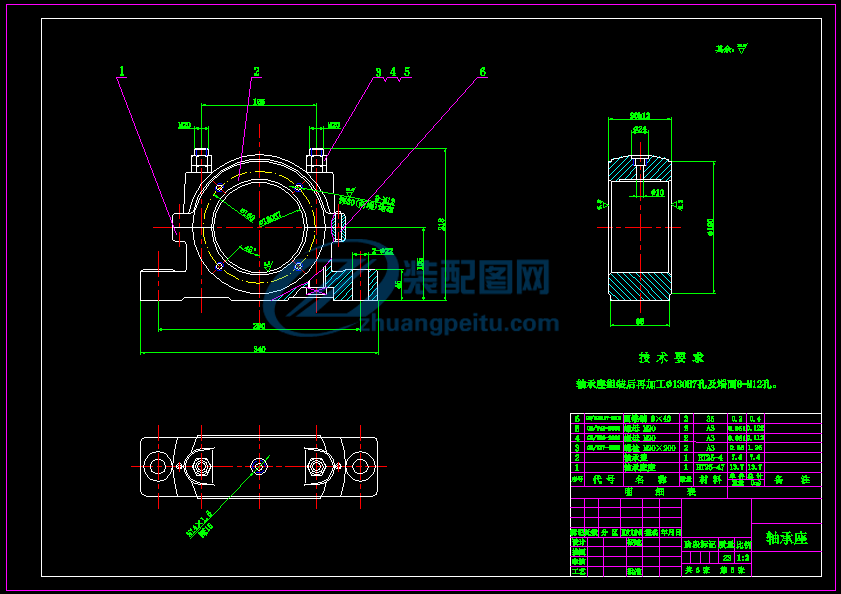
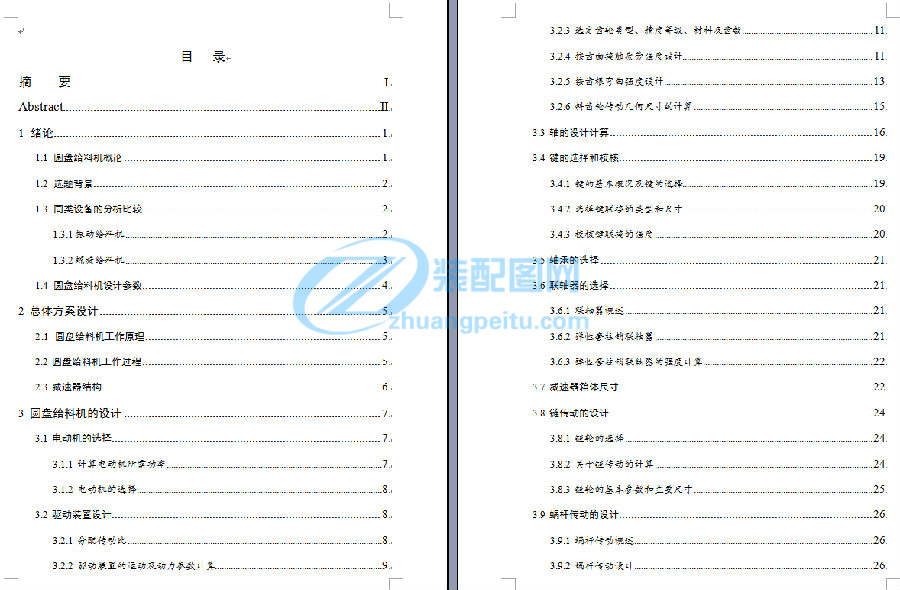
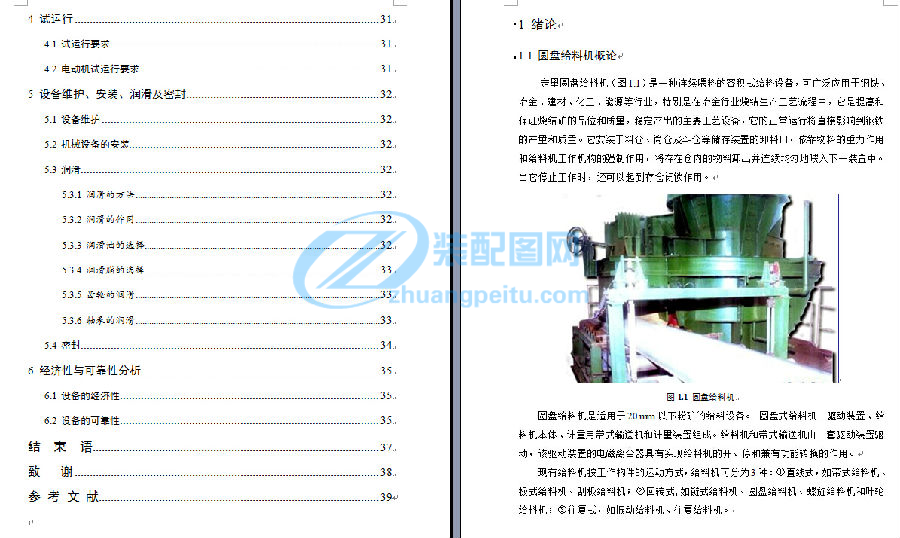

Chip screw conveyor with feed assistAbstractA screw conveyer for conveying metal turnings from a machining operation. The chip screw conveyor includes an auger-like screw configured to move metal turnings in a given direction. The conveyor includes a tubular housing and an input chute defining an input opening. A secondary feeder arm is pivoted to the conveyor housing. The arm is pivoted out of the way in direction when agglomerated scraps/chips are dumped threw input opening into the input chute. Once the chips are dumped in place, the arm is allowed to rotate downwardly to press on the top of the agglomerated scraps/chips. This prevents the chips from “bridging“ between the sides of the input chute and prevents the scraps from “balling“ or rolling on top of the screw in a manner that makes the screw ineffective. The arm creates sufficient force to press the scrap into engagement with the flutes of the screw. In an alternative embodiment, an arm includes a small secondary screw mounted to the arm for moving agglomerated scraps/chips along the arm and into engagement with the underlying screw. In yet another embodiment, an arm includes a vibrator for vibrating the arm to make it more effective. Claims The invention claimed is: 1. A screw conveyor apparatus for conveying agglomerated metal scrap that has a tendency to bridge and ball up in a manner reducing effectiveness of the screw conveyor apparatus, comprising:a screw conveyor including a housing defining an inlet chute with angled sides and a screw rotatable in the housing, the screw including an inlet end proximate the inlet chute, the housing and the screw being constructed from heavy-duty materials and designed to engage and convey highly-abrasive agglomerated metal scrap; and a feed assist operably mounted to the housing at the inlet chute, the feed assist being movable between a first position allowing addition of agglomerated metal scrap into the inlet end and movable to a second position for pressing the agglomerated metal scrap in the inlet end against an outer surface of the screw. 2. The apparatus defined in claim 1 wherein the feed assist includes an arm pivoted to the housing. 3. The apparatus defined in claim 2 wherein the arm is gravity actuated. 