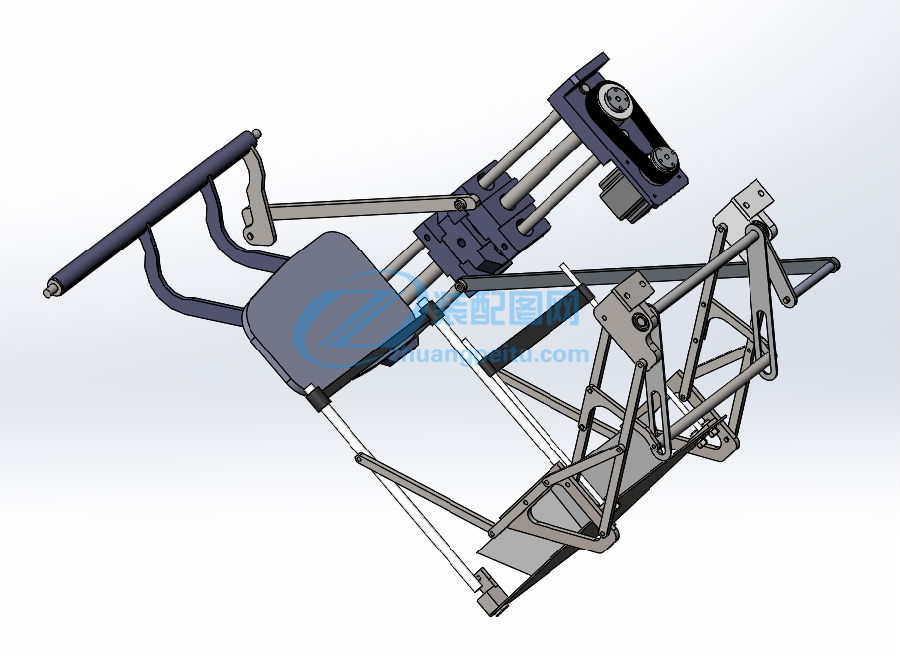
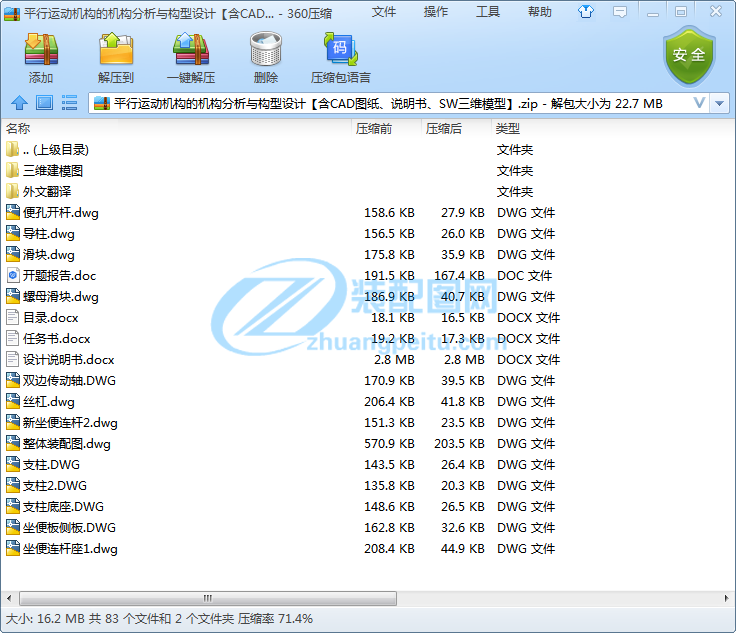

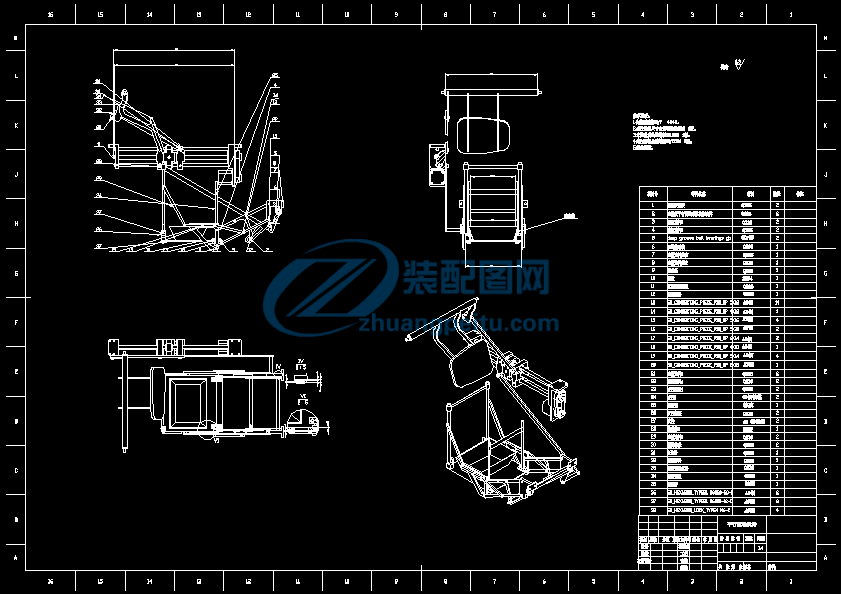
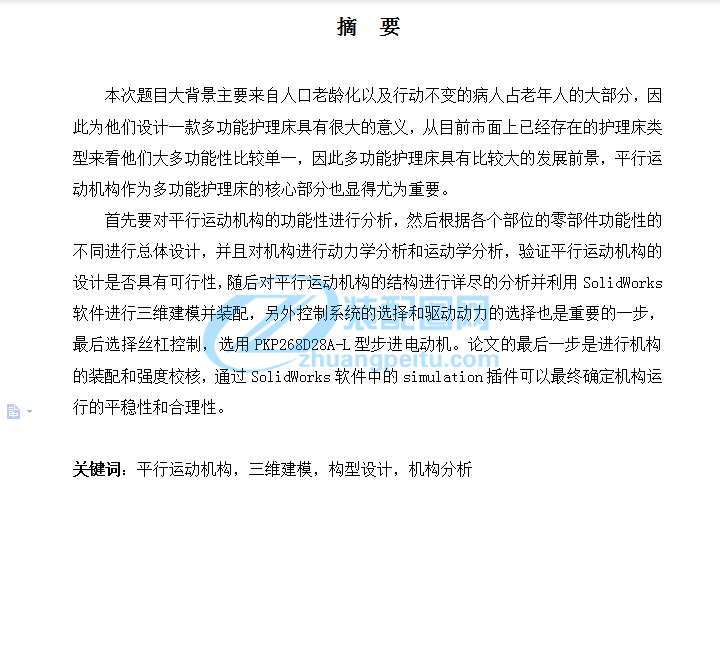
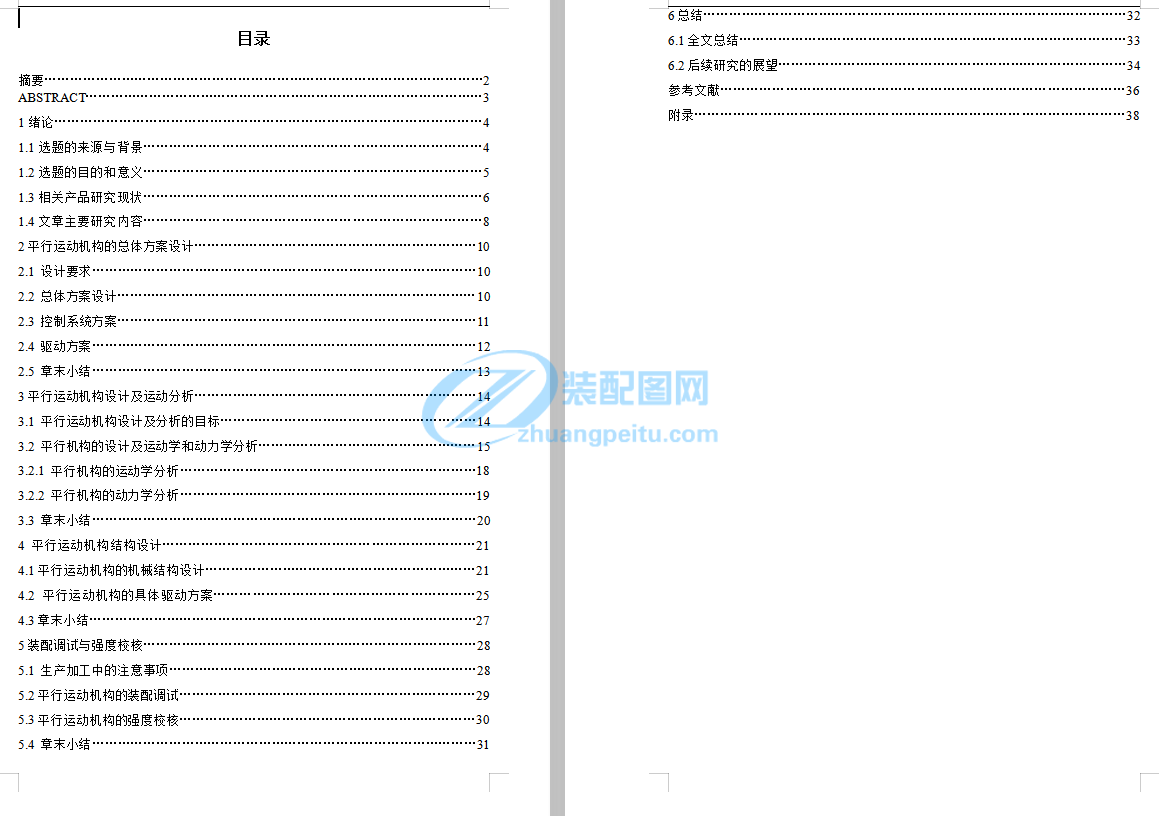
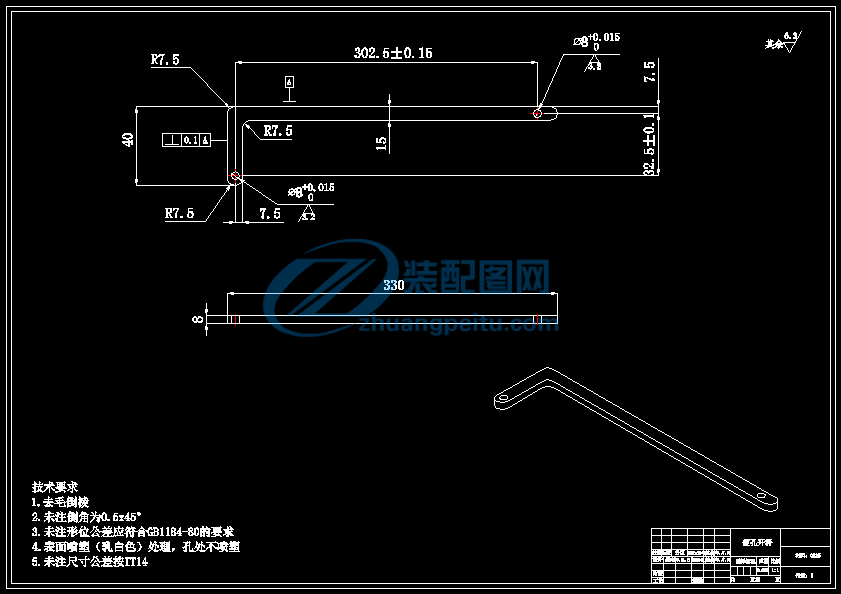
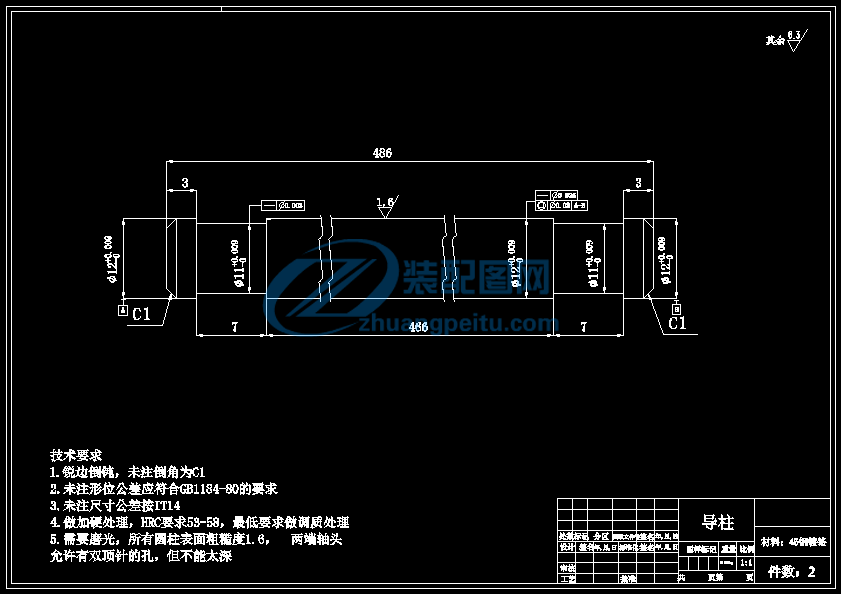
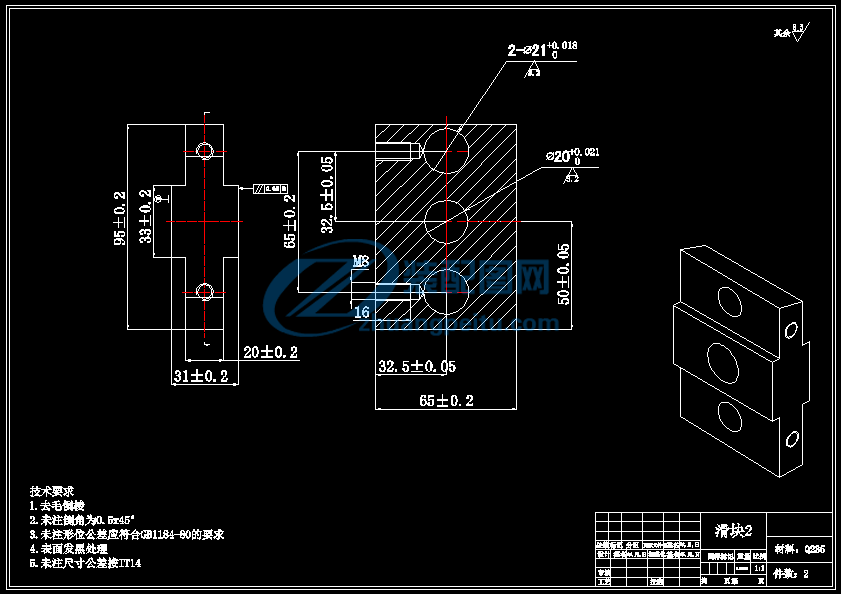
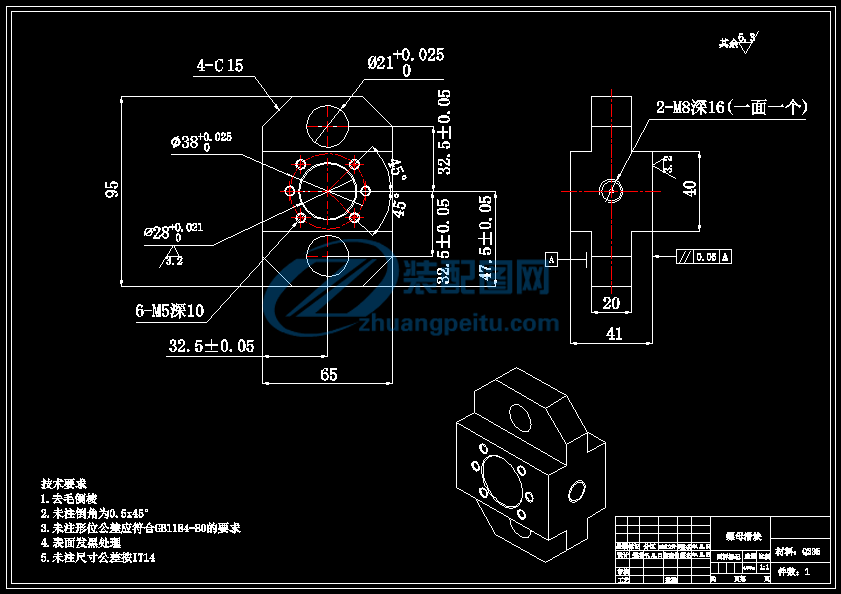
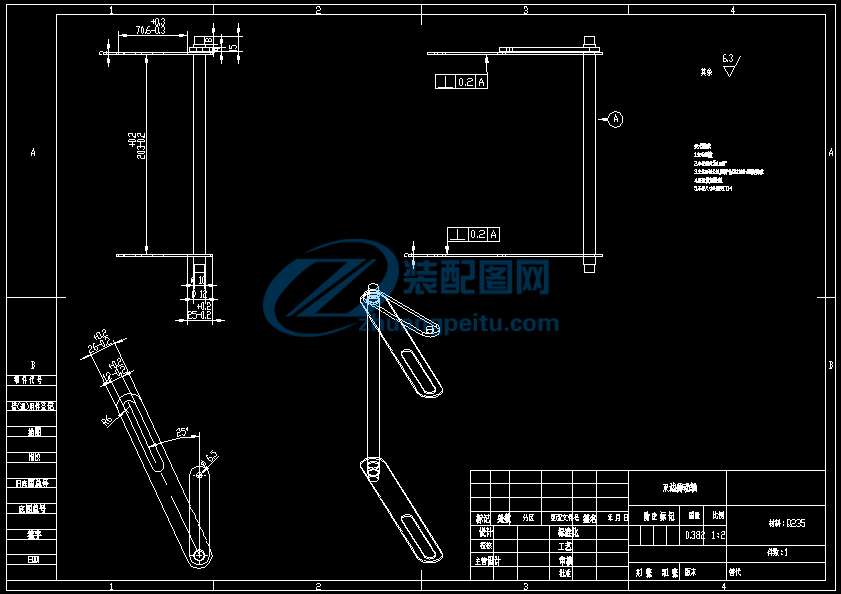
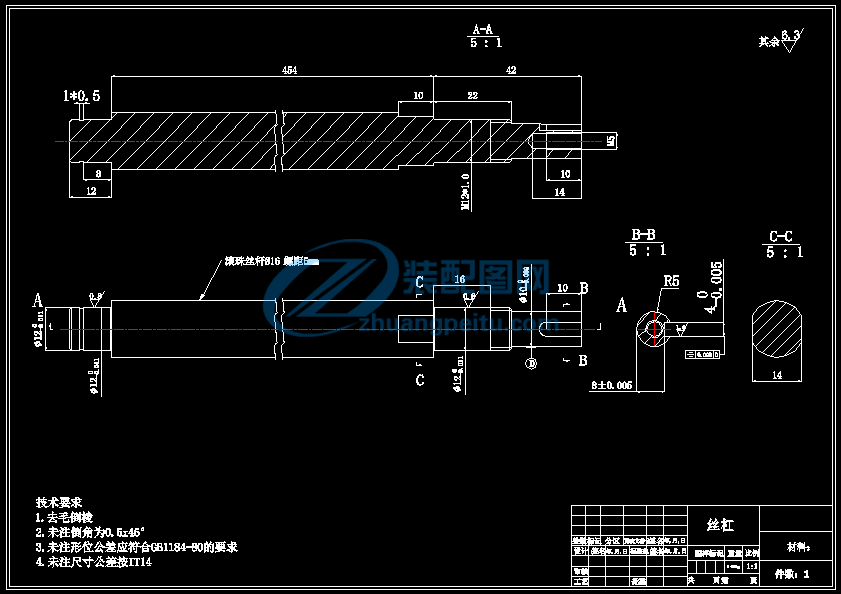
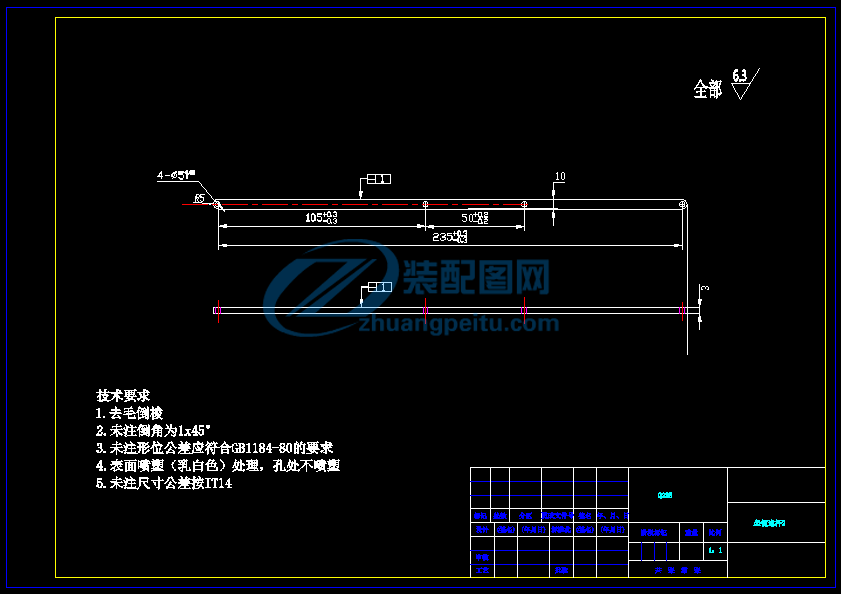
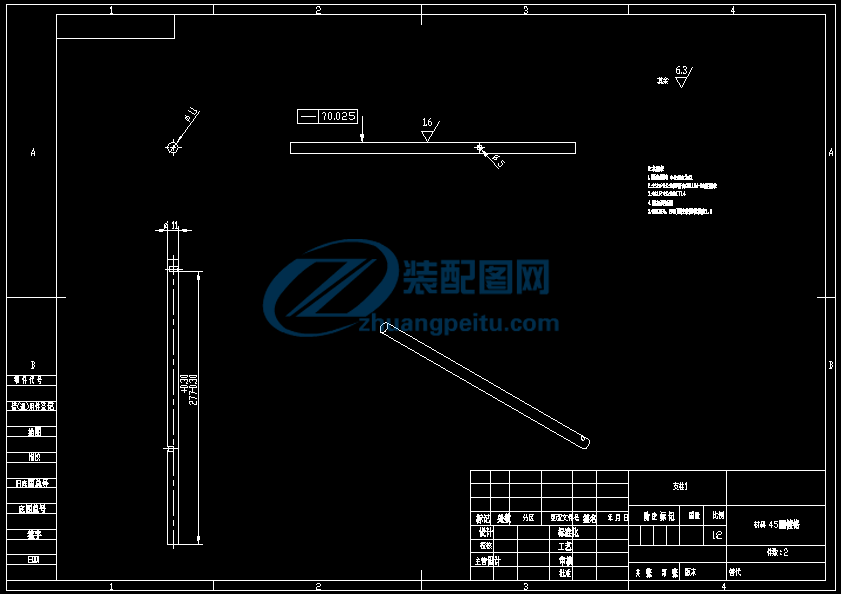
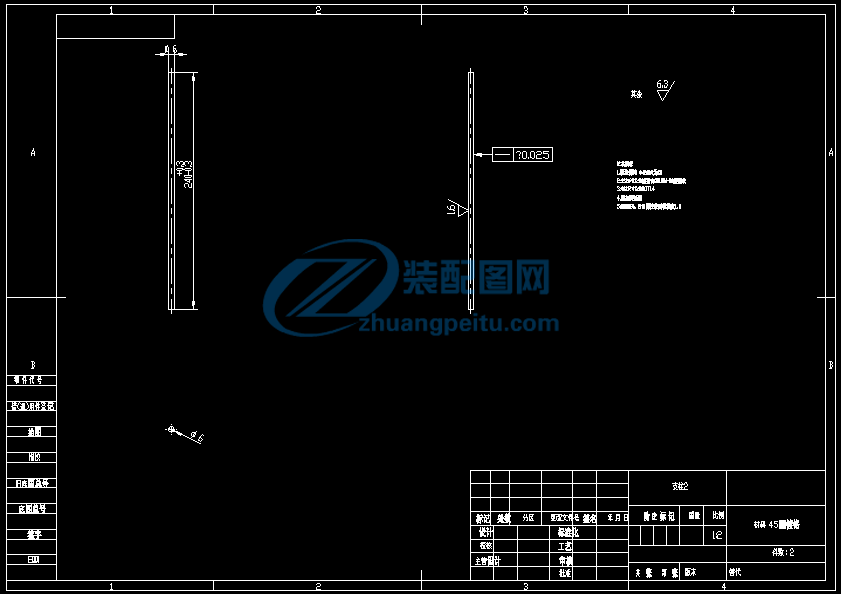
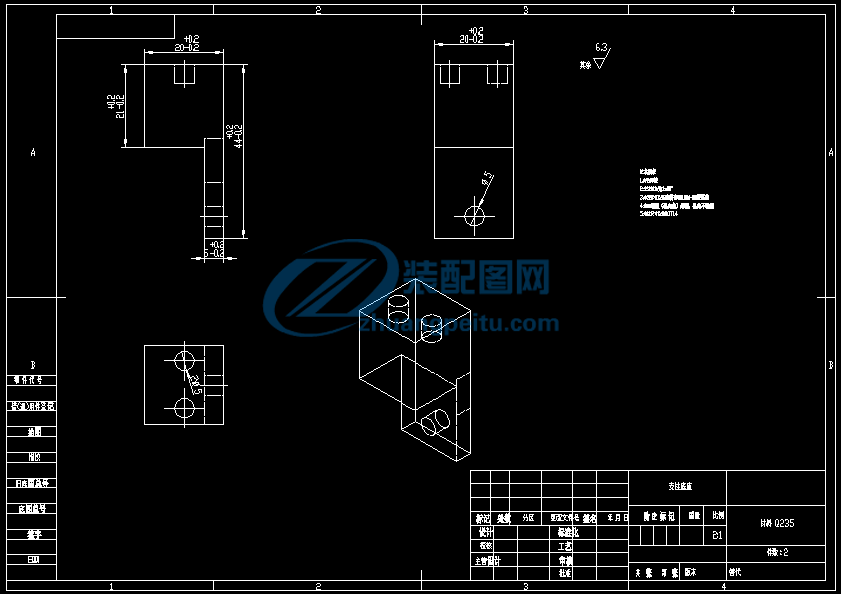
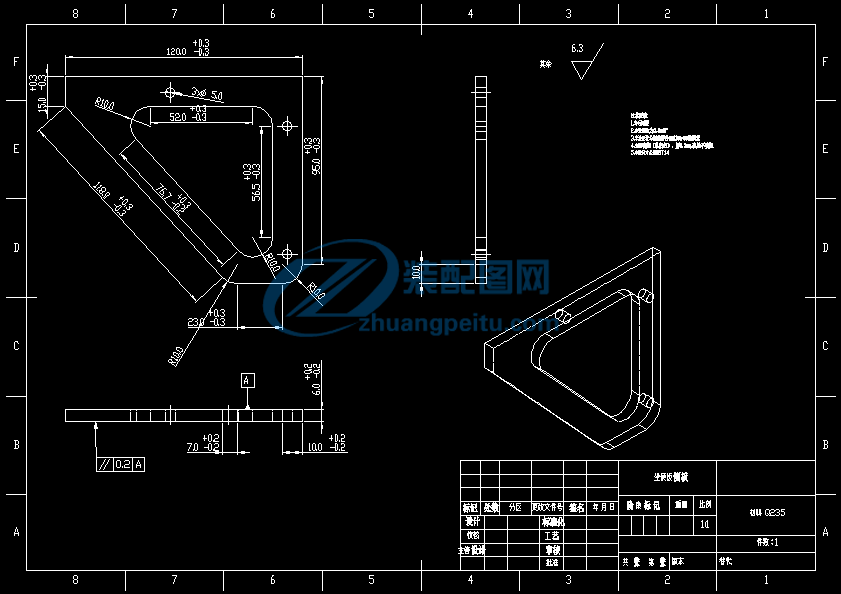
Mechanism Design and Simulation Analysis of Multifunctional Nursing BedLizong Lin, Song Zhang, Xinglong Hu School of Mechanical and Power EngineeringEast China University of Science and Technology, Shanghai, ChinaE-mail: lizonglin@online.sh.cnE-mail: skyzhangsong@163.comAbstract-This research develops a new multifunctional nursing bed that can realize the movements of turning left and right sides and defecating on the bed for clinical use. And use the ADAMS to analysis the effects to the motor torque from the force on the rotated board, friction of contact pair and space position. By analysis of dynamic on the model of the main mechanism can get the curves and the influences of torque, which plays an important guiding role in selecting appropriate motor and installation structure.Keywords- nursing bed, ADAMS, virtual prototyping, dynamic analysisI. INTRODUCTIONNursing beds as parts of medical equipments are necessary for hospital care, and has been widely used in hospitals, nursing homes, retirement homes and many other fields. However, the prices of good quality nursing beds are expensive, the new study can reduce the cost and the difficulty of care, for example, to the patients resting on the bed for a long time, their turning over and lifting back required nurses have sufficient physical strength. Common beds just have head up, leg flexion and extension functions, this bed adds the function as rolling around, defecating on the bed and so on as needed [1].II. MECHANISM DESIGNThe nursing bed can be divided into four parts by the structure and function as: bed body, control cabinet, a framework for activities, removable bedpan. Block diagram as in Fig. 1In the control cubicle, the installment has the master control board, the motor-driven board, the transformer, the switching power supply and so on. The control cubicle connects with the nursing bed by the connection. Except the fixed mechanism, the bed body also includes the drive motor and the vane organization. The active frame installment has the wheels, which may be separated from the nursing bed. In the frame there are the water tank, stool which can rise and fall and the hot air blower. The transportable bed pan also installs wheels and can insert into the activity frame. In addition, the control system also includes the wire operators, the LCD and so on. In the system there are six DC motors