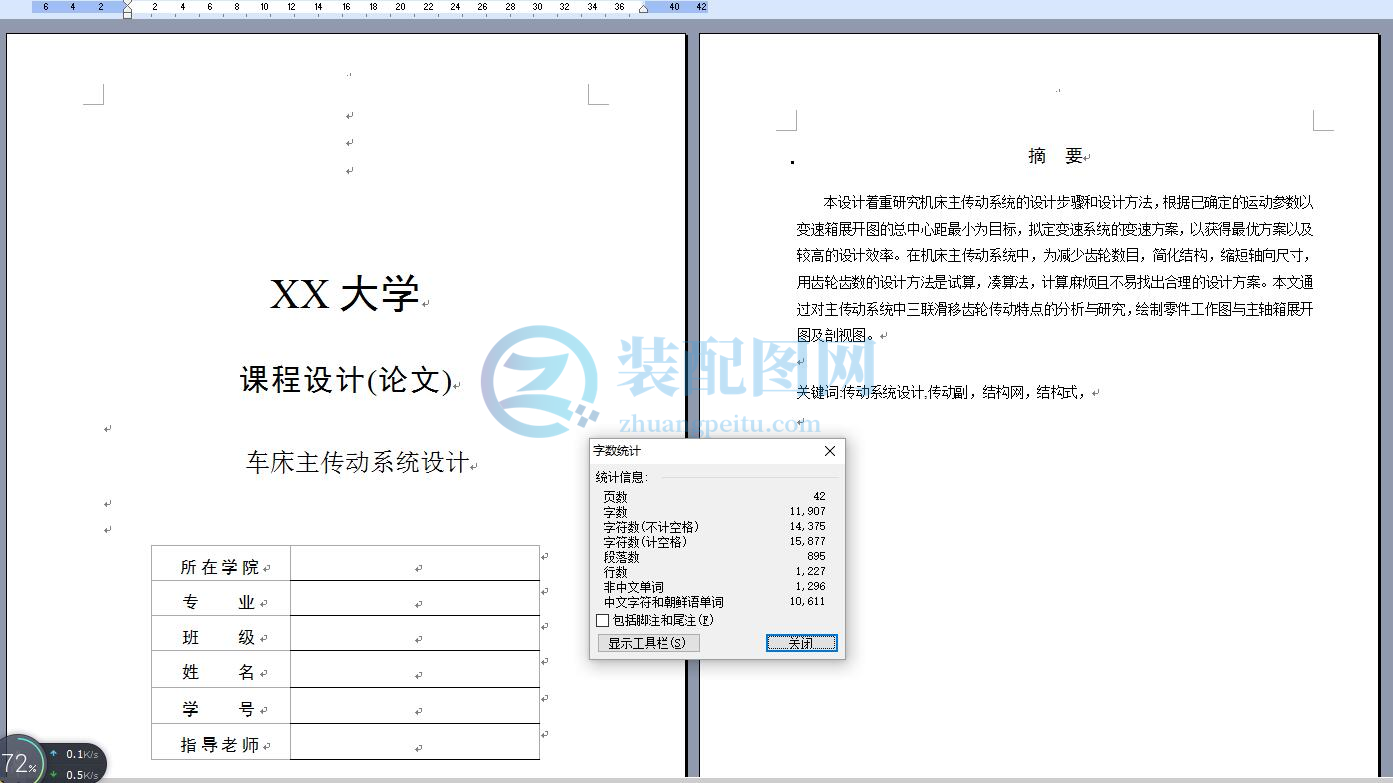
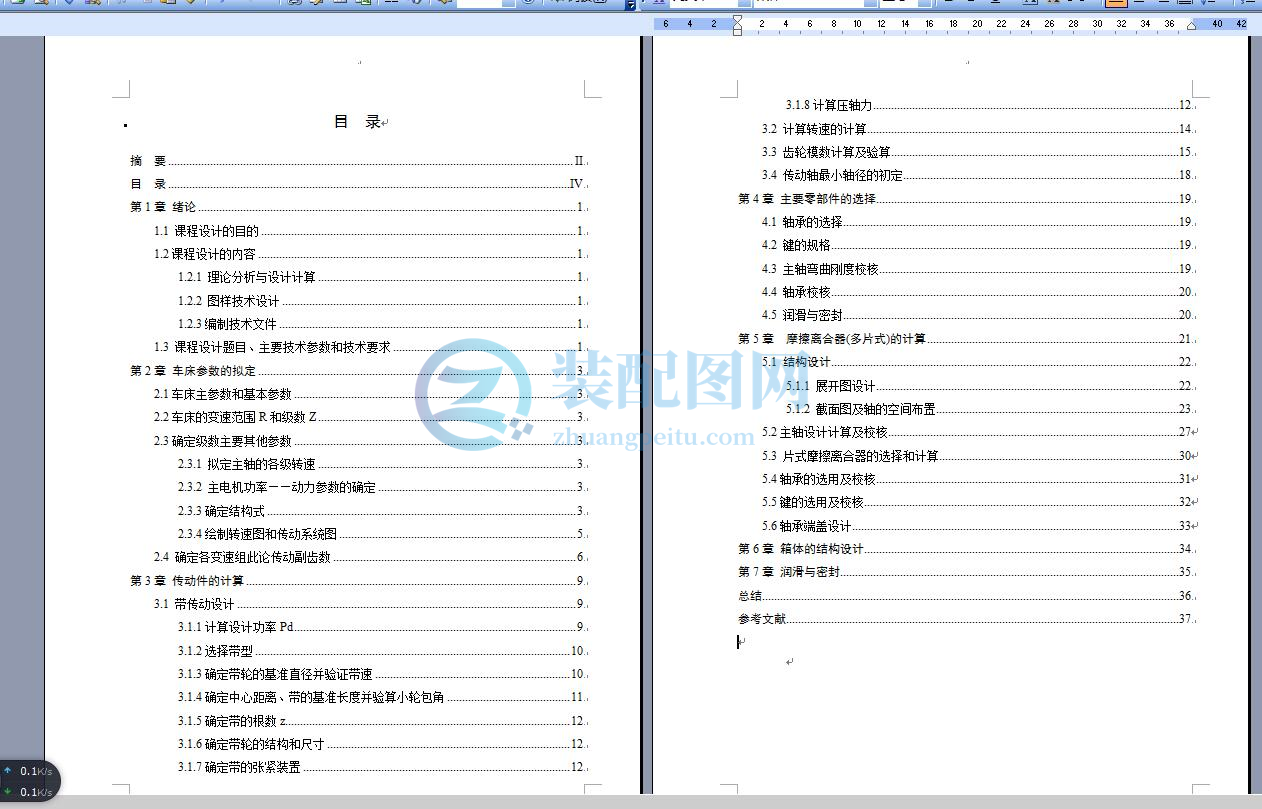

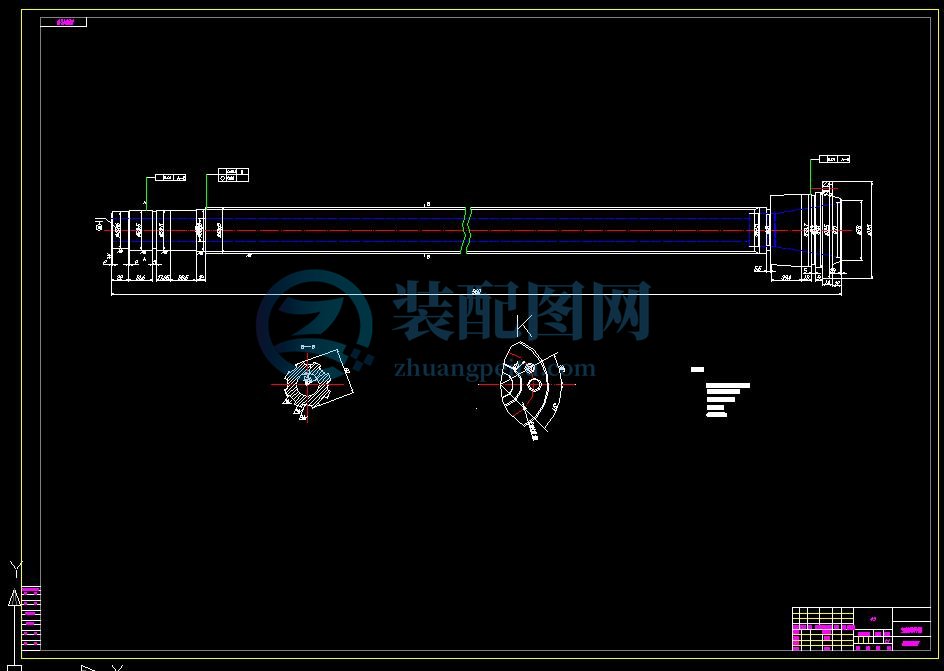
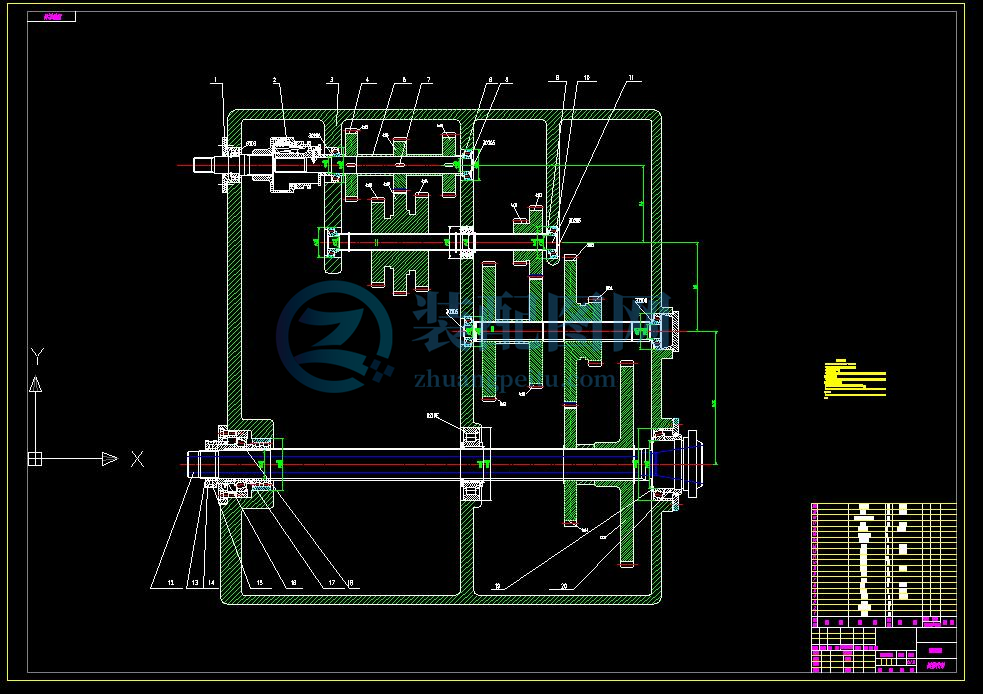
文獻綜述
齒輪作為傳遞運動和動力的基礎(chǔ)元件,在工業(yè)發(fā)展的歷程中,發(fā)揮了十分重要的作用。它在機械傳動中的地位是其它元件一直都無法替代的。隨著現(xiàn)代科學技術(shù)的發(fā)展,齒輪技術(shù)有了很大的進步,它的方方面面都在產(chǎn)生著巨大的變化。例如,在設(shè)計上,基于動態(tài)彈性嚙合理論的齒輪動態(tài)設(shè)計將取代基于剛性力學的靜態(tài)設(shè)計;在加工上,齒輪加工機床及刀具的原始精度正在不斷地提高;在檢測上,齒輪測量技術(shù)正朝著高效率、高精度、多功能和智能化的方向發(fā)展;等等。
齒輪以其形狀復雜而著稱于世,其各項誤差的檢驗項目種類繁多,并且技術(shù)上難度較大,是近一個世紀以來工程界最為關(guān)注的一項課題。我國精密測量技術(shù)和儀器的現(xiàn)狀仍然遠遠不能滿足國內(nèi)機械裝備制造業(yè)迅速發(fā)展的需求,尤其是在先進測量技術(shù)和儀器的基礎(chǔ)理論研究、共性關(guān)鍵技術(shù)的開發(fā)方面與國外的差距越來越大。因此,齒輪測量的發(fā)展尤其是復雜齒輪測量的發(fā)展必然受到很大的限制。隨著我國經(jīng)濟、技術(shù)與世界接軌,測量檢測行業(yè)受到國外先進技術(shù)的沖擊,其競爭能力也就必須加強。
目前國外發(fā)展了一些齒輪測量智能化儀器,但其價格昂貴,使用維修的技術(shù)性很強,所以大多企業(yè)還是沿用傳統(tǒng)的齒輪測量儀器或通用儀器進行齒輪測量。這些儀器的電氣控制及數(shù)據(jù)處理部分可靠性差、故障頻繁,直接影響齒輪生產(chǎn)和新產(chǎn)品開發(fā)。