4. The apparatus defined in claim 3 wherein the arm is weighted. 5. The apparatus defined in claim 2 wherein the arm includes a first end hinged to the housing and an opposite end that is free to move up and down, with the opposite end being located closer to the inlet end than the first end. 6. The apparatus defined in claim 5 wherein the screw conveyor is configured to operate at an upwardly extending angle from the inlet chute. 7. The apparatus defined in claim 2 wherein the arm includes a vibrator. 8. A screw conveyor apparatus comprising: a screw conveyor including a housing defining an inlet chute with angled sides and a screw rotatable in the housing, the screw including an inlet end proximate the inlet chute; and a feed assist operably mounted to the housing at the inlet chute, the feed assist being movable between a first position allowing addition of agglomerated metal scrap onto the inlet end and movable to a second position for pressing the agglomerated metal scrap material in the inlet end against an outer surface of the screw, the feed assist including an arm pivoted to the housing, the arm including a secondary screw positioned adjacent the conveyor screw when the arm is in a downward/operating position. 9. The apparatus defined in claim 8 wherein the secondary screw includes a drive for rotating the secondary screw in a direction the same as the conveyor screw. 10. A method comprising steps of: providing a screw conveyor having a primary screw with a feed assist positioned at an inlet end of the screw conveyor, the screw conveyor being constructed from heavy-duty materials adapted to engage and convey highly abrasive agglomerated metal scrap; moving the feed assist to a first position permitting agglomerated metal scrap to be added to the inlet end; adding agglomerated metal scrap to the inlet end; moving the feed assist to a second position for pressing the agglomerated metal scrap onto the primary screw in the screw conveyor; and pressing the agglomerated metal scrap into engagement with the screw of the screw conveyor to assist in moving the agglomerated metal scrap while rotating the primary screw. 