which complete the actions of rising and falling of the head, the flexion of the leg, rolling around of the left and right, opening and closing of the vane and rising and falling of the stool and so on.A. Bed Function.The bed activity functions including the rising and falling of the head, the flexion of the leg and the bed body tum sides which satisfied patient's active request basically, favors the patients to improve their blood circulation and prevents the bedsore. This nursing bed has designed the flexion of the leg conforms to human body's movement characteristic. The bed body side turns may divide into three movements: the left side to tum, the right side to tum and the even side. Fig. 2, Fig. 3, Fig. 4 is the bed body's three movements.B. Nursing FunctionThe defecation function is rare in other electric nursing bed which suits the paralysis patient especially. In the middle of the bed body there is a rectangular opening, where can only seen two vanes in the normal condition. When defecating, the vane turns down to makes a breach, then the defecation device rise. After the defecation completed, the vane upturns continues to fill the gap. The defecation device is composed of the active frame and the motion bed pan which can inserts into the frame, and the entire frame can coordinate to load the bed body. The nursing bed can also provide the functions of spraying water and drying. In the active frame installed the water tank, the hot air blower and the solenoid valve. The water tank has a water pump, heater, the temperature sensor and the water level sensor. It can be realized that the water temperature establishment, the water temperature maintains and the water tank volume automatic increase and so on under the controller's control. The patient who is sick bed in long-term is the major recipients of this nursing bed. Before defecate, press the key “stool raise“ on the remote control, two vanes open, and then the stool raise, plate of the stool erects automatically, and so as to the bed pan. The patient can defecate after these movements completed. After the defecation completes, press corresponding key, carries on the flushing first, then uses hot blast drying, which has manifested the human nursing function. The water for flushing is preserved in the tank, and use heating wire to maintain the temperature. It's needed to gather and process of the temperature in order to realize the control of it, the gather can completed by the sensor, the process and control can completed by the monolithic integrated circuit. As a result of the patient's defecate time is uncertainty, and requests maintains the temperature constant, for the aim of providing appropriate temperature momentarily.III. SYSTEM MODELINGA. ModellingNursing bed is a very complex structure, which can divided into the mechanical component of the bed body, the active frame, the transportable bed pan, the electronic control system and the motor driven system by the structure and the function. Fig. 5 is the geometric modeling graph of the vane [2].I Right rotated board 2 lever of right rotated board 3 Driving arm of right rotated board 4 Motor of right rotated board 5 Motor of left rotated board 6 Driving arm of left rotated board 7 lever of left rotated board 8 Left rotated board 9 Door axis of rotated boardFigure 6 Lever and driving arm of rotated board I Lever of rotated board 2 Driving arm of boardB. Contact Pairs ProcessingFig. 