為了緩解這種高新科技與落后環(huán)境的矛盾,低成本地提高我國幾何量檢測的智能化程度,用微機技術(shù)對該儀器升級改造、實現(xiàn)檢測系統(tǒng)智能化很有必要。研究真正反映齒輪三維幾何空間形狀和制造誤差組成因素的齒輪整體檢測方法在我國具有積極的現(xiàn)實意義,特別是研究用檢測簡便、精確、迅速的測量方法改造現(xiàn)有測量機更為突出。
20世紀80年代以前,齒輪測量原理主要以比較測量為主,其實質(zhì)是相對測量。具體方式有兩種:一是將被測齒輪與一個標準齒輪進行實物比較,從而得到各項誤差;二是展成測量法,就是將儀器的運動機構(gòu)形成的標準特征線與被測齒輪的實際特征線作比較,確定相應(yīng)誤差。而精確的展成運動是借助一些精密機構(gòu)來實現(xiàn)的,不同的特征線需要不同的展成機構(gòu)。比較測量的主要缺點是:測量精度依賴于標準件或展成機構(gòu)的精度,機械結(jié)構(gòu)復雜,柔性差,同一個齒輪需要多臺儀器測量。對于齒廓誤差測量而言,展成式測量技術(shù)僅限于漸開線齒廓誤差測量上。對于非漸開線齒輪的端面齒廓測量,采用展成法測量是十分困難得,因為展成機構(gòu)太復雜并且缺乏通用性。
多年來,國內(nèi)外諸多學者在大型齒輪測量領(lǐng)域進行了廣泛的研究,豐富了大型齒輪測量方面的理論和方法。在檢測儀器方面,各國均開發(fā)了由計算機控制的齒輪量儀,其機構(gòu)大量應(yīng)用新技術(shù)和新元件,如計算機數(shù)控技術(shù)運用于控制、驅(qū)動、數(shù)據(jù)處理等;光柵、同步感應(yīng)器、容柵、磁柵、電感測微技術(shù)、電容測微技術(shù)、激光測量技術(shù)等用于位移測量,不斷提高齒輪測量精度??偟陌l(fā)展趨勢為:1)測量軟件功能的增強和擴展,由于大齒輪的結(jié)構(gòu)復雜大、重量重等原因,這就要促使其必須實現(xiàn)自動化的要求,即機電一體化的趨勢。用計算機進行控制,用軟件進行復雜的數(shù)據(jù)處理,也就大大提高了效率。