11. The method defined in claim 10 wherein the feed assist includes an arm pivoted to the screw conveyor, and wherein the step of moving includes pivoting the arm. 12. The method defined in claim 11 including vibrating the arm to improve effectiveness of the feed assist.13. The method defined in claim 11 wherein the arm is weighted and wherein the step of moving includes utilizing gravity to cause the arm to move. Description BACKGROUND OF THE INVENTION The present invention concerns screw conveyors particularly adapted for handling agglomerated metal turnings and scrap from machining operations, and more particularly concerns a feed assist for use with a chip screw conveyor. Agglomerated metal scrap from machining and lathe operations is difficult to handle since the metal scrap material is intertwined and twisted, and is very abrasive. Problems arise when trying to convey this agglomerated metal scrap since it bunches up and bridges across side portions of a conveyor chute, preventing the conveyor screw from engaging the scrap material and thus making the screw ineffective. The metal scrap material will also form “tumbleweed“ like masses that roll along a top of the conveyor screw against the operating direction of the conveyor screw. Accordingly, a feed assist is required that is relatively simple, and that will function in the environment of agglomerated metal scrap without itself causing a conveyor plugging problem. Further, it is preferable that any feed assist be compatible with existing equipment so that it is retrofitable. Accordingly, an improved apparatus and method solving the aforementioned problems is desired. SUMMARY OF THE INVENTION In one aspect, the present invention includes a screw conveyor apparatus including a screw conveyor. The screw conveyor includes a housing that defines an inlet chute and a screw rotatable in the housing with an end proximate the inlet chute. Further, the screw conveyor includes a feed assist operably mounted to the housing at the inlet. The feed assist is movable between a first position allowing addition of agglomerated metal scrap into the inlet chute and movable to a second position for pressing the agglomerated metal scrap material in the inlet against the outer surface of the screw. In another aspect, the present invention includes a method including steps of providing a screw conveyor with a feed assist positioned at an inlet end of the screw conveyor. The method also includes moving the feed assist to a first position permitting agglomerated scrap to be added to the inlet, adding agglomerated metal scrap to the inlet, moving the feed assist to a second