6 is the geometric modeling graph of the vane lever and actuating arm. The axis of one of the vane lever ends fixed with the vane, the other end has a curve groove. Both sides of the vane actuating arm are round axes, whose axle centers are parallel. One axis is linked with the motor and fixed, the other coordinated with the curve groove to form a contact. The motor caused the actuating arm to reverse, which can realize opening and closing of the vane.III. SIMULATION ANALYSIS The purpose of dynamics simulation of the vane is to analysis the influence to the torque in the different condition, and guide to improve the design and select the appropriate drive motor [3]. A. !influence to Torque from ActionThe sizes of the left and right vanes are not equal, but the motors are same. Select the right one which has a greater area and force to analysis [4]. Select the action point in middle of the two vanes, and the arm of the force is 15 cm. The friction coefficient of the steel is 1.2 to 1.4, and 0.02 to 0.05 after lubricated, takes the friction coefficient of 0.05.The curves are not smooth seen from Fig.7 and Fig.8, as the high frequency component coupling to them analyzed mathematically, which were considered to be vibration in actual. It is also discovered that the vane has a phenomenon of vibration, which meet with the simulated data when testing. The vibration has a relation to the stress, nature of material, rigidity of material, osculating curve of rigid body, friction coefficient and so on. It is inferred from the simulation analysis that the bigger stress the smaller vibration. Make sure the contact surfaces are smooth when design the curve groove of the vane lever to reduces the nonessential vibration. Fig.9 is the angular velocity when the stress is SOON, the vibration situation can be observed obviously [5].The actual action to the vane from the patient is not constant but increases gradually when the vane turns to the level position nearby. So that, select the larger motor torque as far as possible to prevent overloading.B. lrifluence to Torque from Friction CoefficienttThere are three kinds of restraints altogether in the vane simulation: fixed restraint, hinge restraint and contact restraint. The fixed restraint cannot cause the friction force, but the hinge restraint and the contact restraint can. The hinge to the hinge restraint can be processed as sliding bearing. The friction coefficient of sliding bearing is small. The dynamic friction coefficient of sliding bearings is 3.0xl0-3 and the static friction coefficient is 4 .0 x 10 - 3 ? Although the contact restraint is also a kind of sliding