2)實現(xiàn)自動控制系統(tǒng),由于很多機械加工場地存在一定的危險性,為了達到安全生產(chǎn)的目的,實現(xiàn)遠程控制是大勢所趨的事情。在遠程控制室工作進行實時監(jiān)控在機測量的同時還可以整理數(shù)據(jù)報告,檢驗和打印報告單,既節(jié)約時間又節(jié)約人力資源。對于測量數(shù)據(jù)的處理與利用,在早期的齒輪測量中。人工讀指示表(如千分表等)獲取齒輪誤差,得到的是誤差幅值,僅僅能用來評判被檢項目合格與否。電動記錄器的出現(xiàn),靠人工讀曲線,使工藝誤差分析成為可能。而計算機的采用,使自動處理測量結(jié)果、分析工藝誤差并將分析結(jié)果反饋到加工系統(tǒng)進而修正加工參數(shù)成為現(xiàn)實[9]。目前,在齒輪測量數(shù)據(jù)處理方面,通常采用的方法為最小區(qū)域法和最d'--乘法。理論上討論最多的是最小區(qū)域法,實際中廣泛使用的是最小二乘法,同時數(shù)字濾波技術(shù)也得到一定應(yīng)用。如今的常用漸開線圓柱齒輪測量儀器有幾十種。它們的測量方法都已經(jīng)為人們所熟知。按照齒輪測量的原理不同,可以大致把它們分為兩大類?!愂潜容^法測量,或者稱為相對測量法測量。例如。齒形測量儀通過用機械范成或電子范成的漸開線與被測齒輪的實際曲線比較并獲得誤差。這種測量方法現(xiàn)在用途極為廣泛。另一類是絕對測量法。例如,測量齒形時,把實際的齒形曲線與數(shù)學理論曲線相比較并獲得誤差。
2齒輪精度設(shè)計概述口]
漸開線圓柱齒輪精度設(shè)計涉及面廣,現(xiàn)簡述如下。
(1)公差組與精度等級
對齒輪傳動一般有四個方向的要求
①傳動準確,即傳動比變化盡量??;
②傳動平穩(wěn),即振動與噪聲盡可能?。苊猱a(chǎn)生動
載荷與撞擊;
③工作點面接觸好,即載荷分布要均勻,避免動載荷
大時齒面應(yīng)力集中,引起早期點蝕、折斷而降低使用壽命;
④齒輪副側(cè)隙要合適。
按上述分析,齒輪精度標準按誤第特性對傳動性能的
主要影響劃分為三個公差組.