position for pressing the agglomerated metal scrap onto the screw in the screw conveyor, and pressing the agglomerated metal scrap into engagement with the screw of the screw conveyor to assist in moving the agglomerated metal scrap while rotating the screw. These and other features, advantages and objects of the present invention will be further understood and appreciated by those skilled in the art by reference to the following specification, claims and appended drawings. BRIEF DESCRIPTION OF THE DRAWINGS FIG. 1 is a side view, partially broken away, of an apparatus embodying the present invention; FIG. 2 is an enlarged fragmentary view of a longitudinal cross section of the chute area of the screw conveyer shown in FIG. 1; FIG. 3 is a side view of a modified feed assist similar to FIG. 2 but including an arm with a secondary feeder screw thereon; and FIG. 4 is another modified feed assist similar to FIG. 2 but including an arm with a vibrator thereon. Notably, conveyor screw bearing arrangements and also vibrators are known in the metalworking and conveying industry, and accordingly it is not necessary that these components be described in detail herein for a skilled artisan to understand the present invention. It is contemplated that a variety of means can be provided on the feed assist arm to make the arm more effective, such as plungers, belts, and the like, and the present invention is contemplated to cover such arrangements. Further, different motions of arm movement can be provided to increase the effectiveness of the arm. 遼寧科技大學(xué)本科生畢業(yè)設(shè)計(jì) 第 1 頁帶有給料裝置的碎屑螺旋輸送機(jī)摘要一種螺旋輸送機(jī)用于輸送加工作業(yè)的金屬削。該碎屑螺旋輸送機(jī)包括一個(gè)螺旋式螺桿配置移動(dòng)金屬鏇在一個(gè)特定的方向。傳送帶包括管狀外殼和輸入槽和輸入口。一個(gè)備用饋路機(jī)械臂是轉(zhuǎn)動(dòng)輸送外殼。機(jī)械臂的旋轉(zhuǎn)方向正對(duì)著團(tuán)聚的碎屑從輸入口輸入到輸入槽。一旦碎屑傾倒在地,機(jī)械臂可以旋轉(zhuǎn)向下按頂部的團(tuán)聚碎屑。這樣就避免了碎屑“連接”之間的輸入槽,防止碎屑以一個(gè)使螺旋桿無效的方式在螺旋桿的頂部滾動(dòng)。機(jī)械臂創(chuàng)造足夠的力,去約束螺旋桿。在另一種體現(xiàn),安裝有一個(gè)二級(jí)的螺旋桿的機(jī)械臂,用于移動(dòng)機(jī)械臂和螺旋桿周圍的碎屑團(tuán)。另外,機(jī)械臂安裝有振動(dòng)器,使其更加有效。要求這個(gè)發(fā)明的要求是:1. 輸送燒結(jié)金屬廢料的螺旋輸送機(jī)有一種以橋連和滾動(dòng)的方式減少螺旋輸送機(jī)的影響的趨勢(shì),包括:螺旋輸送機(jī)包括直角進(jìn)槽兩側(cè)的外殼和螺桿旋轉(zhuǎn)的外殼,螺桿包括進(jìn)口和近似的入口槽,外殼和用于輸送高度磨料燒結(jié)金屬的廢料并用重型材料制造的螺桿;和安裝在輸入槽外殼處的給料裝置,可動(dòng)的給料裝置安裝在允許增加燒結(jié)金屬廢料的進(jìn)口底的第一個(gè)位置,和可轉(zhuǎn)動(dòng)的推動(dòng)燒結(jié)金屬廢料離開螺桿外表面的第二的位置之間。2. 要求 1 的條件下,給料裝置外殼上有一個(gè)可轉(zhuǎn)動(dòng)的機(jī)械臂。3. 