friction, but it cannot simply processed as sliding bearing, because the contact is complex, and the stress is also big. Fig. 10 represents the contact force when lever axis and curve groove of actuating arm have a stress of SOON, where the biggest can reach 1800N.Fig. 11 and Fig. 12 respectively represent the torque chart in the friction coefficient of 0.07 and 0.31, and the stress of SOON.Compared with Fig. 11 and Fig. 12, it cannot obviously see the changes of the torque, so as the curve. The biggest diversity is that the vibration reduces when friction coefficient is 0.31. The friction coefficient f.I. has not caused the biggest moment of force change obviously, only has a tendency of enlargement, after the process of filter smooth correlative value [6].C. lrifluence toTtorque from Space PositionWhen design the vane, not only consider the actual installment space and the request size, but also need to pay attention to the relations in the space position between the revolution axis of the vane lever and the revolution axis of the actuating arm. Because their positions are not only relating whether the vane can operation normally, but also affects the biggest driving force. Use the coordinates system as Fig. 13 when establish the coordinate. Fig. 14, Fig. 15 and Fig. 16 are the changing graph of biggest torque in VI-452 Volume I 2010 2nd International Conference on Mechanical and Electronics Engineering (ICMEE 2010) different space position [7]. And the stress is SOON, friction coefficient is 0.03.Comparing the data in the different condition may see that the time and the biggest torque have changed remarkably. And the movement time is the smallest in condition 3, so as the force moment. In the condition 2, the lever arm separated from the drive shaft in the moving procession. When actually determine the data, should consider about the motor of torque, size and structure and so on, the best effort may not be the most suitable [8]. Through the analysis of dynamics simulation to the vane that:1) The motor driven torque is small. In the process of simulation analysis, exerted 500N force to the vane and calculates the biggest torque of the motor is 25Nm, but actually the torque is 18Nm, therefore present the phenomenon of the vane asthenia when raising. Here takes 500N force, it is only the average action size in the normal condition. When actual use, possibly bigger than 500 N, so that it must be considered that the motor should have a sufficient remainder actuation torque to satisfY the request under the dissimilar condition. 2) The influence of the friction coefficient is not big to the torque. Under the condition of constant action, it's indicated that the friction coefficient has a very small influence to the torque, through takes different friction coefficient to calculate the biggest torque. 