關(guān)丁齒厚極限偏差和公法線平均長度偏差兩個項H,由于它們屬于側(cè)隙配臺系統(tǒng),所以不包括在上述三個公差組內(nèi)。齒輪精度設(shè)計就是要確定兩個公差組的精度等級,同時還要根據(jù)實際情況確定三個公差組內(nèi)帽膻評定指標。
圓柱齒輪加工誤差分析
何淑菊, 邱淑英
(哈爾濱工程大學 機電工程學院, 黑龍江 哈爾濱150001)
從加工誤差來看,影響齒向方向接觸精度的主要因素是齒向誤差, 影響齒距累積誤差的主要因素是齒輪的幾何偏心, 就齒輪坯基準面誤差對齒向誤差及齒距累積誤差所產(chǎn)生的影響進行分析, 并找出齒輪坯基準面跳動值的一種確定方法, 并對加工齒輪改進方法進行探討。
1齒輪坯的基準面誤差對齒向誤差的影響
準面是指加工齒輪時的定位面, 齒輪坯基準端面對齒輪軸心線的垂直誤差, 會使被
加工齒輪產(chǎn)生齒向誤差或軸向齒距誤差同理, 當安裝齒輪坯的夾具之端面 (基準面)出現(xiàn)跳動時也會出現(xiàn)類似上述結(jié)果齒向誤差不僅取決于上述兩個方面, 也受其他諸多因素的影響:
(1) 齒輪安裝誤差; 齒輪端面不平 (端面跳動) ; 夾具定位面不平 (支承端面跳動)(2) 機床刀架幾何誤差: 橫向傾斜, 縱向傾斜
2基準面誤差對齒距累積誤差的影響
齒輪的齒距累積誤差是分度圓上任意兩個同側(cè)齒面的實際弧長與公稱弧長之差最大值的絕對值, 而影響齒
距累計誤差的主要因素是齒輪的幾何偏心。, 齒距累積誤差是齒輪的幾何偏心的 2倍.在實際加工中, 引起工件偏心 的齒輪幾何偏心的原因有:
1) 由夾具心軸的徑向跳動所引起的齒輪幾何偏心e1
2) 由齒坯基準孔與夾具軸間的裝配間隙引起的齒輪幾何偏心e2
3) 由夾具支承端面與心軸軸線不垂直即夾具支承面跳動造成的齒輪幾何偏心e3
4) 由齒坯端面跳動引起的齒輪幾何偏心e4
5) 機床工作臺及錐孔等誤差造成的幾何偏心e5
6) 齒輪心軸在夾緊下變形而引起的齒坯幾何偏心e6
上述各種造成工件偏心的總和, 在向量方向未知情況下可近似的按概率法合成為
減小上述某些因素可以通過對機床安裝定位夾具或補償誤差所引起幾何偏心來消除, 但齒坯的端面徑向跳動誤差所引起的幾何偏心是不易消除的 因為工件在制造時必然存在一定的誤差, 而且工件在夾具上安裝的角相位是隨機性, 因此可按下式近似確定
式中: b為工件齒部厚度; d為定位面最大直徑;△b為工件端面在定位最大直徑上的跳動值; k為系數(shù) (根據(jù)機床、 夾具及調(diào)正的精度選擇, 一般為1—3)
)
3,齒輪基準面跳動數(shù)值的確定方法
齒輪的基準面是齒部加工的定位基準, 它的精度將直接影響齒輪的齒向、 齒輪累積誤差和接觸精度, 此項精度值一般可在標準中查得 對于某些要求偏嚴、 加工難度較大的齒輪, 為保證達到齒向誤差和齒距累積誤差的要求, 應(yīng)選擇端面跳動精度要求較高的數(shù)值, 而后把端面跳動數(shù)值做下列比較才能確定 (如圖 )
端面跳動對齒向誤差和齒距累積誤差的比較
(10)
式中: B為齒寬; △b為軸孔配合間隙;△d 為端面跳動值選定的端跳值只有符合上述公式要求才是有
效的, 反之會因 △d的干涉, 使定位面不能接觸而
失效 由上式作相應(yīng)變換,
即表明夾具心軸與齒輪孔的配合間隙也要符合上式, 才能使齒輪坯的定位基準面與夾具定位面很好的接觸
當采用重疊裝夾時, 端面跳動對齒輪精度影響為: 下層工件只受本身下面端跳動的影響, 而上層工件除受本身下端跳動影響外還受下層工件上下兩面端跳動的影響; 工件兩端面是車削而成, 所以其跳動方向不固定, 且重疊工件的裝夾亦是隨機的, 因此, 三個端跳相互獨立, 但其綜合影響亦可采用概率合成, 即
如果下層工件之端跳正好滿足精度要求,(即工藝能力系數(shù), 有 超差) , 則上層工件的工藝能力相對下降3 倍, 其超差量將增加 如果多個工件重疊裝夾,e 引起工件歪斜, 有時便會使各工件接觸面出現(xiàn)間隙或定位軸彎曲 為了保證精度, 當采用重疊裝夾加工時, 應(yīng)將公差適當縮小, 取原計算公差的0.6—0.8 倍即可, 并且控制
端跳的加工誤差
1) 加工齒輪時, 為了減少齒向誤差, 齒坯基準面誤差, 即端面跳動公差應(yīng)為齒向公差的一半
2) 齒輪基準端面跳動值應(yīng)符合式 (10 ) 要求
3) 為了提高加工齒輪精度, 應(yīng)保證齒輪毛坯端面與軸孔的垂直度、 軸孔的精度以及夾具的精度要求, 即保證夾具零件 (工件心軸、 墊圈、 螺母以及夾具底座等) 的制造精度及夾具的精度要求; 保證刀具刀桿、 刀墊、 螺母的制造精度; 刀桿直
徑按 級精度制造; 刀桿各配合粗糙度 應(yīng)在以上
用線性化方法研究直齒圓柱齒輪的動態(tài)性能
胡舸 王建宏 陳國沖
(1.重慶大學化學化工學院重慶400030;2.重慶大學機械工程學院重慶400030)