要求 3 中提到的機(jī)械臂是重力驅(qū)動(dòng)的。4. 要求 3 中提到的機(jī)械臂是加重的。5. 要求 2 中提到的機(jī)械臂,包括一個(gè)外殼上的鉸鏈和可自由上下移動(dòng)的另一端,是另一端更靠近入口底部。6. 要求 5 中提到的螺旋輸送機(jī)被配置為運(yùn)行在從進(jìn)槽向上延伸的角度上。7. 要求 2 中提到的機(jī)械臂帶有一個(gè)振動(dòng)器。遼寧科技大學(xué)本科生畢業(yè)設(shè)計(jì) 第 2 頁8. 螺旋輸送機(jī)包括:螺旋輸送機(jī),包括含有直角邊入口槽的外殼,和在外殼內(nèi)的螺桿,螺桿包括一個(gè)入口端接近輸入槽。和一個(gè)給料裝置安裝在進(jìn)槽外殼處,可動(dòng)的給料裝置安裝在允許增加燒結(jié)金屬廢料的進(jìn)口底的第一個(gè)位置,和可轉(zhuǎn)動(dòng)的推動(dòng)燒結(jié)金屬廢料離開螺桿外表面的第二的位置之間。帶有機(jī)械臂的給料裝置安裝在外殼的樞軸上,帶有二次螺桿的機(jī)械臂被安置在輸送螺桿附近,當(dāng)機(jī)械臂在向下操作位置時(shí)。9. 要求 8 中提到的二次螺桿的驅(qū)動(dòng)旋轉(zhuǎn)方向與輸送機(jī)的螺桿旋轉(zhuǎn)方向相同。10. 包含全部方法的步驟:提供螺旋輸送機(jī)具有帶有給料裝置的初級(jí)螺桿,放置在螺旋輸送機(jī)的入口處,螺旋輸送機(jī)用重型材料制造,以適應(yīng)參與并輸送高度磨料燒結(jié)金屬廢料;移動(dòng)給料裝置到第一位置,允許燒結(jié)金屬廢料添加到入口;填加燒結(jié)金屬廢料到入口;移動(dòng)給料裝置到第二位置,壓下燒結(jié)金屬廢料進(jìn)入螺旋輸送機(jī)的主螺桿;壓下燒結(jié)金屬廢料進(jìn)入螺旋輸送機(jī)的螺桿,在主螺桿旋轉(zhuǎn)時(shí)協(xié)助移動(dòng)燒結(jié)金屬廢料。11. 在要求 10 中提到的給料裝置,包括一個(gè)安裝在螺旋輸送機(jī)樞軸上的可旋轉(zhuǎn)的機(jī)械臂,步驟中提到的可移動(dòng)的機(jī)械臂。12. 要求 11 中的方案,包括振動(dòng)機(jī)械臂臂,用于改善給料裝置的效率。13. 要求 11 中提到的機(jī)械臂是加重的,并且是利用重力來移動(dòng)的。說明書發(fā)明背景介紹本發(fā)明特別適合處理燒結(jié)金屬鏇及廢料加工業(yè)務(wù),特別是涉及到飼料協(xié)助使用給料裝置的碎屑螺旋輸送機(jī)。燒結(jié)金屬廢料加工和車床行動(dòng)難以處理,因?yàn)閺U金屬材料是相互交織和扭曲的,非常粗糙。出現(xiàn)問題時(shí),試圖輸出這一燒結(jié)金屬廢料,因?yàn)樗胁⑶覙蜻B在輸送槽的一側(cè),阻礙輸送螺桿工作,從而使螺桿失效。金屬廢料也將構(gòu)成“團(tuán)”像一團(tuán)糟,沿著輸送螺桿的上方,阻礙輸送螺桿的工作方向。因此,給料裝置,要求相對(duì)簡單,而且對(duì)燒結(jié)金屬廢料造成輸送堵塞問題起作用。此外,任何給料裝置與現(xiàn)有裝置完美配合。因此它是創(chuàng)新的。遼寧科技大學(xué)本科生畢業(yè)設(shè)計(jì) 第 3 頁因此,迫切需要改善設(shè)備和方法解決上述問題。發(fā)明概要一方面,本發(fā)明包括螺旋輸送機(jī)。該螺旋輸送機(jī)包括帶有一個(gè)入口的外殼和一個(gè)可旋轉(zhuǎn)的螺桿直通入口槽。此外,螺旋輸送機(jī)包括可操作的給料裝置在入口的外殼處??蓜?dòng)的給料裝置安裝在允許增加燒結(jié)金屬廢料的進(jìn)口底的第一個(gè)位置,和可轉(zhuǎn)動(dòng)的推動(dòng)燒結(jié)金屬廢料離開螺桿外表面的第二的位置之間。在另一個(gè)方面,本發(fā)明的方法包括提供螺旋輸送機(jī)一個(gè)給料裝置在螺旋輸送機(jī)尾部入口處的步驟。該方法還包括移動(dòng)給料裝置到第一位置,允許增加入口的團(tuán)聚廢料,增加入口的燒結(jié)金屬廢料,移動(dòng)飼料協(xié)助給料裝置到第二位置推動(dòng)燒結(jié)金屬廢料到螺旋輸送機(jī)的螺桿,并使燒結(jié)金屬廢料變形,進(jìn)入螺旋輸送機(jī)的螺桿,以協(xié)助推動(dòng)燒結(jié)金屬廢料。這些和其他一些特點(diǎn),參照一下說明,要求和所附的圖紙,本發(fā)明的優(yōu)勢(shì)和對(duì)象將得到進(jìn)一步的理解和稱贊。圖的簡單說明FIG.1 是一個(gè)側(cè)面,部分脫離,具體體現(xiàn)本發(fā)明的一個(gè)部分。FIG.2 是放大的 FIG.1 中的螺旋輸送機(jī)的縱向截面圖。FIG.3 是修改的帶有二次螺桿機(jī)械臂的給料裝置的側(cè)視圖。FIG.4 是修改的帶有震動(dòng)機(jī)械臂的給料裝置。值得注意的是,在金屬加工和輸送工業(yè),輸送螺桿和振動(dòng)器軸承布置是很常見的,因此,對(duì)這些零部件加以具體說明,對(duì)于熟練技工去了解本發(fā)明來說是沒有必要的。各種設(shè)想與手段可以應(yīng)用在給料裝置的機(jī)械臂上,使其更加有效,如活塞 ,皮帶等與本發(fā)明設(shè)想的這類計(jì)劃。此外,可以提供不同的機(jī)械臂運(yùn)動(dòng)來提升其效率。