3) The space position of the rotation axis has a bigger influence to the torque, the condition 1 and 3 have a difference of 1 ONm, and the movement time also changing.V. CONCLUSIONDiscussed the influence factors include the driving torque action, friction coefficient, space position and so on by the dynamics and the kinematics analysis to the vane of the nursing bed, which improved the theory basis to the design of the structure, and provided the science basis to the performance evaluation analysis of the bed. This bed may also increase the network communication function to the system, which will cause it to be able to transmit the information automatically to the superior machine, and realizing the long-distance patient care monitor.Reference[I] Fang Jinbo, Chen Hong. “The Challenges to Nurses Work from Aging Populations,“ Journal of International Nursing. vol. 3, Feb. 2004,pp.147-149.[2] Zheng Jiaorong. ADAMS-Getting Started with Virtual Prototyping Technology and Improve. Beijing: Mechanical Industry Publishing House. 2002. I [3] Peng Qibo, Li Haiyang. “Modeling and Simulation of Robot Maoipulator Based on Virtual Prototyping Technology,“ Journal of East China University of Science aod Technology, vol. 33, Jun. 2007, pp.58-62. [4] Jin Xin, what Yulin aod Liu Hua. “The Wind-driven Generator Coupled Oscillation Analyzes,“ Journal of Vibration aod Shock, vol. 26,Jun.2007,pp.144-147.[5] Liu Jun, Lin Lizong, Liu Xiaoping aod Waog Gaog. “ADAMS Flexible Body Movement Simulation Analytical Study and Utilization,“ Modem Maoufacture Project, vol. 5, May. 2004, pp. 53-55. [6] Dong Ligaog, Chen Weihai aod Zhang Jianbin. “Kinematic Analysis aod Simulation for Hybrid Type Cable-driven Maoipulator, “ Journal of System Simulation, vol. 19, Sep. 2007, pp. 4007-4011.[7] Waog Yeo “Development of Control System for Multifunction Nursing-bed,“ Control & Automation, vol. 22, Jul. 2006, pp. 117- 119. [8] Jiaog Hao, Waog Wei, Liu Yongping. “The Study on the Multifunctional Nursing Bed,“ Manufacturing Automation, vol. 31, Jun. 2009,pp. 71-73.MOBILE ROBOT SYSTEM TO AID THE DAILY LIFE FOR BEDRIDDEN PERSONSTakashi KOMEDA, Hiroaki MATSUOKA, Yasuhiro OGAWA, Mitsuyoshi FUJII, Tateki UCHIDA, Masao MIYAGI, Hiroyuki KOYAMA and Hiroyasu FUNAKUBOSHIBAURA INSTITUTE OF TECHNOLOGY FUKASAKU307, OMIYA, 330, JAPANABSTRACT People who care for bedridden patients have great burdens in mind and body. The number of old-aged people in the population is increasing in Japan, the problem of care for bedridden patients will become an increasingly social problem. We are trying to solve this problem by developing a small mobile robot system for bedridden patients. The purpose of this system is to pick up and to bring a small object putting it somewhere inside the room semi-automatically. This mobile robot consists of a manipulator, visual sensor unit and mobile unit. This system gives information about the surrounding to the patient through the camera and monitor. When the patient directs an target object on the monitor, the system measures a 3-dimensional location of it, and the mobile unit approaches the object and the manipulator picks up and carries it back to the patient. This system is controlled by the image information and also by human through an interface based on images. 