該文獻是首先建立了一對嚙臺齒輪的有限元模型,然后將用非線性方程表示的模型線性化,通過結(jié)合應(yīng)用有限元理論和接觸力學理論,得到齒輪的動態(tài)傳輸誤差(eDTE)和接觸力以及動態(tài)響應(yīng)的關(guān)系。此方法在齒輪動態(tài)研究領(lǐng)域顯示出了較強的優(yōu)越性。由于將非線性問題轉(zhuǎn)化成線性問題,避開了冗長的迭代過程,加速了求解過程。再者,在接觸及其附近區(qū)域使用接觸力學理論,僅用數(shù)日較少的單元就可得到精度足夠的解。
我國對直齒圓柱齒輪動態(tài)性能的研究已經(jīng)很長時間了。剛開始時,質(zhì)量一彈簧模型得到了廣泛應(yīng)用并得出了很多有用的結(jié)論。但是在這些研究中,系統(tǒng)的激勵被假定為方波或類似的波形,但事實上并非如此。直齒圓柱齒輪的動態(tài)性能是一種很復雜的現(xiàn)象,在本質(zhì)上是非線性的參數(shù)振動。如果不考慮制造誤差,直齒圓柱齒輪的激勵主要來自于接觸剛度的變化和傳動中同時嚙合齒對數(shù)的變化。G.L-OsTIGuY和I.CONSTANINEScu…應(yīng)用有限元法
研究了一個單齒的自然頻率、模態(tài)和由模態(tài)分析得到的嚙合過程中的瞬態(tài)響應(yīng)。R.B.BHA等發(fā)現(xiàn)有限元方法在研究輪系的動態(tài)時十分有用,因為關(guān)聯(lián)的因素可以很容易地在質(zhì)量矩陣和剛度矩陣中得到體現(xiàn)。他們使用具有兩個質(zhì)量、兩個彈簧和兩個阻尼器的模型作為研究對象,其中一組代表嚙合的輪齒,另外一組代表齒輪的其他部分的影響。AM ucHE等”提出了一種對理想齒面使用雅可比矩陣作動態(tài)約束的自動算法來計算輪齒的變形。
很明顯,按照傳統(tǒng)的思維,為了在輪齒上的接觸區(qū)域得到精度足夠的解,有限元的數(shù)目必須相當多才行,而局部細化又不適用于接觸區(qū)域在兩個物體表面移動的情形,但有限元可以以相當?shù)木扔嬎愠鼍嘟佑|區(qū)域一定距離的點的變形。另一方面,當接觸物體遠大于接觸區(qū)域時,彈性半平面法可以比較準確地給出接觸區(qū)域內(nèi)兩點的相對位移。因此,可以綜臺使用有限元法和半平面法來計算出直齒圓
1有限元分析
1.1齒輪的有限元模型
齒輪的有限元模型如圖1所示,輪齒的有限元模型如圖2所示。輪齒受力后表面情況較復雜,因此輪齒表面用八節(jié)點的單元來表示,而在其余地方,情況相對來說比較簡單,用常用的四節(jié)點單元來表示。齒輪主要用來傳遞力矩,就齒輪總體而言,非線性變形主要集中在輪齒上,離輪齒越遠的地方,也就是說離齒輪中心越近的地方,齒輪的變形和受力情況相對越簡單,因此有限元單元的數(shù)目也就相應(yīng)地減少。
1.2數(shù)學模型
直齒圓柱齒輪的動力學模型如圖3所示,可以用以下方程來表示。
在許多有限元分析中,阻尼矩陣。是用質(zhì)量矩陣Ⅲ和剛度矩陣島的線性組合來表示,也就是Ray.1ei曲阻尼模型
式中η和λ是線性系數(shù)。在這里,為了表示方便,可以將主動輪和從動輪的式(1)表示組合起來寫成齒輪對的有限元表示
1.3非線性方程的線性化
應(yīng)用Newmark方法對式(3)離散化,可寫成以下形式
B—一個已知的、非方陣的矩陣,用來將接觸力分配給附近的節(jié)點,矩陣B
決于單元的邊界幾何以及有限元的插值模式
R—動態(tài)項
1.5相對于接觸點的參照點位移
對于相互嚙合輪齒上的一對接觸點,盡管在輪齒的表面是八節(jié)點的單元,但由于輪齒嚙合的復雜性,不能直接由節(jié)點位移根據(jù)位移模式來計算接觸點的位移。但是位于接觸點正下方,距其一定距離的參照點的位移可以用有限元法相當準確地計算出來。而接觸點和參照點之間的相對位移可由彈性半平面法來計算。下面首先用有限元法計算齒輪上參照點的位移
式中,u和v,分別表示參照點在z軸和y軸的位移。G是已知的,由有限元位移模式和參照點的坐標決定的矩陣,用來從有限元節(jié)點位移計算出參照點位移。下標r表示是參照點,下標x和y表示x坐標和y坐標。
1.6接觸點和參照點之間的相對位移
一對相互嚙合的齒輪,輪齒在接觸點的外形輪廓應(yīng)為漸開線,但由于接觸區(qū)域相當小,因此,可以近似地認為接觸區(qū)域的輪廓外形為圓弧,其半徑可由齒輪的漸開線方程得到。
1.7接觸點的位移
齒輪輪齒表面上接觸點的位移是由參照點的位移加上接觸點和參照點之間的相對位移。
如圖4所示,f和f分別表示一對嚙合齒輪的輪齒表面曲線。西表示輪齒上的兩個可能接觸點在未變形之前的初始距離。全局坐標系為x,y,位于接觸點的局部坐標系為x7,y’。局部坐標系的y’軸方向為接觸點的法線方向。d為主動輪和從動輪上接觸點到參照點之間的距離。由式(9)得到的參照點位移為全局坐標系x,y下的位移,利用旋轉(zhuǎn)矩陣將其轉(zhuǎn)換成局部坐標系z’,y’下的位移。一對共軛齒輪,如果不考慮齒輪的彈性變形,接觸點的軌跡應(yīng)為齒輪的嚙合線。但實際上齒輪承載以后,齒輪的彈性變形使得實際接觸點不再是嚙合線上