1. INTRODUCTION We generally have great burdens in mind and body to help bedridden patients. The population of old aged increasing today, this helping work will become a social problem. We are trying to solve this problem by developing a small mobile robot system[l]. The purpose of this system is to bring the target object putting it somewhere inside the room semiautomatic ally. Of course, there are many kinds of works involved in helping bedridden persons, for example changing clothes, giving the medicine and cleaning the bed, etc With this system. however, we think that even if the machine achieves only one type of work instead of a human, the burdens on the helper should decrease in mind and body.2. SYSTEM CONSTRUCTIONFig. 1 shows the overview of the mobile robot. This mobile robot consists of a manipulator, a visual sensor unit and a mobile unit. This system gives information about the surrounding to the patient through the camera and the monitor. When the patient directs a target object on the monitor. the system measures a 3-dimensional location of it. The mobile unit then approaches the target object and the manipulator picks up and carrying it back to the patient. The si7e of the mobile unit is width 600 mm, length 800 mm. height 550 mm, and it has the space to load the controller and batteries. The mobile unit is driven by two DC servo motors and two wheels. Each motor has a pulse encoder for position control. The length of the manipulator is about 1255[mm] and it has 4 degrees of freedom and a hand. Its weight capacity is about 3 kgf. The actuator of each joint is DC servo motor with a pulse encoder to control its position. A pair of strain gages is put on to the wrist part of the manipulator. The weight of a target object can therefore be measured and used in the feedback loop of the controller.3.VISUAL SENSORThe visual sensor system consists of a CCD camera and an image processor which is controlled by a personal computer. The camera is attached on the wrist part of the manipulator. This design makes it possible to move the camera and manipulator simultaneously. Then, the system gives 0-7803-3280-6/96/%5.00 @ 1996 IEEE - 2789 - surrounding information to the operator through the camera and the monitor. If a target object is directed, it measure a 3- dimensional location of it. The target objects for this mobile robot system arc things for daily using which have different size and shape. It is difficult to treat an image processing to recognize such things and “me its location in real time. To solve this problem, we put things for daily using on a tray which has a cylindrical fixed size grip. This grip is the target object of the visual sensor. Therefore, we can easily measure the size of the target object on the image plane as the number of pixels of the CCD camera, and calculate the distance to the object using a simple formula(Fig.2). The treatment to measure a 3- dimensional distance using the image and a following visual tracking of the