的點。對于接觸分析而言,由于輪齒受力后實際接觸點應(yīng)在理論接觸點附近。因此,將輪齒表面上理論接觸點附近的區(qū)域離散化,在齒面的法線方向計算出一系列的可能接觸點, 并計算這些可能接觸點對在受力前的距離,然后將可能接觸點對的距離與動態(tài)項相加,距離最近的可能接觸點對作為實際接觸點。
從該文獻我們了解到使用有限元和接觸力學研究一對參數(shù)相同的齒輪對的動態(tài)性能。接觸力是通過在接觸齒對的半分析法的有限元公式得到。所使用的方法具有以下顯著特點。
(1)需要作任何假設(shè),它克服了有限元法在靜態(tài)分析、響應(yīng)計算等應(yīng)用中的一些限制。
(2)由于在接觸點不是靠增加單元數(shù)目來提高精度,因此所使用的有限元數(shù)目大為減少,相應(yīng)地減少了計算時間。
(3)晟后聯(lián)立求解的方程都是線性方程,求解過程耍遠比直接求解非線性方程簡單,因為目前非線性方程的求解一般都是采用迭代法。
(4)本方法特別適用于離散動態(tài)模型中嚙合建模比較困難的多體多接觸系統(tǒng)。
在三坐標測量機上精確測量漸開線圓柱齒輪的齒形誤差
黃富貴 張認成
華僑大學
針對傳統(tǒng)齒針對傳統(tǒng)齒形誤差測量方法的測量誤差來源多、 測頭與工件裝調(diào)整誤差大等缺點, 提出一種在三坐標測量機上利用掃描法實現(xiàn)漸開線圓柱輪齒形誤差測量的新方法。該測量方法具有測量采集點精度高、 齒形輪廓曲線擬合誤差小、 測量過程與誤差處理過程人工干預少、 測量精度高等特點。
齒形誤差是反映齒輪工作平穩(wěn)性精度的重要指標之一, 齒形誤差的精確測量與評定可以有效地判定第 公差組的性能指標, 同時, 通過對齒形誤差測量結(jié)果的分析, 可以找到誤差的產(chǎn)生原因, 為齒輪加工機床參數(shù)的調(diào)整、 刀具的修磨等提供科學依據(jù)。因此, 齒輪齒形誤差的精確測量一直以來都是齒輪
測量技術(shù)人員的一個研究熱點。目前, 漸開線圓柱齒輪齒形誤差的測量方法主
要有標準設(shè)計齒形比較法、 標準漸開線軌跡法和坐標測量法等三大類。標準設(shè)計齒形比較法是將被測實際齒形與標準設(shè)計齒形曲線進行比較而得到齒形誤差的方法。該方法的主要問題在于: 被測齒輪端面與齒輪定位孔的孔心線垂直度誤差、 成像誤差等將直接影響測量結(jié)果的準確性。因此, 該方法只適于盤類齒輪齒形誤差的測量, 而且測量精度低, 一般只能對/級以下精度的齒輪進行測量。標準漸開線軌跡法是將被測齒形與儀器復現(xiàn)的標準理論漸開線軌跡進行比較, 求出齒形誤差, 并通過在直尺—基圓盤式、 圓盤—杠桿式等機械展成儀或電子展成儀上實現(xiàn)。該方法的主要問題在于: 儀器的基準誤差被測齒輪的安裝誤差以及基圓盤的直徑尺寸誤差等對測量結(jié)果影響較大。坐標測量法是將被測齒形上若干點的實際坐標與理論坐標進行比較的一種測量方法。采用這種方法測量必須解決兩個問題: 實際坐標的獲?。?理論坐標的計算。該方法的主要問題是計算繁瑣特別是測點要求多、 測點布置有特殊要求時,數(shù)據(jù)處理工作量大。針對目前齒形誤差測量與數(shù)據(jù)處理的缺點,本文提出了一種在三坐標測量機上利用掃描法實現(xiàn)測量點數(shù)據(jù)采集、利用三次樣條函數(shù)實現(xiàn)齒形工作曲線擬合、利用展成法實現(xiàn)齒形誤差評定的漸開線圓柱齒輪齒形誤差測量的新方法。該測量方法測量點數(shù)據(jù)采集與齒形誤差評定簡便,測量效率高,測量精度高。
1,其原理如下
GB10095-88《漸開線圓柱齒輪精度》中齒形誤差的定義為:在端截面上,齒形工作部分內(nèi)(齒頂?shù)估獠糠殖猓┌輰嶋H齒形且距離為最小的兩條設(shè)計齒形間的法向距離。設(shè)計齒形可以是修正的漸開線(包括理論漸開線、凸齒形和修緣齒形等)圖1齒形誤差測量簡圖。根據(jù)漸開線圓柱齒輪齒形展成法的形成原理,理論齒形上各點的展開角增量△Φ與△g應(yīng)的展開長度增量 應(yīng)滿足以下關(guān)系式
式中r為齒輪的基圓半徑,可由被測齒輪參數(shù)求得。若被測齒輪為漸開線圓柱直齒輪rb=m**cosa/2;若被測齒輪為漸開線圓柱斜齒輪,則rb=m*Z*cosat/2,rb單位為mm?!鱣為展開長度增量,△Φ 為角度增量。
2,其測量方法是要實現(xiàn)對被測齒輪齒形誤差的評定,首先應(yīng)得到被測齒輪的實際齒形輪廓曲線。該曲線可以采取如下方法獲得:先對實際齒輪齒形輪廓上有限點的坐標數(shù)據(jù)進行精確采集,然后采用三次樣條函數(shù)將實際齒形輪廓上有限點擬合成連續(xù)曲線。三次樣條函數(shù)的主要優(yōu)點是其光滑程度較高,保證了插值函數(shù)一階、二階導數(shù)的連續(xù)性。因此,實際齒形曲線用三次樣條函數(shù)擬合在理論上可行,而且符合齒輪的 設(shè)計要求。三次樣條函數(shù)的擬合精度主要決定于采集點的多少與分布形式。實際測量中,采集點應(yīng)主要分布在齒輪正常工作齒面上,靠近齒頂或齒頂修緣部分盡量不采點;過渡漸開線與正常工作齒面交界處以下部分不采點;靠近齒輪分度圓附近采集點應(yīng)分布較密,靠近齒頂和齒根部采集點應(yīng)分布較疏,采集點的數(shù)量也不要太多。測量實踐表明:對于模數(shù)為’22的齒輪,齒面上的采集點數(shù)一般控制在 *%點以下,這樣可以得到較高的擬合精度。
從該文獻我們了解到在Status FX 777型三坐標測量機上利用掃描法實現(xiàn)漸開線圓柱齒輪齒形誤差的測量方法,可克服傳統(tǒng)齒形誤差測量方法的測量誤差來源多、測頭與工件安裝調(diào)整誤差大的缺點。同時,該測量方法除測量數(shù)據(jù)采集、實際齒形輪廓曲線的三次樣條函數(shù)擬合需要人工干預外,數(shù)據(jù)處理與齒形誤差的評定全部依靠計算機完成,測量誤差與評定誤差小,測量簡便實用。理論分析與比較測量實驗結(jié)果表明:該測量方法的測量精度高,適合于盤類漸開線圓柱直齒輪和斜齒輪齒形誤差的精確測量。
計算機輔助漸開線圓柱齒輪精度設(shè)計
李亞非,王 誠
(長沙理工大學 汽車與機械工程學院,湖南 長沙 410114)
介紹了筆者開發(fā)的一種用Visual C++語言編寫的齒輪精度CAD軟件,該軟件操作簡單,采用了新國標,能快速正確地確定齒輪的精度等級、 檢驗項目及公差值,并可生成齒輪零件圖,實例證明軟件正確可行。
齒輪精度的高低,直接影響到齒輪傳動的工作性能和使用壽命。因此,各國先后多次制訂和修訂了廣泛應(yīng)用于汽車、飛機、 機床、 工程機械、 農(nóng)業(yè)機械、 儀器儀表等機械產(chǎn)品中的圓柱齒輪精度標準。但整個齒輪精度設(shè)計過程十分繁瑣,要查取多張表格,用到的計算公式多而復雜,設(shè)計工作量大,花費時間多,且易出錯。對此,人們想到了計算機輔助設(shè)計的方法,基于 GB/T10095—1988 《漸開線圓柱齒輪精度》 的 CAD系統(tǒng),大多采用 VB 語言編程及三個公差組來控制齒輪公差。本文介紹一種采用Visual C++語言自主開發(fā)的基于2008 年新國標的設(shè)計軟件,摒棄三個公差檢驗組的分類,根據(jù)齒輪工作環(huán)境選擇推薦的檢驗組,用該軟件可以輕松完成齒輪精度設(shè)計工作。
1 軟件的界面設(shè)計
Visual C++是一種面向?qū)ο蟮某绦蛟O(shè)計語言,提供可視化編程工具應(yīng)用程序向?qū)?AppWizard 和類向?qū)?ClassWizard,用它可以方便的設(shè)計出良好的圖形用戶界面。圖 1 為本軟件的界面(含一個實例的運行結(jié)果) 。它用一個界面集成了兩大功能:設(shè)計參數(shù)的輸入,設(shè)計結(jié)果的顯示及輸出。 運行時,用戶只需對有關(guān)控件進行簡單的操作(如在文本框中輸入已知參數(shù)值,或用鼠標點擊按鈕等)就能完成相應(yīng)的任務(wù)。
2 軟件的工作流程設(shè)計
根據(jù)最新的國家標準以及參考文獻第 10 章第 5 節(jié)介紹的圓柱齒輪精度設(shè)計方法和步驟,圓柱齒輪精度設(shè)計的主要內(nèi)容有:
(1)齒輪精度等級的確定;
(2)單個齒輪精度評定指標的確定;
(3)齒輪副精度評定指標的確定;
(4)齒坯精度的確定。
該軟件的工作流程見圖 2。
其流程圖的設(shè)計要點簡介如下:
2.1 輸入已知參數(shù)
在 “輸入已知參數(shù)” 框架內(nèi),包含有 10 個文本框,2 個下拉列表框,下拉列表框中列出了機床、 輕型汽車、 重型汽車、 汽輪機減速器、 一般減速器、 起重機、 農(nóng)業(yè)機械等不同用途的齒輪,輸入齒輪的齒數(shù)、 模數(shù)、 轉(zhuǎn)速、 應(yīng)用范圍等已知數(shù)據(jù)。 確定精度等級
2.3 確定單個齒輪檢驗項目
GB/T 10095—1988 將單個齒輪的各項公差分為三個公差計算機先根據(jù)齒輪應(yīng)用范圍,使用要求,工作條件查表確定精度等級大致范圍,再根據(jù)計算得出的小齒輪圓周速度查表確定其精度等級組,并將同一公差組內(nèi)的各項指標分為若干個檢驗組。然后根據(jù)生產(chǎn)批量、 使用要求、 測量設(shè)備條件等選擇一個檢驗組來檢查齒輪的精度。但 2008 年的國家標準沒有給出公差組和檢驗組,并指出:在檢驗中,測量全部輪齒要素的偏差既不經(jīng)濟也沒必要。該軟件按齒輪工作性能要求推薦了若干個檢驗組,將齒輪使用范圍分為機床、 輕型汽車、 重型汽車等 12 大項數(shù)十小項。表 1 為機床齒輪的分類及推薦檢驗項目舉例。檢驗項目還可以根據(jù)生產(chǎn)實際情況作適當調(diào)整。當有條件檢驗 ' 和 ' 時,可以不必檢驗 和 。測量 簡單、 方便,所以常用。 如果能檢驗 " 和 " ,則不必檢驗 。檢驗項目確定后即可根據(jù)國家標準中給出的計算公式自動求出各偏差允許值。
2.4 確定齒輪副精度
齒輪副的評定指標主要有:齒輪副的中心距偏差 ,齒輪副的軸線平行度偏差 和 ,齒輪副的側(cè)隙 等。側(cè)隙通常由齒厚偏差 或公法線平均長度偏差 來控制。測量公法線長度比測量齒厚方便、 精確,因此生產(chǎn)中常用測量公法線長度的方法來控制齒輪副側(cè)隙。