target object can be done in real time.Monitor screen No.2 is the image of after O.S[sec] of monitor screen No.1. Monitor screen No.1 shows the center and feature points of the target object. Monitor screen No.2 shows that the visual sensor finds new center and feature points by scanning the image. After O.S[sec], the visual sensor will find another new center and feature points.4. VISUAL TRACKINGThe mobile unit is controlled by a personal computer, a control board and motor drivers. The computer calculates the number of drive pulses of each drive motor from the location of the target object, and sends the information to the control board. The control board generates DDA pulse distribution to do the synchronous operation between two motors[2]. Motor drivers observe the feedback pulse to do the rate control and the position control. However, even if we perfectly control two motors of the mobile unit using the feedback pulse, the mobile unit docs not always move exactly because of the difference of the diameter of each drive wheel and the road surface condition. Therefore, we use the visual tracking method to solve this problem. This mobile robot has an image information from CCD camera, and this information renews every 0.5 second. When the mobile unit approaches the target object, the computer calculate the position of the target object on the monitor every 0.5 second. If the position shifts from the center of the monitor, the mobile unit is controlled to change the direction to catch it in the center. This method is able to keep the object in the center of the monitor continuously(Fig.3). The method was confirmed by measure the relation between the center of the target object on the monitor and the angle of mobile robot. Fig.4 shows one of the results when the mobile robot has approached about 1800 mm. This result shows that the center of the target object positioned about 360 pixel point (full pixel is 512) when the mobile robot starts action to approach to the target, and is caught the center of the monitor (256 pixel point) when the mobile robot run about 750 mm. The method is able to keep the center within 5 pixels during 750 mm to 1800 mm running and enough precision for this mobile robot.5. CONTROLLER AND INTERFACEOur mobile robot can bring the target from the undecided position inside the room semi-automatically. However, if the operator wants a specific target, he must communicate with the robot through the computer. For example, if the target is at the right side of the robot, he must point out the arrow on the monitor by the mouse cursor to turn the robot to find the target on the monitor. In addition, he must teach the robot which is the target. Furthermore, this robot is used by the operator who is not professional about robots, and is handicapped.We have therefore developed an interface system between the robot and the operator based on following conceptions. (1) Easy and simple. The operator can control the robot easily like as radio-controlled car and also this input method must be simple.(2) Safety High space is not necessary, and for the softy tic robot can interrupt the movement every time tic robot or operator recognizes a dangerous motion. This robot has the small camera which is attached on the wrist part of manipulator, the operator can recognize the direction of the end cofactor and the sconce through the monitor. But, it is not sufficient to control tic robot with surrounding information through the camera, the operator also necks information about status of the robot. For example if the position of the robot reaches the upper limit of its working space, it is impossible to move the robot even if the operator directs to move UP.Under the configuration of Multi CPU, each task compensate robot motion, and the operator can choose cash task as an object according to his necessity. With this system. the operator can simply choose the robot motion task as an edict from existing several tasks (Fig. 7). These tasks are not always in active, hut always on standby to get the command from the operator. This means that if the operator finds it necessary, he can interrupt the motion to execute another tasks which can escape from a dangerous path.It is also necessary to compensate the safety when the robot finds a danger while the movement, this means not the operator but the robot can recognize the danger. In our system, a pair of strain gages is placed on the wrist part of the manipulator, the robot can measure the load at the wrist part using these strain gages, and rccogni7c the danger when excessiveness force arise at this part. Using the time slice method, we can interrupt the robot motion without influence when robot recognize a danger. This means that this system watches a danger both operator and robot.6. CONCLUSIONS(1)We have developed the mobile robot system which consists of a manipulator, a mobile unit and a visual sensor, and is controlled by image information. (2)We have developed a visual tracking method to correct the motion direction, it is simple way, high response and good accuracy to use this system.(3)We have developed the interface system between our mobile robot and the operator. This interface can observe each task of robot motions and show the graphical motion using the real status information. We tried to check functions of this system, it was simple and easy to operate the robot and also we confirmed that it is useful for safety, In future, we will improve this system more interactive and try to apply to the obstacle avoidance.ACKNOWLEDGMENT We wish to thank the Welfare Equipment Development Center of Japan for support this project.REFERENCES 1. T.Komcda etc. “ Mobile robot system to aid the daily life of bedridden persons in the private house”, Proceedings of 2nd European Conference on Advancement Rehabilitation Technology, 24.4( 1993) 2. T.Komeda etc. ‘I Mobile robot system to aid the daily life of bedridden persons in the private house(2nd report)”, Proceedings of 3rd European Conference on Advancement Rehabilitation Technology, pp.179-181(1995)