2.5 確定齒坯精度齒坯是指在輪齒加工前供制造齒輪用的工件。齒坯精度包括內(nèi)孔、 頂圓、 端面等定位基準面和安裝基準面的尺寸偏差和形位誤差以及表面粗糙度要求。具體數(shù)據(jù)有表可查。
2.6 數(shù)據(jù)打印
為了方便計算數(shù)據(jù)的保存及打印,軟件生成一個 TXT 文本,保存輸入?yún)?shù)、 國標規(guī)定的精度項目和側(cè)隙指標計算值等
2.7 生成工程圖
利用新的開發(fā)工具 ARX(AutoCAD Runtime eXtension)對AtoCAD進行二次開發(fā),ARX程序本質(zhì)上是 Windows DLL程序,與 AutoCAD共享地址空間,以消息驅(qū)動的方式直接調(diào)用AutoCAD的核心函數(shù),AutoCAD通過調(diào)用入口函數(shù)來調(diào)用
該文獻采用 51 單片機及其外部擴展電路對 209T制動梁端軸焊
接預熱溫度進行檢測和顯示,控制了 209T制動梁端軸的焊接
在設(shè)定的預熱溫度下進行。應(yīng)用表明,該預熱溫度檢測系統(tǒng)達
到了改善焊接接頭的塑性、防止冷裂紋和減少焊后殘余應(yīng)力
的目的,提高了 209T制動梁更換端軸的質(zhì)量,保證了客車運
行中制動梁端軸工作的可靠性。
計算機輔助圓柱齒輪精度設(shè)計系統(tǒng)的研究
牛貴峰 姚輝前 邱亞玲
(南石油學院機電工程學院 四川成都610500)
齒輪精度設(shè)計牽涉的因素較多 標準中對漸開線圓柱齒輪精度共規(guī)定了 個指標 使得精度設(shè)計繁雜 麻煩 本文介紹用 語言編寫的軟件來完成齒輪精度設(shè)計工作 人機對話采用交互式窗口 使得設(shè)計方便 迅速經(jīng)實際運行表明該系統(tǒng)在齒輪精度設(shè)計上有效準確
1,齒輪精度設(shè)計概述漸開線圓柱齒輪精度設(shè)計涉及面廣 現(xiàn)簡述如下公差組與精度等級對齒輪傳動一般有四個方面的要求傳動準確 即傳動比變化盡量小傳動平穩(wěn) 即振動與噪聲盡可能小 避免產(chǎn)生動載荷與撞擊工作點面接觸好 即載荷分布要均勻 避免動載荷大時齒面應(yīng)力集中 引起早期點蝕 折斷而降低使用壽命齒輪副側(cè)隙要合適按上述分析 齒輪精度標準按誤差特性對傳動性能的主要影響劃分為三個公差組 詳見表
關(guān)于齒厚極限偏差和公法線平均長度偏差兩個項目由于它們屬于側(cè)隙配合系統(tǒng) 所以不包括在上述三個公差組內(nèi)齒輪精度設(shè)計就是要確定三個公差組的精度等級 同時還要根據(jù)實際情況確定三個公差組內(nèi)相應(yīng)評定指標選擇齒輪精度等級必須根據(jù)其用途 工作條件等要求來確定 如考慮齒輪使用的場合 工作速度 對振動噪聲的要求以及使用壽命等方面的要求 同時還應(yīng)考慮在不同用途不同工作條件時 對齒輪的要求側(cè)重點不同 因此各公差組應(yīng)選用不同的精度等級 精度等級的選擇一般有兩種方法一為計算法 一為類比法 計算法相應(yīng)復雜 類比法必須有豐富的資料 目前已總結(jié)許多資料可供設(shè)計時參考 本文是在類比法基礎(chǔ)上輔以適當?shù)挠嬎銇泶_定齒輪的精度等級齒輪副的側(cè)隙為保證齒輪傳動正常工作 在齒輪非工作點面間應(yīng)有合理的側(cè)隙以貯存潤滑油和補償齒輪在工作時的變形 對于齒輪副的側(cè)隙 精度標準規(guī)定采用基中心距制 即通過改變齒厚以得到不同的側(cè)隙 為此規(guī)定了種齒厚極限
偏差及代號 側(cè)隙的設(shè)計就是要確定齒厚上下偏差及其代號 齒厚上下偏差的確定可用計算法 類比法和試驗法考慮到類比法資料不全 試驗法成本較高 故本文采用計算法 雖然公式中考慮的因素尚不全面 但也是目前設(shè)計中比較可靠的方法
2 ,基于以上分析 我們給出齒輪精度設(shè)計的流程框圖如如下圖所示由于 Visual Basic語言是一種面向?qū)ο缶幊痰哪K化語言與傳統(tǒng)的面向過程的語言不同 它通過鼠標單擊界面上的控件就可以使該控件所代表的事件發(fā)生 即完成相應(yīng)的任務(wù) 所以執(zhí)行程序時 也可以不完全按照框圖所示的順序 如在該軟件中 確 定 好 齒 厚 上下偏差后 又感覺齒輪精度等級確定得不妥 只要再單擊 確定齒輪精度鈕就可重新確定齒輪精度等級。
其特點主要是整個齒輪精度設(shè)計系統(tǒng)始終采取了友好的人機界面用戶只要按計算機提示鍵入相應(yīng)的內(nèi)容 程序就會自動運行并輸出結(jié)果 實踐證明 本算法能夠快速成功地解決漸開線圓柱齒輪的精度設(shè)計問題 程序采用Visual Basic編程語言可方便與其它高級語言兼容 在機械設(shè)計中具有一定的實用性.
看了這么多的文獻論文,對自己所要做的設(shè)計也有了一些初步的理解,相信自己在老師和學長的幫助下,會順利的完成這次課程設(shè)計!